Главная деталь сцепления. Историко-технологические заметки
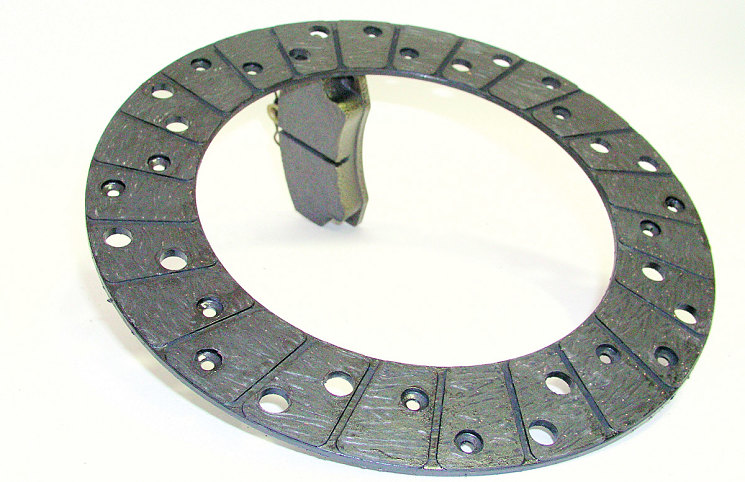
Не просто момент
Как известно, сцепление служит для временного отсоединения силовой передачи от двигателя. Когда сцепление включено, оно передает… крутящий момент двигателя? Не совсем так.
Вот простой пример – стоящий автомобиль. Чтобы стронуть машину, необходимо преодолеть силу трения покоя. Ведомый диск вынужден передавать так называемый момент трения сцепления. А он может существенно превышать крутящий момент, передаваемый при движении, – и узел обязан эту нагрузку выдерживать. Главная роль здесь принадлежит фрикционным накладкам сцепления.
Какие бывают накладки
По способу изготовления накладки классифицируются следующим образом:
- формованные из массы;
- картонно-бакелитовые (прессованные из картона) со специальной пропиткой;
- тканно-бакелитовые, получаемые из текстильной ленты с пропиткой;
- спирально-навитые, получаемые из армированной нити с пропиткой;
- эллипсонавитые, также получаемые из армированной нити, но уложенной иным, более рациональным способом.
В чем же преимущества того или иного способа? Если рассматривать стоимость, то наиболее дешевыми получаются накладки первых трех групп.
Но появление высокооборотных двигателей повысило требования к динамической прочности накладок. Ясно, что современный автомобиль, набирающий большую скорость за считанные секунды, должен иметь сцепление, защищенное от «разноса».
Этому явлению лучше всего противостоят накладки четвертой и пятой групп. Каркас из нити, армированной латунной или медной проволокой и связанный специальным составом, прекрасно справляется с инерционным нагрузкам. Об этом – в следующих разделах.
По спирали
В свое время российские заводы закупили в Германии технологию изготовления накладок сцепления из пропитанной нити, армированной латунной или медной проволокой. Суть в следующем: на специальном станке навивалась бобина – дорн. После соответствующей термообработки дорн подобно колбасе разрезался на кольца – полуфабрикаты будущих накладок. А поскольку нить укладывалась по спирали, эти изделия так и назывались – спирально-навитые.
Они противостояли «разносу» намного лучше формованных, но и здесь нашлась своя ложка дегтя: нить, арматура будущей накладки, оказывалась многократно перерезанной в плоскости, перпендикулярной оси дорна. Поэтому изготовители накладок перешли к индивидуальной спиральной навивке каждой накладки.
