Тормозные этюды в стиле «диско»
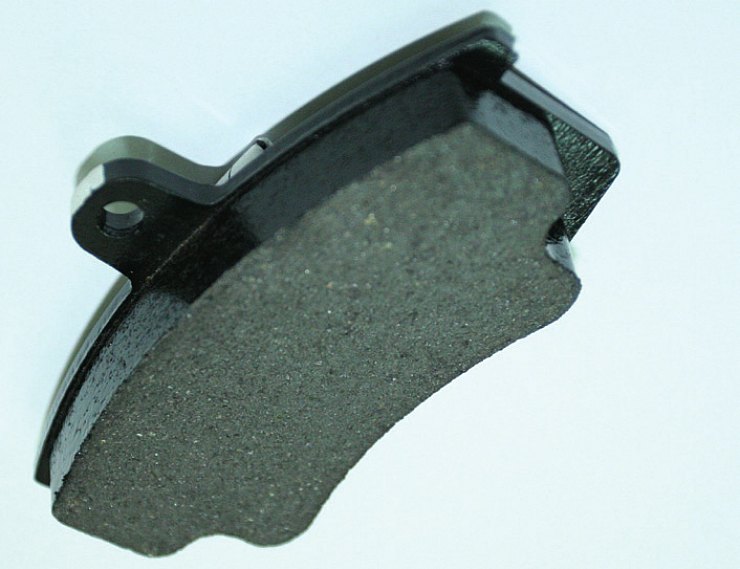
Как следует из названия, эта статья посвящается дисковым тормозам. А точнее – колодкам дискового тормоза, «расходникам». И уж если быть совсем точными – колодкам дискового тормоза для легковых автомобилей. Тех, что на официальном языке называются «автотранспортные средства (АТС) категории М1».
А вот была история!..
Как гласит фундаментальная БСЭ и косящая под энциклопедию Вики, слово «тормоз» происходит от греч. tоrmos – отверстие для вставки гвоздя, задерживающего вращение колеса. Так и представляешь себе каких-нибудь древних завоевателей, расположившихся у костра. Только расслабились – а тут начальник: «Так, ребята... А вы боевые колесницы на tоrmos поставили? А ну-ка!..»
Сколько народу передавили рукотворные повозки из-за того, что не могли вовремя останавливаться, никто не считал. Человечество спохватилось, лишь скрестив паровоз с каретой – т.е. создав паровой автомобиль. Так, в XIX веке в Англии приняли закон, разрешающий безрельсовым паровым экипажам двигаться со скоростью не более... 4 миль в час. По-нашему это 6,5 км/ч – прямо скажем, не густо. Более того, в населенных пунктах эта скорость уменьшалась вдвое, а перед паровиком тащился кочегар с флажком, отгоняя пейзан от огнедышащего чудища. При этом владельцы паровых автомобилей платили неподъемные налоги «за порчу дорог».
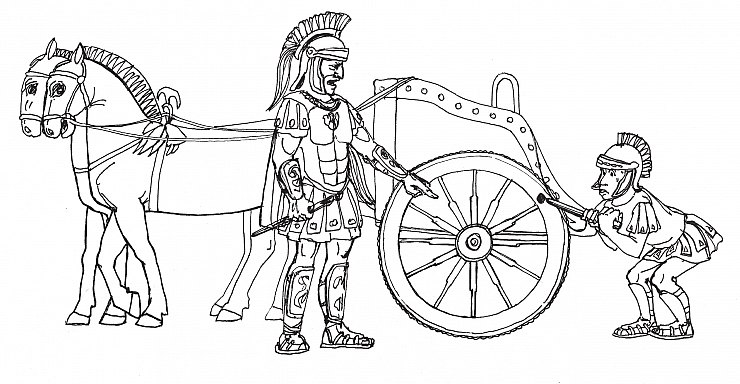
Ищи, кому выгодно, говорили древние! А чего искать-то? И так ясно, что указанные законы лоббировались владельцами конного транспорта. А это была сила, да еще какая! Пассажирские и грузовые перевозки, почта – разве можно было отдать столь доходный бизнес!
И только автомобиль с двигателем внутреннего сгорания одержал безусловную победу над лошадью. Ездил он быстро, ротозеев никто не разгонял, поэтому число жертв прогресса стало расти в геометрической прогрессии.
Не давить, а тормозить
Известное Женевское соглашение, подписанное 20 марта 1958 года, без преувеличения можно назвать судьбоносным – с его принятием конструкция автомобиля подчинилась жестким требованиям безопасности. За минувшие десятилетия Соглашение дополнилось многими Правилами и поправками к ним. Их разработкой занимается ЕЭК ООН – Европейская Экономическая Комиссия Организации Объединенных Наций. Так, Правила № 13 (13Н) ЕЭК ООН устанавливают требования к тормозным системам автомобилей, сходящих с конвейера, а Правила № 90 – к сменным тормозным накладкам, поставляемым в запчасти.
С 1 июля 2000 года указанные Правила ЕЭК ООН были приняты в России в качестве Государственного стандарта. А позже вошли в состав Технического регламента «О безопасности колесных транспортных средств», введенного действие в сентябре 2010 г.
