Школа Федора Рязанова. Диагностика дизельных систем с электронным управлением. Урок 1
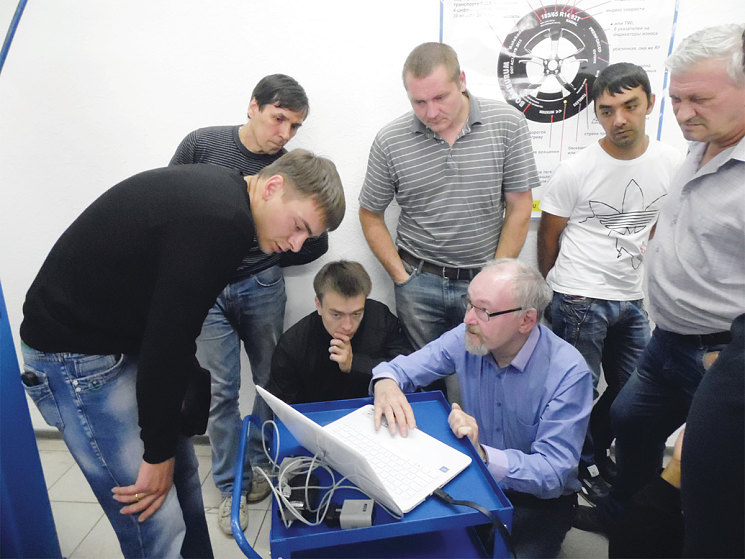
Биографическая справка
Рязанов Федор Александрович
1980 год – окончил МВТУ им. Баумана (факультет «Приборостроение»).
1980–1990 годы – работа в инженерной службе Тихоокеанского флота (г. Владивосток)
С 1990 года – работа в различных автосервисах (специализация – автомобили японского производства).
С 2006 года – преподаватель Школы диагностов «ИнжекторКар» (г. Москва).
Уважаемые читатели!
Полную версию данной статьи можно прочесть в бумажной версии
журнала "АБС-авто" № 1 (2018 г.)
журнала "АБС-авто" № 1 (2018 г.)