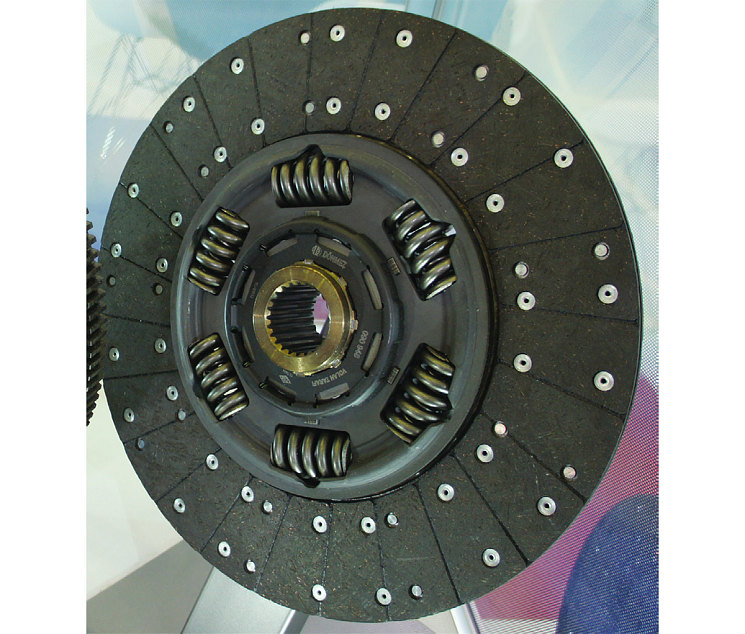
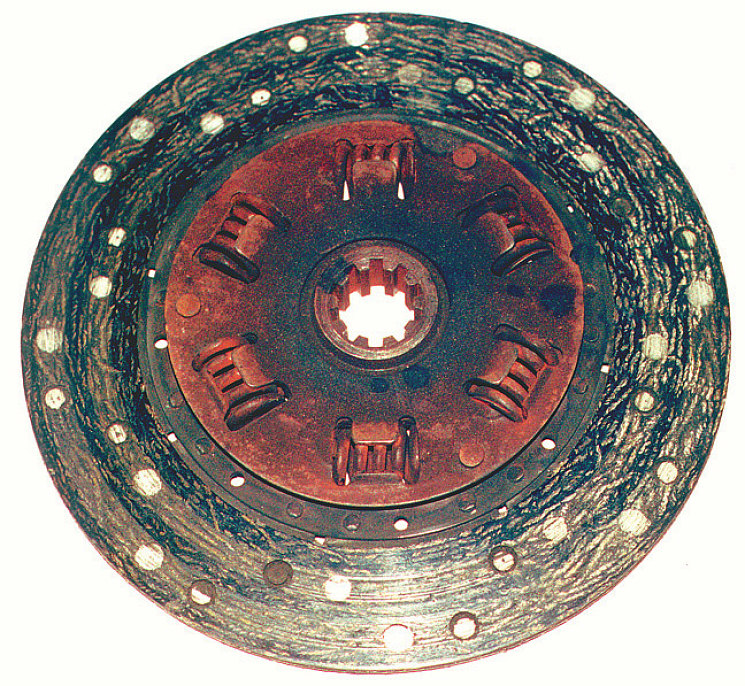
Эллипс и синус
Потом выяснилось, что и спирально-навитые накладки панацеей не являются. Требования к стабильности веса, равномерности износа накладки и контртела (маховика и нажимного диска), переход на безасбестовые ингредиенты и ряд других условий заказчиков привели к внедрению иного, более совершенного способа укладки нити – по дуге эллипса, направленной от внутреннего кольца накладки к внешнему.
При изготовлении детали тарелка навивочного станка вращалась – да так, чтобы при повороте на 360° нить не ложилась на нить. Тем самым достигалась равномерная плотность укладки, а значит, и прочность изделия. Накладки, полученные таким способом, назвали эллипсонавитыми. Эта технология стала господствующей, а потому будем говорить о ней в настоящем времени.
При изготовлении накладок среднего и большого диаметра (например, для дизельных двигателей грузовиков) применяют более «хитрый» способ укладки нити: по синусоиде, «бегающей» между внутренней и внешней окружностями кольца. Нить при этом укладывается еще более равномерно.