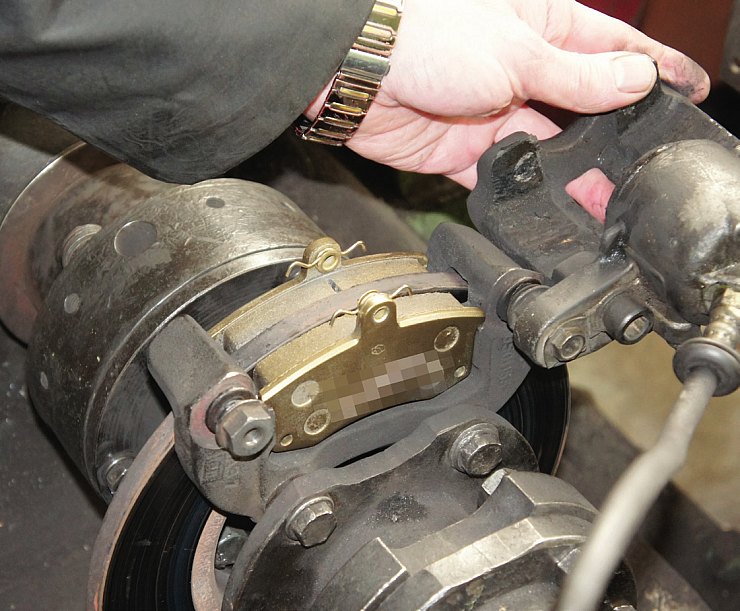
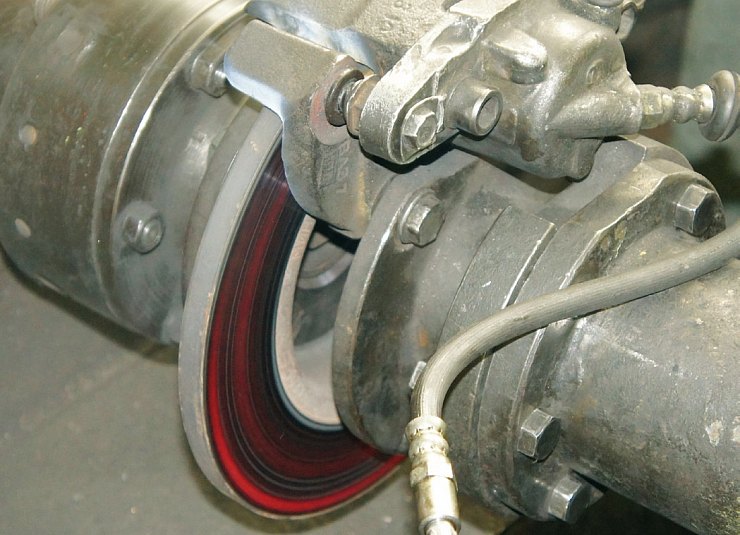
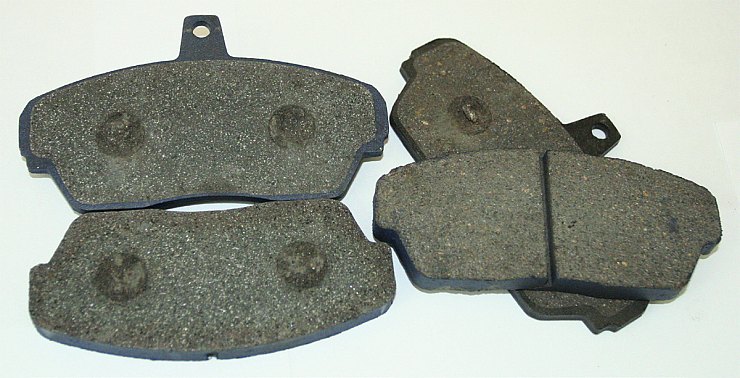
Простая сложная система
Формально автомобиль имеет несколько тормозных систем: рабочую, аварийную и стояночную. Их функции ясны из названий. На практике говорят «тормозная система», подразумевая всё в комплексе.
Эта «простая сложная система» состоит из органа управления, привода и тормозного механизма. Можно сказать по-простому: «Водитель давит на педаль», а можно заявить с умным видом: «Водитель воздействует на орган управления». И то и другое будет верным.
Так или иначе, мускульная энергия упомянутого водителя через усилитель и гидравлический привод передается к тормозным механизмам. Роль тормозного механизма, где, собственно, и создается препятствующая движению сила, выполняет фрикционный узел, главные детали которого – тормозные колодки и контртело (диск или барабан). А теперь несколько подробностей.
Стояночная
Известны два типа стояночной тормозной системы: с приводом на колеса и на трансмиссию (центральный тормоз). Орган управления здесь – рычаг, а привод – тросик. Преимуществами центрального тормоза являются: простота привода; увеличение подводимого к колесам тормозного момента за счет передаточного числа главной передачи; автоматическое уравнивание тормозных моментов между колесами благодаря дифференциалу.
Однако «не все коту масленица». При вынужденном торможении «ручником» с приводом на трансмиссию ее детали получают ощутимые ударные нагрузки. Кроме того, такое торможение приводит к «юзу».
Указанные недостатки полностью исключаются, если стояночная тормозная система имеет привод на колеса. Такое решение применяется практически на всех современных автомобилях.
Рабочая и аварийная
Наличие аварийной тормозной системы обусловлено повышением требований к надежности торможения. Сегодня она является неотъемлемой частью рабочей тормозной системы. Чтобы понять «ху из кто», надо знать «геометрию» гидравлических контуров в данном автомобиле.
