Вопрос, конечно, интере-е-есный… (продолжение, начало в № 4/2015)
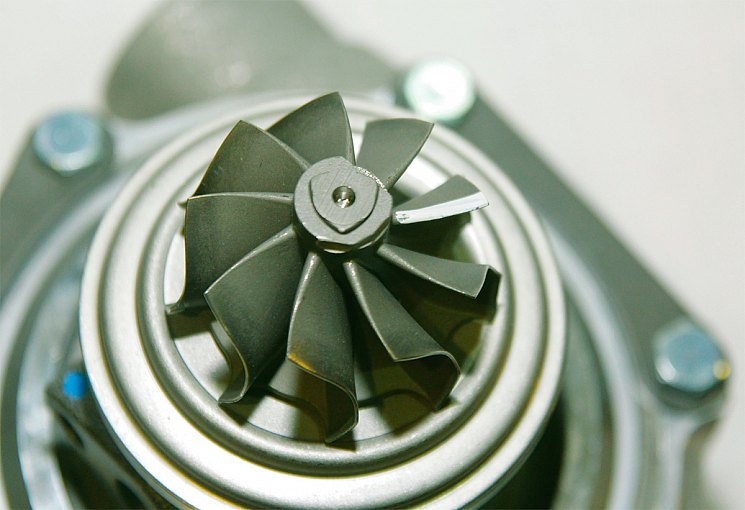
Вот еще несколько любопытных вопросов о турбокомпрессорах, ответы на которые не лишены интереса.
Подскажите, «Гарет» – это чья фирма? А почему на турбине написано «маде ин Корея»?
Вопрос, конечно, интере-е-есный…
Те, кто прочитал предыдущую часть сериала, уже знают, что Garrett («Гарретт») – это не фирма, а торговая марка турбокомпрессоров, которые выпускает турбоподразделение концерна Honeywell. Чей это концерн? Да ничей! В том смысле, что, как и многие гиганты эпохи глобализации, это транснациональное предприятие. В частности, штаб-квартира турбодепартамента Honeywell базируется в Швейцарии, а его многочисленные подразделения (заводы, научно-исследовательские и инжиниринговые центры) разбросаны практически по всем континентам, за исключением, разве что, Антарктиды. У Honeywell есть предприятия по производству турбин и в Южной Корее. В этом нет ничего странного – двигатели многих корейских автомобилей комплектуются «гарреттами», и было бы неразумно возить их на сборку «за тридевять земель». Более того, есть заводы и в Китае! Но они выпускают не пресловутые «китайские турбины» – некачественные копии оригинальных изделий, сработанные незнамо как и неизвестно из чего китайскими умельцами, – а все те же турбины Honeywell/Garrett. Хотите – верьте, хотите – нет, но фирменные производства в любой точке мира работают по единым стандартам, с использованием одинаковых технологий, а потому на выходе получают продукт одинаково безупречного качества. Сказанное касается и прочих производителей турбин, которые упоминались в предыдущей части статьи. Они также интегрированы в глобальную мировую индустрию.
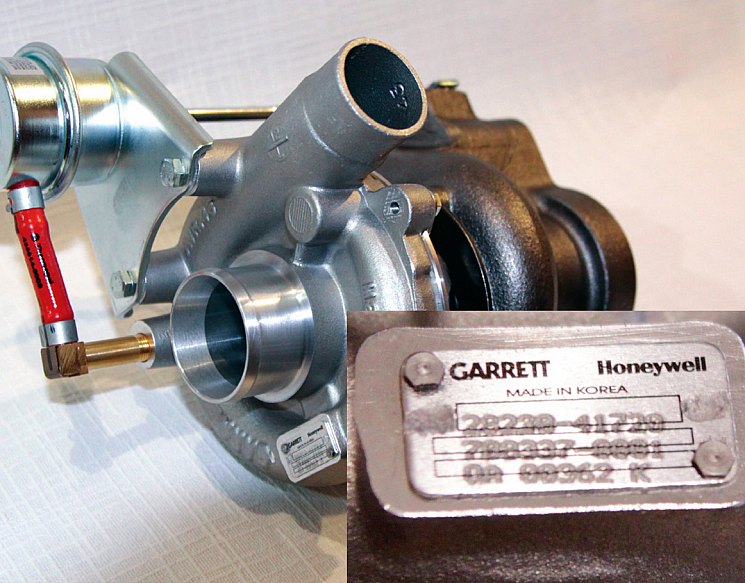
Турбины определенной модели для нужд афтемаркета изготавливаются периодически, партиями, размер которых определяется спросом на рынке запчастей. Какими резонами руководствуются турбопроизводители при размещении заказа на сборку партии турбин – неизвестно, да и неважно. Факт тот, что с регионального склада производителя в обозримый период времени можно получить турбины модели Х, собранные только на заводе, например, в Польше. И нигде кроме. Кстати, место сборки турбины указывают далеко не все и не всегда. Возможно, чтобы потребители не задавали всякие «интересные вопросы».
