Подруга тормозного диска
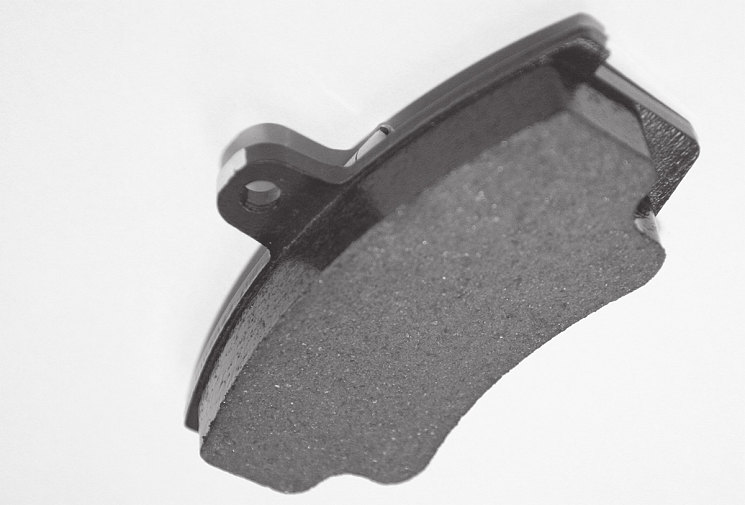
Пролог
Как гласит фундаментальная Большая Советская Энциклопедия и ее младшая сестра Википедия, слово «тормоз» происходит от греч. tоrmos – отверстие для вставки гвоздя, задерживающего вращение колеса повозки.
И сразу представляешь себе каких-нибудь древних завоевателей у костра. Жарят быка, амфоры с вином открывают, девушек в туниках обнимают, дескать, сейчас расслабимся – а тут начальник: «Так, ребята… А вы боевые колесницы на tоrmos поставили? А ну, быстро встали!..».
Сегодня тормоз ассоциируется прежде всего с тормозными колодками. Это понятно – колодки по мере износа заменяются на ТО, помогая бюджету автосервисов и магазинов запчастей. Поговорим о наиболее распространенных колодках – дисковых.
Изысканные рецепты
Упрощенно, колодка дискового тормоза состоит из каркаса и фрикционной накладки. На первый взгляд, все легко и просто.
Приготовил фрикционную смесь, темную массу в виде тяжелого порошка. Вот вам будущая фрикционная накладка.
Вырубил из стального листа фигурную пластину – вот каркас колодки.
Обработал каркас «дробеструйкой» для упрочнения поверхности и пущей адгезии к накладке. Нанес адгезионное покрытие.
Поместил каркас с фрикционной смесью в пресс-форму – и в печь ее, в печь! И получилась колодка.
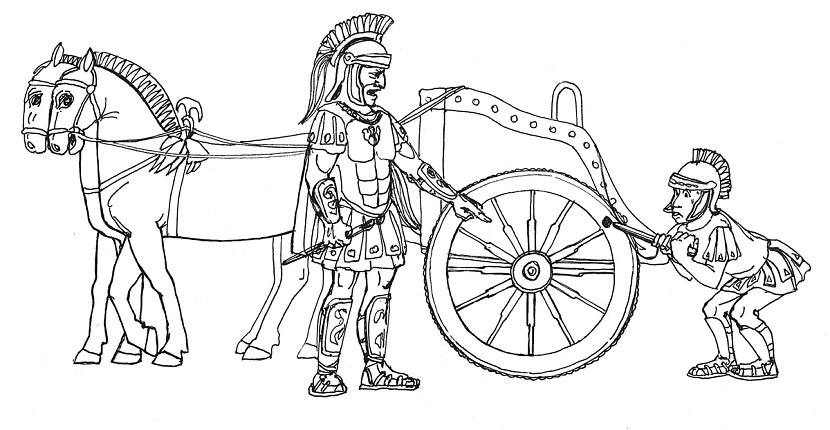
Только простота эта обманчивая. Рецептура фрикционной смеси включает 10, 15 и более ингредиентов, каждый из которых решает собственную задачу. И над их комбинациями день и ночь ломают головы лучшие научно-исследовательские подразделения компаний, выпускающих те самые колодки. Вот об их трудах и поговорим.
Итак, рецептура. Что же в нее входит? Наполнители для получения нужного коэффициента трения и обеспечения его стабильности. Ингредиенты для повышения износостойкости. Армирующие компоненты для упрочнения полимерной матрицы. Этот «скелет» будущей накладки выполняется из комбинаций различных волокон – кое-что о них мы узнаем далее. А пока заметим: фрикционные композиции, надежно работающие в широком диапазоне температур, скоростей и давлений, можно получить только в специализированной лаборатории.
Надежно работающие фрикционные композиции – это не пустой звук. Например, коэффициент трения колодки должен оставаться стабильным при росте температуры. К сожалению, это получается не у всех производителей – иногда по незнанию, иногда в погоне за быстрой прибылью, но чаще по двум причинам одновременно.
Бывают и такие колодки: в холодном состоянии тормозят, а разогревшись до 500° С превращаются из фрикционных деталей в… антифрикционные. И такие результаты не единичны. Сколько протоколов «Не справился с управлением», сколько трагических ДТП породили антифрикционные колодки?