Когда-то гидравлический привод тормозов был одноконтурным. Такую конструкцию имела, в частности, главная героиня фильма «Берегись автомобиля» красавица «Волга» ГАЗ-21. Недостатки одноконтурного варианта были очевидны – разгерметизация системы и утечка тормозной жидкости практически лишали автомобиль рабочей тормозной системы. Приходилось уповать только на «ручник».
Позже для повышения надежности систему сделали двухконтурной, а каждый контур оснастили независимым приводом. Таким образом, в случае разгерметизации одного из контуров второй продолжает работать, становясь аварийным. Он-то и обеспечивает остановку нашего автомобиля.
Контурные карты
Какие же бывают схемы разделения контуров? А вот какие.
• «2 плюс 2» параллельно. В этом случае один контур объединяет тормоза передней оси, а второй – задней. Многие специалисты считают ее неудачной, и вот почему. При разгерметизации переднего контура можно врезаться в «корму» впереди стоящего автомобиля из-за недостаточной эффективности задних тормозов – кстати, у большинства автомобилей с такой схемой разделения контуров они барабанные.
• «2 плюс 2» диагонально. В этом случае один контур охватывает «передний левый» и «задний правый» тормозные механизмы, а второй – соответственно «передний правый» и «задний левый». Недостатки есть и тут: экстренное торможение при отказе одного из «диагональных» контуров грозит вызвать занос. А из-за разницы (примерно в 2 раза) в тормозных моментах переднего дискового и заднего барабанного тормозов автомобиль может даже вылететь на встречную полосу. Здесь многое зависит от мастерства водителя. Словом, на тормоза надейся, а сам не плошай.
• «4 плюс 2» параллельно. В такой схеме первый контур объединяет тормозные механизмы всех четырех колес, а второй – механизмы только передних колес. Последние, естественно, оборудуются двумя колесными цилиндрами каждый. Схема «4 плюс 2» является более надежным решением, чем два предыдущих варианта.
• «3 плюс 3» и «4 плюс 4», оба параллельно. В схеме «3 плюс 3» каждый из контуров охватывает два передних и по одному заднему тормозному механизму. А вариант «4 плюс 4» имеет два независимых контура с приводом на все колеса. Эти решения самые надежные и дорогие.
«А дубы-колдуны...»
В процессе торможения важна возможность регулировки тормозных сил. Она осуществляется водителем через тормозную педаль, а также автоматически.
Все знают, что при торможении автомобиль «клюет», увеличивая нагрузку на передних колесах и соответственно уменьшая ее на задних. Поскольку тормозная сила не должна превышать силу сцепления колеса с дорогой, тормозные силы на передних колесах во время торможения должны возрастать, а на задних – падать. Тем самым исключается возможность блокировки колес – «юза».
Такое перераспределение тормозных сил между осями выполняет регулятор давления, метко прозванный в народе «колдуном». В зависимости от нагрузки на заднюю ось механизм «колдуна» открывает или закрывает доступ тормозной жидкости в цилиндры тормозных механизмов задних колес. Тем самым обеспечивается максимальное использование силы сцепления колеса с дорогой и исключается опережающая блокировка колес задней оси.
Числом поболе, ценою подешевле
Вот и добрались мы до тормозных механизмов. На современных АТС используются как барабанные, так и дисковые узлы.
Возможны следующие сочетания типов:
• дисковые на передней оси и дисковые на задней оси (Д-Д);
• дисковые на передней оси и барабанные на задней оси (Д-Б);
• барабанные на передней оси и барабанные на задней оси (Б-Б).
Сегодня сочетание Б-Б встречается крайне редко, доля Д-Б сокращается, а Д-Д – возрастает. Это неудивительно, поскольку еще в 60-х годах прошлого века стало очевидным, что барабанные тормоза не удовлетворяют возросшим требованиям к безопасности.
Поэтому сначала в США, а затем и в Европе начали активно внедрять дисковые тормоза, как более эффективные и стабильные в работе. В России их впервые массово применили в передних тормозных механизмах автомобилей «Жигули».
И все же самой распространенной схемой на евроазиатском континенте остается схема Д-Б: спереди дисковые тормоза, сзади – барабанные. Причина – недорогая и популярная продукция корейского, китайского и, конечно же, российского автопрома.
Отгадайте, какой отечественный автозавод играет в этой статистике первую скрипку, ставя задние «барабаны» даже на новейшие свои модели? Надо же, отгадали...
Технология дисковой безопасности
Упрощенно, колодка дискового тормоза состоит из каркаса и фрикционной накладки. Основные этапы ее создания следующие:
• приготовление массы (фрикционной смеси);
• штамповка (вырубка) из стального листа каркаса будущего изделия с последующей дробеструйной обработкой – эта операция упрочняет каркас и улучшает адгезию с фрикционной накладкой;
• спекание фрикционной массы с каркасом в прессформе, т.е. формирование собственно колодки.
Вот мы говорим – фрикционная смесь. Вроде все просто... А тем временем современная рецептура накладок дисковых тормозов имеет 15 и более ингредиентов, каждый из которых выполняет различные функции. Так, разработчики колодок подбирают:
• полимерные связующие, способные создать термостойкую матрицу с высокими прочностными свойствами (каучук, смолы, каучуко-смоляные, латексно-смоляные связующие);
• наполнители, обеспечивающие требуемый коэффициент трения и износостойкость;
• армирующие компоненты, упрочняющие полимерную матрицу.
