Грузовые барабанные
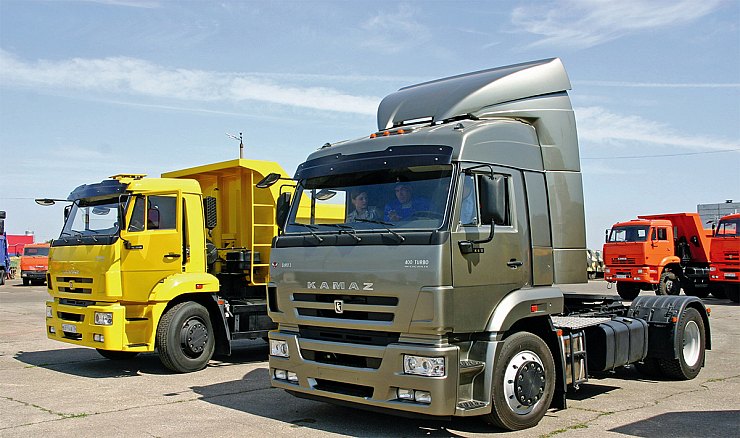
Они еще нас переживут
Эта статья о тормозах грузовых автомобилей. А точнее, о фрикционных накладках барабанных тормозов больших грузовиков и автобусов. Почему именно барабанных, ведь дисковый тормоз эффективнее? Верно. Но в грузовом автопарке барабанные тормоза распространены очень широко, и полная их замена на дисковые произойдет не скоро.
Судите сами: на серийный легковой автомобиль дисковый тормоз пришел в 60-х годах прошлого века. Сегодня на дворе 2012 год – и что же? Большинство легковых автомобилей на евразийском континенте до сих пор имеют комбинированные тормозные механизмы – спереди дисковые, сзади барабанные. За примерами далеко ходить не надо: это бюджетные «корейцы», «китайцы» и относительно недорогие «европейцы», «американцы» и «японцы». И разумеется, наши родные «ВАЗы».
Что же говорить о больших грузовиках, которые стали оснащаться дисковыми тормозами лишь в конце 1980-х? У них еще все впереди! Серийные «траки» с дисковыми тормозными механизмами на всех осях появились лишь немногим более 20 лет назад. Но это были грузовики ведущих мировых фирм. Что касается продукции заводов бывшего СССР, ее удел – барабаны, барабаны и еще раз барабаны. Это «КамАЗ», «МАЗ», «КрАЗ», «Урал», «ЛиАЗ», «ПАЗ» и другие марки.
Исключения – нижегородские «ГАЗель» и «Соболь» (спереди дисковые тормоза, сзади барабанные), «Валдай» (спереди и сзади дисковые), «ЗИЛовский» «Бычок» (спереди дисковые, сзади барабанные), жодинский «БелАЗ» (спереди и сзади дисковые), УАЗ (спереди дисковые, сзади барабанные).
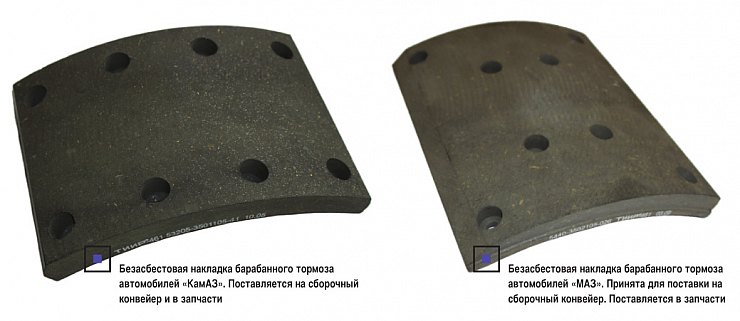
Но согласитесь, легкие коммерческие и средние грузовики да карьерные самосвалы – это несколько иные ниши. Мы же говорим о большегрузных бортовых машинах и самосвалах класса «КамАЗ», коих в России очень много. Прибавьте сюда импортную технику зарубежного производства с барабанными тормозами, выпущенную в прежние годы – а таковой на российских дорогах тоже немало.
Вот и получается, что фрикционные барабанные накладки – товар востребованный, как на конвейерах, так и на рынке запчастей. А значит, он просто обязан быть высококачественным и отвечать Правилам № 90 и № 13 ЕЭК ООН.
