Там, в Вестфалии, где делают кольца
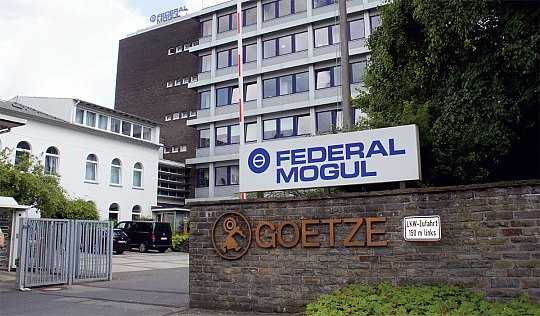
Ну и денек
Материалы и технологии, применяемые при создании двигателей, таят немало резервов для повышения топливной экономичности автомобиля и снижения эмиссии отработавших газов, в частности, выбросов CO2. Мы знаем, как использовать эти резервы! Таков был лейтмотив пресс-конференции Federal-Mogul, проведенной 4 июля на заводе Goetze в Буршайде, пригороде Кёльна.
На этой международной встрече, официально именуемой «День технологий», говорилось о многом: о тенденциях и концептуальных решениях в моторостроении, новых конструкциях и способах изготовления поршней и поршневых колец; гильз и вкладышей; клапанов и клапанных седел; поршневых втулок и пальцев; свечей и прокладок. А еще – о новых конструкционных материалах. О методах испытаний и компьютерном моделировании. О прикладных исследованиях и маркетинге.
Семь базовых докладов, сессия вопросов и ответов, экскурсии по цехам завода, неформальное общение в перерывах... Расскажем о некоторых наиболее важных темах, прозвучавших на форуме.
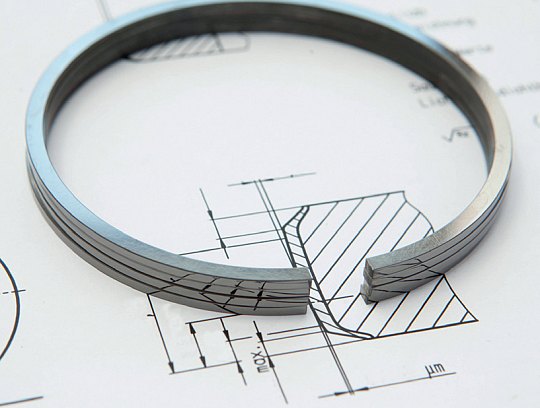
На ринг вызываются...
Побывав на заводе Goetze, логично начать разговор с поршневых колец. От этих «посредников» между поршнем и гильзой в немало степени зависят экономичность ДВС, его мощность и экологичность.
Точнейшая геометрия для сопрягающей посадки поршня в цилиндр, стойкость к непрерывно растущим температурам, давлению, динамическим нагрузкам, минимизация трения и износа сопрягаемых пар – все это лежит на них, кольцах. А значит, они тоже требуют инновационных решений и прецизионных технологий.
Goetze® – «старейшина» в семействе автомобильных компонентов. Как никак, его родословная ведется с 1887 года. И первое в Европе хромированное поршневое кольцо было именно этой марки.
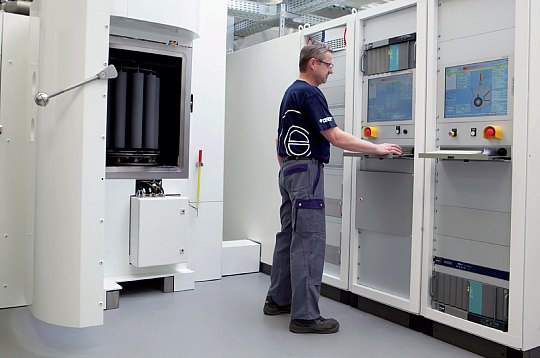
Чем порадовал бренд после вхождения в состав Federal-Mogul? Об этом и многом другом рассказал руководитель технологического подразделения по кольцам и гильзам компании Federal-Mogul Powertrain д-р Стеффен Хопп (Steffen Hoppe).
Нормативы стремительно стареют, и технологии просто обязаны опережать их. Всем известный пример: топливо, служившее естественным смазочным материалом, перестает быть таковым. Причина в резком снижении содержания серы в угоду экологическим показателям. Значит, сегодняшние поршневые кольца обязаны работать при меньшем количестве смазки. И это при непрерывном росте мощности, снимаемой с единицы объема двигателя.
