Вскрытие показало… Часть 2. Эпиданамнез запора
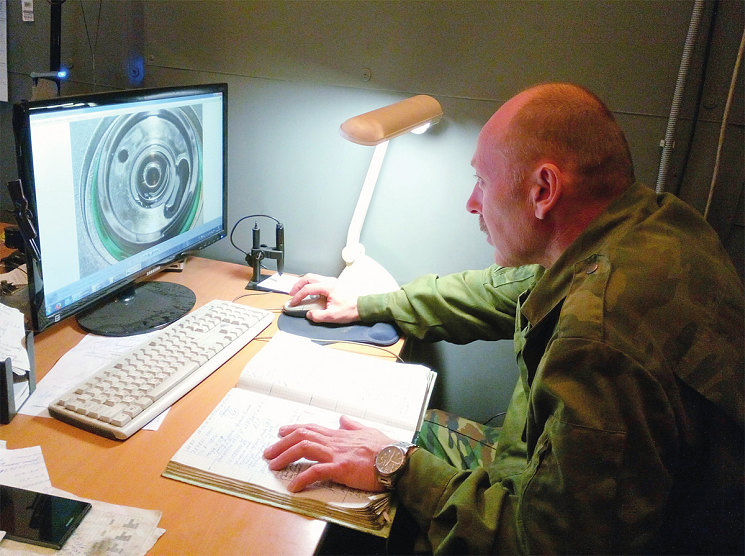
По статистике, подавляющее большинство отказов турбокомпрессоров (по разным источникам – до 80–90%) так или иначе связано со смазкой узла подшипников. Поэтому и вторую часть обзора причин «безвременной кончины» турбин стоит посвятить ему, маслу. Вернее, его отсутствию.
В прошлый раз рассматривались случаи поломки турбокомпрессора из-за дефицита смазки. Причем подчеркивалось, что сокращение подачи масла происходило где-то вне турбины: износился масляный насос, засорился масляный фильтр, забилась маслоподающая трубка. При этом турбокомпрессор испытывает тотальный масляный голод. Однако чаще недостаточная смазка узла подшипников происходит по еще более коварным причинам. Подача масла нарушается прямо внутри турбокомпрессора, из-за частичной или полной блокады каналов подачи масла. Почему такие неисправности коварнее?
Вспомним, с чего должна начинаться замена турбины? Правильно, с определения причины отказа турбоагрегата и ее устранения. Выявить недостаток давления в системе смазки двигателя или снижение расхода масла, поступающего к турбокомпрессору, несложно. Особенности процедуры измерения давления можно уточнить в сервисной документации двигателя. Как правило, это достаточно рутинная операция.
Что касается проверки производительности подачи масла к турбине, ее выполняют после установки нового турбоагрегата. Рекомендуется действовать так. Трубку слива масла из турбокомпрессора не подсоединяют к картеру, а опускают в подходящую емкость. Далее нужно запустить двигатель и дать ему поработать минуту в режиме холостого хода. За это время в емкости должно оказаться не менее 300 мл масла (для большинства турбин легковых автомобилей). Естественно, при измерении нужно следить за тем, чтобы уровень масла в двигателе не падал ниже минимума. Подчеркнем: проводить этот тест нужно с заведомо исправной турбиной. Дело в том, что масляные зазоры в парах трения играют роль ограничителей расхода смазки через турбокомпрессор (рестрикторов). Их величина соответствует норме только у новой турбины, не имеющей эксплуатационного износа или, тем более, аварийных повреждений.
Выполнив оба теста, можно получить объективную информацию и о состоянии масляного насоса, и о пропускной способности магистрали, по которой смазка поступает к турбине. Если испытания пройдены успешно, можно быть уверенным, что турбина получит требуемое количество масла.
Но… но, к сожалению, это не гарантирует, что узел подшипников вскоре не испытает масляного голода. В этом и заключается коварство неисправностей, о которых пойдет речь далее. «Как же так? Я проверил: давление масла в норме, заменил маслоподающую трубку, а турбина отказала из-за масляного голодания!», – пожимает плечами автомеханик. Как? А вот как…
Вскрытие № 4
Объект – оригинальный турбокомпрессор BorgWarner KKK модели K03 для легкового турбодизеля VAG, бывший в эксплуатации, не подвергавшийся восстановительному ремонту. Настройка пневматической камеры управления байпасным клапаном турбины соответствует техническим условиям завода-изготовителя.
После демонтажа корпусов турбокомпрессора выявлено следующее:
– в корпусе компрессора присутствует моторное масло (фото 1);
– радиальный и осевой люфты вала ротора значительно превышают нормы технических условий завода-изготовителя;
– лопатки колеса компрессора и ответные поверхности его корпуса имеют повреждения (натиры) из-за взаимного касания.
После разборки корпуса подшипников выявлено:
– шейки вала ротора имеют выработку в виде кольцевых канавок;
– в месте установки деталей упорного подшипника вал перегрет, видны цвета побежалости (фото 2);
– в масляных каналах корпуса подшипников и подшипников скольжения обнаружены посторонние твердые частицы – продукты деструкции моторного масла и фрагменты металла серебристого цвета, значительно превышающие по размеру величину масляного зазора и диаметр каналов в подшипниках скольжения;
– рабочие поверхности опорного подшипника изношены;
– упорный подшипник и ответные детали имеют следы абразивного износа, полусухого трения и перегрева (фото 3);
– масляный канал упорного подшипника полностью перекрыт посторонними твердыми частицами (фото 4);
– уплотнительные кольца корпуса подшипников и ответные канавки на валу ротора изношены (фото 5).