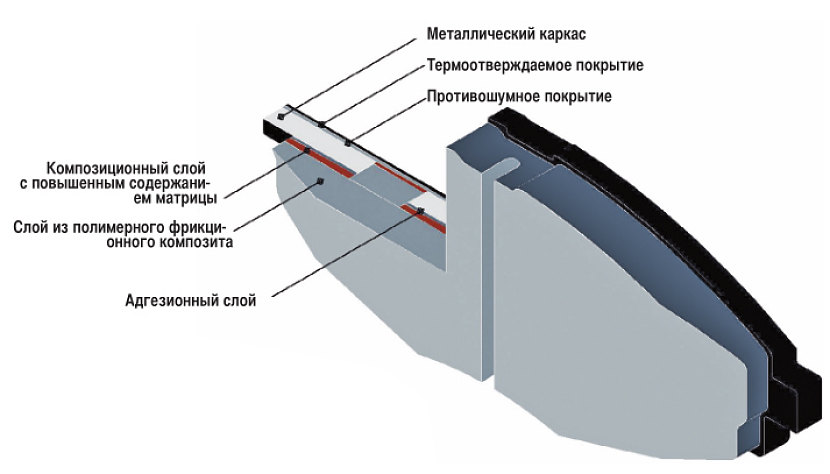
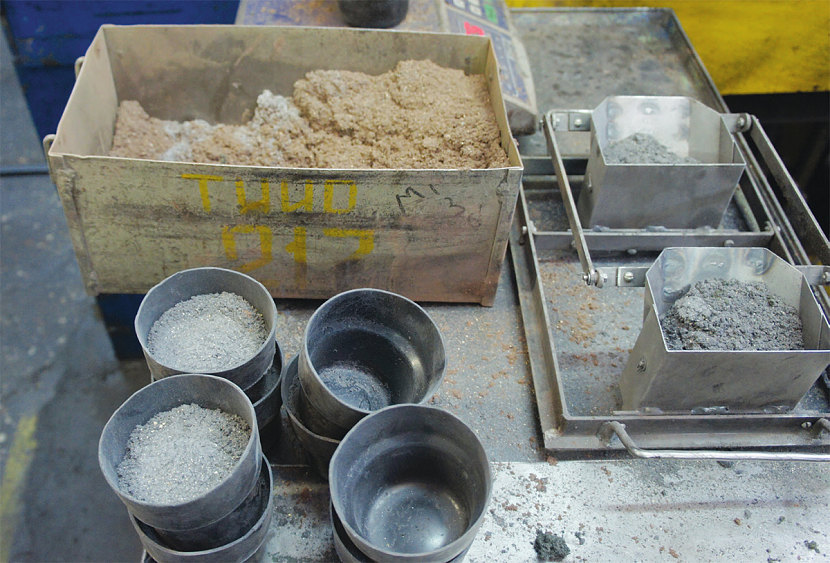
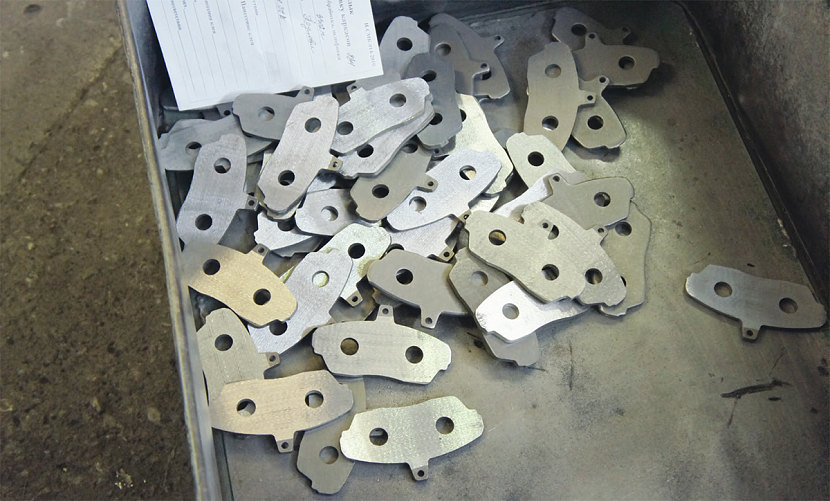
Для справки: антифрикционными считаются изделия, коэффициент трения у которых меньше 0,2. В то время как у колодки для усредненного легкового автомобиля он лежит в диапазоне 0,35–0,45.
Однако думать, что чем коэффициент трения больше, тем лучше, неверно. Излишне эффективные тормоза будут провоцировать «прихватывание» колодок. Если на машине нет ABS, это приведет к юзу.
А если ABS есть, она будет срабатывать при малейшем нажатии на тормозную педаль. Хотите все время тормозить «с трясучкой» на руле? Нет, конечно. Поэтому коэффициент трения должен быть не маленьким и не большим, а оптимальным и стабильным, отвечающим требованиям производителя автомобиля.
А еще колодки должны быть экологичными. Об этом – далее.
