Автостекло в подробностях...
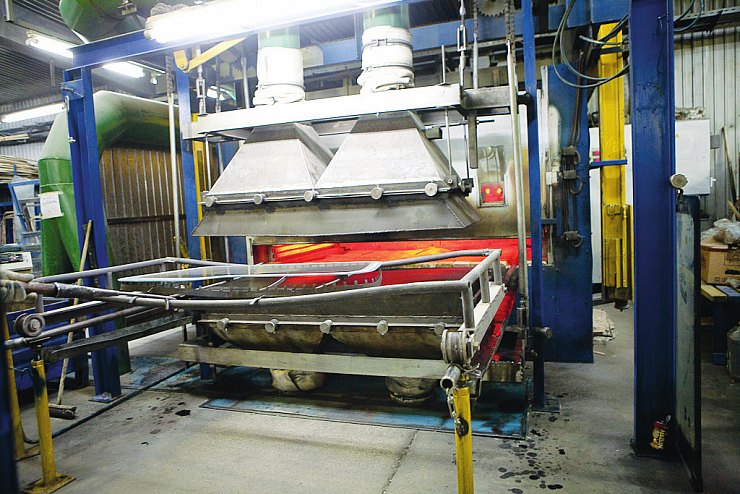
Профессионал в любом деле (и уж точно – в авторемонте) отличается тем, что знает «историю вопроса»: когда был изобретен автокомпонент, с которым он работает, как он производится, в каком направлении его совершенствуют.
На первый взгляд, эти знания могут показаться излишними. Но это далеко не так: они позволяют не совершать так называемых «глупых» ошибок, способных мгновенно уничтожить результат многочасового труда. Мастер должен не просто соблюдать технологию, но и понимать, что конкретно произойдет, если он ее нарушит.
Сегодня мы начинаем серию публикаций, посвященных автомобильным стеклам, которые практически за относительно небольшое время из простой «загородки от ветра» стали высокотехнологичным конструктивным элементом автомобиля, от которого зависит не только комфорт, но и безопасность людей.
В настоящее время существует множество разновидностей автомобильных стекол, разобраться в которых без специальных знаний очень сложно. И мы в нескольких номерах журнала расскажем о типах их конструкции, маркировке, правилах замены и многом другом. Но начнем с начала – с их производства.
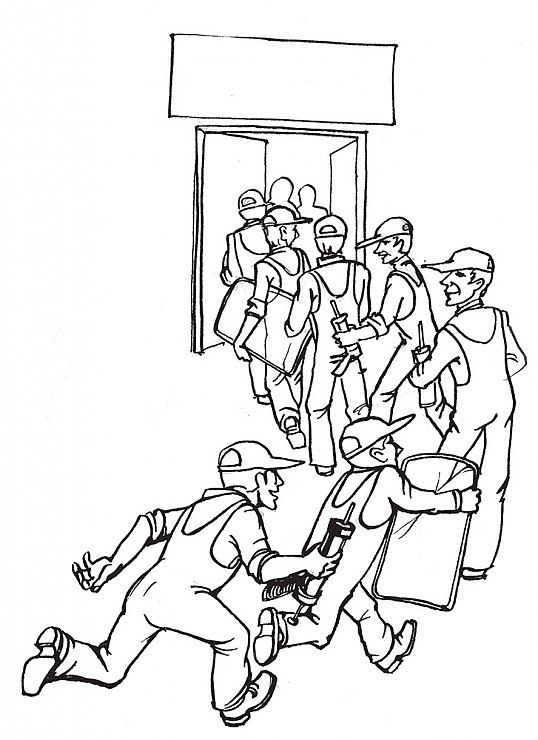
История
Самое первое автостекло представляло собой кусок стекла небольшого размера, закрепленный перед водителем. Он служил для защиты от насекомых и песка, которые попадали в дорожные очки водителя, а также в качестве «ветрозащитного экрана». Со временем производители автомобилей решили обеспечить защиту от ветра и грязи для всех пассажиров – и начали устанавливать стекла по периметру автомобиля.
Сначала на дверях и на задней части автомобиля устанавливали простое однослойное стекло. А в 1927 году появилось первое многослойное ветровое стекло (два слоя отожженного стекла накладывались друг на друга с прокладкой из ацетата целлюлозы). Затем многослойное стекло начали устанавливать во всех окнах автомобиля.
Как его производят
Основным материалом для производства стекла является песок. Но не просто «вообще песок», а чистый кварц (диоксид кремния). Прочие компоненты (которых, кстати, немало) служат для придания прозрачности, упрощения процесса изготовления, добавления цвета и повышения эффективности производства стекла.