Почему на моей старой турбине вал почти не люфтит, а на вашей новой – болтается?
Вопрос, конечно, интере-е-есный…
Редкий покупатель при осмотре турбины не совершает этот «ритуал». Традиционным считается покрутить вал и «поболтать» его из стороны в сторону. Некоторые покупатели этим и удовлетворяются, другие делают удивленный вид и задают вопросы.
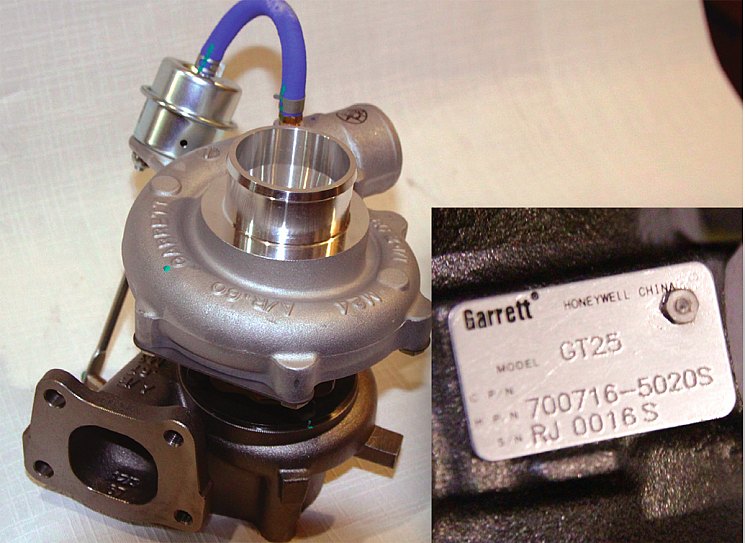
Лично я за традиции, если они разумны и «способствуют». Поэтому я против «покрутить» и «поболтать». Нельзя не согласиться с производителями, которые не рекомендуют вращать ротор новой турбины. Дело в том, что на рынок турбины обычно поступают «сухими». После финишной балансировки и настройки, которые выполняются с имитацией рабочих условий смазки подшипникового узла ротора, остатки масла на заводе удаляются промывкой. Вращая ротор «насухую», можно запросто наделать рисок на парах трения, представляющих собой разнородные материалы: сталь, бронзу, чугун. А это уж точно «не способствует». Замечено, что в последнее время турбопроизводители все чаще пренебрегают промывкой и отправляют на рынок турбины с остатками масла: видимо, жертвуют товарным видом в угоду защите от «крутильщиков». Так же поступают и грамотные ремонтники – не удаляют из корпуса подшипников остатки моторного масла, чтобы уменьшить вероятность повреждения турбины при монтаже и первом пуске. Это – присказка, сказка впереди.
