«На скаку остановит...»
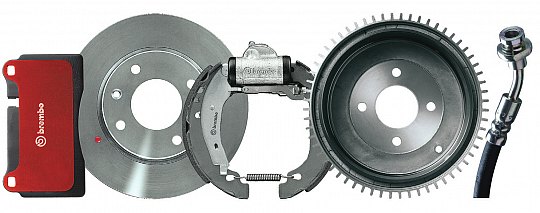
Есть горячие головы, настойчиво твердящие, что тормоза придумали трусы. Что сказать на это? Только одно – что некоторые афоризмы сочинили дураки. А тормоза придумали умные и смелые люди. И сейчас они делают все возможное, чтобы обеспечить нашим водителям безопасную эксплуатацию автомобиля и комфортную езду в любое время года.
«Пешеходов надо любить»
Тормозная система определяет активную безопасность автомобиля, и качество тормозных колодок играет здесь едва ли не главную роль. А требования к ним задаются нормативными документами Европейской экономической комиссии (ЕЭК) Организации Объединенных наций. Так, Правила № 13(13Н) ЕЭК ООН устанавливают требования к тормозным системам автомобилей, сходящих с конвейера, а Правила № 90 – к сменным тормозным накладкам, поставляемым в запчасти.
В частности, к обязательным требованиям, предъявляемым к колодкам дискового тормоза, относятся:
• фрикционные свойства;
• прочность соединения тормозной накладки с каркасом;
• геометрические размеры детали.
Упрощенно, колодка дискового тормоза состоит из каркаса и фрикционной накладки. Фрикционная накладка – деталь наиважнейшая. Основные ее задачи таковы:
• получение необходимых сил трения в процессе торможения;
• обеспечение стабильности коэффициента трения при изменении скорости вращения тормозного диска и давления в системе.
Об этом, и не только – в следующих разделах.
Заказчик – «пограничник»
Ни один автозавод не примет тормозную колодку на комплектацию без точного знания ее поведения под воздействием рядовых и экстремальных нагрузок. А знание это добывается комплексом длительных испытаний:
• образцов фрикционного материала, из которого изготавливается накладка;
• собственно колодок в натурных тормозных механизмах на специальных стендах;
• всей тормозной системы в целом на автомобиле.
Кто такой заказчик тормозных колодок, понятно: это автомобильный завод. И суровые люди в зеленых фуражках здесь ни при чем – не зря же мы взяли слово «пограничник» в кавычки. О каких же границах идет речь? А вот о каких...
Попробуем взглянуть на тормозные проблемы глазами конструктора автомобиля. Ему приходится решать множество сложных задач, назовем лишь две из них, важнейшие:
• обеспечение заданной эффективности торможения при сохранении прямолинейности движения;
• обеспечение строго определенного (запомним!) соотношения тормозных моментов на передней и задних осях.
К примеру, у какого-то автомобиля передние дисковые тормоза должны быть в 2,5 раза эффективнее, чем задние барабанные. У другой машины этот показатель будет иным, и т.д.
После доводки, связанной с проведением большого количества экспериментальных работ и испытаний (как стендовых, так и дорожных) автомобиль представляют в специальную техническую службу, аккредитованную ЕЭК ООН. Там, на полигоне, автомобиль получает (или не получает) подтверждение типа транспортного средства в отношении торможения на основании Правил № 13.
Естественно, в доводке тормозных колодок принимает активное участие и поставщик, разработчик тормозных изделий. Мы не можем в одной статье подробно описать все виды испытаний, поэтому остановимся лишь на оценке фрикционных свойств изделия на примере типовой методики (рис. на с. 42).
Во главу угла ставится оценка эффективности торможения, т.е. замедления. Естественно, существуют формулы и методики для пересчета эффективности торможения в коэффициент трения между колодкой и тормозным диском (контртелом), поскольку эти величины функционально связаны. Если же говорить предметно, определяются следующие характеристики:
• зависимость коэффициента трения от давления (усилия на педали) при торможении со скорости 100 км/ч и температуре 100°C (графики 1 и 6);
• зависимость коэффициента трения от скорости при давлении 50 кг/см2 и температуре 100°C (графики 2 и 7);
• зависимость коэффициента трения от температуры при скорости 100 км/ч и давлении 50 кг/см2 (графики 3 и 8).