Иногда при создании изделия применяют не менее двух-трех связующих и от двух до четырех армирующих наполнителей. Этот своеобразный каркас изделия выполняется из различных комбинаций стального, полиарамидного, минерального, стеклянного или углеродного волокна. Только при таком подходе можно получить изделия, надежно работающие в широком диапазоне температур, скоростей и давлений.
А теперь – комфорт
Производитель современных колодок освоил методы борьбы с «писком» колодок, в частности – противошумные мастики и пластины. Изделия комплектуются сигнализаторами износа. Все это стало обыденным делом. И даже святая святых – безопасность (слагаемые которой – эффективность и стабильность тормозных свойств) тоже пройденный этап, рядовая задача. Смешно, если бы современные колодки тормозили неэффективно, не так ли? Да еще скрипели при этом...
Да, это вам не девяностые. Позывные современного рынка звучат капризно: «Комфорт, комфорт, комфорт...». Слышащим их надо держать курс не на ободранный 15-летний «секонд-хенд», а на сверкающие иномарки.
Владельцы таких авто – люди избалованные. Они привыкли к плавному, как бы незаметному торможению, даже если машина разогналась до 140 км/ч и выше, торможению без рывков, вибраций, визга и прочих сюрпризов. Вот это мы и называем комфортом.
Она податлива?
Одно из важнейших направлений в работе над фрикционными накладками дискового тормоза – это исследования и регламентирование сжимаемости тормозных накладок. От того, насколько податлива накладка, зависит пауза от момента нажатия на педаль до возникновения необходимого тормозного усилия. Мягкая накладка может недопустимо затянуть эту паузу, слишком жесткая – вызовет нежелательные писки и скрипы при торможении. Нужен оптимум.
Но это еще не все. Практика передовых предприятий показывает, что определение сжимаемости на разных стадиях изготовления накладки позволяет отследить, во-первых, стабильность каждого звена технологической цепочки, во-вторых, правильность техпроцесса в целом.
Управление сжимаемостью, ее «программирование» сокращают сроки и стоимость разработки новых видов продукции. А в итоге повышается конкурентоспособность колодок. Ведь тормозить не только безопасно, но и комфортно сегодня желают многие, о чем только что говорилось.
Держать удар и никакой приработки
Еще один интересный факт. У тормозной колодки есть период приработки. Можно ли его минимизировать? Да, можно. Под воздействием высоких температур в зоне трения образуется рабочий слой фрикционного материала и происходит его дополнительная термостабилизация. Для получения такого слоя на поверхности накладки ведущие зарубежные и российские компании применяют операцию «термоудара» – высокотемпературной обработки рабочей поверхности на специальном оборудовании.
После термоудара колодка получает высокие фрикционные характеристики в начальный период эксплуатации. Это сводит к минимуму период приработки и позволяет эксплуатировать колодки в обычном режиме практически сразу после установки на автомобиль. Теперь найти различия между оригинальными колодками и продукцией, поставляемой в запчасти, вообще очень трудно. Привычная «обкатка» современным изделиям не требуется.
Это вам не ЕГЭ
Ни один автозавод не примет тормозную колодку на комплектацию без точного знания ее поведения под воздействием рядовых и экстремальных нагрузок. А знание это добывается комплексом длительных испытаний:
• образцов фрикционного материала, из которого изготавливается накладка;
• собственно колодок в натурных тормозных механизмах на специальных стендах;
• всей тормозной системы в целом на автомобиле.
Для каждого вида испытаний установлены нормативы в виде графиков и таблиц. Эти показатели зафиксированы в «Нормативно-технической документации на изделие». Так гарантируется безопасность транспортного средства.
Приведем пример одной из методик, по которой испытывают колодки дискового тормоза. Она, может, и не нова. Зато весьма интересна и наглядна, поскольку напрямую связана с реалиями эксплуатации.
Итак, перед нами заказчик тормозных колодок – автомобильный завод. После доводки, связанной с проведением большого количества экспериментальных работ и испытаний (как стендовых, так и дорожных), автомобиль представляют в специальную техническую службу, аккредитованную ЕЭК ООН. Там, на полигоне, автомобиль получает (или не получает) подтверждение типа транспортного средства в отношении торможения на основании Правил № 13.
Естественно, в доводке тормозных колодок принимает активное участие и поставщик этих изделий. Во главу угла здесь ставится оценка эффективности торможения, т.е. замедления. Естественно, существуют формулы и методики для пересчета эффективности торможения в коэффициент трения между колодкой и контртелом, поскольку эти величины функционально связаны.
А конкретно?
А конкретно, определяются следующие характеристики:
• зависимость коэффициента трения от давления (усилия на педали) при торможении со скорости 100 км/ч и температуре 100° C;
• зависимость коэффициента трения от скорости при давлении 50 кг/см2 и температуре 100° C;
• зависимость коэффициента трения от температуры при скорости 100 км/ч и давлении 50 кг/см2.
В испытания включен так называемый «режим Фейд» (Fade), предусматривающий два цикла по 25 торможений, по 45 секунд каждое. В процессе замеряется изменение коэффициента трения при давлении 50 кг/см2 в диапазоне снижения скорости от 100 до 50 км/ч. По сути, это имитация спуска по горной дороге с частыми торможениями. Потом режим Fade проводят еще раз. На этих повторных испытаниях проверяют восстанавливаемость колодки.
А теперь самое главное: эталонные кривые автозавод задает в виде областей, или зон, ограниченных верхним и нижним пределами. Вот в эти-то зоны и должна вписаться кривая, полученная в результате испытаний.