«Зеленое» торможение
Прогресс – штука неоднозначная. Например, чем комфортнее человеку, тем хуже природе. И автомобили играют здесь весьма заметную роль.
Эмиссия отработавших газов, утечки технических жидкостей, продукты износа узлов и деталей, автомойки и сервисные станции, построенные с нарушением санитарных норм, несовершенная утилизация, свалки автохлама… Все это ложится непосильным бременем на естественные «фильтры и регенераторы» нашей планеты.
А число «самобеглых колясок» растет фантастическими темпами. Ну как тут не ужесточать экологические требования? Естественно, под раздачу попадают и автокомпоненты, в том числе тормозные колодки.
Фрикционная накладка для современной тормозной колодки изготавливается из сложного композита. Он должен обеспечивать безопасность и комфорт, минимизировать износ контртела (диска или барабана) и побеждать в конкурентной борьбе на рынке. А тут еще экологичность навесили! И куда производителю податься?
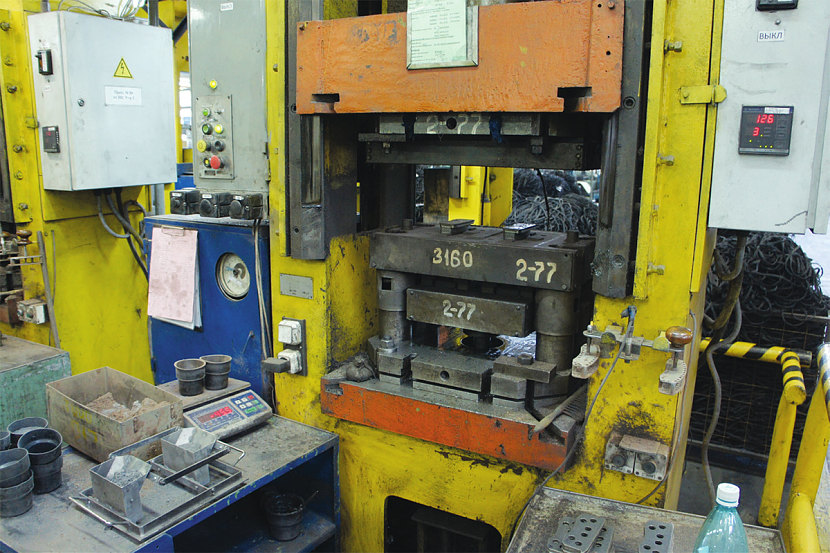
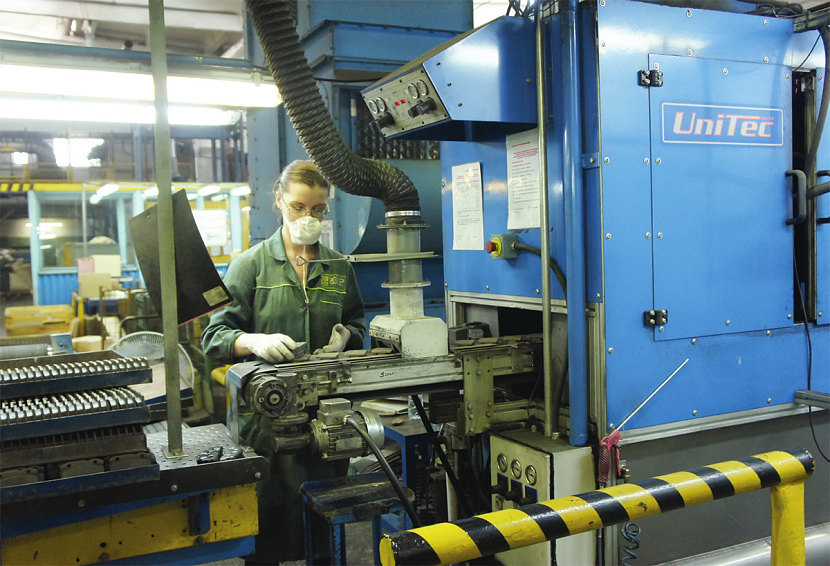
Как это – куда? Завоевывать рынок, разумеется. С огромным сейфом наперевес. А в сейфе – секреты и патенты, патенты и секреты. Секреты секретами, но общие тенденции развития фрикционных рецептур проследить можно.
Начнем с асбеста – его-то в рецептурах использовать точно нельзя. Или все же можно? Это вопрос… Но обо всем по порядку.
Асбест: казнить нельзя помиловать
Еще каких-нибудь 30 лет назад асбестовые волокна в тормозных колодках никого не волновали. Ну, пылят тормоза асбестом и пусть себе пылят. Зато тормозят хорошо и в изготовлении дешевы.
Все было прекрасно, пока в 70–80-х годах прошлого века асбест не объявили канцерогеном. Здесь требуется пояснение. Привычное слово «асбест» объединяет два типа силикатных волокон:
• серпентиновую группу (хризотиловый асбест);
• амфиболовую группу (крокидолит, родусит и др.).
В России распространен хризотил-асбест, в Канаде и Южной Африке – амфиболы. Запомним это.