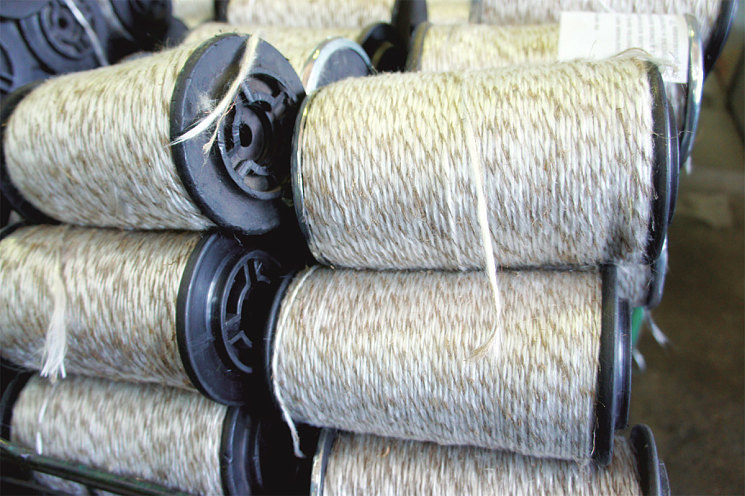
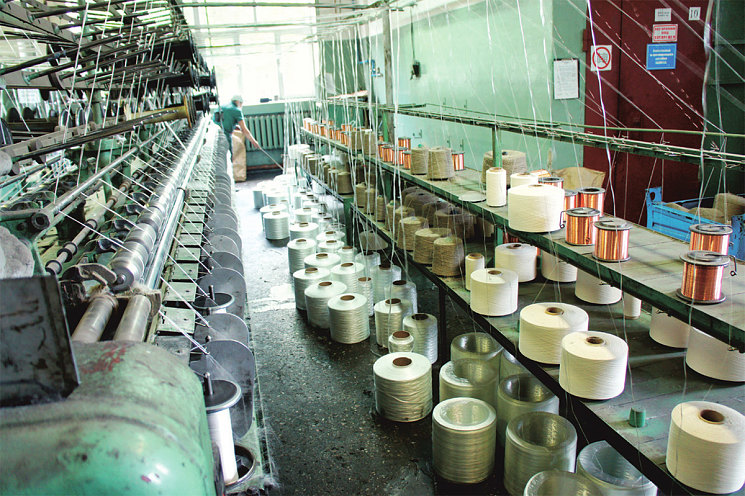
Эллипсонавитые изделия (к ним относят и «синусоидальные») позволили исключить возникновение кольцевых трещин, усреднили кольцевые износы и вылечили многие другие болезни, присущие спирально-навитым накладкам.
Сегодня все производители накладок, как российские, так и зарубежные, выпускают эллипсонавитые изделия. Они легко узнаваемы по характерному рисунку фрикционной поверхности (см. нижнее фото на с. 37).
Об отверстиях
Накладкам необходимы отверстия для крепления. Они должны делаться строго по чертежу предприятия, собирающего узел сцепления.
Отверстия бывают двух типов: под заклепки, с утопленной площадкой (заплечиком) для шляпки, и технологические, для работы с заклепками противоположной накладки.
Однако заводы, выпускающие накладки, изготавливают их как с отверстиями, так и без оных. Дело в том, что многие заказчики, автомобильные и моторные заводы, хотят выполнять эту операцию сами.
Отверстия можно получать тремя способами: закладывать в конструкцию пресс-формы, пробивать специальным штампом или сверлить. Понятно, что изготовитель накладок может применять любой из перечисленных способов, а заказчик (автозавод или ремонтное предприятие) – лишь второй или третий.
На большинстве предприятий отверстия сверлят на многопозиционных станках. Этот метод обеспечивает отменную точность, да вот беда: нить при сверлении перерезается, уменьшая прочность накладки. Поэтому ведущие заводы применяют технологию получения отверстий на стации прессования накладок.
То, что нить при этом остается целой, само собой. Но это еще не все: данная технология позволяет уменьшить толщину заплечиков и увеличить ресурс изделий до контакта заклепок с нажимным диском или маховиком.