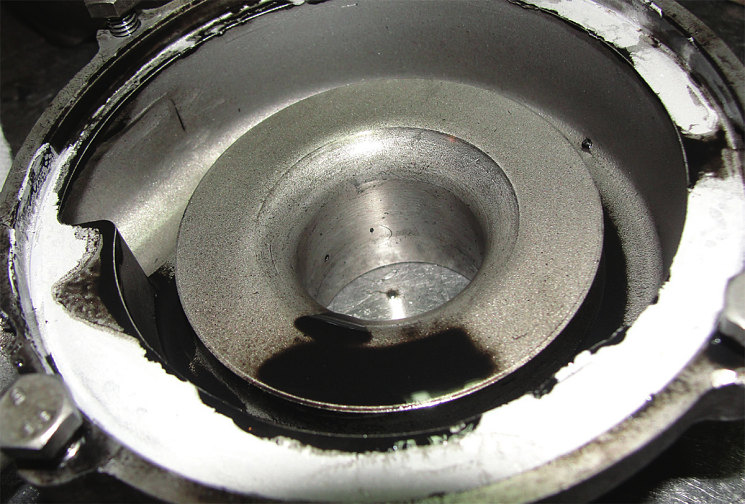
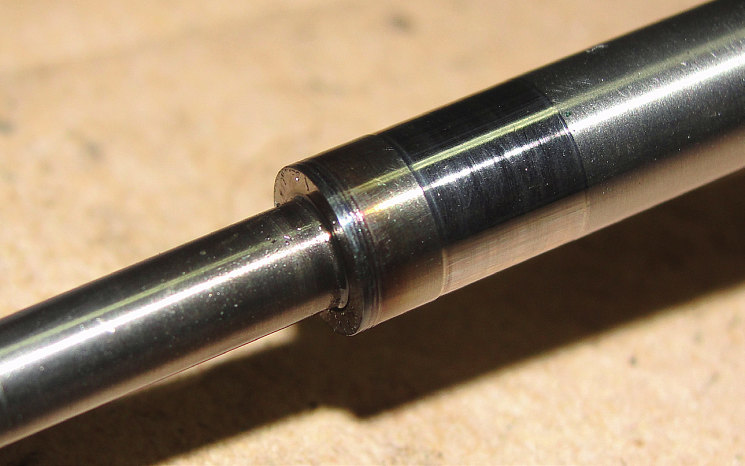
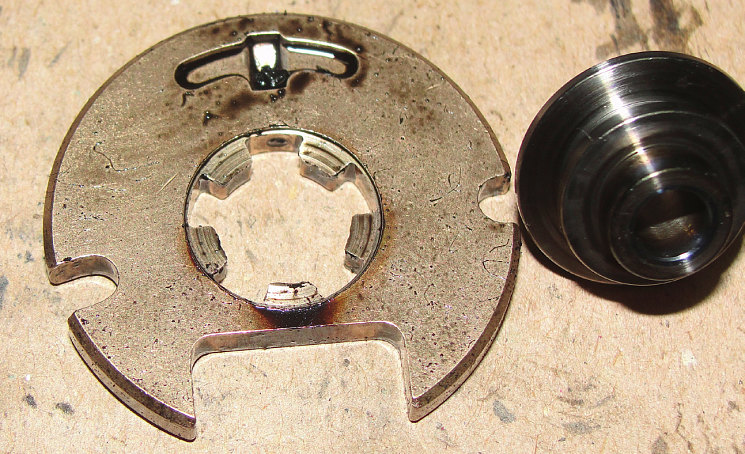
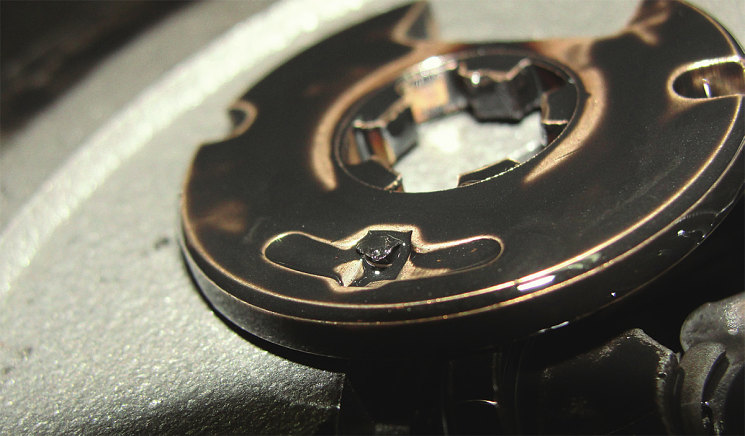
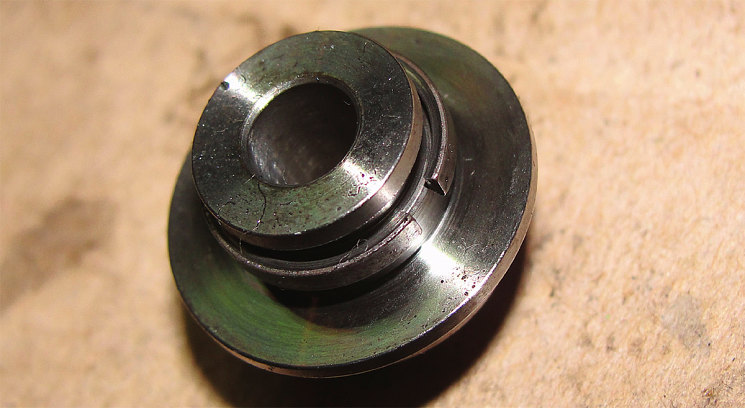
Выводы
Турбокомпрессор неработоспособен. Причины его поломки следующие:
– недостаточный расход масла через корпус подшипников (масляное голодание) из–за перекрытия масляного канала упорного подшипника скольжения посторонними твердыми частицами;
– абразивный износ деталей подшипникового узла посторонними твердыми частицами.
