Delphi производит компоненты тормозных систем и обучает новым технологиям
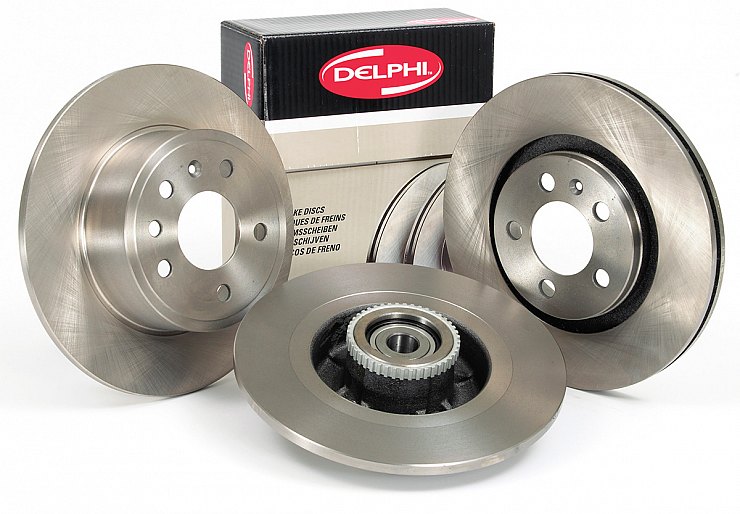
В последние годы на рынке автокомпонентов и запчастей заметным явлением стала новая стратегия ведущих мировых производителей. Период завоевания своего места на российском авторынке сменяется более глубоким и основательным проникновением на сервисные площадки национального автосервиса.
Такой подход говорит о многом – и в первую очередь о том, что лидеры мировой индустрии верят в перспективы расширения рынка. А значит, пришло время закрепить свое присутствие. И подтягивать свои главные силы – богатейшие знания и опыт, наработанные на производственных площадках зрелых рынков.
Наш пассаж кому-то может показаться слегка (а может, и существенно) устаревшим. И мы с этим согласимся – не вчера появились на местных просторах десятки производственных линий по изготовлению современных деталей и компонентов для автосборки и вторичного рынка. Но таких значительных усилий компаний, представляющих известнейшие мировые бренды, в профессиональном просветительстве специалистов по продвижению
продукции и механиков автосервисов мы еще не наблюдали. И это, конечно, радует. Потому что мировые гранды такими действиями хотя бы частично компенсируют чудовищные недостатки наших национальных профильных обучающих заведений.
За аргументами далеко ходить не будем, а вспомним, или прочтем, журнал «АБС-авто» № 4/2013. Кто забыл, напоминаем. В интер-
вью с Люсией Моретти, старшим вице-президентом компании Delphi, президентом Delphi Product & Service Solutions можно прочесть: «Мы знаем, что современный автомобиль – это больше кибернетический, чем механический объект. И поэтому перед нашей компанией, как поставщиком ОЕМ, стоит большая и ответственная задача – чтобы знания об особенностях наших систем передавались специалистам по авторемонту». Сегодняшний, майский, номер журнала мы обещали посвятить тормозной системе. Вот как ее видит упомянутая выше крупнейшая мировая компания Delphi.
Революция в ремонте
Современные автомобили оснащаются все более сложной электроникой. Использование ее в системах, таких как тормозная, вносит огромный вклад в безопасность дорожного движения, обеспечивая стабильную управляемость ТС на дороге. Она помогает водителю осуществлять торможение намного быстрее и сохранять контроль над автомобилем во время сложных маневров. Но в результате автомобили стали более сложными, а технологии, необходимые для их диагностики и ремонта, комплексными.
