Япония. Там, где практичность дружит с инновациями
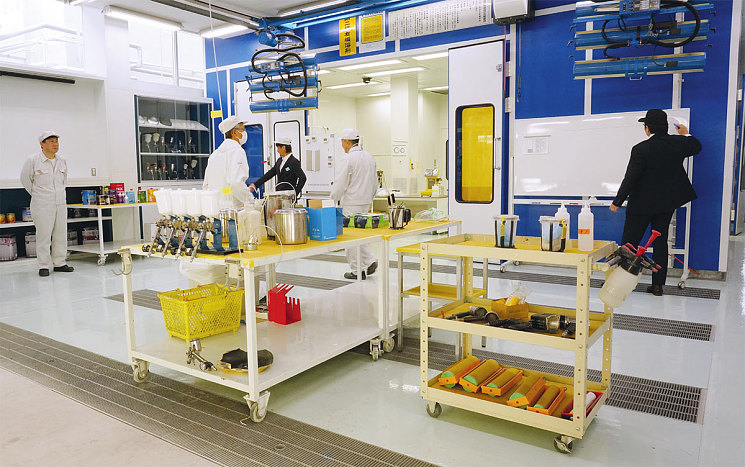
Справка из Википедии: «Инновáция, нововведение (англ. innovation) – это внедренное новшество, обеспечивающее качественный рост эффективности процессов или продукции, востребованных рынком. Является конечным результатом интеллектуальной деятельности человека, его фантазии, творческого процесса, открытий, изобретений и рационализации. Примером инновации является выведение на рынок продукции (товаров и услуг) с новыми потребительскими свойствами или качественным повышением эффективности производственных систем. Инновация – это не всякое новшество или нововведение, а только такое, которое серьезно повышает эффективность действующей системы».
Какое все это имеет отношение к автомобилю и особенно к автосервису? Самое прямое. Об этом мы сегодня и будем говорить на примерах организации работы нескольких авторемонтных предприятий Японии.
Нет, Страну восходящего солнца мы не посещали и японскому колористу ручку не пожимали. Мы просто заинтересовались новостью о том, что группа специалистов компании Бизнес Кар – официального импортера Nippon Paint Co. в конце прошлого года посетила Японию для знакомства с опытом своих японских коллег. Мимо такого события редакция равнодушно пройти никак не могла. Созвонившись с менеджерами компании, напросились на встречу. Сегодняшняя работа – ее результат. Пора начинать разговор. Нашим собеседником будет Илья Колдин, руководитель департамента авторемонтных покрытий и материалов для кузовного ремонта ООО «СП БИЗНЕС КАР».
Редакция журнала (АБС): Илья, Вы посетили несколько японских автосервисов по кузовному ремонту. Скажите, пожалуйста, отличаются ли чем-нибудь японские кузовные производства от российских?
Илья: Если говорить по большому счету, то – нет. Принципиальной разницы я не нашел практически ни в чем. Примерно одинакова организация рабочих пространств кузовных цехов, их оснастка, и даже ритм работы предприятий как-будто не имеет серьезных отличий от наших автосервисов. Все отличия лишь в мелочах. Но, как известно, дьявол кроется как раз в них. Давайте мысленно пройдемся по участкам японского кузовного цеха и обратим внимание на эти самые «мелочи».