А в чем разница между графиками 1 и 6, 2 и 7, 3 и 8? А вот в чем. В испытания включен так называемый «режим Фейд» (Fade), предусматривающий два цикла по 25 торможений, по 45 с каждое. В процессе замеряется изменение коэффициента трения при давлении 50 кг/см2 в диапазоне снижения скорости от 100 до 50 км/ч. По сути, это имитация спуска по горной дороге с частыми торможениями, т.е. обыгрывание жизненно важной ситуации (графики 4 и 9).
Так вот, графики 1, 2, 3 относятся к испытаниям, проводимым до режима Fade, а 6, 7 и 8 – после него. Поэтому три последние зависимости называют «повтором» или восстанавливаемостью колодки – эти термины говорят сами за себя.
А теперь самое главное: эталонные кривые, показанные на рис. 1–8, задает автозавод. Причем задает их в виде областей, или зон, ограниченных верхним и нижним пределами. Вот в эти-то зоны и должна вписаться кривая, полученная в результате испытаний.
Итак, новый автомобиль обрел «правильные» тормозные колодки, качество которых подтверждено документально. А как быть с запчастями – ведь «родные» конвейерные колодки рано или поздно придется менять? Здесь полезно знать следующее.
При разработке колодок для рынка запчастей за основу берутся оригинальные детали, прошедшие испытания по Правилам № 13. Согласно Правилам № 90, сменные колодки по своим свойствам должны отличаться от конвейерных не более чем на ±15%. А теперь взглянем еще раз на зоны, показанные на рис. 1–8. Собственный допустимый разброс коэффициента трения составляет от 10 до 12% в обе стороны. Увеличение этого диапазона до 15% означает лишь небольшое расширение зоны.
Выход за границы зоны недопустим: он грозит нарушением соотношения тормозных моментов по осям автомобиля, – а тут и до беды не далеко. Вот почему так важна сертификация запчастей: она гарантирует попадание фрикционных характеристик тормозных колодок в нужную область.
О технологии
Основные этапы создания дисковой колодки следующие:
• приготовление массы (фрикционной смеси);
• штамповка (вырубка) из стального листа каркаса будущего изделия с последующей дробеструйной обработкой – эта операция упрочняет каркас и улучшает адгезию с фрикционной накладкой;
• спекание фрикционной массы с каркасом в прессформе, т.е. формирование собственно колодки.
Вот мы говорим – фрикционная смесь... Вроде все просто... А тем временем современная рецептура накладок дисковых тормозов имеет 10, 15 и более ингредиентов, каждый из которых выполняет различные функции. Так, разработчики колодок подбирают:
• полимерные связующие, способные создать термостойкую матрицу с высокими прочностными свойствами (каучук, смолы, каучуко-смоляные, латексно-смоляные связующие);
• наполнители, обеспечивающие требуемый коэффициент трения и износостойкость;
• армирующие компоненты, упрочняющие полимерную матрицу.
Иногда при создании изделия применяют не менее двух-трех связующих и от двух до четырех армирующих наполнителей. Этот своеобразный каркас изделия выполняется из различных комбинаций стального, полиарамидного, минерального, стеклянного или углеродного волокна. Только при таком подходе можно получить изделия, надежно работающие в широком диапазоне температур, скоростей и давлений.
Производитель современных колодок освоил методы борьбы с «писком» колодок, в частности – противошумные мастики и пластины. Изделия комплектуются сигнализаторами износа. Все это стало обыденным делом. И даже святая святых – эффективность и стабильность тормозных свойств тоже пройденный этап, рядовая задача. Смешно, если бы современные колодки тормозили неэффективно...