В общем-то, производство автомобильных стекол на первых этапах ничем не отличается от производства оконных стекол, стаканов, бутылок. На начальной стадии из смеси песка, кальцинированной соды, доломита и известняка создается «партия замеса», или «шихта». Каждый производитель использует собственный рецепт (для придания продукту специальных свойств и характеристик), но все применяют одни и те же основные материалы, которыми пользовались еще древние шумеры: песок и соду. Ну и добавляют стекольный бой – для экономии.
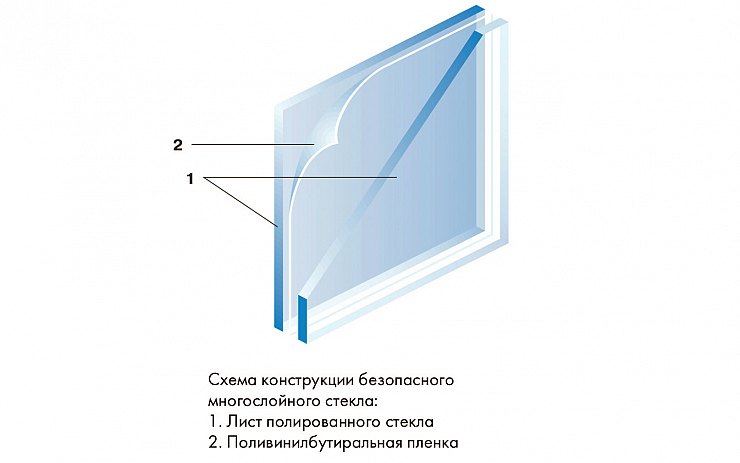
Затем собранная по рецепту смесь подается в плавильную печь (лер) для гомогенизации сырья – проще говоря, в печи все ингредиенты расплавляются, перемешиваются и становятся единой стекольной массой.
А вот дальше начинаются тонкости. Требования к автомобильным стеклам по толщине и чистоте поверхности значительно выше, чем, например, к оконным. И потому для автостекол используют старинную технологию (по которой в Средние века делали зеркала) – стекольную массу выливают в модульную ванну, где находится расплавленное олово. Поскольку температура плавления олова ниже, чем у стекла, то стекло застывает на абсолютно ровном расплаве металла.
Ширина и толщина стекла с помощью объема подачи массы и ее температуры формируются согласно спецификации заказчика.
Когда стекло достигает температуры примерно 1130°F, (610°С), оно становится твердым – и его извлекают из модульной ванны и помещают в печь отжига, где оно постепенно охлаждается до состояния, при котором его можно резать по размерам, требуемым для транспортировки и перемещения.
Постепенное охлаждение в печи отжига необходимо, чтобы снять внутренние напряжения в стекле. И в результате этой процедуры производится отожженное стекло.
Основные виды автостекол
В автомобильной промышленности ветровые и боковые стекла бывают многослойные, закаленные и термоупрочненные. Для разных моделей автомобилей производят стекла с различными свойствами или с их сочетанием.
Многослойное стекло состоит из нескольких различных компонентов. В основном это внешний слой из стекла, промежуточный из поливинилбутираля (PVB) и внутренний слой – тоже из стекла. Оба стеклянных слоя обычно имеют одинаковую толщину: 0,09 дюйма, или 2,29 мм. Хотя делаются также и специальные пуленепробиваемые «сэндвичи» из 10 и более слоев стекла (чаще всего сапфирового).
По заказу клиента могут быть использованы различные покрытия или дополнительные компоненты. Например, может использоваться солнцезащитное покрытие, которое служит в качестве фильтра для ультрафиолетовых и инфракрасных лучей.
Для обозначения каждой из поверхностей многослойного стекла применяется цифровая маркировка – она начинается с внешней поверхности и идет по направлению к внутренней. Поверхности маркируются цифрами от 1 до 4 (в случае с двухслойным стеклом).
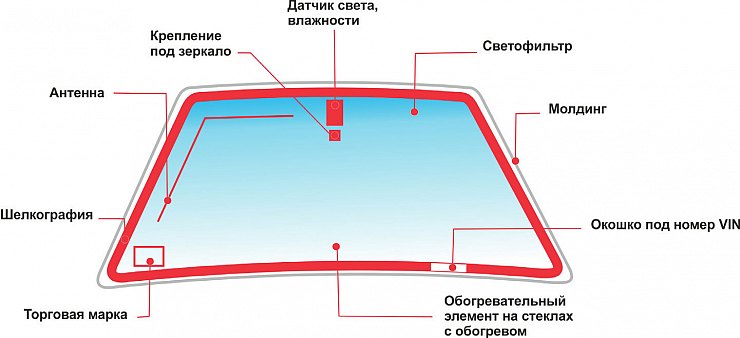
Закаленное стекло примерно в 5 раз прочнее отожженного стекла. Закалка повышает прочность, что гарантирует отсутствие повреждений при захлопывании дверей автомобиля, поэтому такое стекло идеально походит для установки на дверках и других подвижных частях автомобиля.