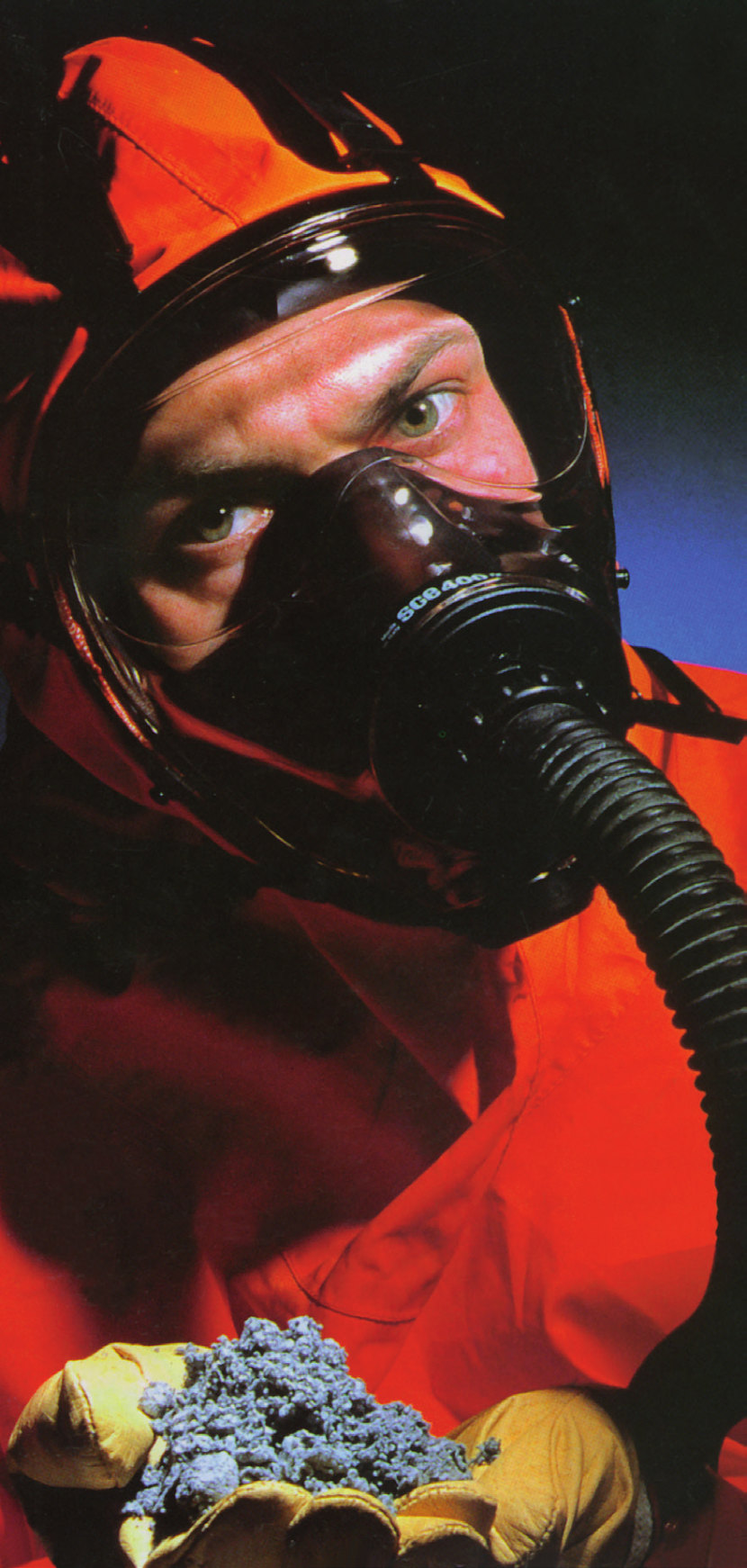
Зарубежные ученые заявили, что асбест при механическом воздействии расщепляется на тонкие волокна. В свою очередь, они распадаются на более тонкие, потом на тончайшие и т. д. Этот процесс называется фибрилляцией. Ее конечный продукт – полые трубки с внутренним диаметром 110–130 ангстрем и с наружным порядка 260 ангстрем. Иными словами, это наноиглы, напоминающие хирургические инструменты для генетических операций.
Если речь идет о шифере, асбестовом утеплителе, огнестойкой ткани, то асбест вреда не приносит, поскольку не расщепляется. А вот при торможении с асбестовыми колодками процесс фибрилляции идет непрерывно. И наноиглы попадают в воздух, оседают в легких, пищеводе и других органах. И уж как они себя поведут, одному богу известно.
И тут разгорелась информационная война. Специалисты Института медицины труда РАМН заявили, что большинство зарубежных исследований проводилось с амфиболами. А это вам не хризотил! Волокна хризотиловой группы со временем выводятся из организма, а вот амфиболовой – накапливаются в нем. Значит, заявили наши ученые, родной хризотил-асбест менее вреден, чем амфиболы.
Но противники асбеста победили. Амфиболовые группы во многих странах объявили вне закона. Заодно запретили и хризотиловый асбест. Говоря официальным языком, использование асбеста в тормозных колодках запрещено Правилами № 13, 78 и 90 ЕЭК ООН.
