Две свечи
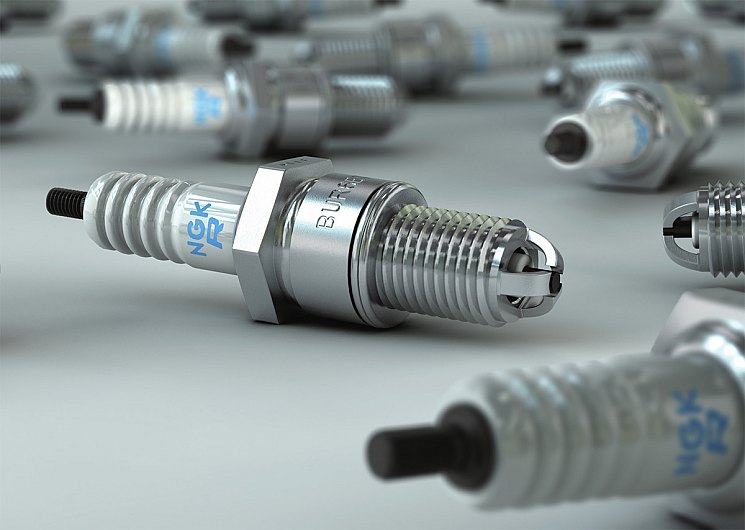
Свеча зажигания и свеча накаливания. Интересно, кому и по какой причине пришло в голову назвать эти моторные компоненты свечами? Со свечой их роднит, пожалуй, лишь способность выделять тепловую энергию. Видимо, это результат «трудностей перевода». Ведь основное значение английского оригинала – plug – отнюдь не свеча, а «пробка», «затычка», «заглушка» и т. п. Мы же решили восстановить его хотя бы в заглавии краткого обзора, посвященного свечам.
Итак...
Свеча накаливания
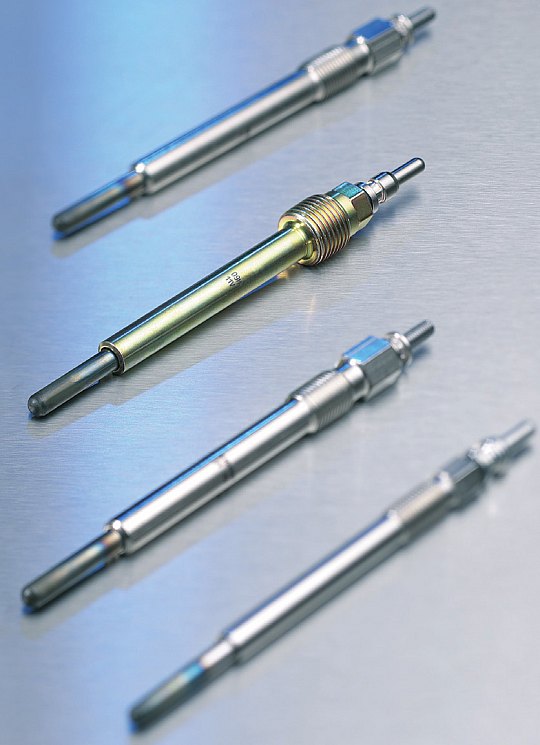
Если серьезно, свечи накаливания действительно не имеют практически ничего общего с обычными свечами. Да и со свечами зажигания их объединяет только одно – «рабочее место». Все остальное – назначение, физические процессы, конструкция, технологии изготовления – другое.
Известно, что свеча накаливания – принадлежность исключительно дизельного двигателя и служит для облегчения его холодного пуска, т. е. запуска двигателя, температура которого ниже рабочей. Необходимость помощи обусловлена тем, что из-за относительно низкой частоты вращения от стартера процесс сжатия воздуха в цилиндре растянут по времени, что приводит к большим потерям давления и температуры.
Если вдобавок к этому и стенки цилиндра, и всасываемый воздух холодные, ситуация усугубляется – воздух не нагревается до температуры самовоспламенения смеси, равной примерно 250 °C. В дизелях с разделенными камерами сгорания (форкамерных и вихрекамерных) такая опасность возникает уже при снижении температуры до +30 °C. Современные дизели с непосредственным впрыском отличаются лучшими пусковыми характеристиками – им помощь нужна лишь тогда, когда они охлаждаются до температуры ниже 0 °C. Но, так или иначе, содействие нужно любым дизелям, и его оказывает система помощи при холодном пуске.