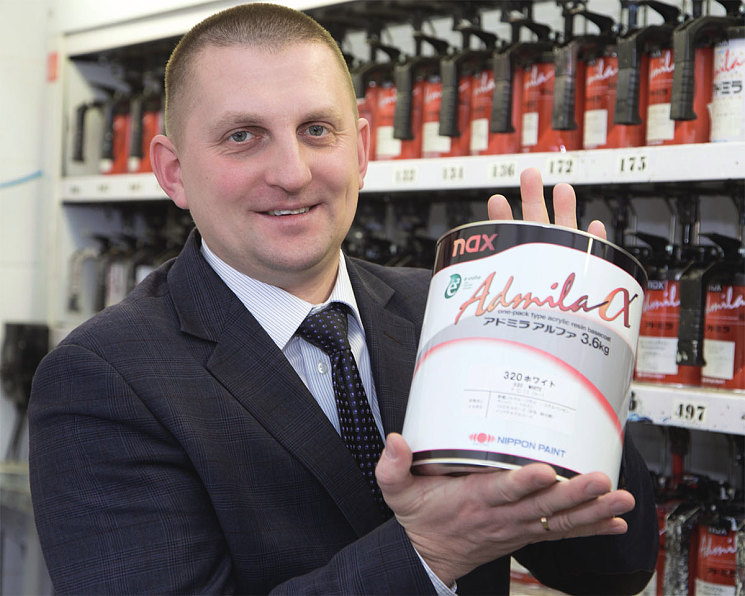
Участок подготовки. Оборудование миниатюрное. Это шлифмашинки и краскопульты. У нас машинки в основном 150 мм, у них чаще всего 125 мм. Круги используют разных брендов, выбор зависит от предпочтений конкретных исполнителей. Приоритет за известными американскими и японскими брендами. Краскопульты применяют миниатюрные, например Anest Iwata W101. У нас такие применяются для небольшого ремонта – у них даже при окраске больших площадей, но это не везде. Используют и совсем уж древние модели краскопультов. Логика простая – если оборудование работоспособное, зачем его менять (фото 1).
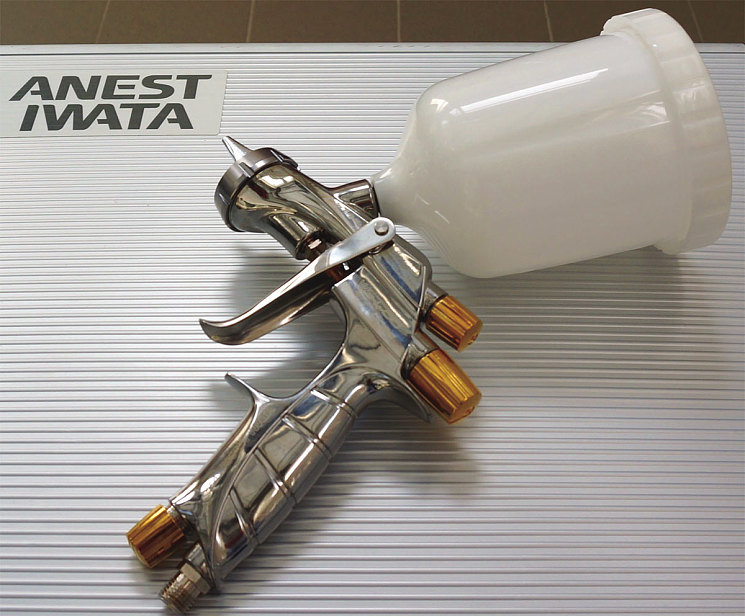
Материалы. Невооруженным взглядом заметно, что в отношении материалов экономичность – главное. Используются большие канистры на 4–16 л. Для работы с ними применяют специальные опрокидыватели. Много быстросохнущих материалов, их можно использовать при температуре внутри помещения от +5 °С.
АБС: Какие краски в почете на японском автосервисе?
Илья: Бренды ЛКМ присутсвуют разные, но в основном японские. На большинстве производств маляр – он же и колорист. Про ЛКМ предлагаю поговорить пошире. Для этого обратимся к истории. Так будет понятнее место каждого типа материала на мировых авторынках.
В Японии используют в основном сольвентные ЛКМ, доля «на водной основе» не более 5%. И связано это со следующими факторами.
В Японии нет жестких требований по обязательному использованию «воды».
«Вода» в настоящее время отстает от «сольвента» в технологическом плане: более высокие требования к оборудованию, условиям использования, хранения и транспортировки, а так же квалификации маляра. Выше и стоимость (фото 2).