Страны Евросоюза и сами асбестовых колодок не производят, и к себе такую продукцию не пропускают. Россия обязалась выполнять Правила еще в 1999 году. Dura lex, sed lex – закон суров, но это закон.
И тут начались чудеса. У нас появился Технический регламент Таможенного союза «О безопасности колесных транспортных средств». С 1 января 2015 года он действует на территории России, Белоруссии и Казахстана.
В основном он повторяет прежний регламент – российский. Кроме одного – Примечания под номером 10, пункт 6. Звучит оно так (читаем внимательно!): «В отношении колодок <…> поставляемых для послепродажного обслуживания транспортных средств, требования пункта 5.1.1.3 Правил ЕЭК ООН № 13, пункта 5.1.1.3 Правил ЕЭК ООН № 13Н, пункта 5.4 Правил ЕЭК ООН № 78, пункта 5.1(d) Правил ЕЭК ООН № 90 применяются факультативно».
Ключевые слова – «применяются факультативно». А ведь эти пункты как раз говорят о запрете асбеста в тормозных изделиях! Получается, на территории Таможенного союза асбест в тормозах применять можно – факультативно.
Вы что-нибудь поняли? Запрещен у нас асбест или не запрещен? По Правилам ЕЭК ООН – запрещен; по Техническому регламенту – нет. При этом мы клянемся, что свято чтим Правилам ЕЭК ООН. Такой вот театр абсурда.
Non-copper
Сегодня понятие «экологическая колодка» расширилось. Ведущие производители автокомпонентов заявляют, что теперь они выпускают тормозные колодки без меди. И очень этим гордятся.
Правильно гордятся. Медь во фрикционных изделиях – тоже не подарок для окружающей среды. Чтобы не быть голословными, давайте разберемся в некоторых химико-технологических тонкостях.
В рецептуру фрикционной смеси, из которой формуют тормозные накладки, издавна вводили медь. А точнее, измельченную латунную или бронзовую стружку. Это было и хорошо, и плохо. Поначалу хорошему радовались, а о плохом не думали.
Что же в ней хорошего – в меди? Во-первых, она обладает отменной теплопроводностью. Вспомните: бабушки в деревнях всегда варили варенье в медных тазах – в них оно не пригорало. По той же причине медь прекрасно отводит тепло из зоны контакта фрикционной накладки с контртелом – тормозным диском.
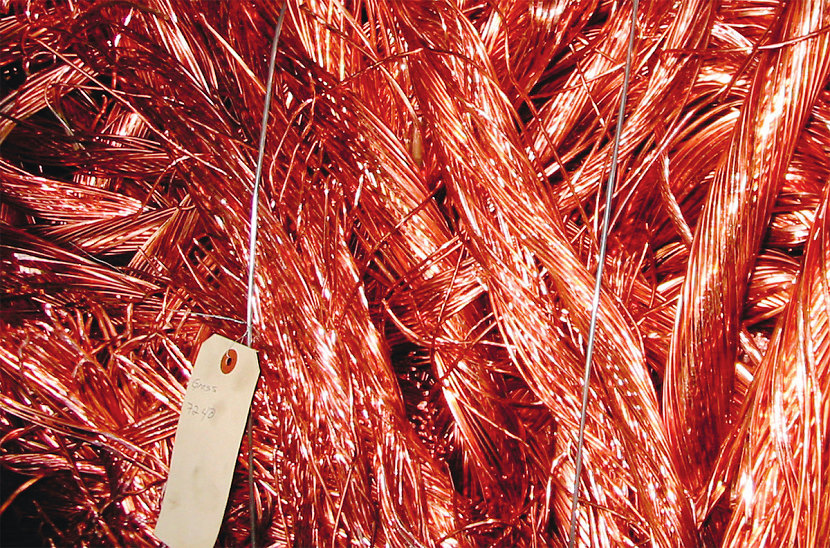
Во-вторых, медь весьма дружественна к контртелу. Являясь более мягкой, чем сталь или чугун, она помогает процессу приработки колодки, оберегая диски от задиров.
Но как оказалось, это не главное! Ведущие ученые-трибологи И. В. Крагельский и А. В. Чичинадзе исследовали и описали так называемый эффект переноса, когда медь в условиях высоких скоростей и температур образует на трущихся поверхностях тончайшую пленку. Она как бы выравнивает и облагораживает эти поверхности и тем самым снижает износ пар трения.
Применительно к дисковым тормозам это означает следующее: медь способствует частичному восстановлению диска, уменьшает его разнотолщинность, стабилизирует коэффициент трения.
А что в ней плохого – в той же меди? Во-первых, свинец! С него-то и начались гонения на медь в тормозных колодках. Ведь во фрикционную смесь шла не собственно медь (химически чистый металл), а всевозможный цветной лом, латунь и бронза. В том числе и бронза свинцовистая. А свинец и живая природа несовместимы – вспомните хотя бы запрет на использование этилированного бензина.
Во-вторых, медь сама по себе является тяжелым металлом. Попадая с продуктами износа накладки в окружающую среду, она окисляется, образуя оксид меди CuO. А тот охотно вступает в реакцию со слабыми кислотами, в частности, с сернистой кислотой H2SO3.