Итак, новый автомобиль обрел «правильные» тормозные колодки, качество которых подтверждено документально. А как быть с запчастями – ведь «родные» конвейерные колодки рано или поздно придется менять? Здесь полезно знать следующее.
При разработке колодок для рынка запчастей за основу берутся оригинальные детали, прошедшие испытания по Правилам № 13. Согласно документам ЕЭК ООН, сменные колодки по своим свойствам должны отличаться от конвейерных не более чем на ±15%.
Выход за границы зоны недопустим: он грозит нарушением соотношения тормозных моментов по осям автомобиля, – а тут и до беды недалеко. Вот почему так важны испытания и сертификация запчастей: она гарантирует попадание фрикционных характеристик тормозных колодок в нужный диапазон.
Как попасть в зону?
При разработке тормозных колодок для конкретной модели автомобиля специалисты поступают следующим образом. В первую очередь проводят комплекс физико-механических и фрикционно-износных испытаний оригинальных изделий, в том числе и на стендах.
Потом из имеющегося «портфолио» различных композиционных материалов (разработанных для дисковых колодок автомобилей с разными техническими и эксплуатационными характеристиками) выбирают материал, близкий к оригинальным изделиям. При необходимости на его основе проводят корректировки, а также полный цикл испытаний, в том числе на выполнение требований тех самых ±15%. Уложившись в разброс ±15%, производитель заявляет: вот тормозная колодка для такого-то иностранного автомобиля, полностью отвечающая Правилам ЕЭК ООН.
Ведущие отечественные производители фрикционных изделий быстро освоили дисковые колодки для популярных зарубежных моделей. Скоростные характеристики иномарок, конечно, отличались от динамики наших автомобилей. Поэтому для зарубежных машин создали более термостойкие фрикционные материалы – помимо надежности торможения они обеспечили и долговечность тормозных узлов, в частности тормозных дисков.
Колодкина физика
Большинство современных тормозных накладок имеет коэффициент трения 0,35–0,45. Почему так? Чем плохи значения 0,28 или, скажем, 0,55?
С первой цифрой все понятно: заниженные фрикционные свойства приводят к увеличению времени торможения и тормозного пути, что отрицательно сказывается на безопасности.
А хороши ли высокие фрикционные свойства? На первый взгляд – да. Но только на первый. На деле же увеличение коэффициента трения сужает диапазон воздействий на педаль от начала торможения до блокировки колес. И начинаются неприятности.
Судите сами: блокировка приводит к скольжению или юзу. Это недопустимо как минимум по двум причинам. Во-первых, ухудшаются устойчивость и управляемость автомобиля. Ведь сцепление колес с дорогой становится одинаковым во всех направлениях – что в курсовом, что в боковом. Во-вторых, увеличивается тормозной путь, поскольку сцепление с дорогой при скольжении колес значительно меньше, чем при качении.
Поэтому при высоком коэффициенте трения накладок требуется осторожность в «топтании педали», определенные навыки вождения и быстрая реакция.
Особо опасны дороги, где чередуются участки с хорошим и плохим сцеплением колеса. Например, асфальт, гололед, асфальт, снег, снова гололед, и это тянется на много километров. Или так: слева асфальт, а справа, ближе к обочине, жидкая грязь. В подобных ситуациях на машинах, не оснащенными тормозной электроникой, торможение может привести к потере управляемости и непредсказуемым последствиям. Такие случаи особенно опасны в условиях интенсивного движения с высокой скоростью.
Как уже говорилось, в большинстве случаев на передней и задней осях автомобиля устанавливаются разные тормозные механизмы. Тормозные накладки в этих схемах различны – и по технологии изготовления, и по набору компонентов фрикционной композиции. Однако они должны правильно взаимодействовать, т.е. иметь согласованные фрикционные характеристики.
Напомним, что опережающая блокировка колес передней оси нарушает управляемость автомобиля, а опережающая блокировка колес задней оси приводит к потере устойчивости, провоцируя занос и опрокидывание. Поэтому эффективность торможения каждой из осей должна находиться строго в своих рамках – и это тоже относится к азбуке безопасности.
Ну вот, с чего начали, к тому и пришли. Это нормально. Ведь речь идет о человеческой жизни.
Слово испытателям
О сертификационных испытаниях колодок дискового тормоза рассказывают научные сотрудники ФГУП «НАМИ» Сергей Батуров (на фото справа) и Николай Вишняков.
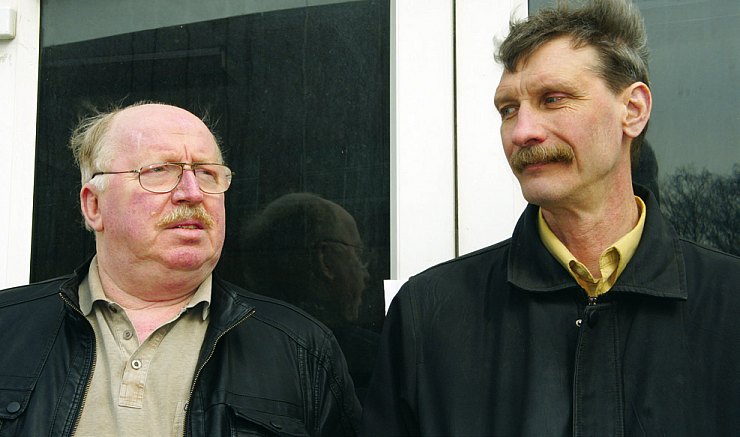
Начнем с того, что наша лаборатория аккредитована «Ростехрегулированием», т.е. официально уполномочена для проведения сертификационных испытаний.