И конвейер, и «вторичка»
Как и во многих статьях фрикционного профиля, нашим консультантом выступит знакомое читателям ярославское предприятие ОАО «ТИИР». В ассортименте этого производителя широкая линейка колодок и накладок дисковых и барабанных тормозов для отечественных и зарубежных автомобилей.
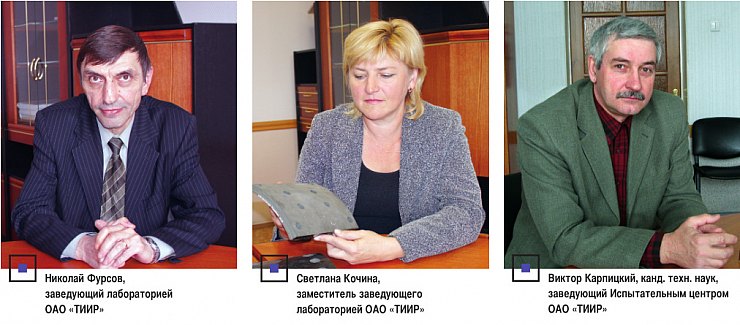
Здесь хорошо знают проблемы «большого барабана» – даром что поставляют фрикционные накладки на конвейеры КамАЗа, «Автозавода Урал», ЛиАЗа, ПАЗа, ЗИЛа. А еще – на троллейбусные заводы и предприятия по выпуску грузовых прицепов и полуприцепов. Тут же отметим, что многие барабанные накладки (например, для того же «МАЗа») приняты на конвейерную комплектацию. Ключевое слово здесь – «приняты». Так что поставки могут начаться в любой момент.
Что касается вторичного рынка, его охват весьма широк: в дополнение к «конвейерным» маркам ОАО «ТИИР» выпускает грузовые барабанные накладки для уже упомянутого «МАЗа», «КрАЗа», Ikarus, MAN, Mercedes, DAF, Iveco, Renault, Volvo и другой техники.
Любопытная подробность: на упомянутом ранее «ЗИЛовском» »Бычке» установлены дисковые тормоза от правительственного лимузина ЗИЛ 4105. Их в далекие советские годы тоже разработал «ТИИР» – тогда он назывался ВНИИАТИ.
Но вернемся к теме. Что же представляет собой современная накладка грузового барабанного тормоза?
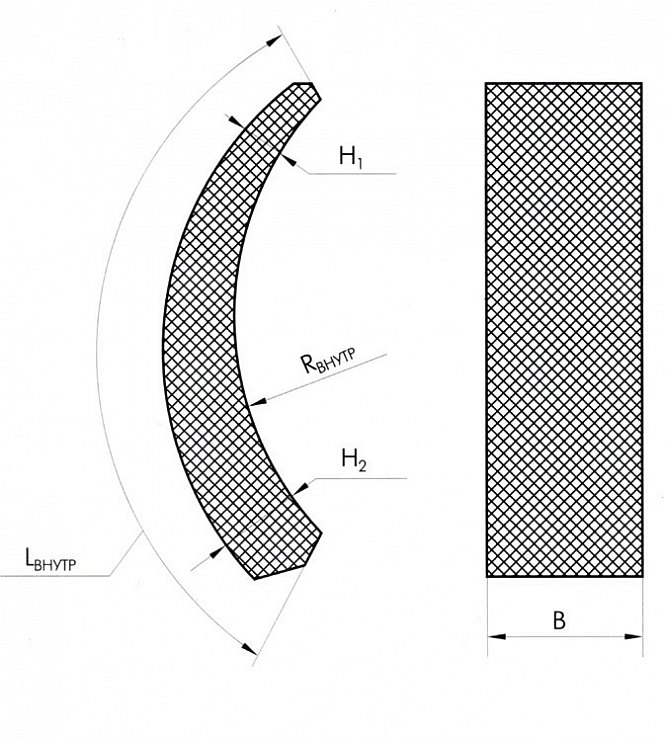
Конструкция, геометрия, рецептура
Фрикционную накладку проектируют исходя из требований автозавода, привязывая ее к тормозной системе конкретного автомобиля. Иными словами, законодатели здесь – конструкторы тормоза. Поэтому геометрия накладок барабанного тормоза для однотипных, в общем-то, автомобилей имеет общие черты и одновременно – существенные отличия. Начнем с общих характеристик.
