Стандарты и особенности антикоррозионной обработки
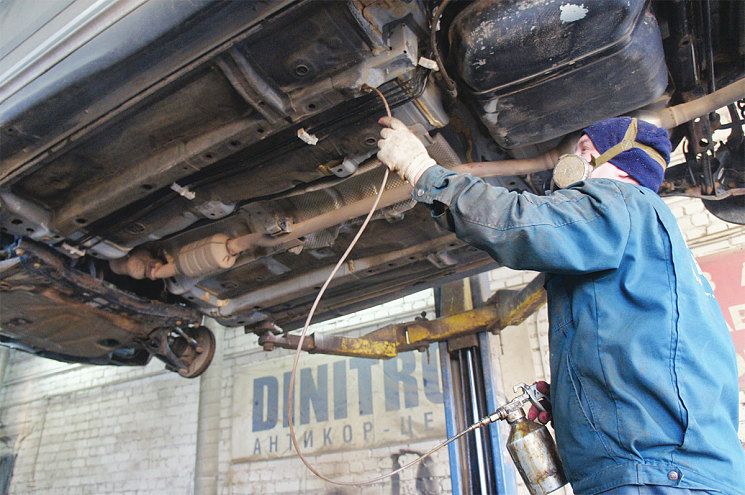
Читать всем
Эта статья родилась из бесед со специалистами компании ЮВК, официального дистрибьютора концернов Dinol и Equalizer. В ней собран ценный опыт практической работы по защите автомобилей от коррозии. Разумеется, далеко не весь опыт – иначе пришлось бы писать отдельную книгу. Но самые интересные и полезные рекомендации здесь приведены.
Почему эту статью рекомендуется прочитать всем – и владельцам автомобилей, и работникам сервиса? А потому, что она поможет им найти общий язык. Тем более, что это взгляд практиков с многолетним опытом.
Вот, например, определение коррозии и классификация ее видов. Казалось бы, мы подробно говорили об этом в «АБС-авто» № 12/2015. Но специалисты ЮВК смотрят на коррозию иначе. Не отказываясь от фундаментальной химии (как можно!), они вкладывают в классификацию коррозии кузова сугубо практический смысл.
Итак, по степени поражения кузова коррозию можно условно поделить на три основных типа – косметическая, проникающая и структурная.
• Косметическая коррозия появляется на наружных, видимых поверхностях. Она ухудшает внешний вид автомобиля, но еще не влияет на его эксплуатационные качества. Однако если не принять своевременных мер, косметическая коррозия может развиться в проникающую. А это еще что за зверь? Читаем дальше.
• Проникающая коррозия чаще всего развивается со стороны труднодоступных для осмотра участков кузова в местах скопления грязи и влаги. Она становится заметной лишь тогда, когда причиненный ущерб трудно исправить. Страшно? Погодите, самое страшное впереди!
• Структурная коррозия – потеря жесткости и прочности конструкции в результате разрушения силовых элементов, составляющих несущую структуру изделия. Она развивается в местах крепления агрегатов, а также в участках кузова, работающих при значительных знакопеременных нагрузках.
Например, коррозия рамы, лонжеронов, подрамника, переднего и заднего усилителей снижает их прочность и жесткость, меняет геометрию кузова и отрицательно влияет на управляемость. Это делает дальнейшую эксплуатацию автомобиля крайне опасной. В случае аварии пораженный коррозией автомобиль не обеспечит сохранности водителя и пассажира.
Что же делать? Ну, это вы уже знаете – обработать автомобиль профессиональными антикоррозионными препаратами и регулярно обновлять защиту. Давайте лучше поговорим, чего делать не надо.
О дешевой «автохимии»
Чтобы понимать разницу между хорошей и плохой антикоррозионной защитой, нужно определиться с критериями их оценки. Качество обработки, говорят в компании ЮВК, зависит от трех составляющих: применяемых материалов, технологии их нанесения и знания особенностей защищаемых поверхностей – днища, колесных арок и скрытых полостей. Для каждой составляющей есть свои требования.
Бывает, автовладельцу предлагается очень быстрая и очень дешевая «антикоррозионная обработка». Берем последние слова в кавычки потому, что именно быстрота и дешевизна вызывают серьезные подозрения.