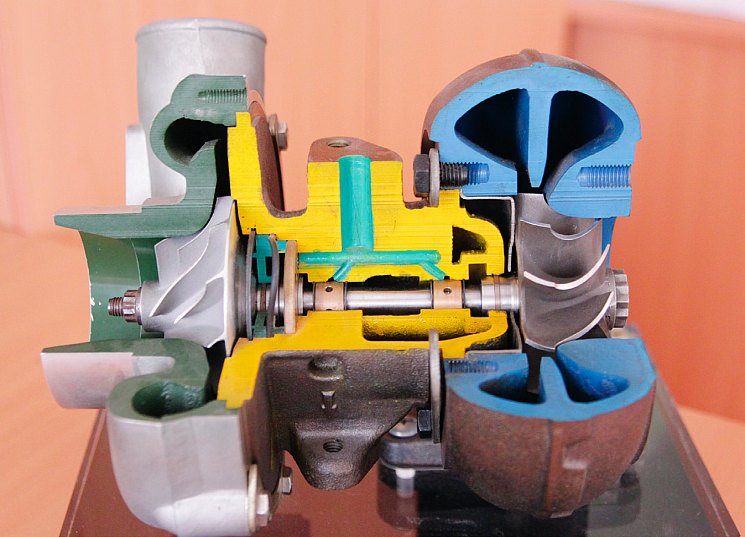
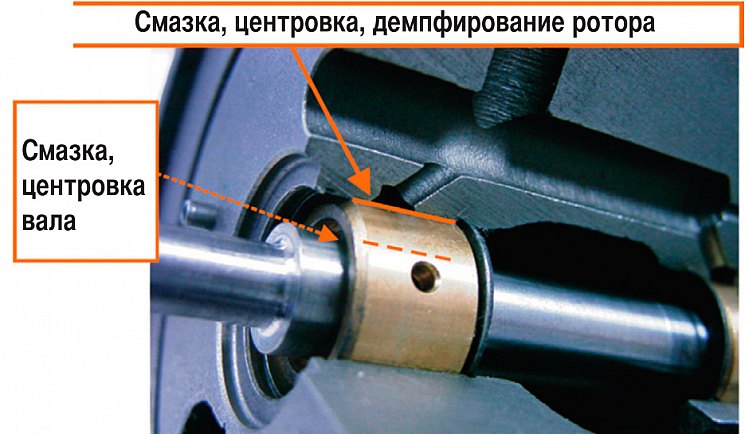
То, что непосвященные ощущают, качая вал со стороны компрессорного колеса, и называют словом «болтается», специалисты именуют перекладкой ротора. Она свидетельствует о том, что в подшипниковом узле турбокомпрессора есть тепловые и масляные зазоры. Они жизненно необходимы, без них турбокомпрессор не протянет и нескольких секунд. Тепловые зазоры, понятное дело, служат для компенсации термического расширения деталей агрегата, горячая часть которого раскаляется чуть ли не до 1000 °С. В масляные зазоры подшипникового узла подается масло от системы смазки двигателя. При нагнетании масла под давлением в условиях вращения смазываемых деталей и зазоров строго определенной величины в них формируется масляная пленка, обладающая высокой несущей способностью. Иначе ее называют масляный клин. Масляный клин действительно «расклинивает» вращающиеся детали, во‑первых, полностью исключая контакт металлических поверхностей, во‑вторых, точно центрируя вращающийся ротор в неподвижном корпусе.
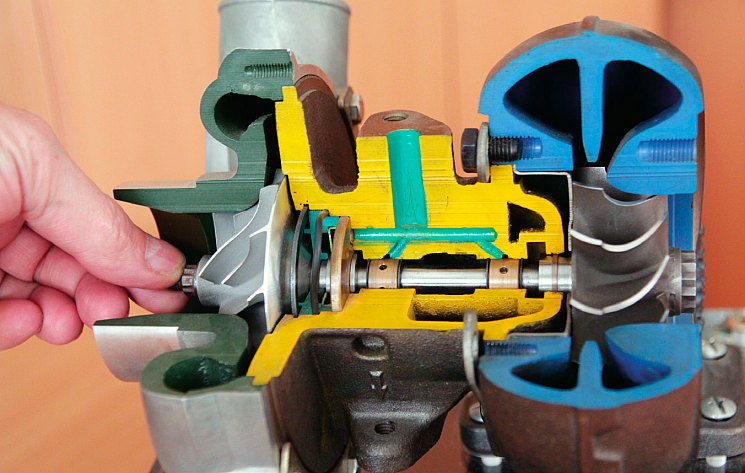
Принцип гидродинамического смазывания широко применяется в технике, в том числе и в конструкции ДВС: так смазываются и коленчатый, и распределительный валы двигателя. Устройство турбокомпрессора отличается тем, что в нем реализована двухопорная схема фиксации вала с плавающими опорными подшипниками. Название, как принято в технике, отражает особенности конструкции. Вал удерживается одним упорным и двумя опорными подшипниками скольжения (втулками особой конфигурации). Причем опорные подшипники разделены масляным зазором и с валом ротора, и с корпусом. При работе турбокомпрессора вращается не только вал ротора, опорные подшипники также вращаются, но примерно с вдвое меньшей частотой. Второй масляный клин между подшипниками и корпусом играет роль дополнительного демпфера радиальных нагрузок.