Сегодня одно из важнейших направлений в работе над фрикционными накладками дискового тормоза – это исследования и регламентирование сжимаемости тормозных накладок. От того, насколько податлива накладка, зависит пауза от момента нажатия на педаль до возникновения необходимого тормозного усилия. Мягкая накладка может недопустимо затянуть эту паузу, слишком жесткая – вызовет нежелательные писки и скрипы при торможении. Нужен оптимум.
Но это еще не всё. Практика передовых предприятий показывает, что определение сжимаемости на разных стадиях изготовления накладки позволяет отследить, во-первых, стабильность каждого звена технологической цепочки, во-вторых, правильность техпроцесса в целом.
Управление сжимаемостью, ее «программирование» сокращают сроки и стоимость разработки новых видов продукции. А в итоге – повышает конкурентоспособность колодок. Ведь тормозить не только безопасно, но и комфортно сегодня желают многие, о чем только что говорилось.
Еще один интересный факт. У тормозной колодки есть период приработки. Под воздействием высоких температур в зоне трения образуется рабочий слой фрикционного материала и происходит его дополнительная термостабилизация. Для получения такого слоя на поверхности накладки ведущие зарубежные и российские компании применяют операцию «термоудара» – высокотемпературной обработки рабочей поверхности на специальном оборудовании.
После термоудара колодка получает высокие фрикционные характеристики в начальный период эксплуатации. Это сводит к минимуму период приработки и позволяет эксплуатировать колодки в обычном режиме практически сразу после установки на автомобиль. Теперь найти различия между оригинальными и «» колодками вообще очень трудно. Привычная «обкатка» современным изделиям не нужна.
«Тормозные» публикации
Все ли изделия отвечают необходимым требованиям? В поисках ответа автолюбители обращаются к популярным журналам и газетам, выискивая «советы бывалых» и рекомендации специалистов. Многие уповают на знания и опыт продавцов-консультантов. Однако ни СМИ, ни труженики прилавка часто не могут предоставить объективной информации.
Да и о какой объективности говорить, если в иных (даже весьма авторитетных!) изданиях то и дело появляются публикации о «независимых редакционных испытаниях» тех или иных запчастей. При этом в «тестах» и «экспертизах» используются самодельные методики, а результаты толкуются весьма фривольно. И тогда... тогда между строк легко угадывается истинный заказчик статьи. Понятно, что польза от такой публикации весьма сомнительна, если не сказать больше.
Удивительно, как любит наш народ пропорции: формула «чем больше, тем лучше» многим представляется всесильной и универсальной, едва ли не магической. Если речь идет о деньгах – это так, спорить не будем. Но в остальных случаях надо крепко подумать, прежде чем делать подобные заявления.
Мы уже писали: большинство современных тормозных накладок имеет коэффициент трения 0,35–0,45. Заниженные фрикционные свойства приводят к увеличению времени торможения и тормозного пути, что отрицательно сказывается на безопасности. А слишком высокие сужают диапазон воздействий на педаль от начала торможения до блокировки колес. А блокировка и безопасность вообще не совместимы.
Однако в разговорах о качестве тормозных колодок некоторые водители рассуждают примерно так: «Чем сильнее "хватает", тем лучше. Надежнее, стало быть». И ладно бы только водители – многие СМИ столь же активно пропагандируют это опасное заблуждение.
Помнится, некое автомобильное издание (не будем оглашать имен, ибо оно не одиноко в своих заблуждениях) опубликовало результаты испытаний колодок дисковых тормозов от различных производителей. Как вы уже догадались, автор той статьи при оценке результатов исходил из тезиса... ну, конечно же – «чем коэффициент трения больше, тем лучше».
Вооруженный пропорцией, а потому линейно мыслящий автор разделил испытанные колодки на три группы: лидеры, середнячки и аутсайдеры. И что же вы думаете? В число аутсайдеров попали известные производители тормозных колодок, чья продукция отличается высоким качеством. И невдомек автору публикации, что именно эти колодки укладываются в требуемые заводом зоны, в то время как выявленные изданием «лидеры» с запредельными коэффициентами трения «уводят» колодку от эталона аж на 30–35% вместо 15%, оговоренных Правилами № 90.