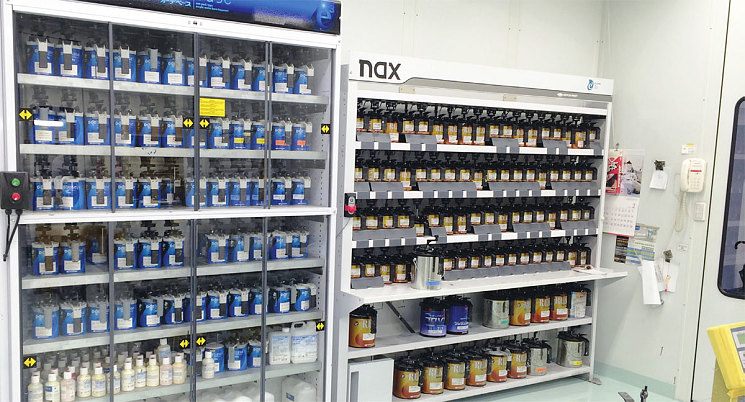
В этом смысле интересен опыт японских производителей ЛКМ, которые смогли выпустить экологичные материалы на сольвентной основе с низким содержанием VOC. Таким продуктом, например, является микс-система nax Admila Alpha концерна NIPPON PAINT, являющегося одним из лидеров японского и мирового рынка в производстве ремонтных и конвейерных ЛКМ (фото 3).
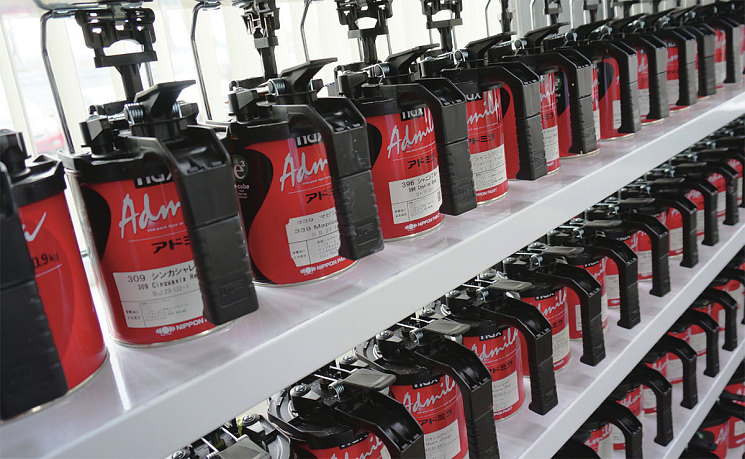
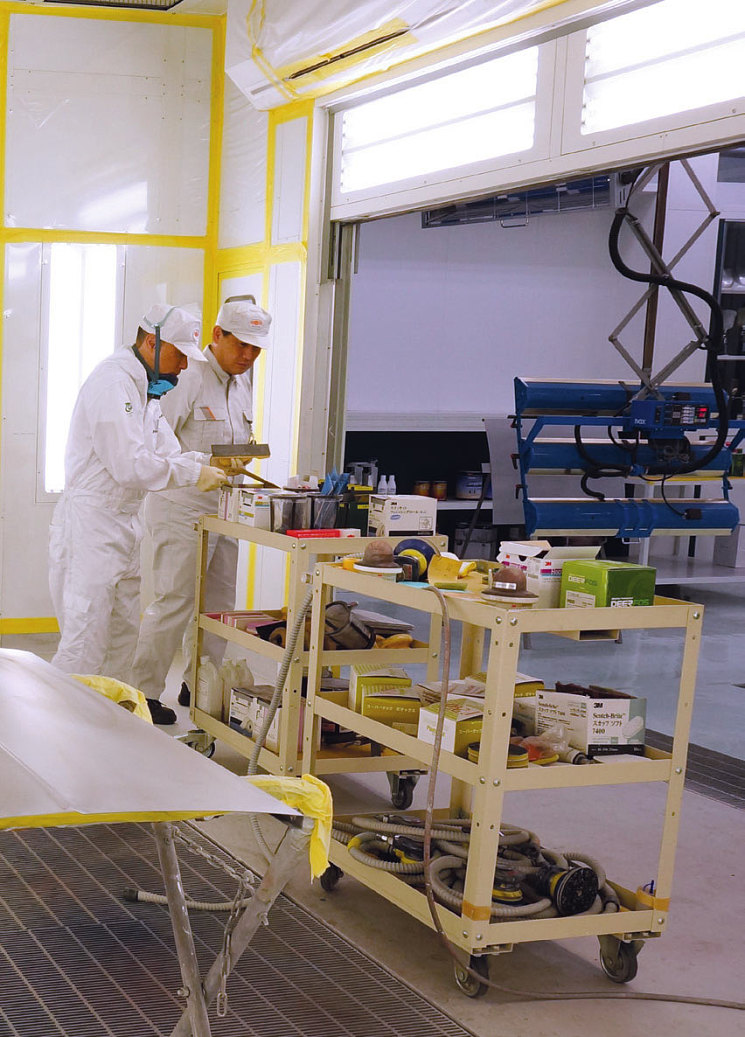
Рациональность и экономия места (дорогая земля). Окрасочные камеры (ОСК) и зоны подготовки (ЗП) оснащаются боковыми подъемными стенками, через которые завозят на специальных тележках автомобили или детали (фото 4). У нас такой тип камер крайне редок. Камеры чаще всего на газе. Режим обогрева могут и не включать, поскольку большинство японских ЛКМ рассчитаны на температуру нанесения от +5 °С и выше. Многие камеры оснащаются встроенными ИК-сушками. СТО (рабочая зона) чаще всего также не отапливается. Тепло лишь в офисе или клиентской зоне. Обогрев местный, электрический, а не централизованный.