Антикоррозионные материалы – это в любом случае химические составы. Они имеют разные классы опасности, а следовательно, по-разному влияют на окружающую среду. И если препараты Dinitrol производятся в Германии, проходят сертификацию, получают паспорт безопасности и одобрения производителей автомобилей, то у дешевых «антикоров» никаких подтверждений качества нет, подчеркивают в компании ЮВК.
Откуда нам знать – какая там используется основа, какие растворители? Наверняка дешевые и агрессивные, иначе обработка стоила бы гораздо дороже. Где гарантия, что при нанесении этих составов не пострадает ЛКП, не потускнеет хром, не станет белесым пластик, не испортятся резиновые уплотнители? А после высыхания пленки материал не растрескается и не начнет шелушиться?
Но самое скверное – это угроза здоровью водителя и пассажиров, не говоря уже о работниках станции, целый день вдыхающих ядовитые испарения.
О пленке и недоливе
Еще одна черта горе-обработчиков – катастрофический недолив материала. Об этом чуть подробнее.
Исследованиями шведских ученых установлено, что разная толщина покрытия обеспечивает различный уровень защиты. Защитная способность пленки увеличивается с ростом толщины лишь до определенного значения, после которого наращивание слоя практически бесполезно – оно не имеет прямой связи с защитной способностью (рис. 1).
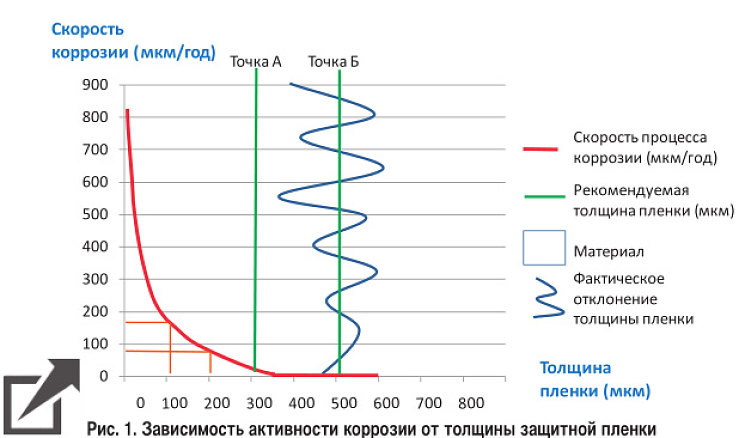
Иными словами, активность коррозии уменьшается с увеличением толщины пленки до точки А, после которой дальнейшее увеличение толщины покрытия на скорость коррозии уже не влияет.
Отсюда важный практический вывод: чрезмерная толщина защитного покрытия вызывает необоснованный перерасход материала. И наоборот, недостаточная толщина покрытия снижает качество защиты.
Так как при обработке контролировать толщину пленки в узких пределах (точка А) трудно, компания ЮВК советует добавлять небольшой запас к критической толщине и выходить на точку Б (снова рис. 1). Это и есть оптимальная толщина. Смысл в том, что отклонения толщины пленки допустимы – но лишь при условии, что покрытие будет не тоньше критической отметки в точке А.
Критическая толщина определяется с помощью испытаний в камере соляного тумана (например, по ГОСТ 9.054–75, метод 3). Пластины из углеродистой стали, покрытые пленкой антикоррозионного состава различной толщины, помещаются в камеру, в которой периодически распыляется 5-процентный раствор хлористого натрия. Продолжительность испытаний в камере соляного тумана составляет от 600 до 2500 часов. Оценка проводится по проценту поверхности стали, пораженной коррозией.
Покрытие эффективно настолько, насколько эффективен его самый тонкий участок (рис. 2.). В пленке не должно быть пустот, посторонних включений и разрывов. Все это уменьшает потенциал защиты.
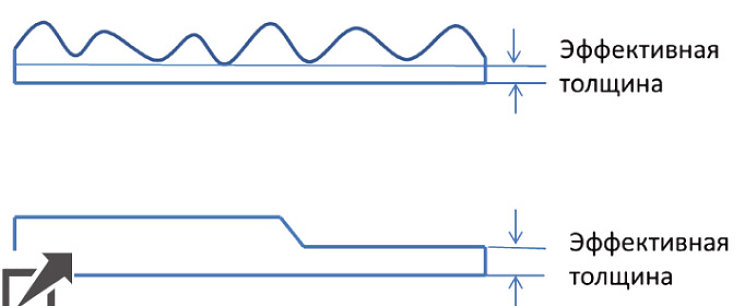
Так говорит фирменная документация Dinitrol. Заботятся ли о правильной толщине пленки сервисные станции, работающие суррогатными «антикорами»? Нет, конечно. Более того, они обещают обработать автомобиль одним-двумя литрами материала. Что ж, давайте рассуждать, говорят специалисты ЮВК.