Твердые частицы, обнаруженные в корпусе подшипников, отношения к турбокомпрессору не имеют и попали в него с моторным маслом из системы смазки ДВС.
Без устранения выявленной причины выхода турбокомпрессора из строя установка нового или восстановленного турбокомпрессора приведет к тем же последствиям.
Бесстрастные фразы акта технической экспертизы допустимо переиначить так: турбокомпрессор скончался от «запора», вызванного посторонними частицами, циркулирующими по системе смазки двигателя.
Вначале разберемся, какие детали подшипникового узла турбокомпрессора наиболее подвержены такой напасти.
Масляный канал в корпусе подшипников, который распределяет поток смазки, направляя его части к опорным и упорному подшипникам, имеет достаточно большой диаметр, а потому перекрывается очень редко. Чаще блокируются каналы в подшипниках скольжения. В опорном подшипнике, как правило, устроено четыре радиальных канала диаметром порядка миллиметра. Оставить его совсем без масла сложно. Такие случаи единичны и обычно происходят из-за применения некачественного масла или нарушения периодичности его замены. В результате масло частично превращается в субстанцию, напоминающую гуталин. Мало того, что гуталин сам по себе не годится для смазки турбины, он способен закупорить сразу несколько масляных каналов.
Другое дело – упорный подшипник. В упорном подшипнике масло поступает к контактной поверхности, как правило, по одному-единственному каналу. Конструкции с двумя и даже тремя каналами – редкое исключение. Мало того, что канал один, он еще и достаточно протяженный, и узкий. Например, у турбокомпрессоров легкового типоразмера масляный канал имеет диаметр 0,8 мм. Поэтому чаще всего случается «запор» именно упорного подшипника. Опыт показывает, что особенно подвержены такой болезни турбины ККК (модели К03, К04). Видимо, в них так устроен проток масла, что грязь непременно попадает в упорный подшипник.
Износ любого подшипника не сулит ничего хорошего, особенно в устройстве, ротор которого вращается с частотой до 5000 оборотов в секунду. Износ упорного подшипника – не исключение. Он приводит к осевому смещению вала ротора в направлении компрессора. Вследствие этого вначале нарушается геометрия лабиринтных уплотнений вала – меняется взаимное положение неподвижного уплотнительного кольца и канавки на валу – а затем происходит контакт и повреждение этих деталей. Уплотнения перестают быть бесконтактными, их работоспособность нарушается с вытекающими отсюда последствиями. Большое осевое смещение ротора также может привести к касанию компрессорного колеса о корпус компрессора. Резкое снижение эффективности турбокомпрессора будет сопровождаться «малиновым звоном».
Что представляют собой крупные частицы, блокирующие масляные каналы? В этом случае «металл серебристого цвета» – это стружка, продукт износа деталей двигателя. Довольно распространенная история. Эксплуатационный износ механической части ДВС – явление обычное. Однако замечено, что некоторые двигатели вырабатывают стружку активнее других, и поэтому чаще не уживаются со своими турбоагрегатами. О них будет упомянуто далее.
Посторонние частицы, присутствующие в масле, не проходят сортировку. Поэтому наряду с крупными там есть и более мелкие. Понятно, что «запор» способны вызвать частицы, величина которых сравнима с сечением масляных каналов или превышает его. Остальные также не безвредны: проходя в зазор между поверхностями трения, самые мелкие их полируют, средние шлифуют, крупные наносят глубокие кольцевые риски. Так что масляному голоданию обычно сопутствует и банальный абразивный износ.
Чтобы минимизировать риск повреждения турбины посторонними частицами, стоит прислушаться к рекомендациям производителей. Замену турбины всегда совмещать с заменой моторного масла и фильтра, а иногда и с тотальной очисткой системы смазки, включая масляный картер. Не совмещать замену турбины с капитальным ремонтом двигателя – после него в двигателе остается много отходов механической обработки, а последующая приработка новых деталей сопровождается интенсивным образованием стружки. Ну и, конечно, регулярно выполнять ТО двигателя с применением качественных расходников и масла.
У читателей, давно не освежавших тонкости устройства системы смазки ДВС, может возникнуть недоумение: откуда в масле какие-то посторонние частицы, тем более крупные, если оно фильтруется? Да, фильтруется, но частично. Фильтрация масла становится полнопоточной только когда двигатель прогрет до рабочей температуры. И конечно, при условии, что пропускная способность масляного фильтра по какой-либо причине не нарушена. В остальных случаях предохранительный клапан фильтра приоткрыт, и часть масла минует фильтр. Поэтому нужно принять как аксиому: все, что попало в масло, рано или поздно окажется в лабиринтах системы смазки, в том числе в узле подшипников турбокомпрессора. И мы в этом еще не раз убедимся.
В подтверждение того, что «запор» подшипникового узла турбокомпрессора – явление не единичное, а, напротив, массовое, рассмотрим еще несколько аналогичных случаев.