Для полировки используют старые тяжелые вертикальные машины. В то же время есть и современные машинки как именитых мировых производителей, так и неизвестных на нашем рынке японских брендов.
АБС: А чем отличается колористика ЛКМ японских кузовных производств по отношению к нашим?
Илья: Есть и в этом различия.
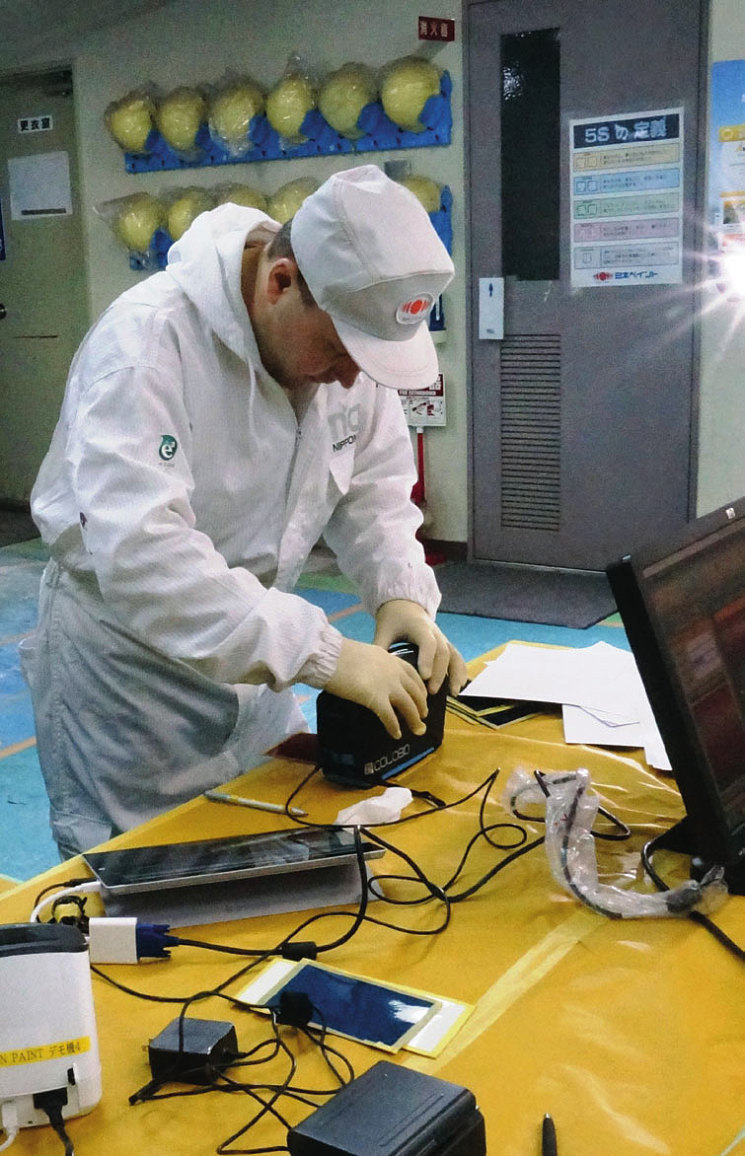
Колористика. Спектрофотометры похожи на европейские, но у японцев побогаче программное обеспечение (фото 5). В работе используют лампу колориста типа «PRO-BRIGHT» (фото 6). Для максимально точного воспроизведения дневного света в лампах используются специальный источник света, соответствующий международным стандартам. Немаловажно, что срок службы таких ламп с сохранением исходных показателей составляет не менее 6000 часов. Цветовая температура 6500 К. Конструкция лампы позволяет использовать ее в качестве мобильной спектральной установки.