Словом, все получилось с точностью до «наоборот». И не дай бог кому-нибудь экстренного торможения на так называемых «лидерских» колодках: конструкторская «развесовка» тормозных моментов из-за чересчур «хватких» колодок неизбежно нарушится – и, здравствуй, кювет!
Наряду с известными российскими и иностранными производителями тормозных колодок на рынке широко представлены так называемые «перепаковщики». Это маркетинговые фирмы, которые размещают заказ «на стороне», а затем выводят на рынок продукт под собственным «брендом».
Упаковки красивые, яркие. Но что интересно: информация о производителе, как правило, отсутствует. Иногда мелким шрифтом стыдливо указывается «страна-изготовитель». Зато сам «бренд» продвигается изо всех сил – в печати, эфире, торговых центрах. «Перепаковщики» используют броские названия с привлекательными и легко читаемыми иностранными словами – SUPERMASTER или MEGASPORT и т.д. (примеры условные).
Мы не утверждаем, что все «перепакованные» изделия плохи. Вы нам расскажите, чем они замечательны?
Вряд ли продавцы смогут вразумительно ответить на данный вопрос. В лучшем случае сошлются на уже упоминавшиеся «тормозные» публикации – и получится замкнутый круг. А покупателю нужна обоснованная и квалифицированная оценка предлагаемых колодок. Это же не магнитола, не коврики, не шампунь автомобильный. Тормоза!
Dura Lex
Покупатель имеет право знать о запчастях все. На его стороне следующие законы:
• «О защите прав потребителей» – суть ясна из названия;
• «О техническом регулировании» – документ, регламентирующий соответствие продукции обязательным требованиям и ее сертификацию;
• «О рекламе» – этот закон не допускает недобросовестной, недостоверной, неэтичной и заведомо ложной рекламы.
Между прочим, за нарушение данных законов предусматривается не только гражданско-правовая, но и уголовная ответственность. Продавец-консультант, рекомендующий или намеренно продвигающий чей-то «бренд», по-видимому, о таких законах просто не знает. Или не понимает, какая на нем лежит ответственность.
А тем временем, по зарубежным данным, половина дорожно-транспортных происшествий вызвана неисправностями автомобиля. К сожалению, российская статистика грешит неточностями: разбирательства аварий чаще всего заканчиваются вердиктом «не справился с управлением». Если же тщательно проанализировать причины ДТП, то лидировать будут дефекты тормозной системы.
Думается, сказанное – достаточный повод для выбора именно оригинальных запчастей, в том числе и тормозных колодок. Да, они зачастую дороже, зато их надежность гарантирована. Они одобрены автозаводами и поставляются не только в запчасти, но и на комплектацию конвейеров. На их стороне не только официальное одобрение качества, но и постоянно действующий входной контроль при поставках.
В статье использованы редакционные материалы, а также фрагменты статей, подготовленных автором совместно с В.Л. Карпицким и опубликованных в «АБС-авто» в разное время
Информация от производителя
Рассказывать о новых тормозных колодках Delphi – сложно. Ежегодно компания, крупнейший производитель автомобильных компонентов и систем, поставщик конвейеров и рынка запчастей, значительно расширяет свой и без того огромный ассортимент, который только в области тормозных систем превышает 9000 наименований.
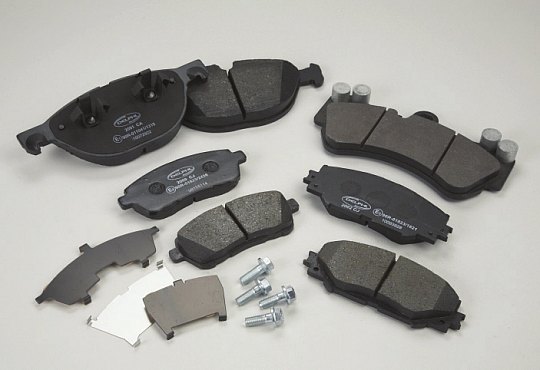
В частности, в прошлом, 2012 году компания представила 220 новых артикулов: тормозные диски, тормозные колодки, тормозные накладки и барабаны, новые датчики ABS для новых Audi A6, A7, A8, Citroen C4 & DS4, Peugeot 508, BMW 5-й и 6-й серий, Seat Alhambra и VW Amarok и Sharan.