На фото 6, 7 показан результат «вскрытия» турбокомпрессора KKK модели K03, применяющегося на 2,5-литровом двигателе D4CB автомобиля Hyundai Starex CRDI. Фото 8, 9 – это внутренности похожей турбины такого же двигателя, но другого «корейца» – KIA Sorrento 2.5 CRDI. Видно, что в обоих случаях причина их попадания на стол «прозектора» идентична – обилие крупной металлической стружки, блокировавшей масляные каналы в подшипниках скольжения. Последствия также схожи: фатальный износ пар трения, прежде всего в упорном подшипнике, увеличение радиального и осевого люфтов ротора, повреждение уплотнений, касание колеса и корпуса компрессора.
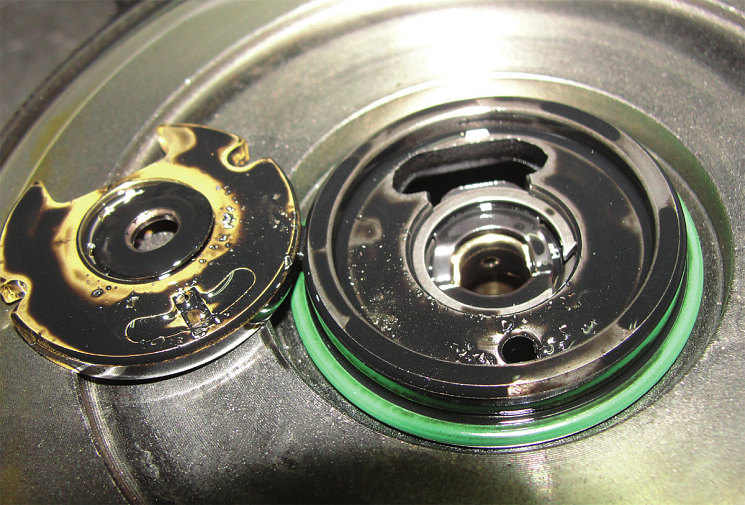
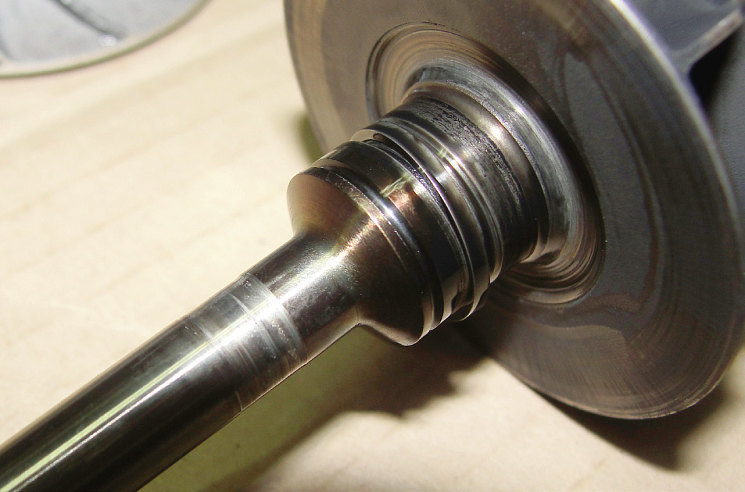
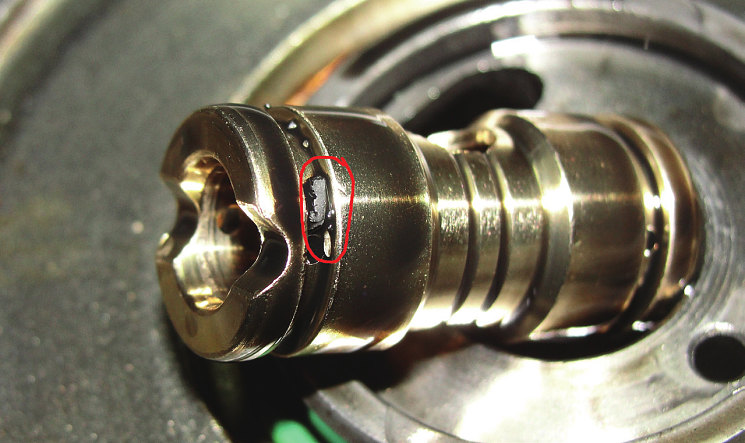
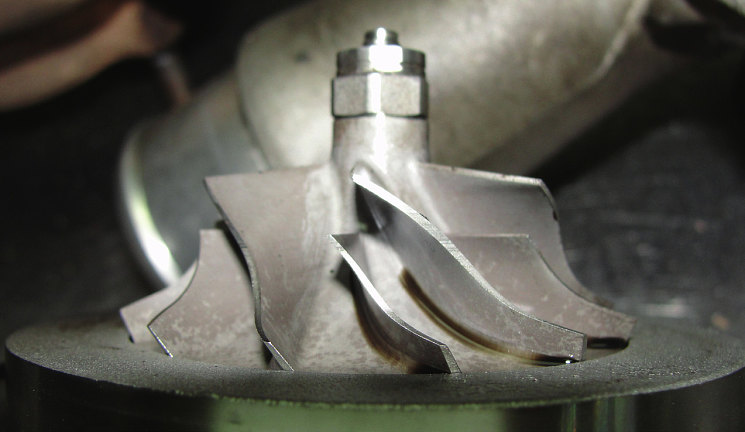
Кстати, турбокомпрессоры упомянутых корейских автомобилей пользуются повышенным спросом на вторичном турборынке. У вышедших из строя агрегатов картина повреждений обычно похожа до мелких деталей. По неофициальным данным, полученным от официальных представителей этих популярных брендов, обилие стружки – результат износа масляного насоса, который начинается задолго до пробега 100 тыс. км. Так что тут очистка системы смазки от посторонних частиц даст лишь временный эффект. Радикально решить проблему может только замена изнашивающейся детали двигателя.