Абсолютное большинство современных «грузовых» накладок имеют переменную толщину – у одного торца она больше, чем у другого. Их так и называют – разнотолщинные. Подобная форма не прихоть: на каркас колодки приклепывают две накладки, толстыми торцами друг к другу. Утолщения приходятся на наиболее нагруженную зону контртела (тормозного барабана), где эпюра давлений максимальна, благодаря чему накладка изнашивается равномерно.
На профессиональном жаргоне такие накладки называют «запятыми», что весьма удачно – в профиль они действительно похожи на всем известный знак препинания (см. рисунок). А еще современные барабанные накладки имеют индикаторы износа в виде небольшой боковой ступеньки – благодаря ей остаточный ресурс изделия легко отслеживается визуально.
Общим для накладок является и метод крепления к колодке. Если на коммерческих автомобилях типа «ГАЗели» накладки заднего тормоза могут как приклеиваться, так и приклепываться, то на тяжелых грузовиках их только приклепывают – никакого клея!
Значит, нужны отверстия под заклепки? Да, нужны. Причем выполненные соосно с отверстиями в каркасе, чтобы клепка не создавала остаточных напряжений, иначе механические и тепловые нагрузки приведут к трещинам и сколам.
Сверлить отверстия может как производитель накладок, так и заказчик, т.е. автозавод. А как правильно? Однозначного ответа нет – все зависит от условий договора на изготовление продукции.
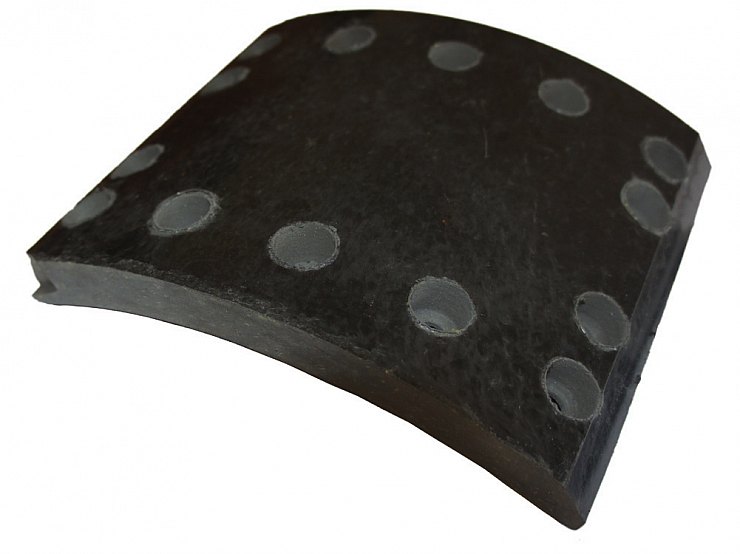
Возьмем, к примеру, КамАЗ. Когда-то автозавод самостоятельно сверлил отверстия в накладках. Потом «ТИИР» предложил поставлять накладки с уже готовыми отверстиями, а соединение накладки с каркасом КамАЗ поручил дочерним предприятиям. Так конвейер получил готовый продукт, колодку в сборе.
Большую роль в повышении качества колодки сыграло решение КамАЗа перейти со сварного каркаса на литой. Такая технология давала более точное изделие, накладка не деформировалась и работала стабильно. В результате все остались довольны – и потребители, и автозавод, и производители накладок. К слову, львиная доля поставок на КамАЗ сегодня осуществляется ОАО «ТИИР».
А вот «Автозавод Урал», что раскинулся в г. Миасс, пошел другим путем. Там предпочитают сверлить отверстия самостоятельно и собирать колодку на месте. И опять же все довольны результатом.
Оба примера показывают, что современный производитель барабанных накладок готов к любому варианту поставок и всегда найдет общий язык с заказчиком.
На автобусный завод ЛиАз, что в подмосковном Ликино, накладки поставляют в составе мостов. В основе автобусного тормоза прототип, созданный в свое время педантичными немцами. Все в нем слаженно и аккуратно, работать с такими узлами очень приятно. Под стать общей конструкции и фрикционная накладка – с рациональными скосами и оптимально распределенными отверстиями под заклепки. Кстати, в торцевой части их не два, а четыре, что обеспечивает высокую надежность соединения с каркасом.
И еще об автобусах: ОАО «ТИИР» является единственным российским предприятием, чья продукция принята для комплектации популярных автобусов «ПАЗ». Накладки также поставляются с отверстиями под заклепки.