Причем, что характерно, все поставки осуществляются в комплектах, в эргономичных упаковках. Это удобно для сервисов – легко транспортировать, сортировать, хранить.
Такой высокий темп выпуска новых продуктов понятен – в компании действует правило: при выходе на рынок новой модели автомобиля тормозные колодки для нее должны появиться не позднее, чем через шесть месяцев.
Однако самостоятельно разобраться в этом «изобилии» практически невозможно. Поэтому в компании огромное внимание уделяется изданию и переизданию каталога своих изделий.
Номенклатура каталога Delphi включает как уже выпускающиеся, так и новейшие модели автомобилей. Все новые детали представлены в последней версии каталога «European Friction».
Кроме того, информация доступна в электронном виде, например, в каталоге «Tec Doc», в котором Delphi фигурирует в качестве «Сертифицированного первоклассного поставщика информации».
Высокий уровень качества поддерживается благодаря сильной научной базе. В лабораториях компании каждый год испытывается и оценивается около 200 новых фрикционных материалов, и их параметры сравниваются с параметрами уже используемых. После этого инженеры подбирают тип материалов для каждой модели автомобиля. Выбор зависит от ряда факторов: использование автомобиля, рынок, место установки (передние или задние тормоза) и распределение веса машины.
Что важно – все тормозные колодки Delphi проходят ряд испытаний: стандартное европейское AK Master European, испытание Auto Motor und Sport (AMS), анализ шума на динамометре, испытание в горных условиях, испытание на высокой скорости на автомагистрали, испытания FMVSS и Ameca (для выполнения требований США).
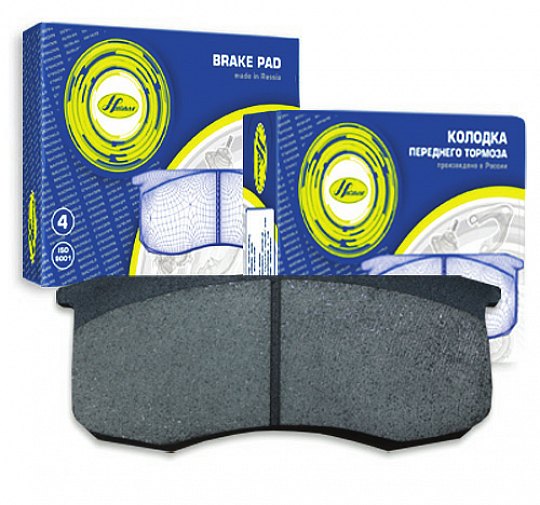
Информация от производителя
В феврале 2013 года производственное объединение «Начало» приступило к выпуску новых передних тормозных колодок для автомобилей. Новые изделия поступили в продажу уже в марте.
Передние тормозные колодки 3160-350190 полностью соответствуют необходимым техническим требованиям, имеют хорошие показатели эффективности торможения, обладают большим запасом прочности и, что немаловажно, при их использовании тормозные диски при экстренных и частых торможениях не деформируются. Каркас тормозной колодки имеет лакокрасочное покрытие, которое обеспечивает надежную коррозийную стойкость вне зависимости от климатических условий.
Информация от производителя
Корпорация Federal-Mogul производит тормозные колодки двух основных брендов: Wagner и Ferodo.
Wagner – бренд массовый, рассчитанный на вторичный рынок. Его номенклатура охватывает примерно 96% европейского парка легковых автомобилей. Кстати, он занимает лидирующее место и на рынке США. Колодки Wagner относятся, скорее, к среднеценовой категории продукции – хотя есть и «премиальные» продукты с этим брендом.