Эти и многие другие противоречия на предприятиях Federal-Mogul разрешают более 200 ученых, инженеров и других специалистов, занимающихся разработкой и тестированием поршневых колец. Работа ведется по нескольким направлениям. Магистральными являются два: совершенствование геометрии и разработка новых материалов, в том числе покрытий.
По кромочке
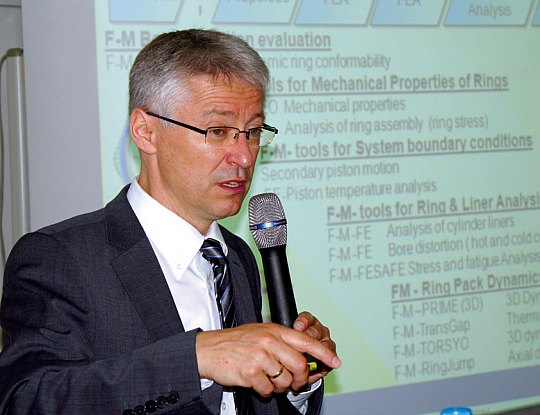
Говоря об оптимизации геометрии маслосъемного кольца, нельзя не вспомнить изделие Goetze LKZ-Ring. Это кольцо имеет особую ступенчатую конструкцию рабочей кромки, снижающую насосные потери в такте сжатия. А вот в такте расширения масло со стенки цилиндра мгновенно сбрасывается в картер – причем это происходит гораздо эффективнее, чем при использовании стандартного кольца.
В результате масло в камеру сгорания не попадает, нагар на свечах не образуется, а само масло не угорает. В цифрах это выглядит так: в сравнении с «коллегами» кольцо LKZRing снижает расход масла до 50%, а трение – до 15%.
Изначально инновационное кольцо LKZ-Ring создавалось для требовательного дизеля, а сейчас используется и в бензиновых двигателях с непосредственным впрыском топлива.
В 2011 году компания Federal-Mogul получила за него награду PACE.
А вы его покройте
Покрытия – почему они так важны? Дело в том, что требования к свойствам основного материала кольца и его поверхностного слоя сильно отличаются. Основной материал обеспечивает прочность и термостойкость, а «пограничник» минимизирует трение и износ – как самого кольца, так и сопрягаемых пар.
Начнем с хромокерамического покрытия, по стандартам компании именуемого CKS. Оно было разработано специально для дизелей с целью повышения долговечности цилиндропоршневой группы. Результатом явилось снижение износов колец и стенок цилиндров, а также отсутствие задиров.

А потом наступила эпоха алмазных покрытий. Напомним, что алмаз – одна из форм углерода, у них даже химическая формула одинаковая – С, просто С. Такие вещества называют аллотропными. Поэтому в литературе иногда встречается термин «алмазно-углеродное покрытие».
Так вот, следующим шагом стало создание Goetze Diamond Coating – сокращенно GDC. Слово Diamond говорило само за себя. Использование частиц технического алмаза позволило в 4 раза превысить ресурс стандартного хромированного покрытия, и в 2 раза – соответствующие показатели хромокерамического. А главное, это решение открыло новые перспективы для создания следующего поколения компактных, но мощных дизелей.
Потом появилось покрытие третьего поколения, названное CarboGlide. Здесь уже формировалась многослойная алмазная структура, модифицированная особым композитом, содержащим вольфрам и другие ингредиенты. CarboGlide позволил отыграть 18–20% потерь на трение и обеспечивал более толстый, до 10 мкм, защитный слой.
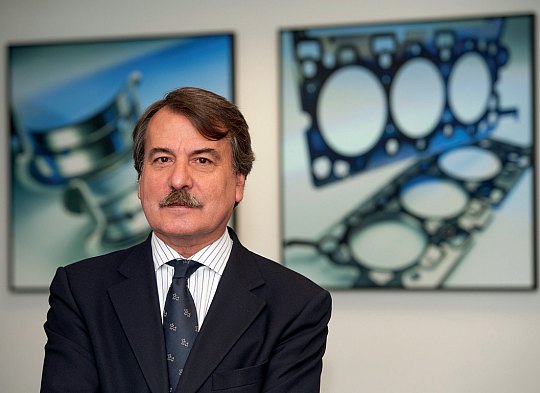
Но оказалось, что это еще не все...