Откуда в окружающей среде сернистая кислота? А про выбросы промышленных предприятий забыли, про сернистый газ SO2, например? Про кислотные дожди, систематически выпадающие то тут, то там? Вот и реагирует оксид меди с кислотой, образуя соли, в частности – медный купорос CuSO4•5H2O. А тот не только с вредителями садов и огородов борется, но и человека угробить способен. Шутка ли – смертельная доза медного купороса для взрослого человека составляет от 8 до 30 граммов.
Так и попала «колодочная» медь в немилость к экологам – и поделом ей. Солям тяжелых металлов с человеком не по пути…
Они заменили асбест и медь
Основа основ колодки – это фрикционная смесь, композиция, из которой «выпекается» фрикционная накладка. Именно композиция обеспечивает эксплуатационные свойства детали. Например, коэффициент трения должен оставаться стабильным с ростом температуры. За это отвечают определенные ингредиенты. Другие составляющие обеспечивают износостойкость. Третьи выполняют роль арматуры в полимерной основе (ее еще называют матрицей), четвертые борются с шумом, пятые отводят тепло – список это можно продолжить.
Мы уже писали, что самая «простая» рецептура фрикционной смеси насчитывает 10, 15 и более ингредиентов, каждый из которых решает собственную задачу. И над их комбинациями день и ночь ломают головы лучшие научно-исследовательские подразделения компаний, выпускающих тормозные изделия.
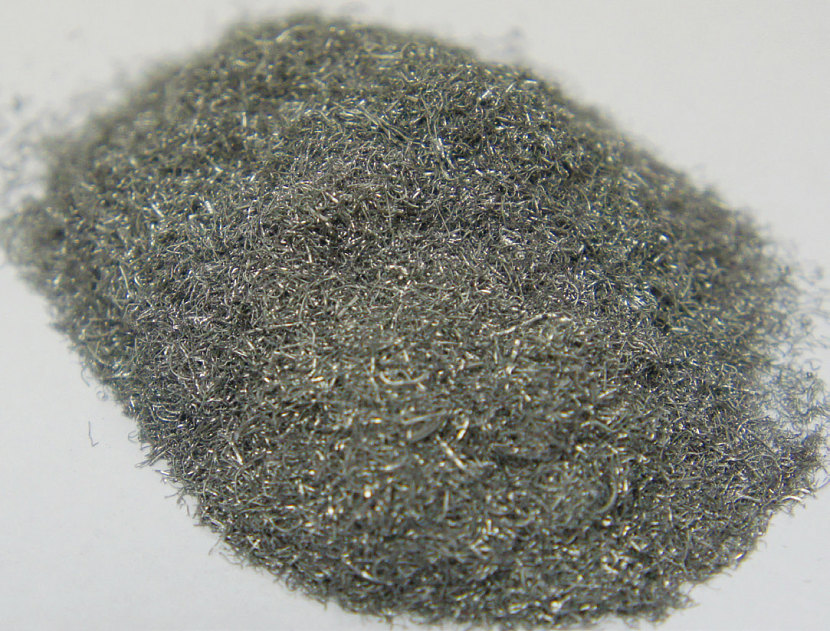
Производители колодок сегодня применяют три вида фрикционных материалов:
• полуметаллические (Semi Metallic);
• с низким содержанием стали (Low Steel);
• неасбестовые органические NAO (Non-Asbestos Organic).
Здесь важно знать следующее. Безасбестовыми являются все три группы. Термин Non-Asbestos в аббревиатуре NAO – это прием, призванный подчеркнуть экологичность рецептуры. А теперь – подробнее.
Semi Metallic
Первые безасбестовые колодки появились в Европе еще до запрета асбеста. Это легко объяснимо: залежи асбеста далеко, его надо импортировать, а это немалые расходы. Ну прямо по русской пословице «За морем телушка – полушка, да дорог перевоз». Поэтому европейские фирмы напряглись и создали Semi Metallic – полуметаллические фрикционные композиции.
Почему «полуметаллические»? Никакого секрета: в них примерно половину объема фрикционной смеси (а точнее, от 40 до 65%) составляют стальные волокна. Но это не просто стружка! Получают волокна так: берут стальную проволоку и на специальном станке счесывают тончайшие полоски. Затем рубят их и вводят в композицию.
