KANSAI PAINТ. Преимущества японских ЛКМ
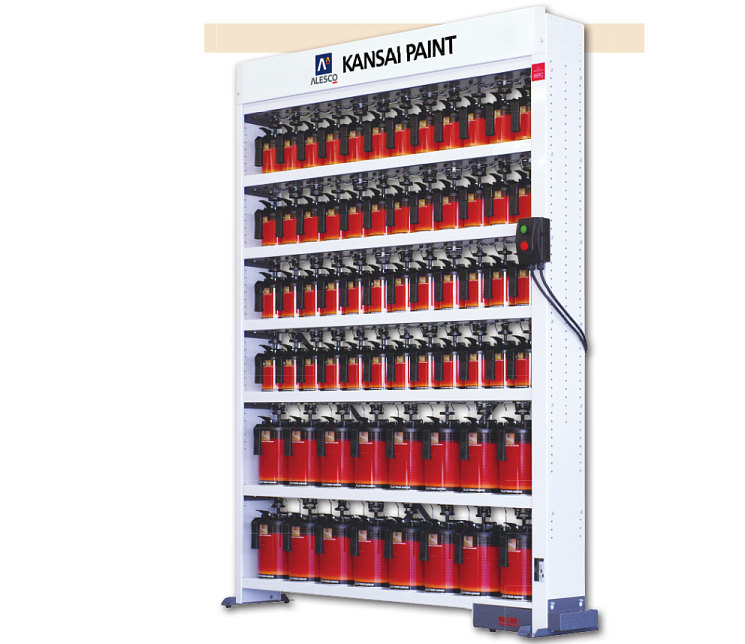
Рынок лакокрасочных материалов (ЛКМ) России переполнен всевозможными брендами, в том числе недорогими. И каждый производитель убеждает нас в достойном качестве своей продукции.
В действительности произвести ремонт автомобиля можно любыми лакокрасочными материалами, и при этом результат работы первое время будет удовлетворять как исполнителя, так и клиента. Но так называемая просадка материала, помутнение, отслоение финишного покрытия, появление сколов, возможное изменение цвета и прочие «подводные камни» такого кузовного ремонта проявятся уже в первые месяцы эксплуатации автомобиля, даже при том, что осуществлял ремонт профессиональный работник, который строго соблюдал технологию проведения лакокрасочных работ.
В итоге сервисмены теряют время на устранение недостатков и несут дополнительные затраты на ЛКМ. А как возместить потерю деловой репутации? Поэтому ремонт с использованием бюджетных лакокрасочных материалов не всегда приводит к удешевлению кузовного ремонта и желаемому результату. По статистике, после негативного отзыва не менее десяти человек отказываются делать кузовной ремонт на таком автосервисе, а каждый довольный клиент передает положительный отзыв о ремонте трем своим знакомым. Выбор за вами!
Известно, что Япония в мире занимает лидирующие места в различных отраслях промышленности. Производство лакокрасочной продукции не является исключением. Японские мастера по своему менталитету трудолюбивы и ценят каждую минуту рабочего времени. Поэтому их лакокрасочные материалы обладают соответствующими характеристиками. В кузовном ремонте авторынка Японии нет определений «бюджет» и «премиум», а есть одно понятие – «качество». Оно безупречно и конкурентоспособно на мировом рынке кузовного ремонта.
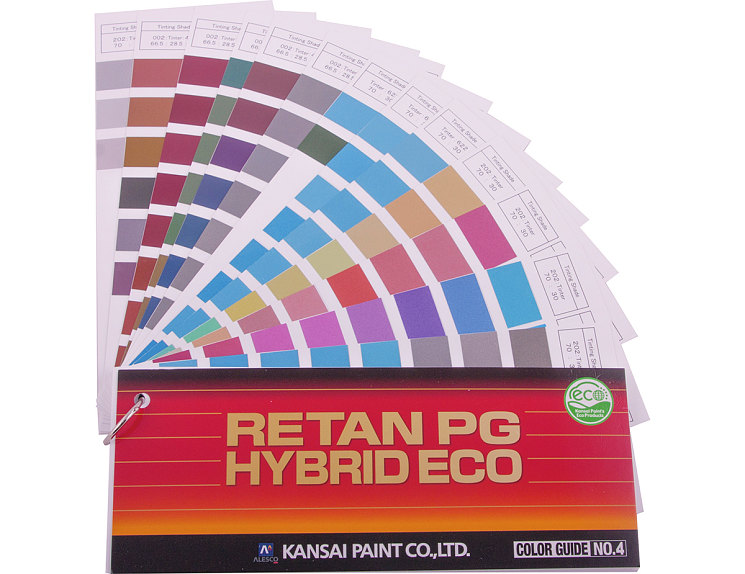
В любом ремонте всегда присутствует человеческий фактор. Ведь работу выполняют люди, а не роботы, и им свойственно ошибаться. При использовании в работе японских лакокрасочных материалов KANSAI PAINТ эти ошибки практически сводятся к нулю. Таким материалам не обязательна межслойная выдержка, они не дают усадки, не боятся обдува воздухом и перепада температур, материал можно наносить на ремонтное покрытие любой толщины. При этом результат ремонта будет гарантированно замечательным.
Важно только соблюдать технологию при разведении лакокрасочных материалов и подготовке поверхности к ремонту. ЛКМ выдерживают температуру до –45 °C, а взаимодействие с отвердителем начинается при температурах от +5 °C.