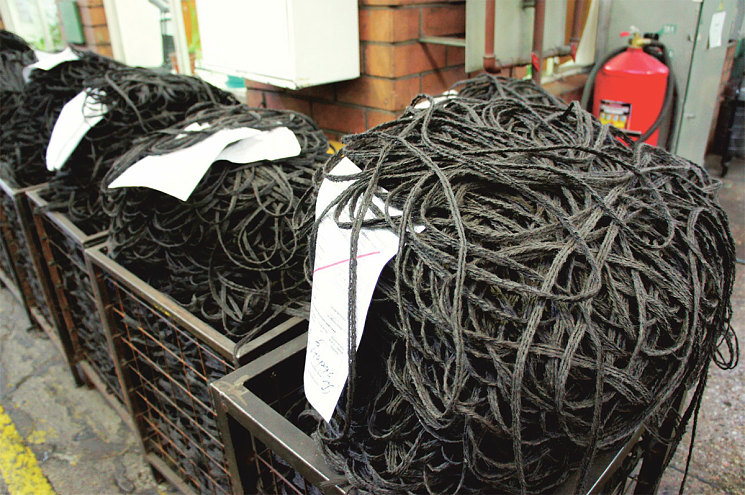
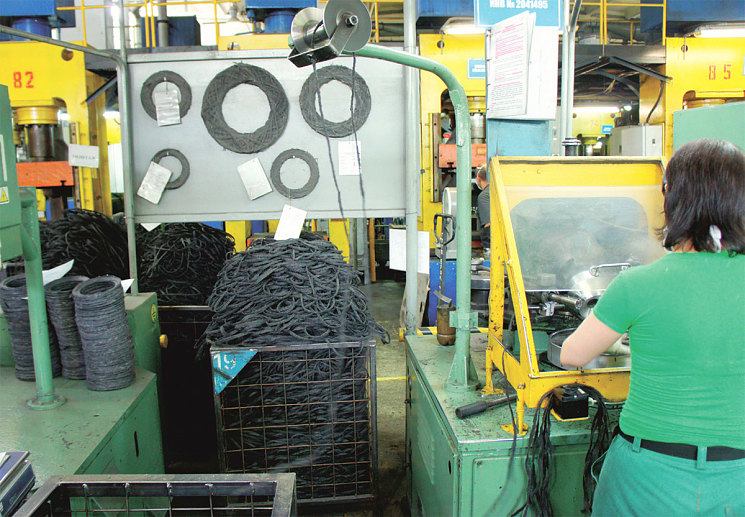
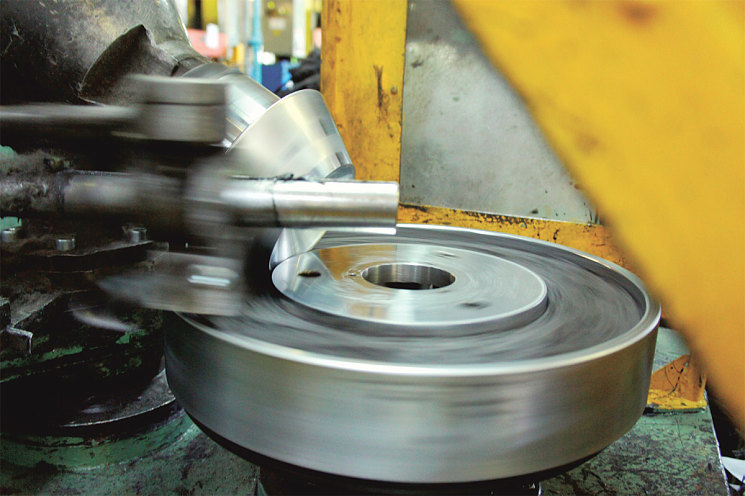
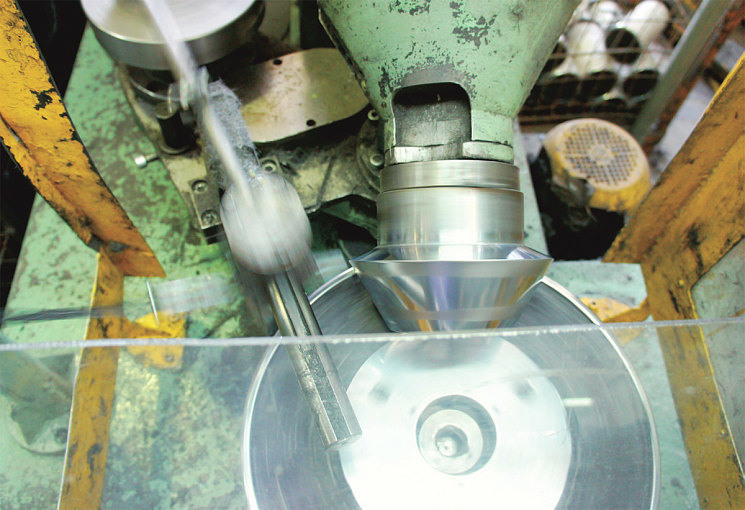
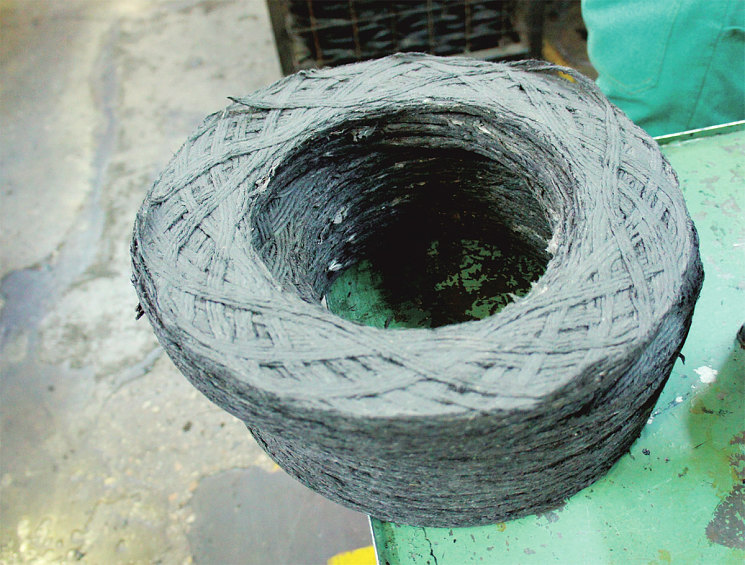
О канавках
Канавки на поверхности накладок – зарубежное изобретение. Считается, что они служат для отвода тепла и удаления продуктов износа на периферию. Линии канавок располагаются, как правило, по хордам, под некоторым углом к радиусу кольца. Они имеют форму отрезка прямой или дуги малой кривизны. Такая конструкция канавки несколько компенсирует потерю прочности накладки.