Чаще применяют цветовые веера. В отличие от европейских «фан-деков» в Японии цветовой веер имеет реальное напыление, а не «типографию». Есть особенность и в применении ЛКМ. Краски и другие материалы разводят не по объему, а по массе, используя специальные весы nax Synergy Scale или им подобные с точностью «до сотых» (фото 7). Японские микс-системы, такие, например, как NIPPON PAINT – помимо достоинств ЛКМ имеют особое отношение к колористическим весами.
АБС: А какие?
Илья: Такие весы разрабатываются под оригинальный бренд ЛКМ и имеют общий с ними софт, который предоставляет расширенные возможности колористу или маляру, готовящему краску. На веерах есть специальный код, по которому можно загрузить рецепт на весы через сканер. Колористу или маляру, подобравшему по цветовому вееру нужный цвет краски, достаточно лишь поднести лепесток с картинкой кода краски к весам, и программа сама идентифицирует цвет материала.
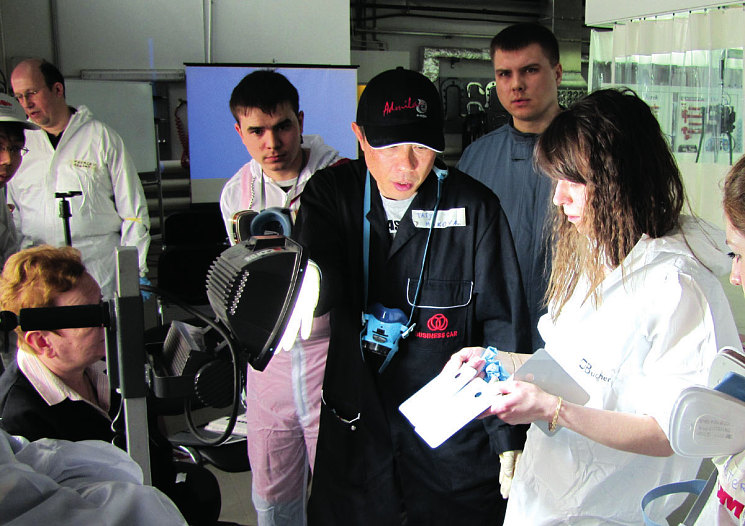
Из так называемой экзотики еще следует отметить, что наряду с привычными фильтрами заводского производства используются и «разработки» из чулочного материала. Сказать, что на всех автосервисах идеальная чистота, нельзя. Но в среднем чище, чем в большинстве наших сервисов. Стаканы одноразовые (полиэтиленовые) в специальной оправке (тоже полиэтиленовой) для смешивания ЛКМ (фото 8). Они разного размера. У нас же смешивают в банках или жестких пластиковых стаканах. По эргономике производства стоит поговорить отдельно и не сегодня. Япония, как страна, давшая миру многое в этой области, не обошла своим вниманием и независимый автосервис.