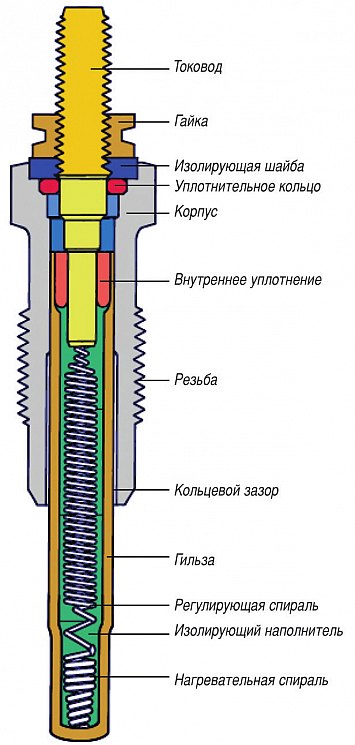
Не очень известно, что в отличие от стандартных свечей накаливания, работающих в двухфазном цикле (перед и во время пуска), функции современной свечи накаливания не ограничиваются предпусковым подогревом. Свеча продолжает отдавать тепловую энергию в течение некоторого времени после пуска. Третью фазу рабочего цикла свечи, которая в зависимости от температуры двигателя и воздуха может длиться до 6 мин., называют остаточным накалом, вторичным нагревом, послепусковым нагревом и т. п. Она нужна, чтобы непрогретый двигатель работал более устойчиво и приемисто, менее шумно и с меньшим уровнем выброса токсичных веществ. С ростом требований к комфорту и экологии эта функция свечи накаливания становится все более важной.
Производство свечи накаливания было бы не сложнее изготовления обычных бытовых ТЭНов, если бы не ряд специфических требований к этому изделию. Свеча должна продолжительное время сохранять работоспособность в суровых условиях камеры сгорания дизеля, характеризующихся высокой температурой, давлением, ударными волнами, вибрациями и коррозионно-активной средой. Минимальное (исчисляемое секундами) время разогрева стержня до рабочей температуры и строгие габаритные ограничения – также непростые условия, выполнение которых невозможно без применения уникальных технологичных процессов и материалов.
Такова конструкция стандартной штифтовой свечи накаливания с одной спиралью. В последнее время стандартом становятся свечи с двумя спиралями – регулирующей и нагревательной. Соединенные последовательно, они образуют общий резистивный элемент. Такие свечи получили название «саморегулирующиеся» и предназначены для трехфазного режима работы. Вторая спираль автоматически уменьшает ток, протекающий через нагревательный элемент, в третьей фазе работы свечи. Если этого не сделать, свеча перегреется и выйдет из строя – ведь после того как двигатель запустился, она начинает испытывать тепловое воздействие сгорающего топлива. На словах все просто: регулирующая спираль изготавливается из материала, сопротивление которого с ростом температуры многократно увеличивается. Обычно для этого используется никелевый сплав. Варьируя длину, диаметр проволоки и витков регулирующей и нагревательной спиралей, подбирают время разогрева и температуру, нужные для согласования свечи с данным типом двигателя.
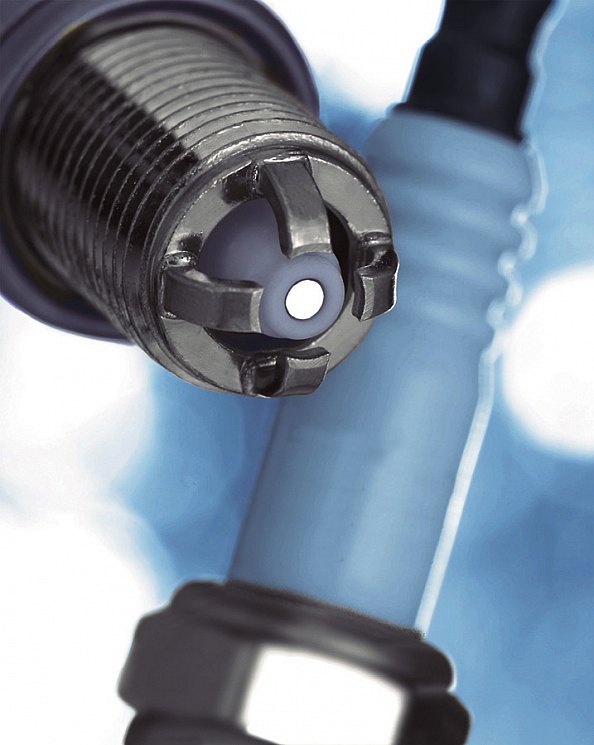
Полсотни лет тому назад для холодного запуска дизеля нужно было включить предпусковой подогрев, после чего можно было «закурить и оправиться»: процесс разогрева свечей накаливания занимал примерно полминуты. Современному дизелю с непосредственным впрыском, как упоминалось, помощь при пуске оказывается только при температурах ниже нуля. В зависимости от того, насколько «ниже нуля» охладился мотор и окружающая среда, свечи справляются с этой задачей за 2–5 с. Сокращение времени разогрева свечей – одна из основных проблем, которая была успешно решена.