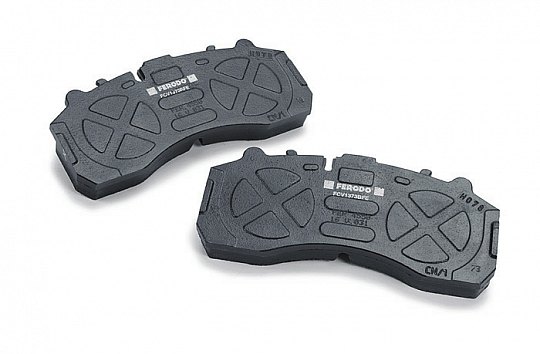
Ferodo считается брендом «премиального» уровня – и продукция этой марки поставляется в основном на сборочные конвейеры крупнейших производителей автомобилей. Кроме того, в ассортименте Ferodo есть линейка колодок для спортивных гонок и тюнинга.
Стоит отметить, что номенклатура фрикционных изделий Federal-Mogul большая, а качество стабильно высокое. И на российском рынке представлена практически вся гамма этой продукции. Потому выбор конкретных тормозных колодок ограничен лишь моделью автомобиля и финансовыми возможностями покупателя.
Информация от производителя
Авто-Евро работает на рынке автозапчастей уже 20 лет. Наша компания за годы работы зарекомендовала себя как надежный поставщик мультибрендовых запчастей для автомобилей (европейского, японского корейского, китайского и российского производства) – можно заменить для иномарок и российского производства. В настоящее время наш ассортимент насчитывает более 40 тыс. позиций запчастей для легковых, грузовых и коммерческих автомобилей. Все запчасти проходят обязательную сертификацию, и на них предоставляется гарантия.
Одним из старейших брендов в нашем ассортименте является бренд ATE. ATE – это торговая марка, принадлежащая компании Continental Teves. Фирма была первопроходцем в разработке гидравлических тормозов, а позже антиблокировочных систем ABS. Её достижения становились вехами, которые отмечают непростую работу над тем, чтобы сделать управление автомобилем безопасным и надежным.
Качество продукции ATE, поставляемой на вторичный рынок, соответствует качеству, поставляемому на сборочные конвейеры автопроизводителей. Продукция ATE часто становится выбором автопроизводителей автомобилей, это обусловлено лидирующими позициями продукции ATE в области разработки тормозных систем.
Единое качество для автопроизводителей и вторичного рынка делает марку ATE очень популярной. Продукция ATE на вторичном рынке № 1 в Германии с долей рынка 30%, № 2 в Европе, и входит в десятку лучших в мире.
Помимо основной линейки, в ассортименте Авто-Евро представлена линейка продукции с улучшенными характеристиками, это: усиленные тормозные диски серии ATE PowerDisc и тормозные колодки ATE Ceramic.
Отличительная особенность тормозных дисков ATE PowerDisc – бесконечная канавка, которая отводит газы и загрязнения, снижающие эффективность торможения. В результате чего не происходит падение эффективности тормозов, вызванное нагревом тормозных колодок.
Еще одно преимущество – «эффект очищения» – обеспечивается снашиванием детали без рифления и волнистости, это удлиняет срок службы дисков. А если усиленные диски скомбинировать с высокотехнологичными накладками ATE Ceramic, то эффект будет более явно выражен.
Тормозные колодки ATE Ceramic
Специалисты фирмы Continental нашли решение, благодаря которому выделение пыли при торможении и шумность понижаются, а бережное отношение к материалам и к экологии повышается. Это техническое решение называется ATE Ceramic. Секрет тормозных накладок нового типа заключается в инновационной смеси, применяемой для их изготовления. Используется технология композиционного материала на углеродоволокнистой основе. При торможении эти накладки образуют на тормозном диске так называемый трансферный слой. Он препятствует быстрому истиранию дисков. Результат: меньше пыли, больше комфорта, меньше износ.