Канавки получают непосредственно в прессформе. Если внимательно посмотреть на канавку, то около края накладки можно заметить перекрывающий буртик – это след выхода фрезы при изготовлении прессформы.
Этот буртик может препятствовать отводу абразива, то есть играть роль, противоположную требуемой, и его следовало бы удалять. Но на практике этого никто не делает.
Да и споры на тему «нужны ли нам канавки» не закончены до сих пор. Судите сами – глубина канавки гораздо меньше глубины шляпки заклепки. Канавка полностью истирается, когда накладка вырабатывает 30–50% своего ресурса, после чего сцепление работает со сплошным диском. А увеличить глубину канавки нельзя – это резко уменьшит прочность накладки.
Поэтому накладки выпускают и с канавками, и без оных. Последний вариант удешевляет как пресс-формы, так и сами изделия.
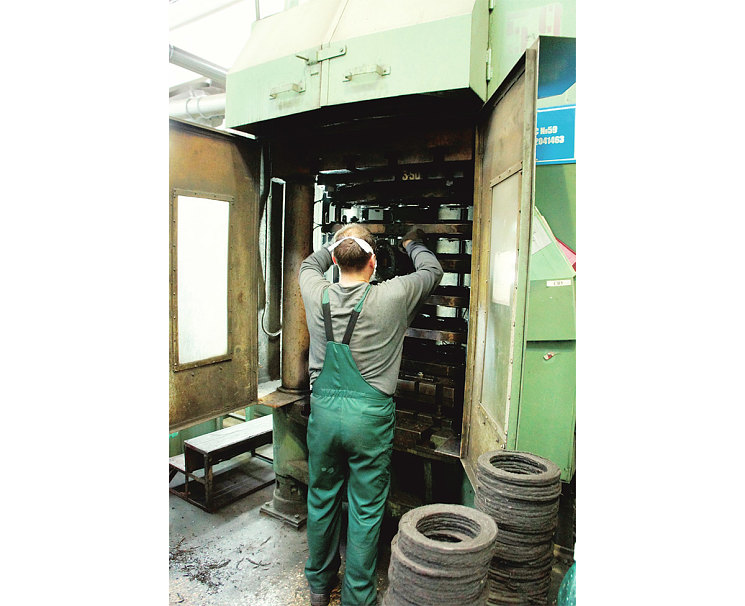
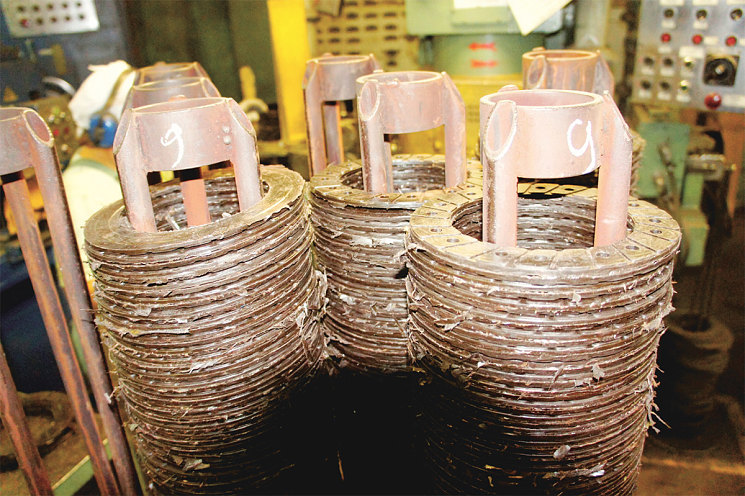
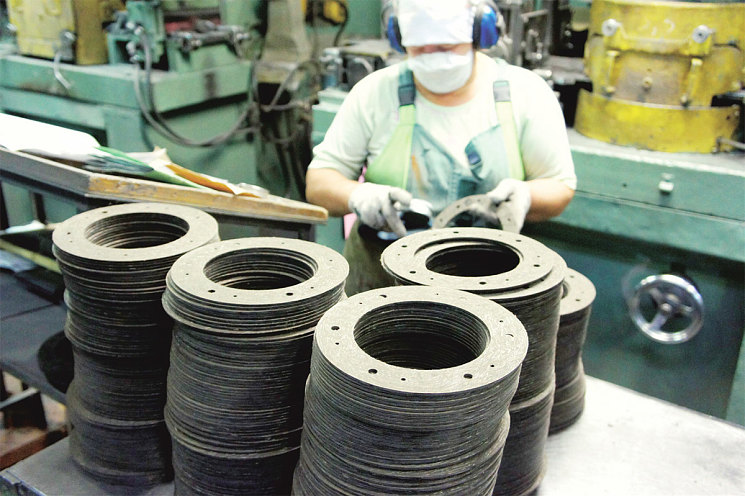
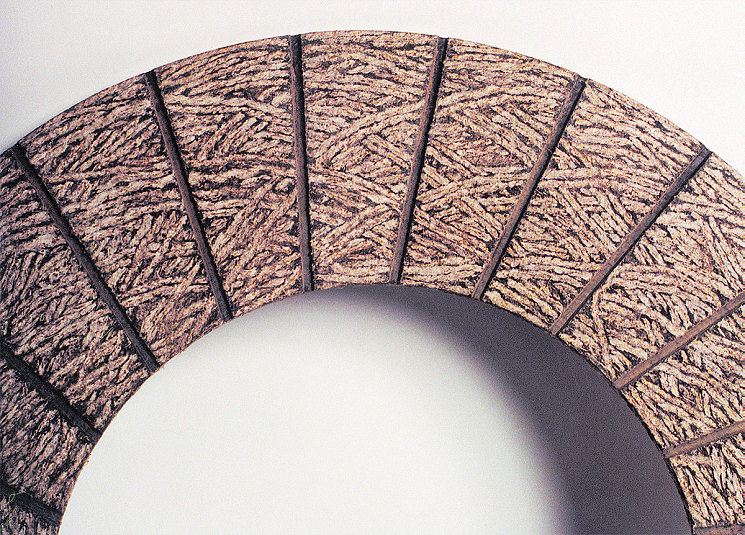
Об автозаводах
Кроме общих, формальных требований к накладкам сцепления у автомобильных и моторных заводов есть и собственные, индивидуальные.
Так, АВТОВАЗ во главу угла ставит комфортность движения, в частности обеспечение плавности при трогании и отсутствие вибраций. Ульяновский автозавод, «военная косточка», предъявляет повышенные требования к температурным характеристикам, а Ярославский моторный требует от накладок передачи большого крутящего момента на сравнительно небольшой площади трения.
О ресурсе
Сколько служат накладки сцепления? Эта величина оговорена в нормативной документации в форме так называемого гамма-процентного ресурса. Но нам с вами привычнее километры. Так вот: АВТОВАЗ требует от изготовителей накладок ресурс 160 тыс. км, за рубежом производители сцепления называют 150 тыс. км пробега.
Доводить сцепление до запредельного износа не следует – при уменьшении толщины накладок начинают работать торцы заклепок. Это приводит, как правило, к пробуксовке сцепления и к появлению кольцевой выработки на контртеле.
Перенаклепка накладок на бывшем в употреблении ведомом диске, по мнению специалистов, восстановит его работоспособность лишь на 80%. Ведь многие другие детали, и прежде всего демпфирующие пружины, уже будут «усталыми». Поэтому лучше менять диск в сборе. И разумеется, он должен быть с фрикционными накладками от надежного производителя.
В статье использована информация АО «ТИИР»