Успех достигнут благодаря мерам, направленным на повышение теплопроводности и снижение тепловой инерции нагревательного стержня. Стержень со временем значительно уменьшился в диаметре (с 6 до 3 мм), в его конструкции применяются все более совершенные материалы и технологии. Не последнюю роль в ускорении нагрева свечей сыграли и «саморегулирующаяся технология», позволяющая безболезненно резко увеличить ток в предпусковой фазе, и современные системы управления запуском, точно дозирующие параметры питания свечи.
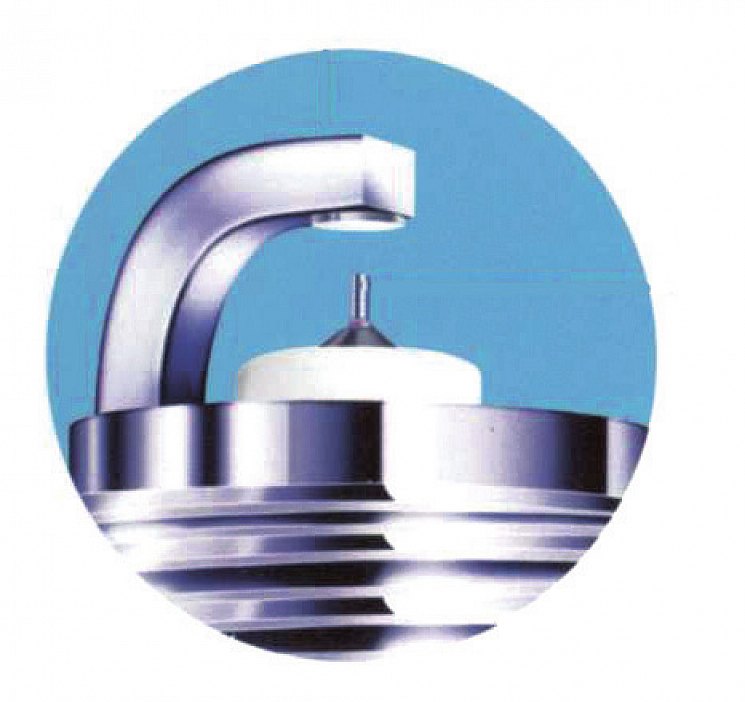
Заметно, что со временем внешний облик свечей менялся – подобно фотомоделям, они худели и удлинялись. Уменьшение диаметра корпуса, так же как и в случае свечей зажигания, вызвано сокращением свободного пространства в головке вследствие увеличения количества клапанов и размеров тарелок. Удлинение потребовалось для того, чтобы дотянуться стержнем накаливания до камеры сгорания, в то время как раньше было достаточно достать до вихревой камеры или форкамеры.
Совершенствование свечей накаливания продолжается. Одно из направлений их эволюции – применение нагревательных стержней из керамики. Керамические свечи превосходят свечи с металлической оболочкой по скорости разогрева (менее 2 с), времени и температуре остаточного накала (до 10 мин. при 1200 °C). При этом энергопотребление у них ниже (менее 40 Вт против 70–80 Вт), а ресурс выше (до 240 000 км против 60 000–100 000 км). Керамические стержни изготавливают из нитрида кремния, обладающего высокой теплопроводностью и теплостойкостью. Нагревательная спираль из материала с высокой температурой плавления «запекается» в керамику при изготовлении стержня. Производство керамических свечей уже освоено ведущими компаниями, они выпускаются в вариантах с одной или двумя спиралями, т. е. в обычном или саморегулирующемся исполнении.
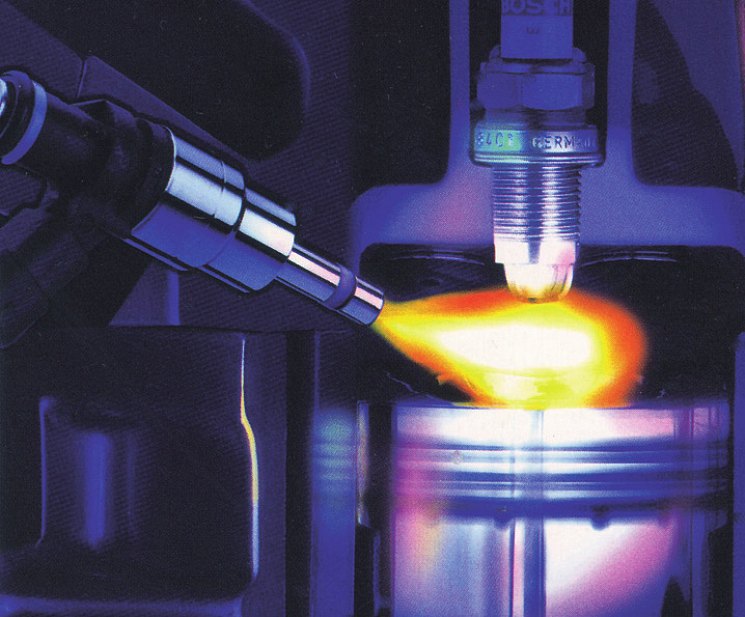
Другое перспективное направление – придание свечам накаливания диагностических функций, например измерения давления в камере сгорания. На основании точной информации об этом параметре в каждом цилиндре можно оптимизировать сгорание так, чтобы достигались предельно высокие значения максимального давления цикла. Помимо этого, появляется возможность компенсации разницы в задержке самовоспламенения по цилиндрам. Все эго позволяет добиться от двигателя большей мощности, эффективности и плавности работы. Например, в инновационные свечи накаливания Вегu PSG (Pressure Sensor Glow Plug) встроен пьезорезистивный сенсор.