Процедуры испытаний описаны в Правилах ЕЭК ООН № 90 и № 13, Приложение 15. В документах сказано, что эффективность колодок, идущих в запчасти, может отличаться от эффективности оригинальных колодок не более чем на 15%. Иными словами, назначается «коридор» с границами ±15%, и если показатели эффективности выходят за эти пределы, то колодка испытания не проходит.
Что подразумевается под эффективностью? Для стендовых испытаний это коэффициент трения при взаимодействии фрикционной накладки с контртелом, т.е. тормозным диском. Главное требование – он должен быть стабильным и не выходить за пределы упомянутого коридора. Тут же отметим, что коэффициент трения может быть пересчитан в момент трения, в величину тормозного пути автомобиля.
Еще один вид испытаний – это определение прочности соединения накладки с металлическим каркасом. Проводится на специальном прессе. Порядок проведения испытаний регламентирован ГОСТ Р 6312, а норма такова: давление отрыва накладки от каркаса должно быть не менее 2,5 МПа.
После испытаний протокол передается в Орган по сертификации, где колодкам выдается «путевка в жизнь» – сертификат.
Важно знать, что производитель колодок предоставляет пять образцов, четыре из которых отправляются собственно на испытания, а один хранится в лаборатории в течение срока действия сертификата. Это необходимо для разрешения споров, в том числе и судебных, если вдруг сертифицированная колодка станет причиной ДТП. И тогда «виновницу» можно сравнить с контрольным образцом и определить – а та ли это колодка, которая испытывалась на предмет безопасности?
Слово производителю
Тормозная колодка – простота и ответственность
Тормозная колодка дискового тормоза – на вид не очень сложная деталь автомобиля, гораздо проще многих других деталей, которые предназначены для разгона и движения автомобиля. Но только эта простенькая тормозная колодка под действием давления прижимается к чугунному тормозному диску и останавливает автомобиль, превращая всю кинетическую энергию движущейся на солидной скорости машины (весом в 1,5–3 т) в тепловую энергию торможения. А условия работы этой детали сверхтяжелые: температура обычного торможения в зоне контакта может составлять 300–350° С, а при аварийном торможении достигать 700–900° С. И эта простенькая деталь должна в любой ситуации выдержать и остановить автомобиль. А цена работоспособности колодок очень высокая – это жизни людей, пассажиров и пешеходов.
Подавляющая масса современных автомобилей оснащена дисковыми тормозными колодками как более современными в отличие от применяемых ранее барабанных тормозов.
Дисковая тормозная колодка обычно состоит из стального каркаса различной формы и фрикционного слоя, который прикрепляется к стальному каркасу различными способами: с помощью клея, с помощью подложки через спецобработку шероховатости стального каркаса. Кроме того, тормозная колодка может содержать различные пружины для компенсации вибрации, шума; устройства в виде многослойных прокладок; различные типы индикаторов износа «аудио?» и «электро-», которые извещают водителя автомобиля о предельном износе колодок.
Все эти дополнительные устройства нужны, чтобы обеспечить нормальную работу фрикционного слоя колодки при его взаимодействии с чугунным (или стальным) тормозным диском.
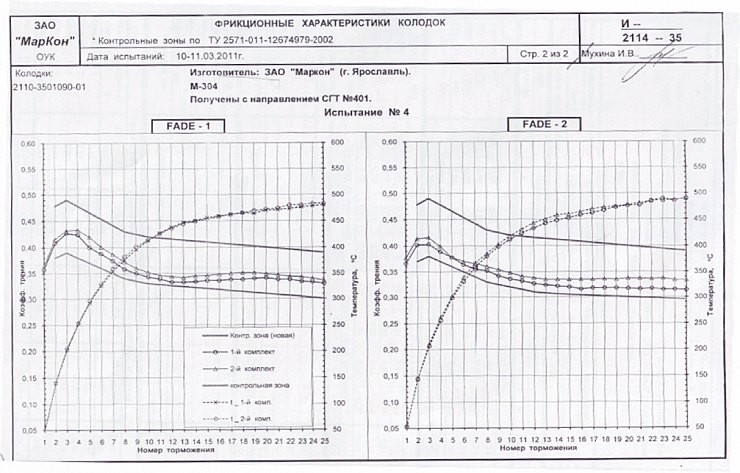
Фрикционный слой колодки состоит из различных ингредиентов, которых в смеси около 20. Они смешиваются в специальных смесителях (как правило, импортных), затем прессуются в прессформах под большим давлением (1000 кг/см) на стальном каркасе, термообрабатываются в специальных установках, далее механически обрабатываются, собираются с комплектующими, маркируются, упаковываются. Всё. Можно отправлять потребителю. НО!
Производитель должен гарантировать, что его продукция вовремя остановит автомобиль. Для этого необходимо проводить регулярные исследования и подтверждать те характеристики, которые задает изготовитель автомобиля.
Существует два типа тормозных колодок:
• оригинальные (ОЕМ), которые ставят на автомобиль на заводе-изготовителе;
• сменные, которые ставит на автомобиль владелец после износа оригинальных.