И тут появился DuroGlide
Новейшая технология покрытия поршневых колец, разработанная Federal-Mogul – это DuroGlide. Она объединила два инновационных решения – по «архитектуре» слоя и методу его нанесения.
Здесь тоже используется многослойная структура с применением молибдена и «хитрых» композитов. В основе покрытия – комбинация алмазно-графитовых ингредиентов и некристаллического (аморфного) углерода.
Покрытие обладает, казалось бы, противоречивыми свойствами – и все благодаря аллотропным «зеркалам» углерода. С одной стороны, это высокая твердость и стойкость к износу – кстати, в сравнении даже с лучшими покрытиями она увеличилась вдвое.
Что, впрочем, неудивительно – ведь доля алмазной составляющей возросла на 50%. С другой стороны, этот слой улучшает смазываемость поверхностей и действует как физически и химически инертный барьер, предотвращающий непосредственный контакт сопряженных поверхностей в режиме граничной смазки.
Слой стал гораздо большей толщины – до 20 мкм. Для такого рода покрытий необычайно много. Не будет ли отслоения? Не будет, уверяют разработчики. Дело в том, что нанесение покрытия производится комбинированным способом – оптимальным сочетанием конденсации из паровой фазы (PVD – physical vapour deposition) и плазменного осаждения.
В ходе испытаний кольца с покрытием DuroGlide продемонстрировали уникальную долговечность, обеспечив уменьшение расхода топлива на 1,5% – для легковых автомобилей это означает снижение выбросов CO2 на 3 г/км.
Новая литейная технология выполняет подачу литейного расплава непрерывно и равномерно, обеспечивая однородное распределение графита в структуре чугуна. А комплексный контроль гарантирует одинаковые скорости заливки и оптимальное заполнение форм колец, что она способна принести на алтарь снижения вредных выбросов? Оказывается, немало.
«Поскольку трение в двигателе можно снизить за счет использования более тонких поршневых колец, требуется изготавливать кольца из более прочных материалов, которые обеспечивают необходимое сопротивление изгибу, – говорит д-р Стеффен Хопп. – Для этого мы разработали новые материалы, а также процессы литья и методы их моделирования».
Теперь конкретно. Можно отливать кольца методом стопочной заливки, когда несколько литейных форм располагаются горизонтально одна над другой. Это усложняет конструкцию литниковой системы, поскольку давление и скорости заливки расплава различаются на разных уровнях стопки. Кроме того, использование неразъемных литейных форм ограничивает число типоразмеров продукции.
Federal-Mogul преодолела указанные трудности, внедрив автоматизированный процесс вертикального литья. В нем используются особые литейные формы, позволяющие варьировать конструкцию литниковой системы в зависимости от конфигурации и габаритов отливки, а кроме того, оптимизировать движение расплава.
В итоге однородность распределения графита в структуре серого чугуна существенно улучшилась. А полная автоматизация литейных операций с непрерывным контролем процесса обеспечила, во-первых, одинаковые скорости заливки; во-вторых – улучшение заполнения формы. Результатом явилось более высокое качество отливок поршневых колец. И прежде всего увеличение прочности – в том числе и на изгиб.
Для усовершенствования процесса вертикального литья специалисты Federal-Mogul разработали принципиально новый метод моделирования литейных процессов – Slow Motion Casting Simulation (SMCS). Перевести можно так: «Моделирование литья методом замедленной съемки». SMCS обеспечивает непрерывное и очень точное отслеживание поведения расплава при разных температурах и скоростях заливки.
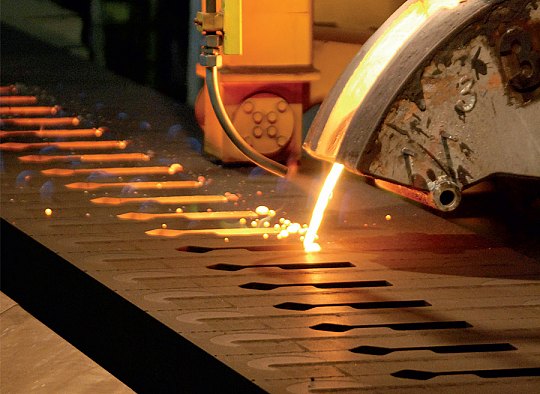
И несколько слов о материалах для отливки изделий. Обычно для изготовления поршневых колец дизелей используется высокопрочный мартенситный серый чугун с шаровидным графитом. Он достаточно пластичен и имеет предел прочности (временное сопротивление) около 1200 МПа.