Стержень накаливания не запрессован в корпус свечи, а установлен подвижно. Смещаясь под действием давления, стержень воздействует на мембрану сенсора, генерируемый сенсором электрический сигнал передается в систему управления двигателем.
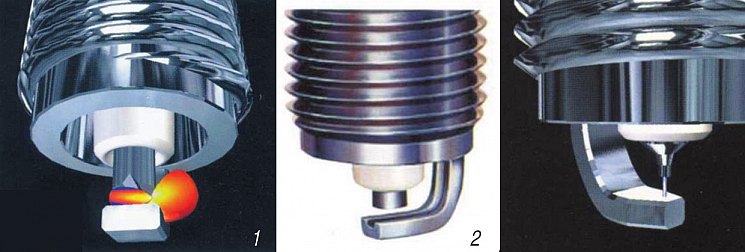
Современные системы помощи при холодном пуске на основе саморегулирующихся свечей накаливания, как правило, не содержат каких- либо электронных управляющих устройств. Постепенно они станут все чаще оснащаться электронными блоками управления, которые будут рассчитывать алгоритм электроснабжения свечей, необходимый для обеспечения конечных параметров пуска, задаваемых системой управления двигателем.
Состав «высшего дивизиона» производителей свечей накаливания не отличается от премьер-лиги по изготовлению искровых свечей: японские концерны Denso и NGK, немецкие Вегu и Bosch и входящий в корпорацию Federal- Mogul бельгийский Champion. Продукция этих брендов составляет примерно 40% объема российского рынка. Что касается их расстановки в европейском «табеле о рангах», многие эксперты, а вместе с ними и автопроизводители, отдают пальму первенства фирме Вегu, отмечая ее инновационное превосходство в области пусковых систем даже над известным «дизелеведом», концерном Bosch. Достойную конкуренцию им составляют японские производители, продукция которых все чаще используется европейскими автозаводами для первичной комплектации и теснит соперников на афтемаркете.
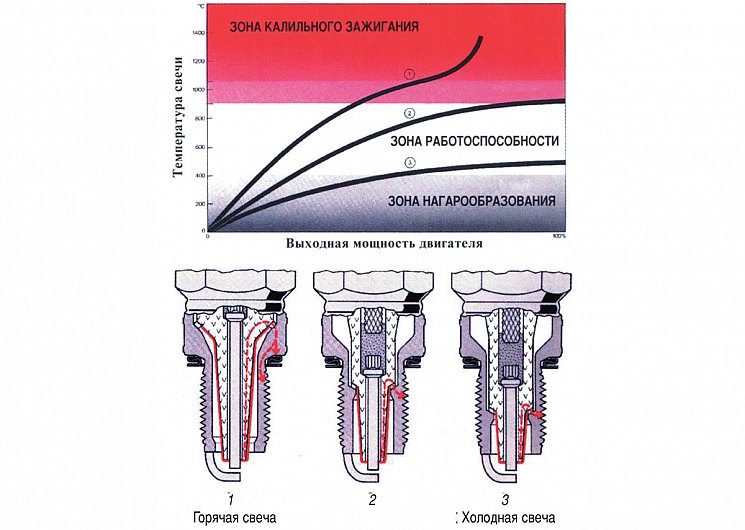
Bosch предлагает новую линейку двухспиральных свечей Duraterm Chromium. Регулирующая спираль выполнена из сплава, содержащего кобальт. Свечи Duraterm Chromium обладают всеми преимуществами саморегулирующихся свечей: разогреваются до рабочей температуры за 4 с, стабильно держат температуру в режиме остаточного нагрева, экономно потребляют электроэнергию и надежны.