Автомастерские должны уметь ремонтировать все большее количество таких систем, как антиблоки-ровочная система (АБС) и контроль стабильности. Электронное управление позволяет системам быстрее реагировать на действия водителя и приводит к сокращению тормозного пути. К тому же внедрение в автомобиль электронных компонентов реализует очень важную функцию интеграции нескольких систем, ранее работающих в раздельном режиме. Растущий интерес к установке электронной системы мониторинга давления в шинах помогает обеспечить максимальное сцепление автомобиля с дорогой и минимизировать сопротивление качения. А также позволяет обеспечить электронную связь педали тормоза с главным тормозным цилиндром.
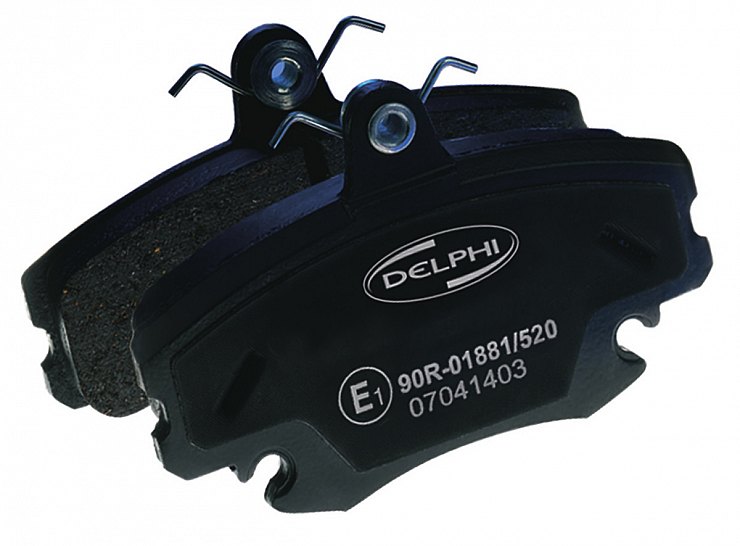
Таким образом, электроника оказывает революционное влияние на работу автомобиля, что неизбежно отзывается революционными технологиями в его обслуживании и ремонте. Визуальной проверки и хорошего знания системы уже недостаточно. Без электронного диагностического инструмента работа может занять намного больше времени, или стать вовсе невозможной.
Например, в случае некорректного ремонта в связи с отсутствием диагностического инструмента и необходимых знаний механик может «запутать» систему управления, что приведет к неисправностям. Они затем на дороге могут проявиться любыми чрезвычайными ситуациями. Наличие необходимых диагностических инструментов становится важнейшим условием эффективной работы автомастерской. Это ключевой момент обеспечения постоянного рабочего процесса и повышения прибыльности каждой операции по ремонту.
Новые вызовы
Delphi разрабатывает новые образцы колодок для систем тормозов в течение шести месяцев с выпуска нового автомобиля, поэтому процессы разработки и испытания дисков и колодок должны быть одновременно и скорыми, и высоконадежными. Колодки для вторичного рынка также проходят жестко регламентированные всесторонние испытания на проверку качества. Все новые разработки проходят полные эксплуатационные испытания на работу в крайне неблагоприятных условиях, соответствующих самым плохим дорогам мира. На рынок поступают только изделия, успешно прошедшие самые жесткие испытания.
Группа инженеров – разработчиков Delphi конструирует ежегодно около 150 тормозных колодок, предназначенных для работы в конкретных условиях, указанных заказчиком. Эти изделия применяются приблизительно на 600 моделях автомобилей. Чтобы компания могла выйти на рынок тормозных компонентов первой, всесторонние испытания обычно должны быть выполнены производителем за три месяца. Каждая колодка после этого полностью разбирается, а компонент/материал, из которого она изготовлена, подвергается анализу с особым вниманием по следующим аспектам:
• типу и качеству регулировочных прокладок;
• конструкции и типу стали опорного диска;
• конструкции и типу фрикционных накладок;
• типу и качеству аксессуаров.