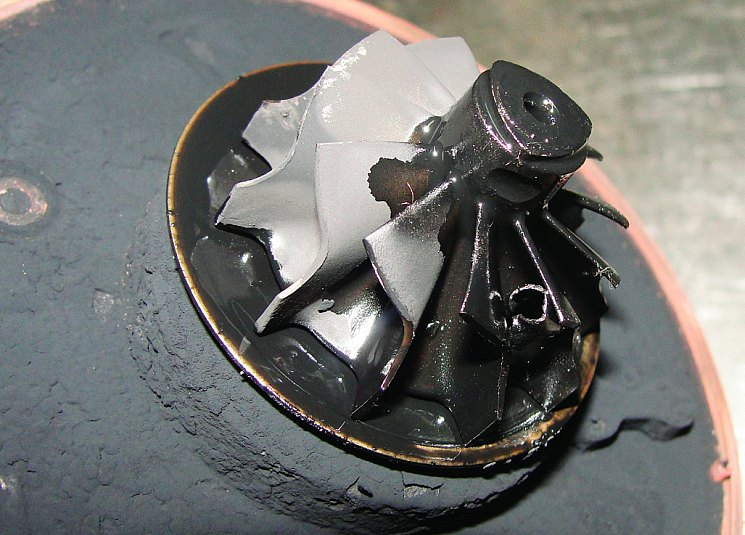
Теперь понятно, откуда берется перекладка ротора. Отклоняя вал за консольно закрепленное компрессорное колесо, мы перекашиваем его между двумя опорами. При этом на каждой выбирается по два масляных зазора с противоположных сторон. Масляный зазор легковой турбины составляет примерно 0,05–0,07 мм. Значит, в районе опор вал сместится на 0,1–0,15 мм, да еще и в разные стороны. Законы геометрии подсказывают, что величина перекладки превысит смещение более чем в 2 раза, что также зависит и от расстояния между опорами, и от вылета консоли вала. Так что у турбин разной конструкции и типоразмера она разная. Типичные величины для легковых турбин – от нескольких десятых долей до миллиметра.
Остается ответить на вопрос, почему на старой турбине «вал не люфтит». Учитывая сказанное выше, напрашивается очевидный вывод: потому что она неисправна. Обычно снижение подвижности ротора происходит из-за накопления внутри корпуса подшипников и на тепловом экране сажевых отложений, кокса. Наиболее интенсивно коксуются детали с горячей стороны, примыкающей к турбинной части. В некоторых случаях процесс коксования заходит так далеко, что ротор становится сложно провернуть рукой. Отложения не только тормозят ротор, но и нарушают работу уплотнений вала, о чем пойдет речь далее.
Купил новую турбину, поставил – тут же потекла. В чем дело? Сальники некачественные?
Вопрос, конечно, интере-е-есный…
Ответить на него, не разобравшись с принципом работы и конструкцией уплотнений вала турбокомпрессора, затруднительно. С этого и начнем. Заодно предпримем очередную попытку раз и навсегда закрыть тему «сальников».
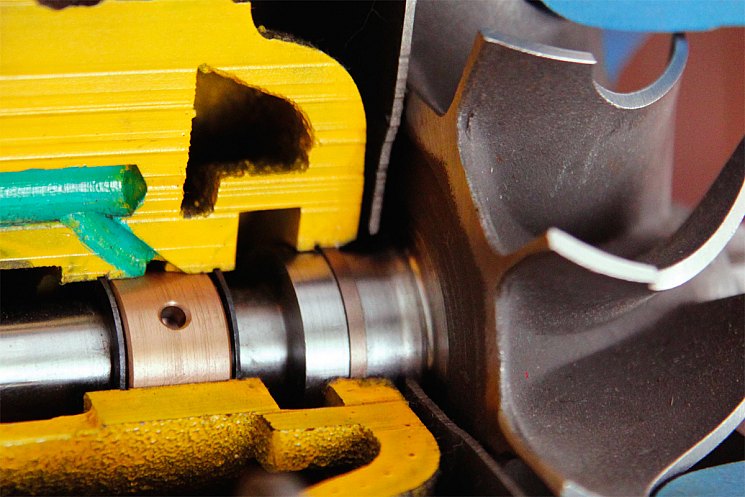
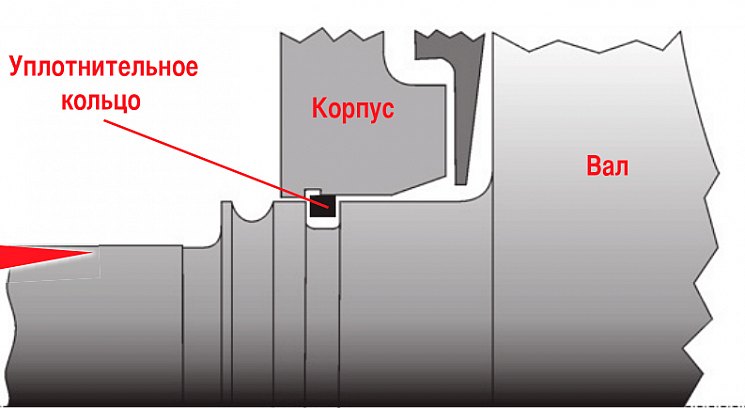
Сальниковое уплотнение, представляющее собой войлочное кольцо с набивкой из консистентной смазки, – архаизм, который в современной технике давно не применяется. Последний раз мне доводилось видеть сальник в уплотнении коленвала пожилого мерседесовского двигателя в далекие времена, когда я был молод и, не поверите, лохмат. Если говорить о турбоагрегатах, в них сальники не применялись никогда. Сами подумайте: какой войлок и набивка при таких температурах? Как можно бороться за снижение инерционности ротора и одновременно зажимать его сальником?