Начав разговор о двигателях – истребителях турбокомпрессоров, нельзя не упомянуть еще об одном популярном агрегате – моторе DISI Turbo автомобиля Mazda CX‑7. Двигатель 260-сильный, прилично форсированный и теплонапряженный. В силу этого турбокомпрессору Hitachi K0422–582/581 приходится туго, несмотря на охлаждаемый корпус подшипников. Мало того, двигатель в изобилии генерирует стружку, источником которой, по сведениям от мотористов, являются постели распредвалов. Что из этого вытекает, отражено в выдержках из протокола вскрытия одной из таких турбин.
Вскрытие № 5
Внешним осмотром установлено:
– корпус турбины и корпус подшипников имеют следы перегрева (цвета побежалости) и коррозии;
– в отверстии подвода моторного масла в корпус подшипников обнаружены посторонние твердые частицы (фото 10).
После демонтажа корпусов турбокомпрессора выявлено:
– в корпусе турбины обнаружено моторное масло;
– внутренние поверхности корпуса и колесо турбины закоксованы продуктами деструкции моторного масла;
– радиальный и осевой люфты вала ротора превышают нормы технических условий завода-изготовителя;
– лопатки колес турбины и компрессора повреждения из-за касания корпусных деталей;
После разборки корпуса подшипников обнаружено:
– в масляных каналах корпуса подшипников и упорного подшипника скольжения обнаружены посторонние твердые частицы (продукты деструкции моторного масла, фрагменты металла), размеры посторонних частиц значительно превышают величину масляного зазора (фото 11);
– шейки вала ротора и рабочие поверхности опорного подшипника скольжения имеют следы абразивного износа в виде кольцевых рисок;
– упорный подшипник и ответные детали его узла изношены;
– уплотнительные кольца корпуса подшипников повреждены (фото 12).
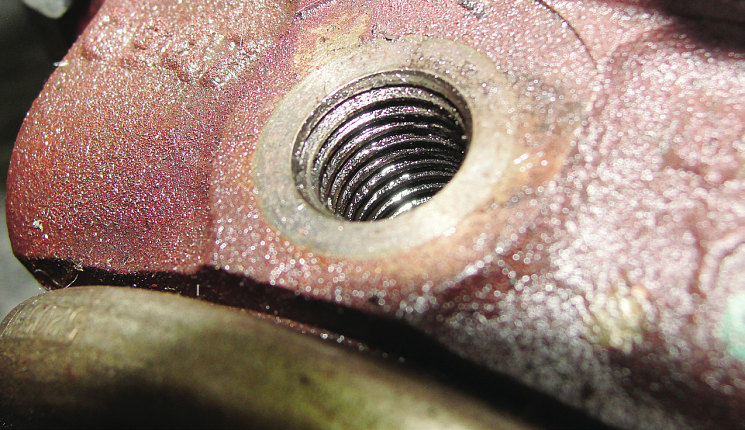
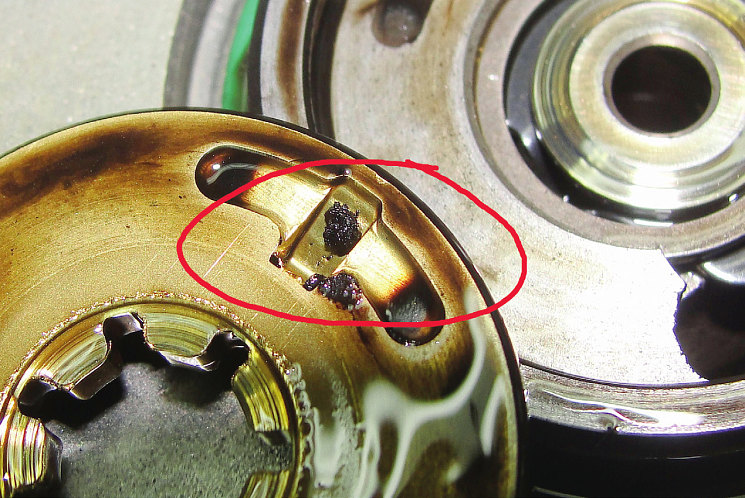
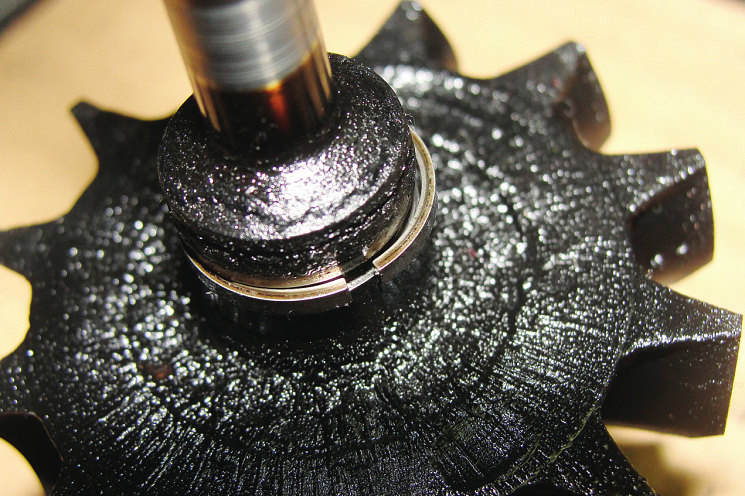
Выводы экспертизы не приводим, поскольку они очевидны – турбина пала жертвой двигателя. На что следует обратить внимание? В отличие от предыдущих, данный турбоагрегат – бензиновый. Бензиновые турбины отличаются от дизельных повышенной рабочей температурой. К чему это приводит?