Расход материала напрямую связан с сухим остатком и нормой нанесения, т.е. рекомендуемой толщиной пленки. Исходя из этих данных, рассчитаем примерное количество материала, необходимого для покрытия некоторых участков автомобильного кузова.
Всем известно, что 1 л жидкости (речь именно об объеме!) покрывает площадь 1 м2 слоем толщиной 1 мм (рис. 3). Рассчитаем расход материала при обработке днища автомобиля.
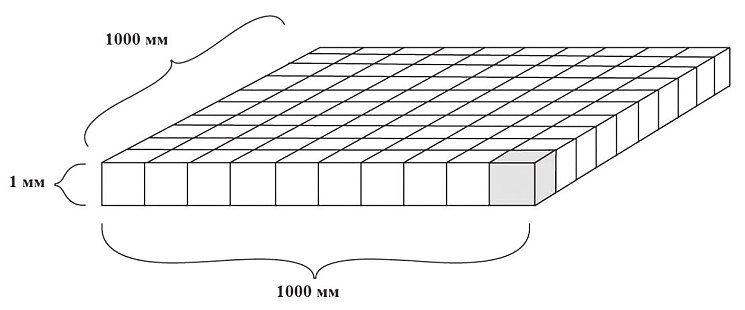
Пусть средняя площадь днища 4,5–5,5 м2. Рекомендуемая толщина мокрой пленки для Dinitrol Metallic 450–750 мкм. Таким образом, расход материала на 1 м2 составит 0,6 л, на все днище – 0,6 × 5 = 3 л.
Аналогичные расчеты показывают, что на обработку колесных арок при толщине слоя 1000 мкм нам понадобится 3,6 л материала.
Вот и думайте: как же можно обработать весь автомобиль одним-двумя литрами материала? Никак, разве что просто «обозначить защиту» для доверчивого клиента.
Быстро хорошо не бывает
И наконец, о «быстроте» антикоррозионной обработки. По опыту ЮВК, на полноценную комплексную защиту от коррозии автомобиля с пробегом потребуется два дня (рис. 4).
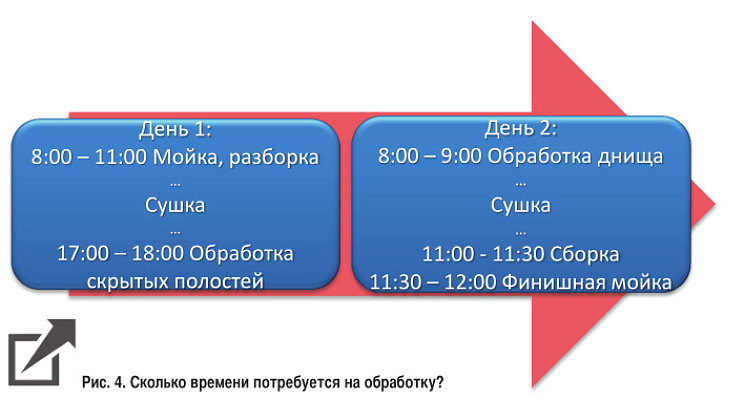
Разумеется, это время учитывает не только распыление материала, но и подготовку автомобиля к обработке. А она весьма длительная и кропотливая. Судите сами.
Процесс начинается с демонтажа всей пластиковой защиты днища и арок. Снимаются колеса, ступицы маскируются защитной пленкой.
Затем следует мойка днища и арок. Промывается не только само днище, но и пороги, лонжероны, для чего применяются специальные насадки. Обезжириваются замасленные поверхности, если таковые имеются.
Зачищаются участки, где есть отслоения ржавчины. Важно уделить этому этапу особое внимание, поскольку оставшиеся на поверхности пыль, грязь и маслянистые загрязнения ухудшают адгезию антикоррозионного материала.
Сушка – длительный и важный этап обработки. Она может быть естественной, когда авто просто оставляют в хорошо проветриваемом месте, и принудительной – в этом случае автомобиль продувают сжатым воздухом, обдувают тепловыми пушками. В холодное время года этот этап одновременно служит и для согревания автомобиля. Ведь нанесение материала на холодный и влажный металл также ухудшает адгезию.