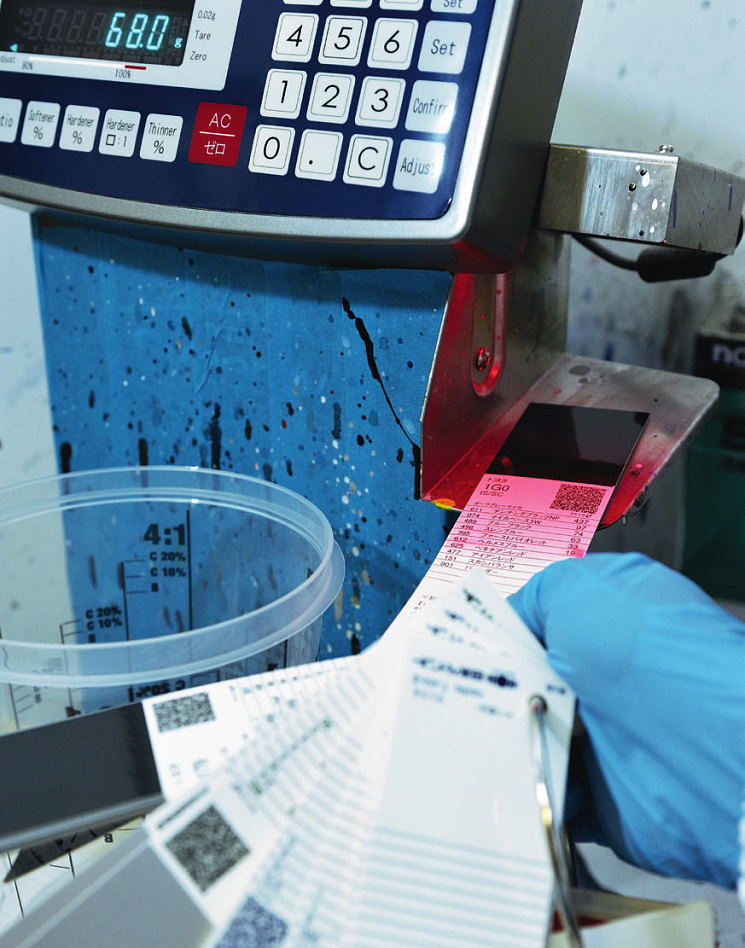
Охрана труда. Работают ВСЕГДА в комбинезонах, респираторах, перчатках (фото 9). Есть специальный шкаф, где хранятся каски на случай землетрясения.
Квалификация сотрудников (маляров). Из вышесказанного вы можете сделать вывод, что производство «провоцирует» экономить на квалификации персонала, но это совершенно не так! В Японии принято обязательно проходить обучение в специализированых УЦ (как правило, при заводах, производящих ЛКМ), и «повышать» квалификацию с определенной периодичностью.
Причем в отличие от нашего рынка, где для клиентов (потребителей краски) производитель или импортер проводит обучение бесплатно, все курсы в Японии платные.
АБС: А это плохо или хорошо?
Илья: Имея достаточный опыт работы в данном бизнесе, могу с уверенностью сказать – для повышения эффективности обучения, ответственности обучаемого и ожиданий работодателя – это положительный опыт. Но, к сожалению, наш рынок сейчас к этому не готов…
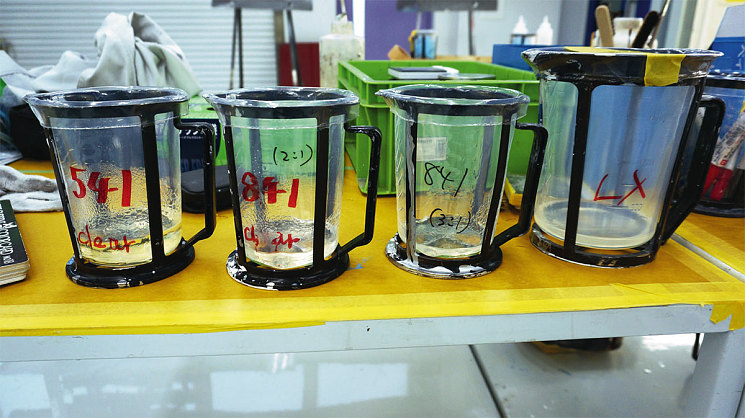
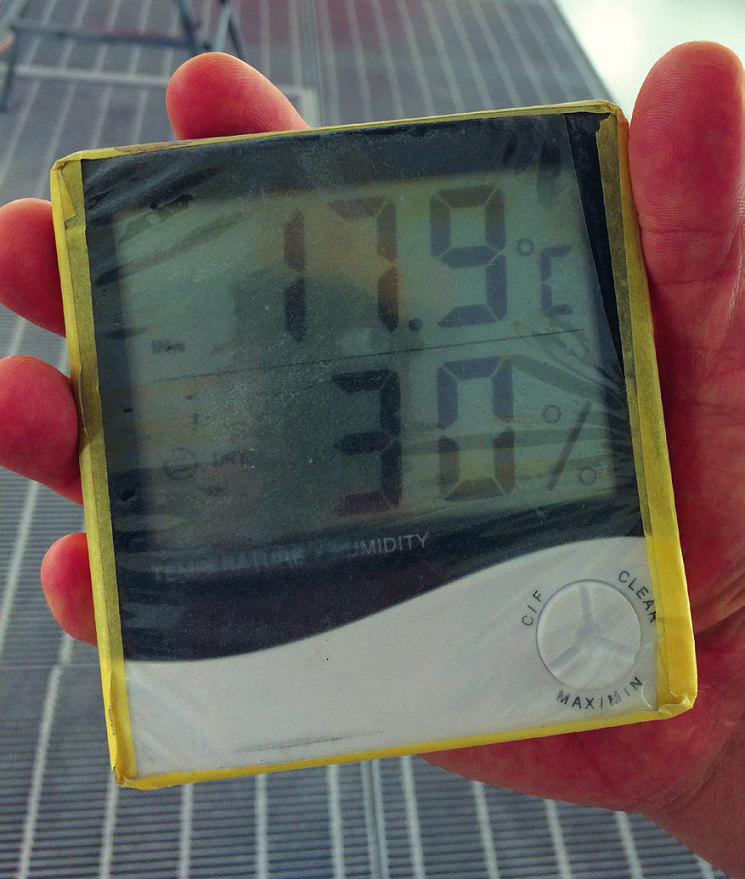