Наряду со свечами накаливания, полностью идентичными оригинальным компонентам (поставляются в фирменной желтой упаковке), NGK предлагает новую линейку свечей D-Power. Она составлена из усовершенствованных аналогов ОЕ-изделий. Все свечи серии – и металлические, и керамические – саморегулирующиеся. Линейка разработана так, что минимальное количество наименований закрывает порядка 1400 моделей автомобилей, упрощая жизнь продавцам и покупателям. «Прочие» бренды остались вне поля зрения не по злому умыслу. Как упоминалось, будущее российского рынка свечей накаливания – за высокотехнологичными компонентами. Их производство по плечу лишь лидерам «свечестроения», доля которых на афтемаркете будет только увеличиваться.
Свеча зажигания
Производители свечей зажигания отмечают, что в среде автолюбителей, да и профессионалов авторемонта, распространено не совсем верное представление об их продукции. Попробуем хотя бы частично исправить эту ситуацию.
Свеча зажигания – ровесница ДВС с принудительным воспламенением топливовоздушной смеси и, пожалуй, один из самых привычных (и для автолюбителей, и для автопрофессионалов) компонентов двигателя. Как и с большинством привычных нам вещей, мы обращаемся со свечей запросто, «на ты». Меж тем, если разобраться, свеча заслуживает уважительного отношения. Это не только неотъемлемый элемент системы зажигания, но и весьма хитроумное устройство, вмещающее множество уникальных технологий.
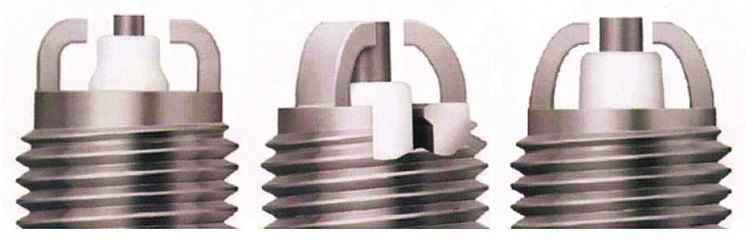
Свеча зажигания, без преувеличения, «экстремал» мира искровых моторов. Температура в камере сгорания в различные моменты рабочего цикла изменяется от 70 до 2000 и даже 2700 °C. Давление при сгорании топливовоздушной смеси достигает 50–60 бар, при этом усилие, стремящееся «выплюнуть» свечу из свечного отверстия, доходит до 300 кГ. Тепловое и механическое воздействия – циклические, они изменяются с частотой до 50 раз в секунду. С такой же периодичностью на свечу поступает высокое (до 40 000 В) напряжение.
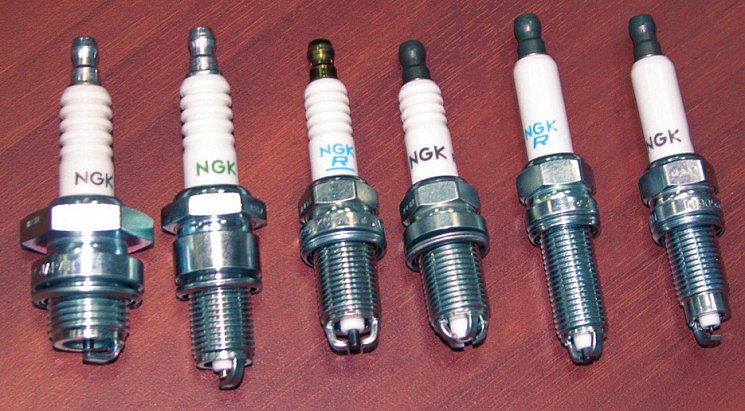
Раскаленные продукты сгорания оказывают сильное коррозионное воздействие на материалы электродов и изолятора. Вдобавок к этому электроды подвергаются искровой эрозии. Несмотря на такие «нечеловеческие» условия, свеча стабильно и в течение длительного времени выполняет свою основную функцию – транспортирует электрическую энергию внутрь камеры сгорания и преобразует ее в энергию искрового разряда, формирующего ядро пламени. Срок службы стандартной свечи в современном моторе превышает 20 тыс. км пробега, а свечей специальной конструкции – переваливает за 100 тыс. км!
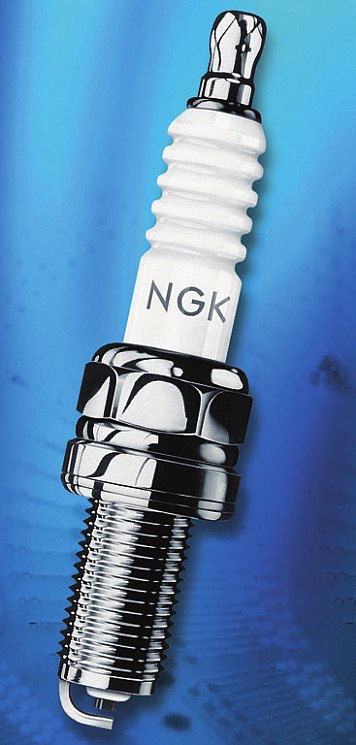
Если со знанием дела посмотреть на конструкцию свечи, можно увидеть, что в ней совмещено несовместимое: металлический корпус и керамический изолятор, биметаллический центральный электрод, керамический резистор и вновь металлический сердечник. Материалы, из которых изготовлены эти детали, в несколько раз отличаются по способности к температурному расширению и не поддаются неразъемному соединению традиционными способами. Следуя обычной логике, такая конструкция должна была бы тут же развалиться от циклического нагрева. Однако она работает и выдерживает упоминавшиеся немалые нагрузки!