Материалы для скрытых полостей способны вытеснять влагу, поэтому их допустимо наносить на влажные поверхности – но не в «лужу», разумеется. Составы для днища наносятся только на сухую поверхность. Этап сушки занимает от 2 до 7 часов.
Как вы знаете, обработка скрытых полостей заключается в распылении состава внутрь порогов, лонжеронов, дверей, крышек капота и багажника, стоек и других полых элементов кузова. Мы повторяем это с единственной целью – подчеркнуть, что эти операции требуют немалого времени.
Специалисты ЮВК приводят такой пример: только на днищевой части автомобиля Subaru Forester находится 69 технологических отверстий, в которые необходимо ввести насадку и распылить материал. Причем многие эти отверстия заглушены, т. е. необходимо вытащить заглушку, а затем установить обратно – а на это тоже нужно время.
Распыление проникающего состава на поверхность днища и арок происходит достаточно быстро, но здесь также нельзя спешить. После нанесения необходимо выждать не менее 20 минут, чтобы материал успел «сработать», а именно пенетрировать в щели, углубления и в очаги коррозии.
Наступает очередь нанесения уплотняющего состава. На этом этапе также не стоит торопиться. Необходимо обработать всю поверхность равномерным слоем рекомендованной толщины. На участке должна быть обеспечена яркая подсветка снизу.
Поскольку на днище имеются выступающие элементы, отбортовки, углубления и проч., необходимо обрабатывать днище тщательно, наклоняя пистолет под разными углами.
Затем производится монтаж пластиковых элементов и колес. И вот завершающий этап – бережная мойка кузова.
Теперь вы сами можете оценить уровень качества будущей обработки, спросив на сервисе: «И сколько времени понадобится для полноценной обработки моего автомобиля?».
Три метода обработки
Продолжаем беседу со специалистами ЮВК. Сегодня ассортимент Dinitrol насчитывает более 240 наименований. Причем составы отличаются не только названиями, но и уникальными характеристиками.
Разнообразие продукции позволяет обеспечить комплексную защиту автомобиля. Это в общем и целом. Если же говорить об индивидуальном подходе, то специалисты компании Dinol разработали три метода антикоррозионной обработки автомобилей.
Методы эти называются Tuff-Kote Dinol, Dinitrol и Dini. Они способны удовлетворить любые требования в зависимости от возможностей клиентов и условий эксплуатации их автомобилей. Отличие методов заключается в различной степени скрупулезности антикоррозионной обработки конкретных деталей кузова.
Tuff-Kote Dinol представляет собой наиболее завершенную систему защиты. Ее отличительная черта – использование комбинации проникающего и уплотняющего составов для обработки как днища, так и скрытых полостей.
После тщательной мойки и сушки внешних частей кузова производится обработка скрытых полостей и днища проникающим составом, содержащим эффективные ингибиторы коррозии. Пробираясь по всевозможным микротрещинам, зазорам и вытесняя влагу, материал эффективно изолирует металл от электролита. После этого многие скрытые полости покрываются более долговечным уплотняющим густым составом, а некоторые – даже уплотняющим составом для днища. Таким способом достигается эффективная защита на длительный срок.
Некоторые элементы днища также обрабатываются в два этапа – сначала проникающим, а затем уплотняющим составами. Если на автомобиле присутствуют следы коррозии, необходимо провести их предварительную обработку преобразователем ржавчины.
Комплексная система Dinitrol кардинально не отличается от Tuff-Kote Dinol. Обработка некоторых деталей кузова производится только одним препаратом для скрытых полостей (это касается стоек, дверей и некоторых элементов днища). Также не предполагается использование преобразователей ржавчины. В остальном методы Dinitrol и Tuff-Kote Dinol схожи друг с другом.
И наконец, бережливым автомобилистам адресуется наиболее простой метод под названием Dini. Он представляет собой обработку лишь наиболее подверженных коррозии частей кузова. Dini – самый недорогой из трех методов, поскольку расход антикоррозионных материалов у него минимальный.
Таким образом, три системы комплексной антикоррозионной защиты от компании Dinol AB позволят найти оптимум по соотношению цена/качество для любого автомобилиста. Подробности методов приведены в таблице.