В результате термической деструкции масла в любом турбокомпрессоре со временем накапливаются отложения. В бензиновых турбинах они приобретают характер твердого кокса темно-коричневого цвета с лаковой поверхностью. Зафиксировано немало случаев масляного голодания подшипников из-за коксования масляных каналов или их блокирования отслоившимися частицами кокса. Собственно, и в приведенном выше случае посторонние частицы – это смесь стружки и твердых отложений. В дизельных турбинах отложения рыхлые, кашеобразные, черного цвета. Здесь каналы коксуются редко, если такое и случается, то обычно – в подшипниках со стороны турбинного колеса.
Более ярко выраженный случай блокирования масляных каналов коксом иллюстрируют фото 13–15. На них зафиксированы внутренние органы турбокомпрессора бензинового 1,6-литрового двигателя EP6DT1, что широко применяется на автомобилях группы PSA. Не стоит забывать, что углеродсодержащий кокс – это прекрасный абразивный материал. Так что пары трения подшипникового узла страдают не только от полусухого трения, вызванного дефицитом смазки, но и от истирания.
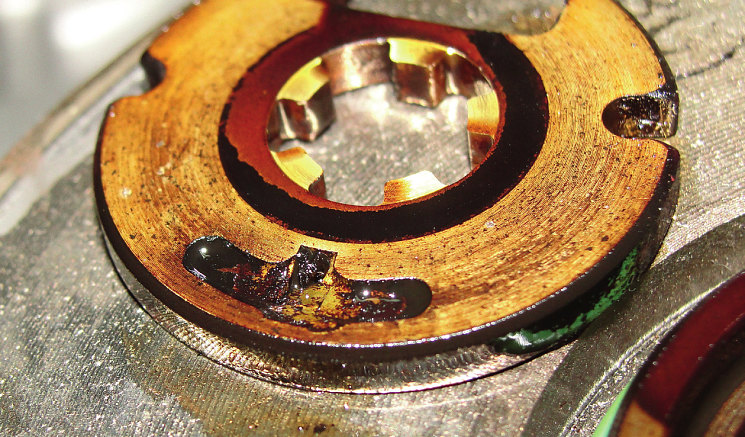
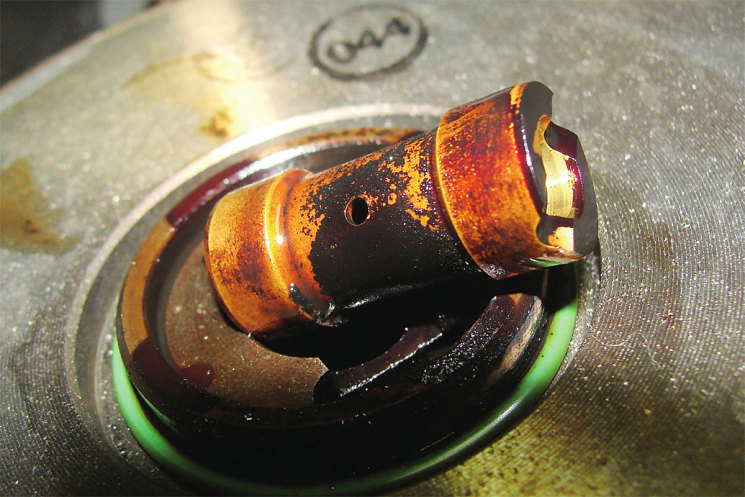
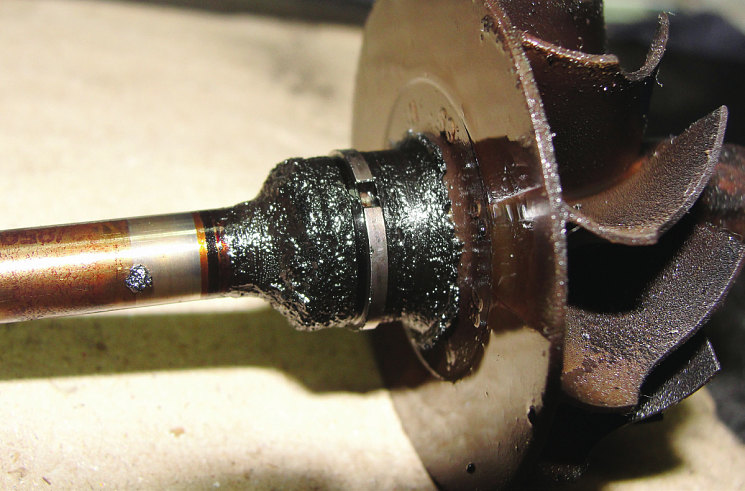
Так уж непреднамеренно получилось, что все вскрытые нами до сих пор турбокомпрессоры – агрегаты легковых двигателей. Может сложиться ложное представление, что более массивным грузовым турбинам «запоры» не страшны. Действительно, у них валы так валы, подшипники – во подшипники, а уж масляные каналы..! На самом же деле грузовые турбины ничуть не меньше страдают от «запора», что и подтверждает нижеследующее вскрытие 20-килограммового «гарретта» от двигателя Detroit Diesel объемом 12,7 л тягача Freightliner.
Вскрытие № 6
Объект – оригинальный турбокомпрессор Garrett GTA, бывший в эксплуатации, не подвергавшийся восстановительному ремонту.