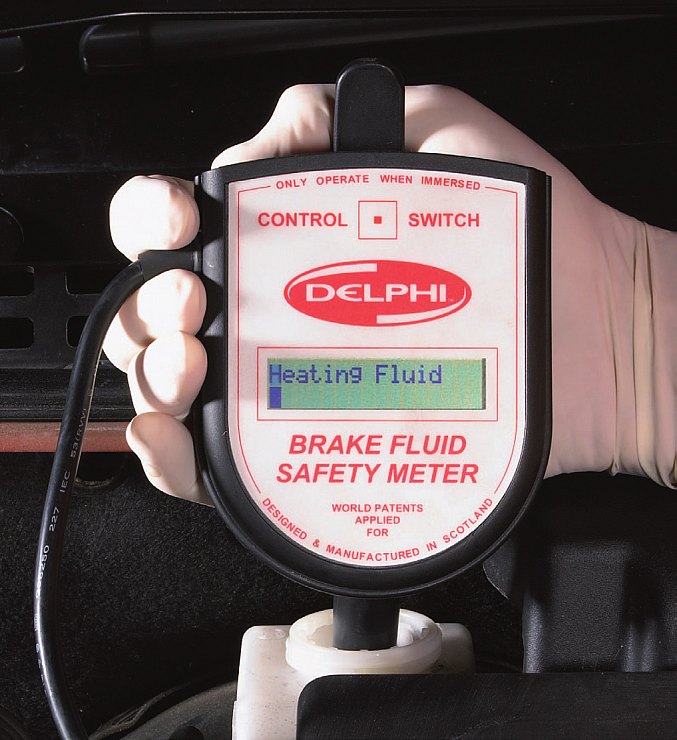
Используемая Delphi номенклатура фрикционных материалов постоянно пересматривается. Каждый год испытывается и оценивается около 200 новых материалов, и результаты сравниваются с уже применяемыми материалами. Основные сравниваемые параметры включают: коэффициент трения, стабильность коэффициента трения и степень износа (при определенных температурах или при определенных условиях).
Выполнив полный анализ оригинального изделия, инженеры отдела разработки изделий Delphi переходят к выполнению рабочих чертежей. Они также выбирают тип фрикционных материалов для каждой модели автомобиля. Выбор зависит от ряда факторов: назначение автомобиля, рынок эксплуатации, место установки (передние или задние тормоза) и распределение веса автомобиля. После чего изготавливаются образцы, которые подвергаются всесторонней оценке и лабораторным испытаниям на долговечность на динамометрических стендах и ходовым испытаниям на автомобилях. После внутреннего одобрения образца отделом разработок компания заказывает инструментальную оснастку для изготовления детали. После этого Delphi может подать заявку на получение сертификата R90 (стандарт качества, необходимый для европейских изделий) на готовые изделия.
Все детали для вторичного рынка проходят такие же строгие процессы разработки изделия, как и изделия для первичного рынка, включая верификацию производимого изделия (PPV). Должны подтвердиться рабочие характеристики производимого изделия, которые должны быть не хуже, чем у опытных образцов. А также соответствия (PPAP): подтверждение соответствия каждого изделия всем требованиям для опытных образцов.
Тормозные колодки Delphi проходят ряд испытаний в реальных условиях. В том числе: стандартное европейское испытание AK Master European, испытание Auto Motor und Sport (AMS), анализ шума на динамометре, испытание в горных условиях, испытание на высокой скорости на автомагистрали, испытания FMVSS и Ameca (для выполнения требований США).
Динамометр калибруется под характеристики соответствующего автомобиля. На основании веса автомобиля и радиуса качения шины автомобиля вычисляется инерция для моделирования действующих сил. Используются также гидравлические компоненты и диски соответствующей модели автомобиля. Скорость при испытании может быть выбрана в соответствии с возможностями автомобиля. Delphi применяет одинаково строгие критерии к разработке и проектированию всех своих тормозных колодок. Поэтому автомастерские, использующие изделия Delphi, могут быть уверены в их качестве и надежности. Продукция Delphi – это удовлетворение заказчиков и безопасность вождения.
Комментарии, как говорится, излишни.