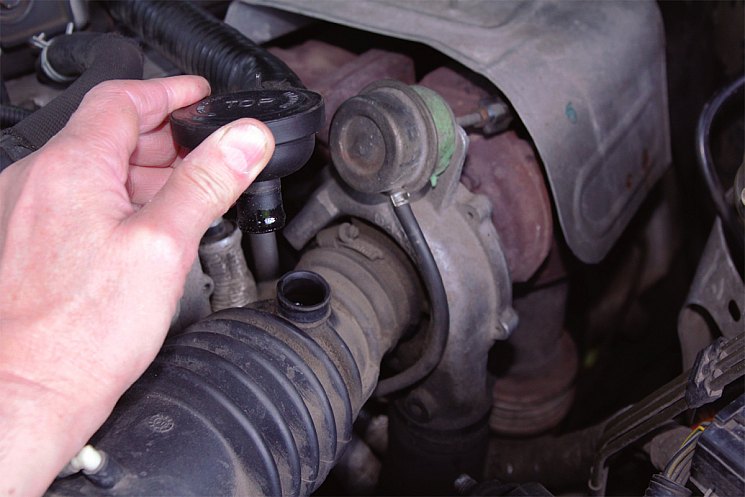
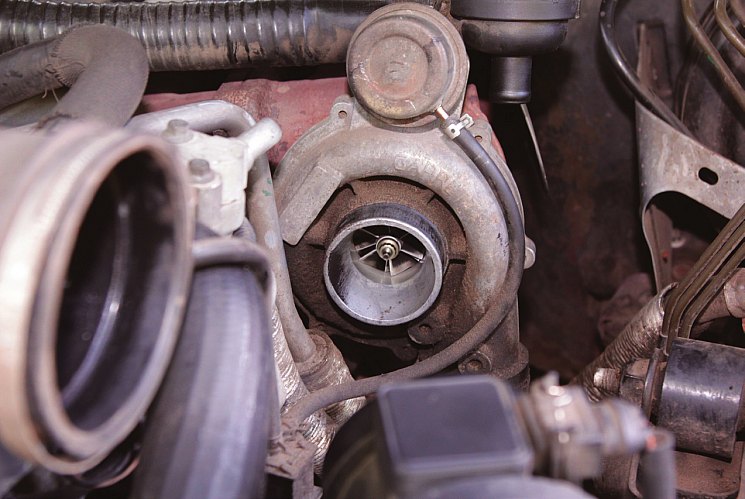
В турбокомпрессорах использовали и по сей день используют уплотнение, исключающее механический контакт вращающегося вала с корпусом. Оно так и называется – бесконтактное. И еще нужно дополнить: газодинамическое и лабиринтное. Собственно, в «ФИО» уплотнения зашифрованы и его функции, и принцип действия, и особенности конструкции. С бесконтактностью все понятно. Термин «газодинамическое» означает, что уплотнение разделяет полости с разным давлением газовой среды, препятствуя газообмену между ними, и проявляет свои свойства в динамике, когда вращающаяся деталь узла перемещается относительно неподвижной детали. Добавим – с высокой скоростью. Слово «лабиринтное» поясняет, что уплотняющее действие узла основано на создании между подвижной и неподвижной деталями малого зазора сложной извилистой формы – лабиринта. Так, лабиринт в уплотнениях вала турбокомпрессора формируется между кольцевой канавкой на валу и входящим в нее разрезным кольцом, неподвижно закрепленным в корпусе за счет сил упругости. При вращении вала в изгибах лабиринта за счет газодинамических эффектов создаются зоны повышенного давления, препятствующие перетеканию газов сквозь уплотнение.
