«Экспертиза технического состояния и причины неисправностей автомобильной техники». Отрывок из книги. Глава 5
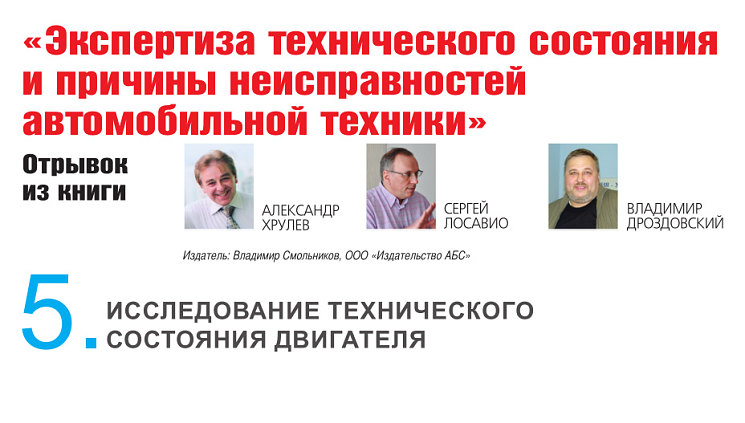
5. Исследование технического состояния двигателя
Поиск неисправностей и их причин во многих случаях неизбежно приводит к необходимости изучения состояния деталей механической части. Действительно, на деталях могут быть следы износа и повреждений, которые могут указывать на причину неисправности. В таком случае без разборки выявить причину неисправности невозможно.
Совершенно очевидно, что разборка является одним из завершающих этапов исследования двигателя и должна проводиться тогда, когда остальные этапы уже выполнены. Однако на практике значительное количество исследователей нередко совершает стандартную ошибку – проводит разборку двигателя без проведения тех работ, которые должны предшествовать разборке. В первую очередь речь идет о подробно описанной в предыдущем разделе безразборной диагностике, когда многие признаки повреждений можно выявить простыми диагностическими методами.
Понятно, что при выполнении необоснованной и/или поспешной разборки двигателя некоторые важные признаки теряются, причем теряются безвозвратно. Примеры подобной утери данных весьма многочисленны. Так, например, следует напомнить об осмотре цилиндров с помощью эндоскопа – этим способом можно выявить характерное замасливание различных зон камер сгорания. Если замаслены тарелки клапанов, иногда даже со следами стекания масла с их нижнего края по стенке камеры, – это типичный признак негерметичности уплотнений стержней клапанов (маслосъемных колпачков) и/или износа направляющих втулок. Если же головки клапанов сравнительно сухие, а в верхней части цилиндра круговая зона замасливания, – это типичный признак износа или повреждения поршневых колец. Однако стоит только разобрать двигатель, как все эти признаки окажутся неочевидными и фактически утерянными.
журнала "АБС-авто" № 12 (2018 г.)