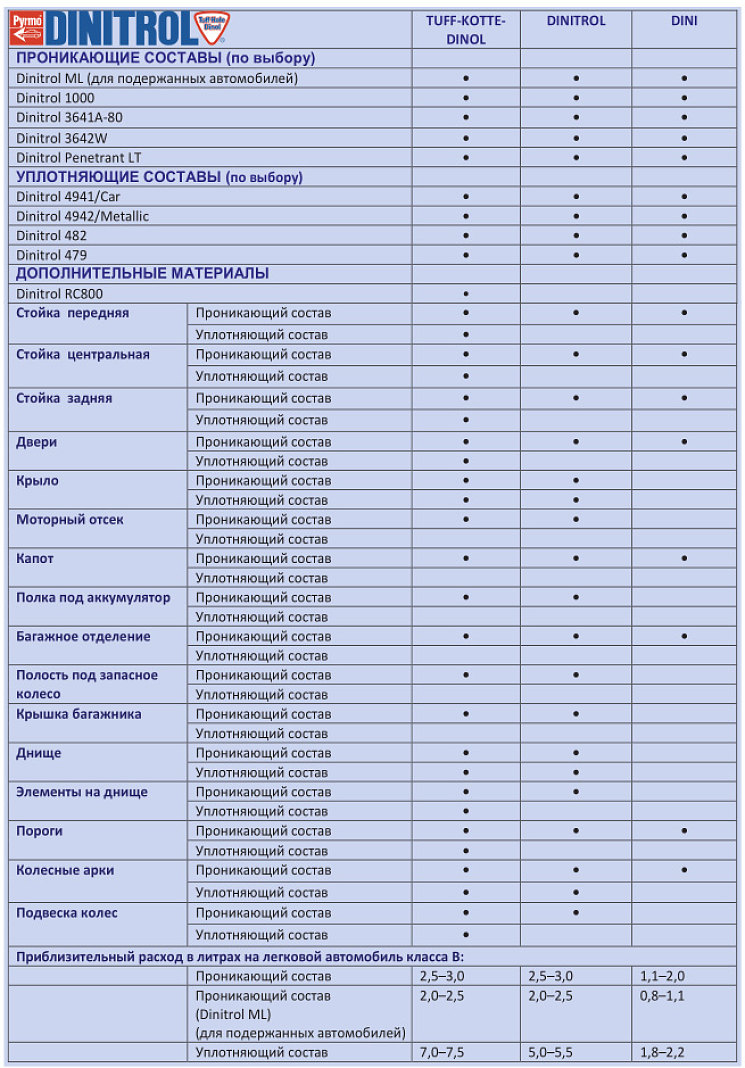
О двухслойной методике «заливки»
Препараты Dinitrol для скрытых полостей имеют восковую основу и отличаются высокой пенетрацией. Они проникают в очаги ржавчины, стыки металла, нахлесты, швы, болтовые соединения, останавливают процесс уже начавшейся коррозии и блокируют появление ее новых очагов.
Наносятся эти составы МL-методом. Он заключается в распылении жидкого материала через технологические либо специально просверленные отверстия. При распылении материал образует густой туман и равномерно оседает на внутренние поверхности.
В ассортименте Dinitrol существует несколько наименований проникающих составов. Наиболее популярные из них Dinitrol ML, Dinitrol 1000, Dinitrol Penetrant LT, Dinitrol 3641/А 80. Они различаются несколькими свойствами, но чтобы понять суть двухслойной обработки, остановимся на двух характеристиках: пенетрации материала и долговечности пленки.
Выше компания ЮВК рассказала о трех методах или стандартах защиты от коррозии. При обработке по методу Dinitrol автомобилей с пробегом необходимо применить состав с самой активной пенетрацией, чтобы он проник во все имеющиеся очаги коррозии, вытеснил влагу и консервировал ржавчину. Для этой цели выбирается Dinitrol ML.
Показатель стойкости к солевому туману у этого материала 96 часов, что соответствует примерно году эксплуатации. Получается, что необходимо либо повторить обработку скрытых полостей через год, либо нанести вторым слоем более стойкий состав.
Какой именно состав? Например, Dinitrol Penetrant LT, который выдерживает 1000 часов в соляном тумане, что соответствует 10 годам эксплуатации. К слову, Penetrant LT обладает пенетрацией до 30 мм и при обработке новых автомобилей (без признаков коррозии) используется самостоятельно.
Вот так, комбинируя различные препараты, можно составлять оптимальные схемы обработки для любых автомобилей – новых и подержанных, существенно тронутых коррозией и имеющих относительно свежий кузов.