Также немаловажны такие показатели, как расход материала и время сушки лакокрасочного покрытия. К примеру 1,5-слойный лак Retan PG Eco HS Clear (Q) сохнет при 60 °C всего 8 минут, а при 20 °C его сушка составляет 1,5 часа. И все это до полировки. Расход лака на деталь площадью 0,54 м2 составляет 90–100 грамм готовой смеси.
Если эти показатели перевести в деньги, учитывая при этом сокращения сопутствующих расходов на электричество, топливо для ОСК, на время покрасочного цикла, – получается заметная экономия до 30–40%.
Попытаемся сравнить японские и европейские системы подбора красок. Сделать это будет крайне сложно, так как какие-то компоненты будут схожими во всех системах подбора, а какие-то – абсолютно разными. А вот если сравнивать не системы подбора, а подходы производителей ЛКМ к бизнесу и партнерству, можно заметить следующее.
В программах для изготовления красок есть формулы, обозначающие конвейерную краску (ОЕМ). В японских ремонтных системах подбора компоненты, присутствующие в формулах, изготовлены абсолютно из того же сырья (цветовые пигменты, металлики, перламутры и проч.), что и те, из которых изготавливается краска для конвейерных производств. Отличия могут быть только в связующем, так как в ОЕМ другой способ нанесения продукта. Но сами пигменты – высшего качества, причем аналогичные ОЕМ.
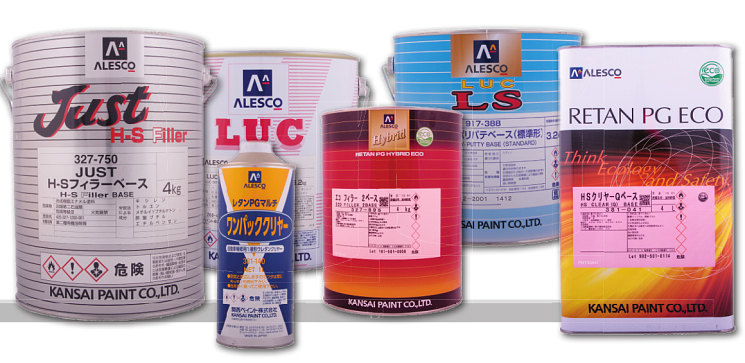
Мало того, Европа изобилует так называемыми бюджетными линейками – в основном от производителей дорогого сегмента. В Японии такой практики не существует и конкуренция идет скорее по качеству, нежели по удешевлению конечного продукта.
Теперь немного о компонентах систем подбора.
Основной черный компонент в европейских системах чаще всего далек от глубокого черного. Во многих европейских системах глубокий черный даже называют «Toyota 202», и он является дорогостоящим специальным черным пигментом. Но сегодня это часто используемый пигмент, который необходим постоянно, и им одним можно вполне обойтись в большинстве случаев (помимо оттеночного черного). К тому же не всегда этот европейский «Toyota 202» сравним по глубине цвета с японским черным компонентом.
Часто у европейских систем синие компоненты – с излишним красным оттенком (особенно под острым углом). Мало того, некоторые цветовые компоненты не обладают той чистотой и яркостью, которые присутствуют в японских красках. И колористам приходится идти на ухищрения с заменой компонентов, делая вместо двухслойной системы трехслойную.
Современные тенденции ОЕМ используют яркие краски. Но есть побочный эффект: с повышением чистоты и яркости резко падает укрывистость. Поэтому, когда говорят, что в какой-то определенной системе известный яркий неукрывистый цвет кроют в два слоя – это означает, что цвета у них будут грязными, и полное цветосовпадение гарантировано быть не может.
Чистый цвет повторить из чужих пигментов крайне сложно. Да и как повторить цвет пигментами, которые в несколько раз дешевле, чем пигменты составляющие краску для заводского покрытия.
В компонентах типа «металлик» достаточно сложно визуально определить качество пигмента, что дает возможность больше экономить разным европейским производителям. Чем больше разница флоп-эффекта (перелом из яркого в черный) в металликах, тем качественней обработка частиц алюминия и соответственно – дороже продукт. Европейские производители, не имеющие в линейке дорогостоящих компонентов «металлик», предложили колеровать продукт низкого качества разными добавками, методом нанесения и подложками. И крайне неохотно идут на включение в систему новых компонентов. А если и включают, то недостаточно высокого качества, с примесями частиц другого типа и градации.
У японцев с этим гораздо строже и обычно какой-то один европейский компонент «металлик» можно повторить двумя-тремя японскими, несколькими разными способами. Проделать такую работу с европейскими ЛКМ – практически провести исследовательскую работу с неизвестным результатом.
По сравнению с японскими, в европейских системах очень скромен набор перламутров и ксиралликов. Поэтому в определенных углах обзора не хватает оттенков или яркости. Колористам приходится доколеровывать краску лишними компонентами, чтобы поймать нужные оттенки. Да и изначально в «кодовых рецептах», там, где у японцев в составе один перламутр, у европейцев бывает их три.
Технологи европейских систем по цвету учат: нужно добавить еще один пигмент, чтобы скрыть лишнюю желтизну; потом – еще один, чтобы скрыть лишнюю зелень; потом – чтобы скрыть лишнюю красноту; и т. д. Но ведь краски для заводской окраски создаются по методу добавления оттенков, а не по методу избавления от побочных тонов. То есть и сам принцип подбора красок в корне другой, нежели у японцев.
Как видим, разница между японскими и европейскими производителями материалов выглядит достаточно ощутимой, по очень большому ряду причин. Расписывать преимущества товара можно очень долго. Вы сами можете в этом убедиться, попробовав лакокрасочные материалы KANSAI PAINT. По отзывам специалистов, пользующихся японскими материалами, их потребности удовлетворены полностью.
По материалам компании