Новый литейный стальной сплав GOE70, разработанный инженерами корпорации, имеет мартенситную основу с включениями карбида хрома и может похвастать пределом прочности не менее 1800 МПа.
Подвергнутый азотированию, этот материал приобретает высокую износостойкость и твердость поверхности по Виккерсу 1300 HV.
Поршневые кольца, изготовленные из GOE70, прошли серию испытаний в тяжелонагруженных дизелях, показав исключительно низкий износ – как собственного «тела», так и боковой поверхности гильз. И все это на фоне уменьшенного прорыва газов в картер и пониженного расхода масла.
Серийное производство таких поршневых колец началось в 2012 году. Двигатели, в которых они трудятся, отвечают требованиям стандарта токсичности отработавших газов Euro VI.
С каналом охлаждения
Но не кольцами едиными... Подразделение Federal-Mogul Powertrain представило на пресс-конференции инновационные поршни Elastothermic для компактных бензиновых двигателей нового поколения.
Основой для их создания послужили известные поршни Elastoval для бензиновых двигателей, конек которых – уменьшенная масса и низкие показатели трения.
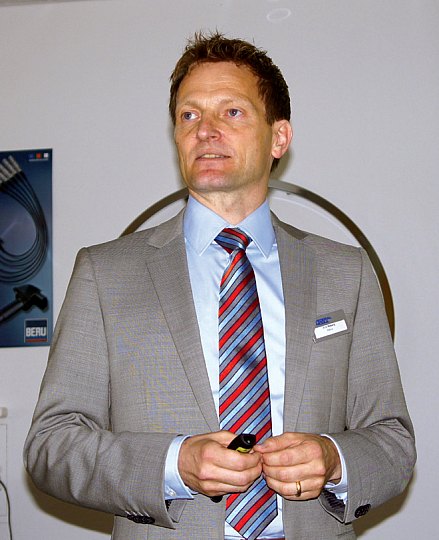
Теперь эти преимущества усилены и дополнены: поршни Elastothermic обрели высоко расположенный канал охлаждения. Такая конструкция позволяет уменьшить температуру днища поршня, благодаря чему снижается риск детонации – особенно в теплонапряженных двигателях.
Показательный пример: температура канавки первого кольца в поршнях Elastothermic была уменьшена на 60°C, опустившись ниже 250°C. Это позволяет: избежать образования нагара и залипания колец; уменьшить расход масла; улучшить компрессию.
Кроме того, более низкая рабочая температура обеспечивает повышенную стойкость к образованию задиров на гильзе, благодаря чему можно использовать более жесткие допуски. А уже упоминавшееся снижение риска детонации позволит не беспокоиться об износе и деформации канавки первого кольца.
Вывод весьма оптимистичен: используя эти поршни, производители автомобилей могут увеличить удельную мощность и степень сжатия без снижения эксплуатационных характеристик и долговечности двигателя.
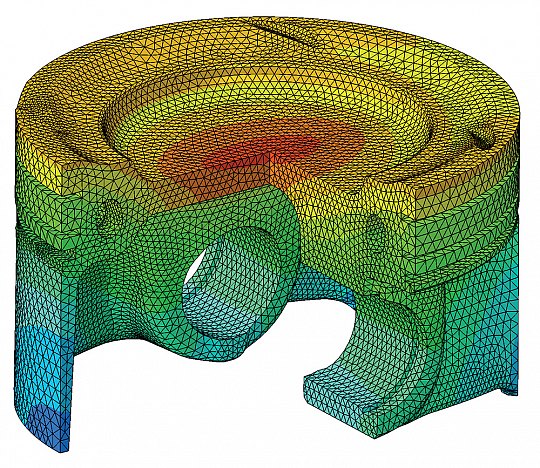
И они, производители, это отлично поняли! Автомобильные компании в Северной Америке, Европе и Азии уже сейчас проектируют двигатели с поршнями Elastothermic. Новые поршни созданы в конструкторскоисследовательском центре Federal Mogul в Нюрнберге, а их производство начнется уже в этом году. И это не все новости по Elastothermic: корпорация Federal-Mogul представит данную технологию на выставке IAA, которая пройдет во Франкфурте с 10 по 13 сентября сего года. То есть совсем скоро.
Москва – Дюссельдорф – Буршайд – Москва