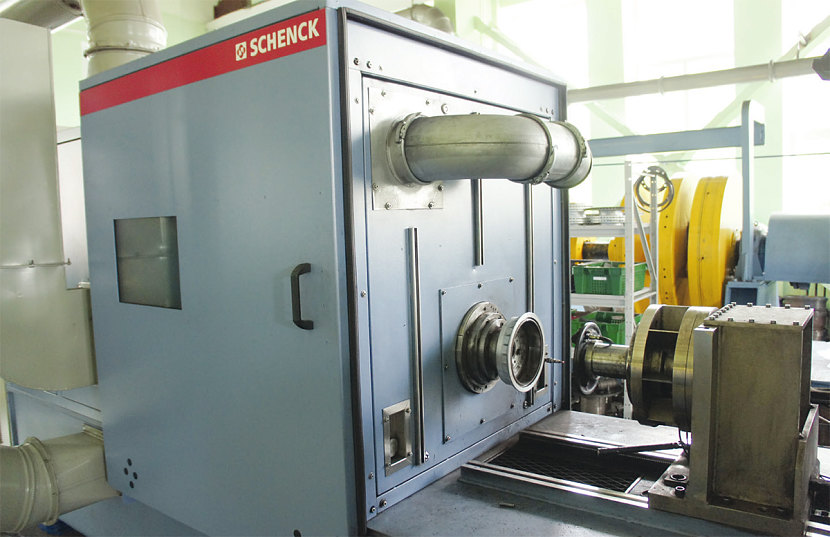
Чем привлекательны Semi Metallic? Они термостойкие, с хорошо армированной матрицей. Обеспечивают требуемые эксплуатационные характеристики, прекрасно отводят тепло.
А плохи они шумностью при высоких скоростях и агрессивностью к тормозному диску. Да и теплопроводность выходит боком: при нагреве до 500–700° C возможно закипание тормозной жидкости. Все же теплопроводность должна быть оптимальной, а не просто «низкой» или «высокой».
В СССР полуметаллические рецептуры не применялись. И не потому, что наши специалисты могли их освоить – просто стальное волокно было стратегическим сырьем и в автомобильную отрасль не поставлялось.
Но нет худа без добра: в поисках заменителя наши разработчики создали композиции из других волокон – базальтовых, углеродных и полиарамидных. И тем самым опередили время. Сегодня это пригодилось.
Low Steel
Со временем на Западе стали отказываться от полуметаллических рецептур в пользу Low Steel – малометаллических композиций. Они тоже содержали стальные волокна, но в меньших количествах – от 20 до 30%.
Разумеется, рецептура усложнилась. Задачи эффективности торможения, стабильности коэффициента трения, восстанавливаемости и т. д. теперь решали другие ингредиенты, – в частности, хитрые комбинации минеральных волокон. У каждой фирмы они были свои, хранимые как зеница ока.
В результате уменьшилась шумность, повысился ресурс тормозных дисков, стабилизировался отвод тепла, снизилось металлическое пыление колодок, улучшилась восстанавливаемость после нагрева, термомеханическая стойкость и другие качества.
NAO-материалы
Но самые интересные и перспективные композиции – это Non-asbestos Organics, те самые NAO. Главное отличие этих материалов в следующем: в них нет стального волокна. Вообще нет. Задачи, возложенные на него в рецептурах Semi Metallic и Low Steel, решают другие ингредиенты – керамика и комбинации альтернативных волокон. Тоже, разумеется, засекреченные.
Как они появились на свет, эти NAO? Их родина Азия, а точнее, Япония. Причем Япония, нацеленная на североамериканский рынок, – недаром она поставляет туда огромные партии автомобилей.
А в США действуют строгие нормы на «черную пыль». Поэтому рецептуры Semi Metallic и Low Steel там хоть и применяют, но не жалуют – они пылят оксидами железа, образуя характерный черный налет на суппорте и колесе. А вот NAO ведут себя безупречно – никакой «черной пыли» от них нет.
Поэтому, скажем, для европейского Ford стальная шерсть в тормозных колодках допустима, а для американского Ford – нежелательна. Соответственно и колодки для него в Старом и Новом Свете должны быть разными. Для Европы – Semi Metallic или Low Steel; для Америки – NAO.
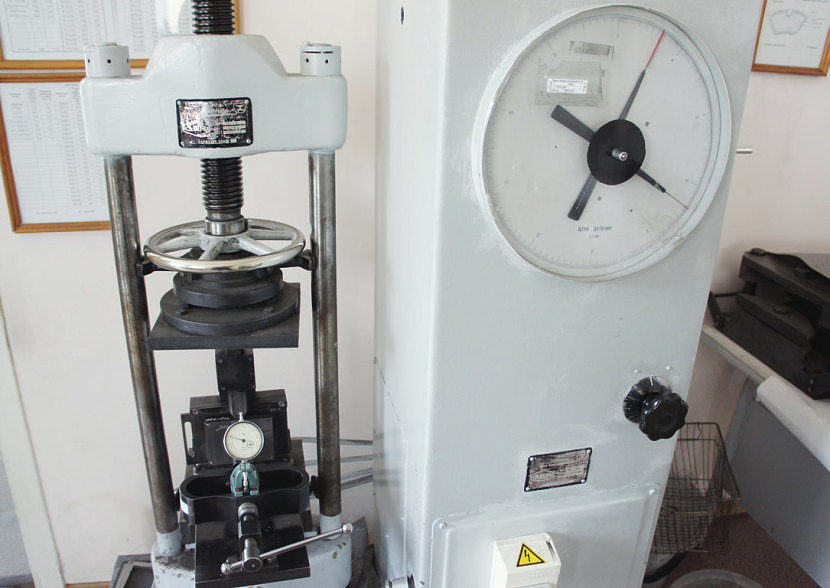
А нельзя ли поставлять колодки NAO в Европу? Нельзя, и вот почему. Американцы во главу угла ставят комфортность и чистоту, а европейцы – эффективность. Вспомните: в Германии скорость на автобанах не ограничена. Значит, нужны соответствующие тормоза. А комфортные NAO проигрывают по эффективности композициям Semi Metallic и Low Steel.