Внешним осмотром установлено:
– в резьбовом отверстии фланца подвода моторного масла в корпус подшипников обнаружены следы применения герметика (фото 16);
– на корпусе турбины замечены последствия перегрева (цвета побежалости);
После демонтажа корпусов турбокомпрессора выявлено следующее:
– осевой и радиальный люфты ротора превышают нормы технических условий завода-изготовителя;
– лопатки колес турбины и компрессора имеют повреждения из-за касания корпусных деталей в осевом и радиальном направлениях;
Разборка корпуса подшипников показала:
– сечения масляных каналов корпуса подшипников и подшипников скольжения перекрыты посторонними твердыми частицами (фрагментами герметика, металла, продуктами деструкции моторного масла) (фото 17);
– вал ротора деформирован и закоксован продуктами деструкции моторного масла (фото 18);
– на шейках вала обнаружены последствия полусухого трения, перегрева, прихвата и наволакивания материала опорных подшипников;
– опорные подшипники имеют следы полусухого трения, прихвата, перегрева и износа, масляные каналы опорных подшипников частично затянуты вследствие трения с валом ротора (фото 19);
– места установки опорных подшипников в корпусе повреждены в результате полусухого трения и наволакивания материала подшипников (фото 20);
– упорный подшипник скольжения и ответная деталь его узла имеют следы полусухого трения перегрева и износа (фото 21);
– уплотнительные кольца и ответные канавки на валу ротора повреждены.