Требования к оригинальным колодкам задает конструктор автомобиля, и завод-изготовитель проводит испытания на соответствие требованиям. После положительных испытаний проводятся сертификационные в специализированной организации (в РФ это – «НАМИ-ФОНД», первый в России аккредитованный Орган по сертификации автомобильных изделий, Москва) в соответствии с ГОСТ Р41.13-11-99 и постановлением Правительства № 720 от 10 сентября 2000 года «Об утверждении технического регламента о безопасности колесных транспортных средств».
Существует несколько способов испытания транспортных средств с данными тормозными колодками: дорожные испытания по специальной программе; горные испытания (Fade); испытания на специальных динамических стендах.
Наиболее достоверную информацию о характеристиках тормозной колодки можно получить на специальных динамических стендах, где испытания проходят в натуральном узле автомобиля и по соответствующей программе с обработкой всех данных на компьютере.
Такие стенды с электронным управлением есть на АвтоВАЗе, г. Тольятти и в компаниях «МарКон» и ТИИР, г. Ярославль.
Условия испытаний: скорость со 100 км/ч снижается до 50 км/ч, цикл повторяется через каждые 45 секунд, производится 25 торможений.
В результате температура поднимается до 500–550° С. И что самое главное – коэффициент трения µ остается практически постоянным (кривая). Это великолепная тормозная колодка. Она полностью соответствует всем требованиям.
В определениях тормозного момента есть зависимость формулы от коэффициента трения: Мт = = 2µ • S • P • ср.R:
Мт – тормозной момент;
µ – коэффициент трения;
S – площадь поршня тормозного цилиндра;
P – давление тормозной жидкости;
R – среднеквадратичный радиус тормозного диска.
Таким образом, коэффициент трения играет главную роль в развитии тормозного момента.
Постоянство коэффициента трения (в диаграмме) говорит о стабильности тормозного момента, предсказуемости для водителя об управлении торможения и безопасности тормозной пары «колодка – диск».
В результате мы такими испытаниями подтвердили качество тормозной колодки в соответствии с требованиями стандартов. Но это еще не все!
Необходимо принять меры, чтобы все тормозные колодки, равно как и другие детали, которые вы производите, были одинаковыми по качеству. И это – не менее трудная задача.
Для решения задачи стабильности производства, обеспечения выпуска всех деталей одинаково хорошего качества необходимо внедрить на производстве «Систему менеджмента качества» – СМК.
Требования к СМК, ее разработка и внедрение рассматриваются в международных стандартах ISO 9001.
Первыми среди фрикционных производителей систему ISO 9001 внедрила компания «МарКон», Ярославль, в 1999 году и сертифицировала в немецкой компании DQS.
Внедрение этой СМК – достаточно сложный и трудоемкий процесс, требующий огромного внимания и труда как руководства завода, так и всего коллектива. Однако результаты внедрения обеспечивают хороший порядок во всех звеньях производственного процесса и взаимоотношениях с клиентами, значительно повышают качество продукции.
Позднее, в 2000-х годах был разработан специальный международный стандарт на базе ISO 9001 для автомобильной промышленности – стандарт ISO 16949.
Компания «МарКон» была аттестована и на этот стандарт немецкой фирмой DQS в 2007 году.
Учитывая, что аттестацию компании на эти стандарты проводили грамотные, педантичные и очень работоспособные немцы, которые кроме аттестации раз в три года проводят еще и ежегодные аудиты, получить сертификаты соответствия было достаточно сложно и совсем недешево.
Кроме требований к колодкам по постоянству к коэффициенту трения, предусматривается еще целый ряд требований, таких как норма износа, прочность на сдвиг фрикционного слоя, сжимаемость, экологичность (отсутствие асбеста, тяжелых металлов), теплопроводность, отсутствие шума и др.
Эти требования также заслуживают внимания и контроля и, безусловно, должны выполняться.
И еще один показатель – цена.
Не гонитесь за дешевой тормозной колодкой! Например, тормозная колодка для автомобиля Priora хорошего качества стоит ≈ 400 руб./компл. в магазине, а неизвестного качества ≈ 250–300 руб./компл. Вы делаете эту покупку в среднем один раз в 1,5–2 года, и разница в цене не критична, а безопасность значительно дороже.
Требуйте при покупке в магазине обязательно предъявить свежий сертификат качества (выданный институтом НАМИ) на данную марку колодки и фирму-производителя. Помните, что без сертификата качества продажа тормозных колодок запрещена, и продающая организация подвергается серьезному штрафу.
В России наиболее добросовестные и организованные производители дисковых тормозных колодок – это ЗАО «МарКон», ОАО «ТИИР», Ярославль, ЗАО «ВАТИ Авто», г. Волжский, Волгоградская обл.
Поддерживайте российских производителей!
Покупайте дисковые тормозные колодки производства «МарКон»!
Удачи вам!
Л.В. Молев
Слово производителю
Delphi на вторичном рынке
Delphi разрабатывает и производит современные автокомпоненты и системы для крупнейших мировых автопроизводителей. Как ведущий поставщик запчастей на конвейер компания применяет те же высочайшие стандарты для вторичного рынка и в настоящее время является одним из ведущих поставщиков на вторичном мировом рынке с общим объемом продаж приблизительно 1 млрд долл. в год.