Здесь не может не возникнуть вопрос: о каких газах идет речь и почему ни слова не сказано о масле? Ведь в традиционном представлении роль уплотнения – удерживать в смазываемом корпусе масло, препятствовать его утечке вовне. Дело в том, что в полости корпуса подшипников нормально работающего турбокомпрессора масла быть не должно. Такая вот эпидерсия… Система смазки работает так, что заполнения корпуса маслом не происходит. Масло поступает по каналам непосредственно к парам трения, продавливается сквозь масляные зазоры и разбрызгивается вращающимся валом на стенки корпуса. По ним масло стекает вниз и самотеком удаляется обратно в картер двигателя по сливной трубке. Поэтому среда внутри корпуса подшипников похожа на ту, что создается в картере двигателя над масляной ванной: это смесь газов с взвесью частиц масла (масляным туманом) при давлении, близком к атмосферному.
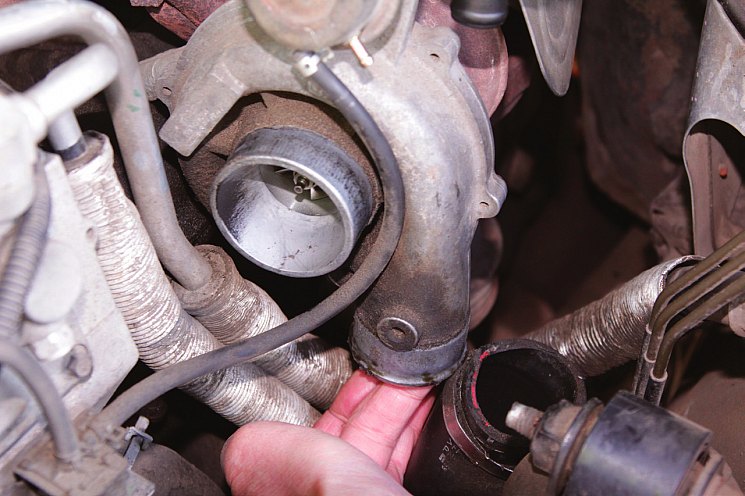
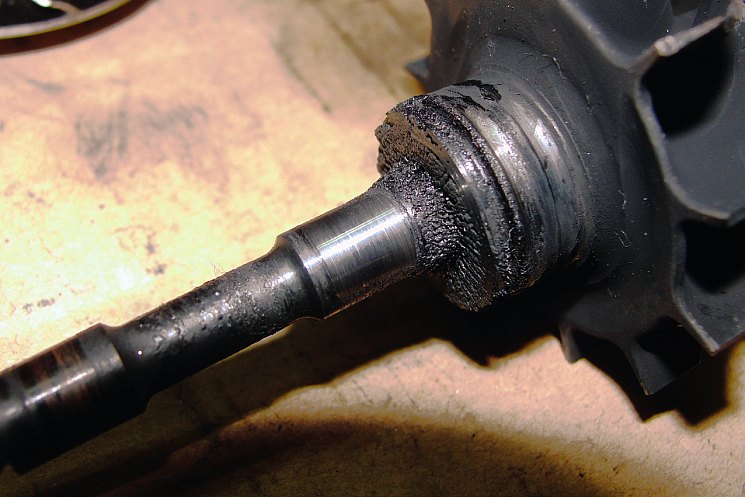
Тогда всплывает другой вопрос: зачем вообще нужны уплотнения вала? Вот он очень интересный… Их основная задача – изолировать корпус подшипников (и картер двигателя, сообщающийся с ним по трубке слива масла) от проникновения газов из турбины и компрессора. Давление в корпусе турбины выше атмосферного на всех режимах работы двигателя, в компрессоре оно превышает атмосферное тогда, когда создается ощутимое давление наддува, т.е. на большинстве эксплуатационных режимов. Если не предусмотреть уплотнения, в картер двигателя поступали бы отработавшие газы и наддувочный воздух, что недопустимо. И лишь второстепенная задача – препятствование выносу из корпуса масляного тумана (не масла, заметьте) на некоторых режимах работы двигателя.