При минимальных площадях, отданных под кузовное производство, ремонт кипит вовсю, причем никто никому не мешает, а все перемещения как людей, так и объектов ремонта происходят в спокойном расчетливом режиме (фото 10). Ремонтируемые автомобили расставлены, кажется, идеальным образом: удобным для ремонта и простым для перемещения. Кайдзен в действии! При ремонте гораздо большее предпочтение отдано рихтовке детали, а не как у нас – ее замене. В кузовном ремонте значительно превалирует количество независимых автосервисов. Значительно!
Теперь, вероятно, нужно подытожить. Сказать, что все увиденное повергло нас в шок, не могу. Как и говорил, по большому счету японские автосервисы мало отличаются от наших, российских. Но при более внимательном анализе увиденного приходишь к мысли, что эти различия как раз и говорят о зрелости бизнеса. О его высоком уровне, когда органично переплетены несколько основополагающих факторов. Это забота о здоровье персонала, эргономичность в организации всего и вся на автосервисе и мудрая расчетливая практичность. Для нашего рынка такая организация может трактоваться как инновационность.
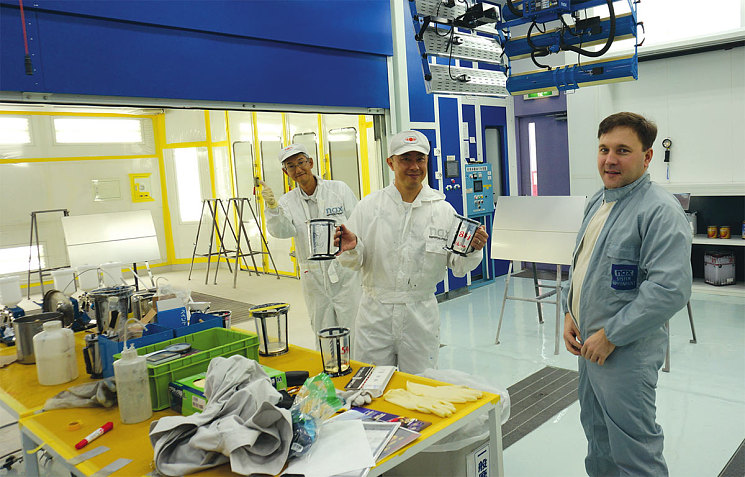