Информация от производителя
Продукция «ЕЗАТИ» известна российским потребителям уже несколько десятков лет. Автомобильные прокладки и колодки «ЕЗАТИ» ассоциируются у отечественных автолюбителей с недорогой продукцией, появившейся в советское время и отличающейся высокой надежностью.
История «ЕЗАТИ» насчитывает более 75 лет: первые цеха завода автотормозной ленты были введены в строй в конце 20-х годов прошлого века. За это время завод переживал эвакуацию, второе рождение (1969 год), расширение, модернизацию, но практически все время он оставался одним из ведущих предприятий в своей отрасли. C 1973 года предприятие на 100% обеспечивало фрикционными изделиями конвейер АвтоВАЗа. Параллельно шло интенсивное освоение производства деталей для отечественных автомобильных заводов АЗЛК, ГАЗ, УАЗ. В 2005 году штат работников завода составлял 900 человек, а ассортимент выпускаемой продукции превышал 250 наименований изделий.
В 2008 году «ЕЗАТИ» перешло в собственность волжского предприятия «ВАТИ-АВТО», выпускающего аналогичную продукцию. Новые хозяева начали работу с модернизации производства, благодаря которой удалось улучшить качество продукции и оставить цены на прежнем уровне.
Сегодня завод «ЕЗАТИ» производит продукцию в г. Волжском Волгоградской области, отсюда же ведутся отгрузки. В руках новых владельцев начал расти ассортимент деталей «ЕЗАТИ». Последняя новинка производства – колодки дискового тормоза на автомобили иностранного производства:
• DAEWOO Nexia, Lanos;
• HYUNDAI Accent;
• FORD Focus, Focus II;
• RENAULT Logan/ VAZ Largus;
• Chevrolet Lacetti, Aveo;
• KIA Rio.
Заботясь о комфорте и безопасности потребителей, предприятие непрерывно ведет исследовательские и испытательные работы, в результате которых совершенствуются технологии и процессы изготовления тормозных колодок. Специалисты «ЕЗАТИ» и «ВАТИ-АВТО» смогли вовремя отреагировать на внедрение новых правил, касающихся содержания асбеста, и разработать новые составы и смеси для фрикционных материалов тормозных колодок, которые позволяют нивелировать ухудшение эксплуатационных свойств, связанное с отказом от асбеста.
Большое внимание завод уделяет борьбе со скрипом колодок. Сотрудники предприятия на основе многочисленных проведенных испытаний и анализа существующих решений разработали свою конструкцию колодок, позволяющую избавить продукцию от этого неприятного недостатка.
При установке тормозные колодки «ЕЗАТИ» не требуют никаких регулировочных работ и обеспечивают высокую работоспособность тормозной системы на протяжении всего срока службы. Используя данные тормозные колодки, потребитель может забыть о замене на ближайшие 45 тыс. км пробега в жестких условиях эксплуатации, а это немаловажный факт, так как замена колодок – это затраты не только денег, но и времени.
Иными словами, на современном рынке автозапчастей передние тормозные колодки «ЕЗАТИ» выделяются оптимальным соотношением цена/качество, гарантируют эффективность торможения при любом стиле езды, доступны по цене и обладают хорошими рабочими характеристиками.
Отдел маркетинга ЗАО «ВАТИ-АВТО»
Тел. для справок в г. Волжском:
8 (8443) 210-968.
E-mail: omavto@vati.ru
Информация по оборудованию
Как работает тормозной диск автомобиля? Движущийся автомобиль обладает кинетической энергией. Затормозил, остановился – и эта энергия преобразовалась в тепловую: произошел нагрев тормозов, в том числе и тормозных дисков. Их температура может возрастать до 300–400°С, а при интенсивном торможении превысить и 500°С. При этом диск прогревается очень неравномерно. Самая высокая температура наблюдается в области контакта диска с колодками. В других участках температура ниже за счет охлаждения воздухом и отвода тепла к более холодным частям диска.