С обеими задачами лабиринтное уплотнение справляется, но не «на отлично». Оно по определению не является абсолютно непроницаемым. Это означает, что при исправной турбине и исправном двигателе неизбежно идут процессы проникновения газов в корпус подшипников (чаще – со стороны турбины) и вынос из него масляного тумана (в основном в сторону компрессора). И вся «петрушка» в том, укладывается ли их величина в допуск или превышает его. Никаких количественных оценок допустимой степени проницаемости уплотнений нет. Считается, что в двигателе с турбонаддувом «запотевание» стенок патрубков в напорной части впуска – норма. Но если при их расстыковке масло сливается ручьем – это признак неисправности, подлежащей устранению. Впрочем, для проверки работоспособности уплотнений не обязательно расстыковывать напорные трубопроводы. Достаточно контролировать расход масла по его уровню в картере. Если убыль укладывается в норматив, установленный производителем двигателя, – значит, все в порядке.
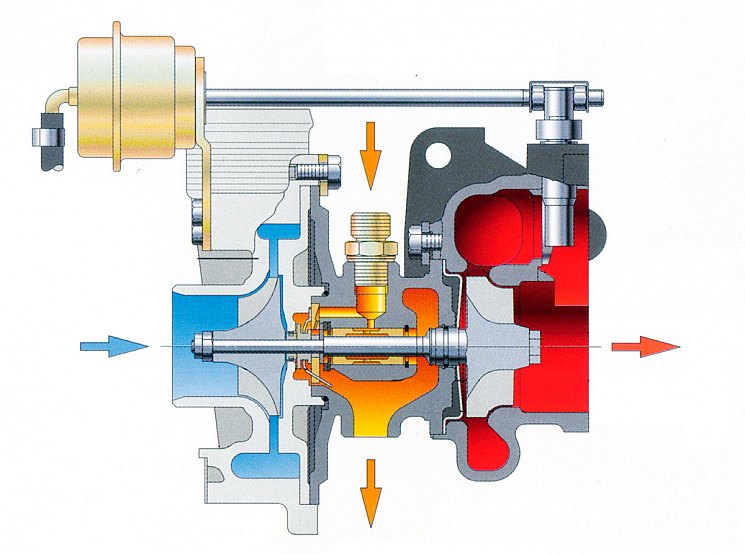
Обычно к этому кульминационному моменту повествования у жаждущего ответа клиента кончается терпение, «ум заходит за разум», и он удаляется с проклятиями и обещанием встретиться в суде. Надеюсь, что пытливый читатель окажется выносливее слушателя и домучает еще несколько абзацев. Тем более что мы уже приступаем к ответу на заданный «интересный вопрос».
«Турбина потекла» – выражение не техническое и может означать все что угодно. Если подразумевается, что сразу после замены турбокомпрессора дымность выхлопа не уменьшилась, это может быть следствием многих причин. Например, при замене турбины не были очищены впускная и выпускная системы двигателя и продолжается выгорание остатков масла, попавших туда ранее. Масло может попадать во впуск через неисправную систему вентиляции картера. В дизелях канал вентиляции, как правило, выходит во всасывающий патрубок перед компрессором. Если входные кромки компрессорного колеса в масле – значит, масло попадает не из компрессора, а в компрессор и через него – в двигатель. Естественно, повышенный расход масла, сопровождающийся дымным выхлопом, может быть вызван изношенными уплотнениями и клапанов, и деталей ЦПГ, что также следует проверить.
Достоверное свидетельство аномально высокого выноса масла из турбокомпрессора – присутствие его заметного количества в улитке компрессора после непродолжительной работы. Чем это может быть вызвано?
Возможных причин – множество. Большинство из них, как ни странно, не является следствием неисправности турбины. Проницаемость уплотнения напрямую зависит от перепада давлений в разделяемых им полостях. Если разность давлений превышает величину, на которую рассчитано уплотнение, его эффективность резко снижается. Поэтому работоспособность уплотнений очень чувствительна к соотношению таких параметров, как давление в корпусе компрессора, давление в корпусе турбины, давление в картере двигателя. Нарушить их допустимый баланс могут:
• затруднение во всасывающей части впуска (например, засоренный воздушный фильтр);
• негерметичность напорной части впуска (например, трещина в патрубке или интеркулере);
• снижение пропускной способности выпуска (например, забитый катализатор или сажевый фильтр);
• негерметичность системы выпуска (например, трещина, неисправность клапана рециркуляции ОГ);
• негерметичность уплотнений поршней (износ ЦПГ, повышенный прорыв газов в картер);
• снижение пропускной способности вентиляции картера (засорение магистралей и фильтров отсечки масла);
• затруднение в трубке слива масла из турбокомпрессора.