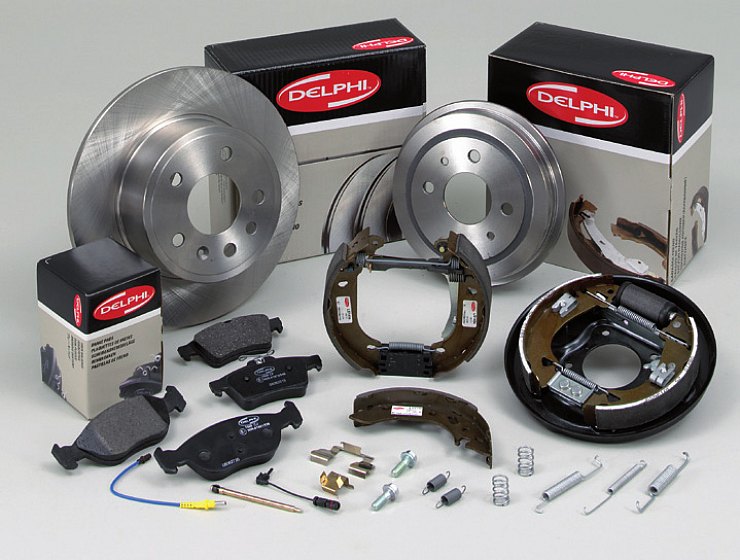
Подразделение Delphi Product & Service Solutions (DPSS) предлагает изделия на независимый вторичный рынок и в дилерские сети. Полный ассортимент продукции включает автомобильную электронику, дизельную продукцию, детали тормозной системы, амортизаторы, системы рулевого управления, подвески и кондиционирования воздуха, а также полный спектр сложного оборудования, средств диагностики и оборудования для проведения испытаний топливных систем.
Расположенный в Москве офис DPSS оказывает поддержку профессиональным специалистам вторичного рынка в России благодаря созданию сети дистрибьюторов, а также через авторизованных сервисных дилеров, предлагая средства диагностики, услуги и ремонт для топливного оборудования высокого давления. Программа для дизельных двигателей разработана для легковых и грузовых автомобилей, автобусов, грузовой, сельскохозяйственной, промышленной и морской техники.
Вниманию сервисмена
Почему некоторые автосервисы говорят: «Мы диски не точим, мы диски меняем»?
Обоснованно считается:
• диски надо не точить, а менять;
• автовладельцы не спрашивают эту услугу;
• допуски на дисках слишком малы, а износ от торможения тяжелой машины велик.
БАРКЛАЙ ХОЛДИНГ полностью согласен с этими аргументами.
Зачем в таком случае нужна проточка PRO-CUT?
Технические основания:
• при установке нового качественного диска на ступицу боковые биения тормозного диска, как правило, превосходят заводские нормы из-за микродеформаций ступицы;
• через 200–500 км после установки новых дисков автовладелец может ощутить вибрации при торможении и вернуться в автосервис с рекламацией.
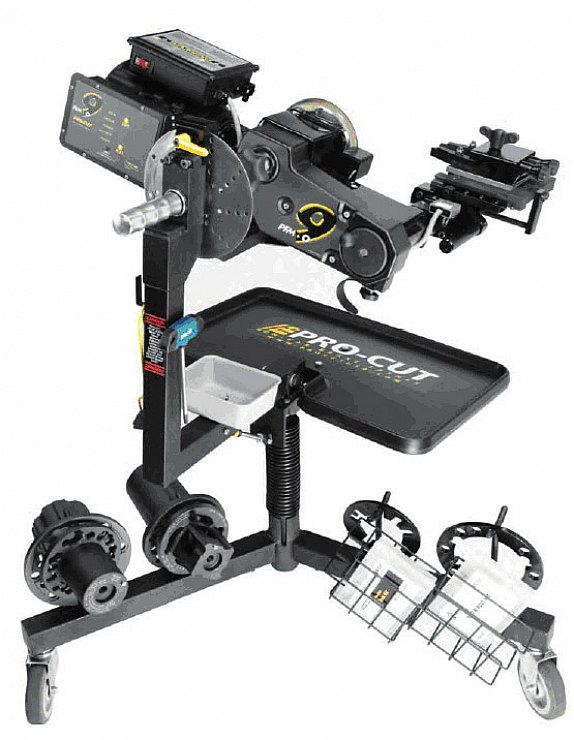
Что делает Pro-Cut:
• проточка нового диска при его установке или малоизношенного диска при установке колодок предотвратит появление вибраций и необоснованные рекламации со стороны автовладельца;
• снятие 20–50 мк с поверхности нового или малоизношенного диска не уменьшают его ресурс;
• PRO-CUT восстанавливает не только качество поверхности тормозного диска, но прежде всего его геометрию вращения в суппорте;
• 10 минут работы Pro-Cut на диск делают работу рентабельной для автосервиса и приемлемой по стоимости для автовладельца;
• простота и автоматика Pro-Cut делает работу по силам даже автомеханику-стажеру;
• восстановление заводской геометрии вращения диска в суппорте делает работу ABS, антипробуксовочной, антизаносной и других современных систем безупречно точной;
• автовладелец выбирает специализированный автосервис PRO-CUT Центр по сервису тормозных систем в качестве предпочтительного сервиса по ремонту тормозов своего автомобиля.
PRO-CUT меняет представления о проточке дисков.
От редакции. В этом обзоре использованы авторские материалы, а также фрагменты статей, подготовленных редакцией совместно с В.А. Соколовым и В.Л. Карпицким и опубликованных в «АБС-авто» в разное время.