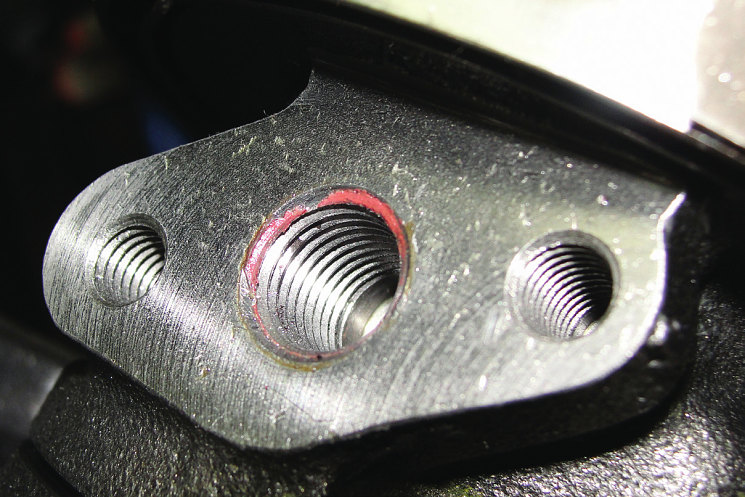
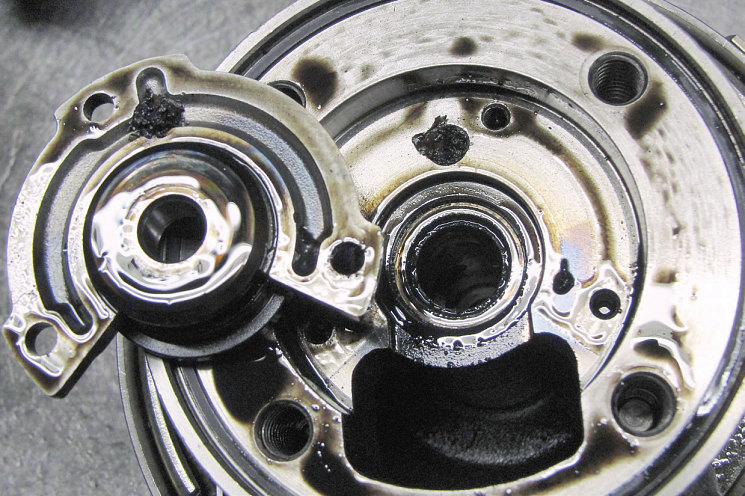
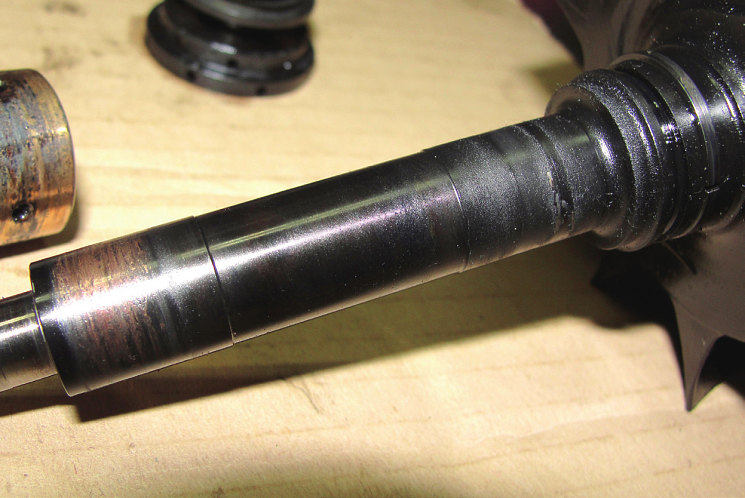
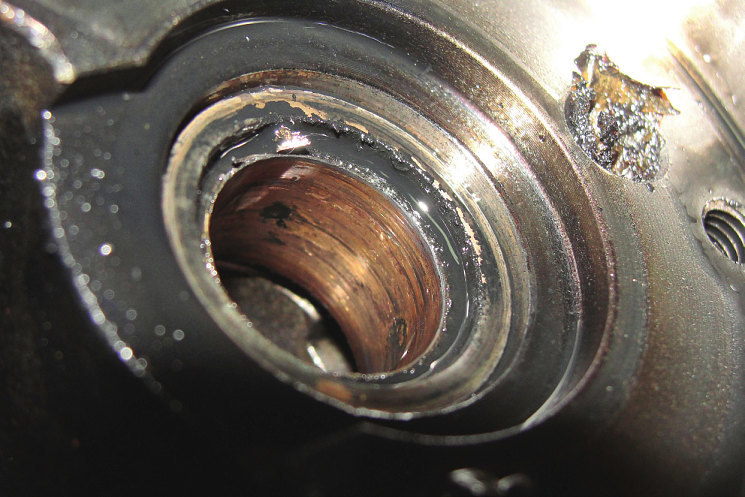
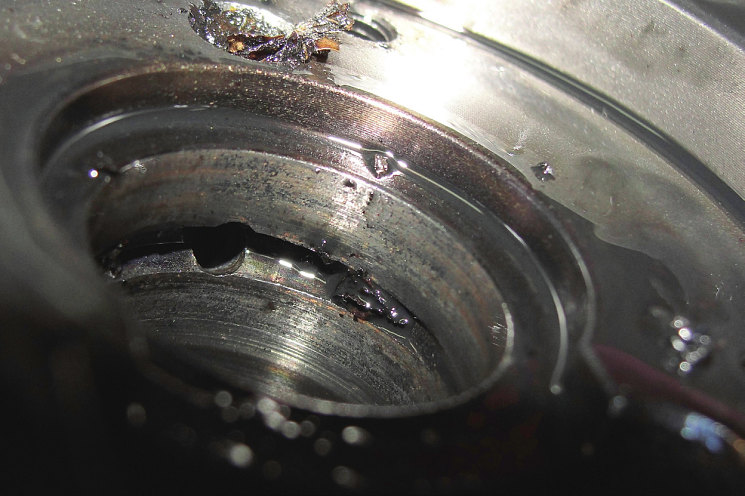
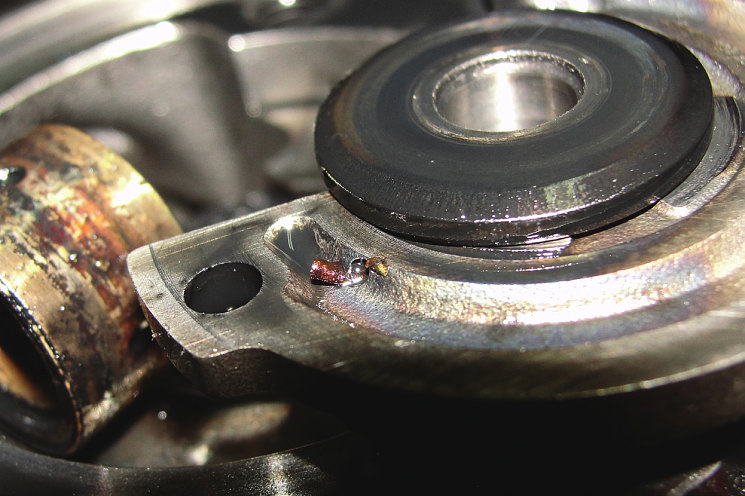
Выводы
Турбокомпрессор неработоспособен.
Причина выхода данного турбокомпрессора из строя – недостаточный расход масла через корпус подшипников из-за перекрытия масляных каналов корпуса подшипников и подшипников скольжения посторонними твердыми частицами. Масляное голодание вызвало полусухое трение, перегрев и сварку трением деталей подшипникового узла, деформацию вала ротора и увеличение его люфтов, касание колес и корпусных деталей, повреждение уплотнительных колец.
Что к этому можно добавить? Только то, что применение герметика при монтаже турбокомпрессора – распространенная причина масляного голодания подшипникового узла турбины. «А что такого – я же приклеил фланец слива масла?» Во-первых: выдавливаясь вовнутрь сливного отверстия, герметик уменьшает его сечение, возрастает интенсивность просачивания масла сквозь уплотнения. Во-вторых, кусочки выдавленного герметика рано или поздно отвалятся, попадут в картер, а оттуда вернутся в турбокомпрессор уже с противоположной стороны. К такому же результату может привести и неаккуратное использование герметика при ремонте двигателя. Не верите? Взгляните на фото 22!
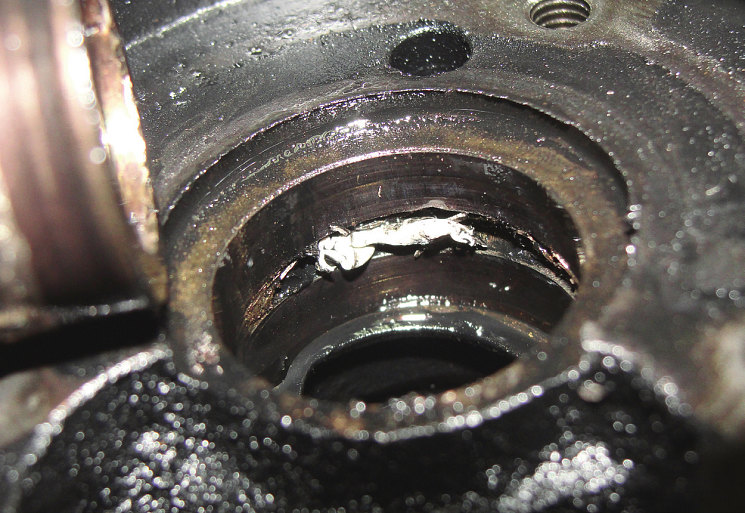
Продолжение следует