Впрочем, геометрия, отверстия – это еще не всё. Бывают задачи и посложнее. Например, связанные с распределением тормозных моментов по осям. Вспомним: при торможении легкового автомобиля основную роль играют передние тормоза. На них приходится примерно 70% общего тормозного момента, в то время как на задние – всего лишь 30%. У грузовиков всё наоборот: первенство принадлежит тормозам задних осей.
Значит, задние «грузовые» накладки должны быть шире и «мощнее» передних? Совершенно верно, на «МАЗах» и на «иностранцах» так оно и есть. А вот на «КамАЗах», фактически «одноклассниках» минских грузовиков, передние и задние фрикционные накладки... одинаковые. Что поделаешь, такова конструкция тормозных узлов. Поэтому эффективность торможения и ресурс колодок приходится обеспечивать (внимание!) исключительно за счет рецептуры фрикционной смеси.
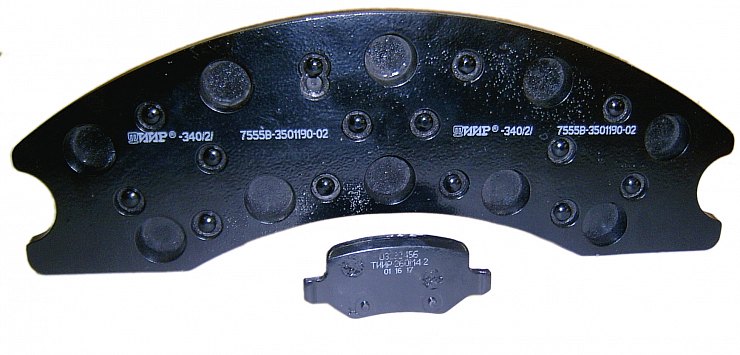
Спасибо научной школе ОАО «ТИИР» – эту задачу тоже решили успешно. Подтверждение тому – уже упоминавшиеся поставки на конвейерную комплектацию. Разумеется, на предприятии применяются только безасбестовые рецептуры – причем не только для конвейеров, но и для вторичного рынка. Мы уже писали ранее: территория предприятия свободна от асбеста с 2004 года. В цехах, на складах, в подсобках вы не найдете даже горсточки асбестового сырья – нет, значит нет.
В заключение этого раздела отметим, что безасбестовые фрикционные смеси содержат 15–20 ингредиентов, а умелая работа с ними позволяет в буквальном смысле программировать фрикционные свойства, износостойкость и другие важные характеристики накладок.
Об испытаниях
Внедрение невозможно без испытаний. Но, оказывается, и с этим все нормально: в Испытательном центре «ТИИР» имеется такое же оборудование, как у завода-заказчика. Речь о мощных инерционных стендах СН-6М, которыми пользуются НАМИ, ЗИЛ, «Автозавод Урал», МАЗ, КрАЗ.
На этих стендах проводят фрикционно-износные испытания тормозных механизмов транспортных средств с осевой нагрузкой до 10–15 т – как раз то, что требуется для тяжелых грузовиков. А единая методология испытаний автозавода-заказчика и производителя фрикционных изделий позволяет адекватно оценивать требования к накладкам и находить правильные решения.
Что же испытывают? Если кратко, испытания в натурных узлах позволяют оценить соответствие изделия обязательным требованиям безопасности АТС и определить:
• эффективность торможения;
• стабильность накладки в зависимости от скорости и температуры;
• восстанавливаемость изделия после экстремальных воздействий – например, длительного торможения.
Важно знать, что комплекс требований не ограничивается безопасностью тормозов. Он включает и такие показатели, как сжимаемость накладок. А эта характеристика позволяет оценить множество показателей работы тормозной системы. Среди них «жесткость» педали, скорость срабатывания, расход воздуха в пневмоприводе, а также шум и вибрация при торможении.
Кроме того, используется еще ряд оборудования для оценки продукции. Изучаются функционально-износные свойства на машинах трения, образцы проверяются на срез, исследуется твердость материала накладок, намокаемость в разных средах, прочность на изгиб и другие свойства. Таким образом, на предприятии действует система всесторонних испытаний, важных как для разработки, так и для производства изделий.
Напоследок я поинтересовался: а может ли «ТИИР» делать дисковые колодки для больших грузовиков? Не только может, отвечают, но и делает. Для «БелАЗа», например. Как только у наших грузовиков появятся дисковые тормоза и последуют заказы от автозаводов, сразу же расширим ассортимент. Никаких неразрешимых задач тут нет. Одно слово – школа.