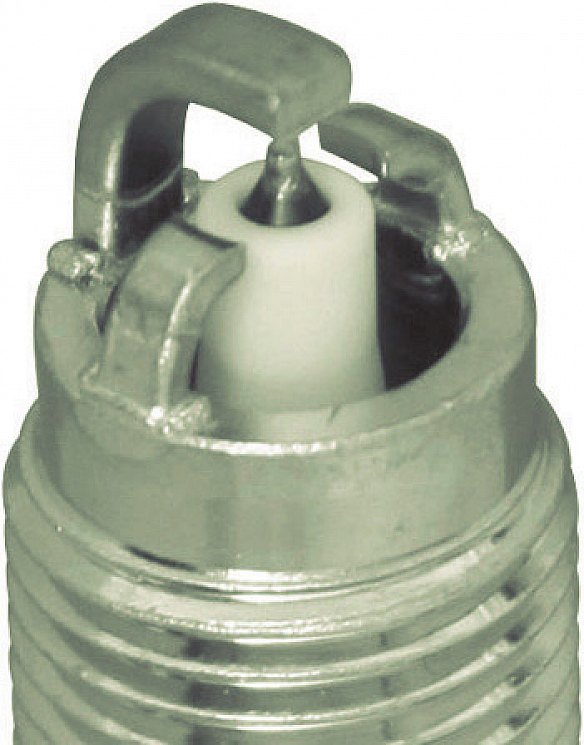
Более того, детали соединены так, что центральный токовод обладает высокой электропроводностью. Места контакта центрального электрода с изолятором и изолятора с корпусом герметичны и имеют низкое тепловое сопротивление. А чего стоит с высокой точностью изготовить ажурный алюмооксидный изолятор сложной формы, «обернуть» миниатюрный медный керн центрального (а в некоторых конструкциях и бокового) электрода в тонкую оболочку из никелевого сплава, лазером приварить к его торцу кусочек платиновой или иридиевой «иглы» диаметром в 0,5 мм?
Но самое потрясающее, что все эти технологические чудеса происходят в особо крупносерийном производстве – ведущие компании изготавливают свечи сотнями миллионов штук в год! К примеру, один из «свечных заводиков» NGK производит 1,2 млн свечей ежедневно! Начинаешь понимать, что сто с лишним лет эволюции «свечной» отрасли промышленности не прошли даром.
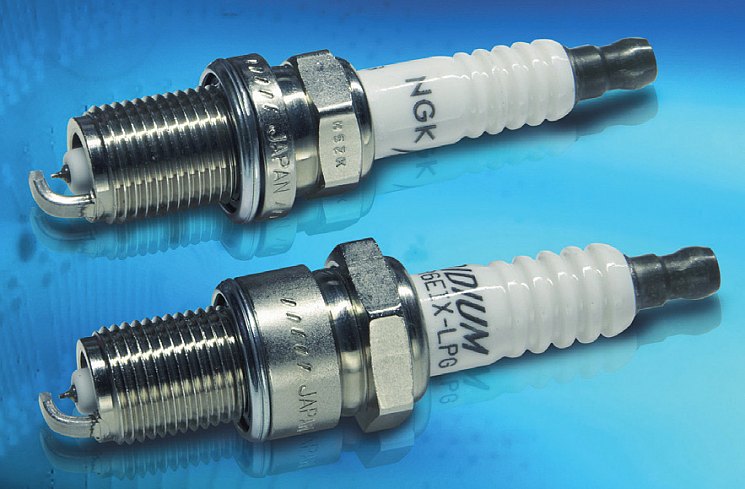
Тепловой режим свечи очень важен для исполнения ее основной, «зажигательной» функции. Он оптимален, если температура самой горячей ее части – кончика теплового конуса (юбки) изолятора, соседствующего с межэлектродным зазором, остается в пределах примерно от 450 до 800 °C. Нижнюю границу диапазона называют температурой самоочищения. Название говорит само за себя: начиная с этой температуры происходит активное выгорание с поверхности изолятора углеводородных отложений – изолятор очищается. При меньшей температуре нагар накапливается, образуется электропроводный слой, который шунтирует (закорачивает) искровой промежуток – искрообразования не происходит.