Такая прочность достигается путем более быстрого охлаждения наружного слоя, чем «сердцевины». Однако прочность – не единственное преимущество закаленного стекла. При повреждении оно разрушается на мелкие осколки с тупыми краями, гораздо менее опасными, чем осколки отожженного стекла.
Термоупрочненное стекло появилось благодаря применению новой технологии закалки тонкого (от 1,7 до 2,0 мм) стекла. Термин «термоупрочненное» обозначает промежуточный класс между отожженным и закаленным стеклом.
Термоупрочненное многослойное стекло сегодня наиболее широко используется для производства ветровых и боковых стекол в автомобилях. Оно позволяет снизить уровень шума внутри автомобиля, уменьшить воздействие проникающих внутрь салона ультрафиолетовых лучей. И что самое важное, максимально уменьшить риск травмирования людей при его разрушении.
Как его делают изогнутым
Есть старая шутка: «Паровозы надо давить, пока они чайники». Вот и вырезать многослойное стекло под размер отверстия в кузове автомобиля начинают еще тогда, когда оно – всего лишь стопка из не склеенных между собой стекол.
Эту стопку вырезают «наискось» – будущая «внутренняя часть» делается меньше, для того чтобы после изгибания стекол их края совпадали. Затем части разделяют и тщательно зачищают.
Далее стекла опять соединяют и устанавливают в приспособлении для гибки, которое помещают в специальную печь, где нагревают до температуры примерно 1125°F (607°С). Стекло становится мягким и принимает форму, которая полностью совпадает с формой спроектированного отверстия автомобиля.
Затем стекла вновь разделяют, подвергают мойке – и между ними помещают слой PVB. Далее уже собранный пакет пропускают между роликами для максимального удаления воздуха между частями.
На данном этапе пакет из стекол и пленки еще не прозрачен. Для этого есть завершающая операция – «сборку» примерно на 45 мин помещают в автоклав, где она нагревается и подвергается максимальному давлению. В автоклаве протекает химическая реакция, которая «спаивает» все вместе, что и придает ветровому стеклу чистоту и прозрачность.
Стандарты на автомобильные стекла
В мире существует несколько стандартов, определяющих свойства автомобильных стекол, технологию их производства, качество материалов и многое другое.
Например, европейские производители пользуются стандартом UNECE R43 (это соглашение, которое определяет основные и специфические требования, критерии отбора и соответствия изделий).
Китайский стандарт (GB 9656, GB 5137.1, GB 5137.2, GB 5137.3) очень схож с UNECE R43 – за исключением пропускания видимой части спектра для ветровых стекол, а также того, что в UNECE R43 есть понятие «понижающей зоны B», не предусмотренной в GB 9656.
Американцы пользуются своими документами. Федеральные стандарты по безопасности автомобилей (FMVSS) 205, которые включают стандарт ANSI Z26.1, определяют требования к применению автомобильных стекол, а также основные критерии функциональных характеристик остекления.
Вкратце данный стандарт определяет проведение некоторых эксплуатационных испытаний стекол, установленных на автомобиле. Наиболее распространенными являются испытания на пропускание света и на проникновение.
Стандарт FMVSS 205 указывает на то, что лобовое стекло должно выдерживать попадание стального шарика, брошенного с определенной высоты, и не допускать его проникновения внутрь. Для проведения указанных испытаний промежуточный слой PVB должен иметь толщину как минимум 0,03 дюйма, или 3 мм. Любой другой, более тонкий, слой дает возможность шарику пройти через стекло, что не позволяет применять такое стекло в качестве ветрового.
Должно обеспечиваться «70% проникновение света», что означает то, что 70% имеющегося света должно проникать через стекла для обеспечения оптимальной видимости. Любые другие, более низкие, показатели проникновения света указывают на то, что стекло не может использоваться в качестве ветрового стекла или стекол, устанавливаемых непосредственно слева или справа от водителя либо перед стойкой «В».
На всех автомобильных стеклах, произведенных по тому или иному стандарту, есть соответствующие обозначения. О том, как их правильно читать, мы поговорим во второй части, которая будет опубликована в следующем номере журнала.