При таком неравномерном нагреве диск прогибается, а его толщина изменяется в зависимости от степени нагрева. В результате плоские рабочие поверхности диска деформируются, а их износ становится неравномерным. Кроме того, механические абразивные частицы, попадающие между диском и колодкой, серьезно усугубляют эту картину.
Все это приводит к уменьшению площади контакта диска и колодки.
Понятно, что в трущейся паре «диск-колодка» изнашиваются оба участника процесса, причем на изношенном диске колодки стираются интенсивнее, чем на исправном.
Допустим, вместо положенных 20–30 тыс. км, комплект передних колодок прошел всего 10 тыс. Снимаем колеса, меняем колодки на новые и едем дальше. Почувствовали разницу? Вы давите на педаль изо всех сил, а автомобиль едва удается остановить. Поверхность колодок ровная, а у диска – вкривь и вкось. Пока колодки не притрутся, так и будет. И чем сильнее изношены диски, тем заметнее и дольше этот эффект проявляется. Некоторые производители колодок даже пишут на упаковке предупреждение – соблюдать осторожность после замены в течение первых 200–300 км пробега автомобиля.
Бывает и так – при торможении появился характерный скрежет металлической основы колодок, работающей по диску. Сняли колодки, посмотрели – осталось еще 4–5 мм фрикционного материала, а уже требуется их замена, поскольку на краях изношенных дисков образовались характерные «буртики», в которые при торможении упирается основа колодки.
Иногда при торможении появляется вибрация. Она может проявляться на кузове автомобиля, но в ряде случаев сильнее всего ощущается на руле и педали тормоза. Такие проявления говорят о дефекте тормозных дисков. Обычно это связано с неравномерностью износа диска, при котором его толщина по всей окружности оказывается различной.
Нередки и случаи коробления диска. Это может случиться при быстрой езде с интенсивными разгонами и торможениями. Такой режим эксплуатации автомобиля способствует сильному разогреву тормозных дисков. Случайное резкое охлаждение разогретых дисков в луже или на автомойке может привести к тому, что диски «поведет». Это проявится биением рабочих поверхностей тормозных элементов относительно оси вращения колеса.
Дефектный тормозной диск, естественно, потребует серьезного ремонта. Его, конечно, можно заменить, но для владельцев некоторых марок и моделей автомобилей это будет весьма накладно. Сегодня многими автосервисами освоен ремонт тормозных дисков с применением специального оборудования. Различные производители такой оснастки предлагают разные способы проточки. Голландская компания MAD Tooling производит установки, у которых механизм подачи резцов закрепляется непосредственно на корпусе колесного подшипника или на поворотном кулаке вместо тормозного суппорта. При такой схеме ремонта биение проточенной поверхности диска не превышает 5 мкм, что в 5, а то и в 10 раз точнее, чем у нового диска! К тому же такой метод учитывает реальное положение тормозного суппорта, а значит, и после ремонта он обеспечит строгую перпендикулярность поверхности диска к оси тормозного цилиндра. Установка MAD DA-8700 существенно снижает затраты времени на ремонт дисков. Ремонтнику требуется всего 5–7 минут для проточки, еще столько же для снятия и установки колеса, тормозного суппорта и блока резцов. В общей сложности, с учетом совмещения операций – не более 30–40 минут на ремонт всех дисков автомобиля.
Стандартно установка поставляется с комплектом универсальных кронштейнов, шайб и болтов (SK-425). Нами сформировано специальное предложение: расширенная комплектация по стандартной цене. Вместо SK-425 мы комплектуем установку новой конструкции быстромонтируемыми универсальными кронштейнами USM2002R и USM2002B. Они позволяют быстро и точно установить блок резцов на автомобилях с резьбой на поворотном кулаке или ступице (USM2002B), либо с резьбой на тормозном суппорте (USM2002R).
Стоимость установки MAD DA-8700 (с новым блоком привода) по спецпредложению в полном комплекте всего 3840 евро.
По вопросу приобретения установки обращаться в компанию «ГАРДИА»:
+7 (495) 956-31-66
www.gardia.ru