Если температура превышает верхний порог оптимального теплового диапазона, возрастает интенсивность износа электродов свечи. Более того, возникает опасность преждевременного воспламенения смеси (калильного зажигания) от раскаленного кончика изолятора, грозящая повреждением свечи и двигателя. Поэтому температура кончика изолятора не должна выходить из указанного поля допуска на любых режимах работы двигателя.
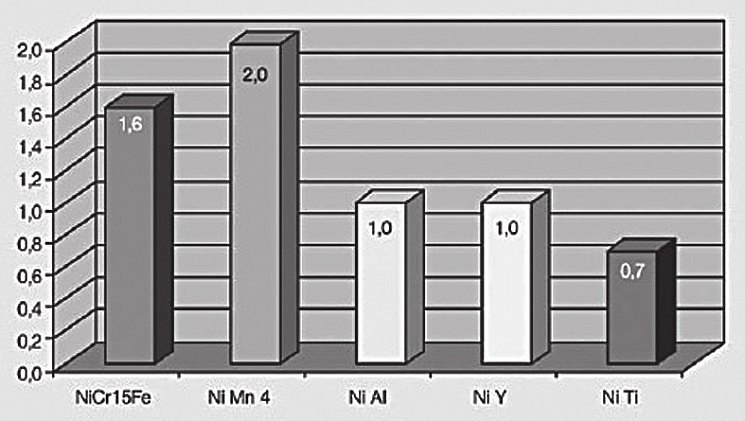
Способность свечи отводить тепло характеризуется небезызвестным калильным числом. Чем оно больше, тем выше теплопроводность свечи, тем ниже температура теплового конуса изолятора при равной температуре в камере сгорания – свеча более «холодная». И наоборот, чем меньше калильное число, тем «горячее» свеча. Помимо теплопроводности центрального электрода калильное число зависит от его длины, площади поверхности (высоты) юбки изолятора, теплопроводности материала изолятора, вылета юбки относительно металлического корпуса. Варьируя эти параметры, получают изделия с различными тепловыми характеристиками. Увеличение теплового диапазона свечей позволило существенно сократить их ассортимент – границы применимости свечи с определенным калильным числом расширились.
Когда разработчики автомобилей озаботились увеличением межсервисных интервалов и сокращением объемов технического обслуживания, перед производителями свечей зажигания была поставлена задача увеличения ресурса их продукции. Основное препятствие, ограничивающее срок эксплуатации свечей, – искровая эрозия электродов. Со временем она искажает первоначальную форму электродов и увеличивает межэлектродный зазор. Установлено, что с каждой пройденной тысячей километров расстояние между электродами из никелевых сплавов возрастает на величину от 3 до 10 мкм. Это постепенно приводит к повышению пробивного напряжения. Нагрузка на систему зажигания растет до тех пор, пока не достигнет предела – искрообразование становится нестабильным.
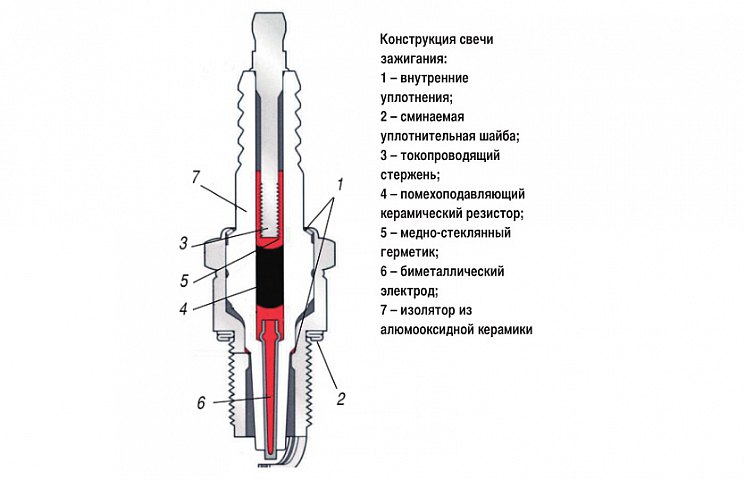
Кардинальным решением проблемы эрозии стало использование в электродах драгоценных металлов: золота, платины, иридия, родия, а также соединений иттрия. Бесспорное достоинство перечисленной «экзотики» – именно повышенная стойкость против эрозии, которая позволила увеличить ресурс свечи в несколько раз. Прочие преимущества, которые иногда упоминаются в некоторых рекламных проспектах (вроде предварительной ионизации искрового промежутка, каталитического воздействия и т. п.), туманны и не всегда согласуются с теорией искрового разряда.