Во всех перечисленных случаях проницаемость абсолютно исправных уплотнений вала турбокомпрессора превысит норму. Насколько – зависит от интенсивности воздействия той или иной неисправности. Пожалуй, наиболее критичными являются три последних фактора, поскольку создают препятствие для свободного слива масла из корпуса подшипников. Если корпус заполняется маслом, ничто не мешает ему истекать во все стороны – ведь уплотнения не гидро-, а газодинамические.
Поэтому инструкции турбопроизводителей по сервисной замене их продукции обязательно включают проверку состояния упомянутых систем двигателя. Нужно подчеркнуть, что если причину повышенной утечки масла своевременно выявить и устранить, работоспособность турбокомпрессора не пострадает.
Причина увеличения выноса масла может заключаться и в самом турбокомпрессоре. Работоспособность лабиринтных уплотнений зависит от точности конфигурации лабиринта. Она может быть нарушена. Как правило, это происходит при износе опорных или упорного узлов трения. Износ опорных подшипников приводит к увеличению радиальных зазоров. Подвижность вала в радиальном направлении возрастает, и геометрия лабиринта меняется. Износ упорного подшипника сопровождается смещением вала в осевом направлении, что также меняет величину зазоров в сопряжении канавки и уплотнительного кольца. Большое смещение приводит к контакту кольца и канавки и их взаимной выработке.
При длительной эксплуатации турбокомпрессора износ подшипникового узла ротора – явление обычное и вопросов, как правило, не вызывает. Но может ли такое случиться, если турбину только что установили? Ответ: может, если монтаж и первый пуск были выполнены некорректно. Установлено, что задержка в подаче масла всего на 4 секунды уже вызывает износ подшипников турбокомпрессора. Задержка в 8 секунд может привести к повреждению, не подлежащему ремонту. Поэтому инструкция по замене требует предварительно заполнить турбину маслом и добиться подачи масла к турбине в режиме прокрутки стартером, без запуска двигателя. Если этого не сделать, велика вероятность устроить «сухой пуск» и в течение нескольких секунд «убить» турбину. Нередко так и происходит – машина даже не успевает покинуть подъемник.
Выходит, в том, что новая турбина сразу «потекла», виноваты или неисправности двигателя, или «монтеры». А почему не производитель? Где же объективность? Может, на заводе что-то не так или не из того сделали, перепутали, не поставили? Такая вероятность, безусловно, существует, но в истории с турбокомпрессорами она мизерна. Особенность технологии сборки турбокомпрессора такова, что каждый агрегат подвергается финишной балансировке и настройке устройств регулирования. При этом контролируются и правильность сборки, и работа уплотнений вала, а также происходит его обкатка. Так что если речь идет об оригинальном изделии, о его заводском дефекте нужно думать в последнюю очередь. Реальность именно такова.
Хорошо, допустим, двигатель неисправный или я что-то не так сделал. Но почему: ставлю старую турбину – течет, но терпимо, ставлю новую – льет как из ведра?
Вопрос, конечно, интере-е-есный…
Действительно, казалось бы, железобетонный аргумент в пользу того, что новая турбина неисправна – раз уж она даже хуже старой. Однако это не так. И производителям, и продавцам турбин такой эффект известен. Его механизм становится понятным после вскрытия изрядно послужившего турбокомпрессора. Все его внутренности, включая и уплотнения, обычно бывают забиты продуктами деструкции моторного масла. Скопившийся в лабиринтах кокс превратил бесконтактное уплотнение в контактное. Разумеется, ни о какой эффективности работы турбокомпрессора тут речи быть не может. Тем не менее проницаемость «коксовой набивки» оказывается ниже, чем у исправного уплотнения в условиях присутствия в двигателе причины, провоцирующей повышенный вынос масла из турбокомпрессора. В такой ситуации нужно выявить эту причину и устранить ее.
Продолжение следует…
Автор благодарит сотрудников компаний «Диас Турбо» и «ТурбоИнжиниринг» за помощь в подготовке статьи
Уникальную информацию по устройству, эксплуатации и ремонту систем турбонаддува смотрите на сайте turbomaster.ru