Вначале «драгоценным» стал центральный электрод, поскольку он в наибольшей степени страдает от эрозии. Во всех системах зажигания (за исключением Э13) на него подается отрицательный потенциал. Поэтому при искровом разряде его поверхность «бомбардируется» высокоэнергетичными ионами, в то время как боковой электрод «обстреливают» легкие электроны.
Позже «для большей лучшести» эрозионно-стойкими начали делать оба электрода. Свечи типа «дабл экзотик» объективно нужны для применения в упоминавшемся выше исключении – 013-х системах зажигания, где каждая пара свечей обслуживается одной «двухискровой» катушкой. Во-первых, в них свечи «искрят» вдвое чаще, чем в других, так что повышенные меры по увеличению ресурса им очень кстати. Во-вторых, половина свечей питается высоким напряжением обратной полярности, поэтому противостоять ионам приходится и боковому электроду. Впрочем, такими свечами комплектуются некоторые современные моторы с иными системами зажигания. Для этого у их разработчиков есть другие веские мотивы, которые не стоит оспаривать.
Еще одним, более заметным глазу способом повышения ресурса свечей стало увеличение количества боковых электродов. В многоэлектродных свечах искровой разряд возникает между центральным и одним из боковых электродов. Образно говоря, искра сама выбирает межэлектродный промежуток с наилучшими для нее условиями. Так как корпусные электроды работают попеременно, у центрального электрода используется более развитая боковая поверхность, а самих межэлектродных зазоров несколько, негативное влияние эрозии многократно уменьшается. Эксплуатационная особенность многоэлектродных свечей состоит в невозможности регулировки величины зазора. Предельный вариант многоэлектродной свечи – так называемая свеча с блуждающей искрой. Роль бокового электрода выполняет бортик в форме кольца на торце резьбового корпуса. Межэлектродный зазор представляет собой кольцевую щель, в которой искра произвольным образом перемещается по кругу. Сделать свечу такой конструкции горячее проблематично: сплошной кольцевой электрод экранирует юбку изолятора от раскаленных продуктов сгорания. Не случайно она чаще применяется в спортивных моторах.
Дальнейшая борьба за увеличение ресурса свечей зажигания большого смысла не имеет: вечный «расходник» не нужен ни автомейкерам, ни производителям свечей, ни сервисменам. Сегодня эта задача снята с повестки дня.
Требования к стабильной работе в условиях повышенного нагарообразования и надежному воспламенению до предела обедненных, недостаточно гомогенизированных топливовоздушных смесей повышаются. Какие меры предпринимаются для их удовлетворения?
Повысить надежность и эффективность свечей удалось путем оптимизации конструкции электродов. Играя важнейшую роль в формировании искры, они же способны оказывать негативное влияние на воспламенение смеси. Негатив вызывается двумя эффектами: экранирующим и подавляющим действием электродов. Экранирующий эффект создает боковой электрод (или электроды), который, как ни крути, является препятствием для смеси, поступающей к искровому промежутку. Подавляющее воздействие оказывают оба. Находясь вплотную к зародившемуся ядру пламени, имеющие высокую теплопроводность электроды «сосут» из него тепло, которого на начальной стадии не так много. Электрическая мощность искрового импульса составляет несколько десятков ватт, а тепловая – и того меньше.
Обойтись вовсе без бокового электрода нельзя, так же как нельзя сделать его тоньше по соображениям прочности. Поэтому для минимизации экранирования применяют способы, вытесняющие искровой разряд от оси электродов на их периферию. Как сказано выше, в свечах NGK V-line на торце центрального электрода сделана насечка V-образного профиля. Поскольку при физических условиях, в которых работает свеча зажигания, разряд происходит по кратчайшему пути между электродами, удается исключить его привязку к центру электрода.
В конструкции современных свечей используется ряд технологий для повышения надежности зажигания в условиях повышенного нагарообразования. Часть из них направлена на то, чтобы с помощью самой искры очищать кончик теплового конуса изолятора. Для этого межэлектродному зазору придается такая конфигурация, что искровой путь проходит вблизи поверхности изолятора и искра выжигает отложения. Так работает, например, технология полуповерхностного разряда. В свечах с дополнительным воздушным зазором и с «перехватывающим» электродом основной искровой зазор дублируется дополнительным, который перехватывает искру в том случае, если она «стекает» по поверхности изолятора. Тем самым опасность пропуска зажигания уменьшается.
Если говорить об отдаленной перспективе, на смену привычным свечам зажигания, скорее всего, придут лазерные технологии. Оптическая «свеча», соединенная с источником лазерного излучения гибким световодом, будет направлять интенсивные лазерные импульсы в разные участки камеры сгорания, обеспечивая быстрое и максимально полное сгорание топливовоздушной смеси. По мнению исследователей, такими системами можно оснащать уже существующие бензиновые двигатели, что позволит сократить потребление топлива и улучшить экологию.