Но так будет не всегда. Специалисты прочат колодкам из NAO-композиций большое будущее. Ведь они обладают более стабильными и прогнозируемыми характеристиками, чем их «железные» собратья. Кроме того, они обеспечивают постоянное ощущение педали, бережное отношение к диску, меньшую склонность к шуму и вибрации. А про отсутствие оксидов железа в продуктах износа NAO-композиций мы уже говорили.
О шуме при торможении
Ученые-трибологи говорят, что трение в тормозном узле – это чередование прихватывания трущихся поверхностей и проскальзывания. Поскольку это процесс циклический, неизбежно возникновение колебаний. Колеблется колодка, колеблется контртело, а с ними и весь тормозной узел. А где колебания – там и звук.
В зависимости от частот звуковые волны могут оказаться в слышимом или неслышимом диапазоне. Причем мы слышим достаточно узкий спектр в виде писка или скрипа. Они-то и раздражают водителя, покушаясь на святое понятие «комфортный автомобиль». Ведь одним из ключевых требований к современному авто наряду с безопасностью и экологичностью является комфорт.
А если звука нет вообще, изначально? Хорошо это или плохо? Не спешите отвечать «хорошо» – здесь кроется коварный подводный камень.
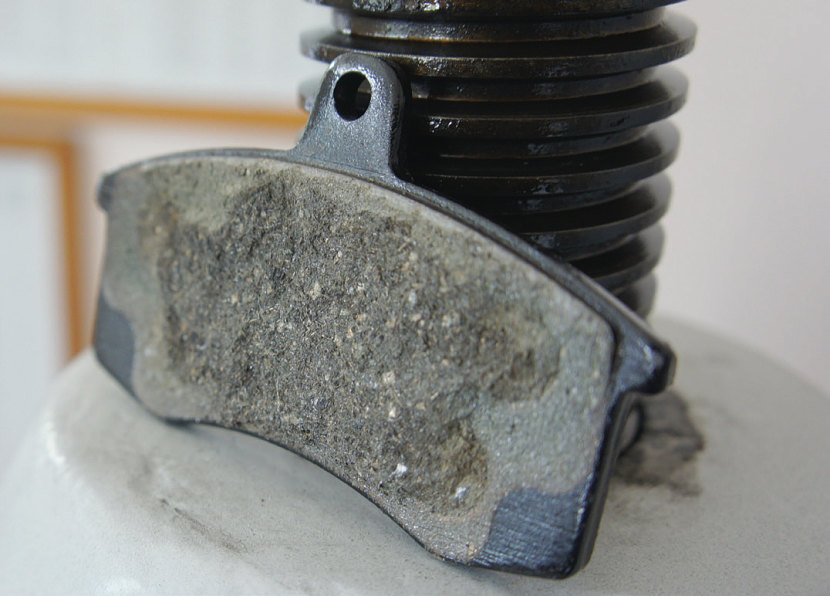
Дело в том, что в паре «колодка – диск» никаких звуков не издают только антифрикционные материалы. А у них, как мы уже знаем, коэффициент трения менее 0,2. В то время как у колодки для усредненного легкового автомобиля он лежит в диапазоне 0,35–0,45.
Понятно, почему антифрикционные материалы «молчат» – у них нет того самого циклического «прихватывания-проскальзывания», описанного учеными-трибологами. Соответственно, нет и генерации колебаний.
Так что, прикажете бесшумно рассекать на антифрикционных поделках и не вылезать из травмопунктов и больниц (это в лучшем случае)? Или ставить скрипящие колодки и, заткнув уши, ездить безопасно?
Как совместить несовместимое – колебания и тишину? Эту противоречивую задачу и решают, борясь с шумом при торможении. Звук неизбежен? Да, неизбежен. А человек слышит весь диапазон звуковых колебаний? Нет, не весь. Так сдвигайте диапазон в зону, недоступную человеческому уху, и тормозите бесшумно!
Конструкторы изучают собственные колебания элементов тормозной системы на специальном оборудовании. У каждого элемента есть собственная частота, зависящая от геометрической формы, материала, массы и других факторов.
А задача производителя фрикционных изделий – сдвиг собственной резонансной частоты колодки при ее взаимодействии с тормозным диском. Его называют сдвигом магнитуды.
Задача не из простых: где масса колодки и где – здоровенного чугунного диска! А тут еще суппорт и другие детали тормозной системы.
И все же сделать можно многое. Например, «играя» рецептурой фрикционной смеси, изменяя ее негомогенность (неоднородность) или вводя специальные ингредиенты.
Можно изменить коэффициент взаимного перекрытия накладки и диска. На практике это означает оптимизацию конфигурации накладки. На ней могут выполняться скосы, фигурные закругления по периметру (так называемые «бабочки») и другие геометрические решения. Дело это эмпирическое, кропотливое, но реально работающее.
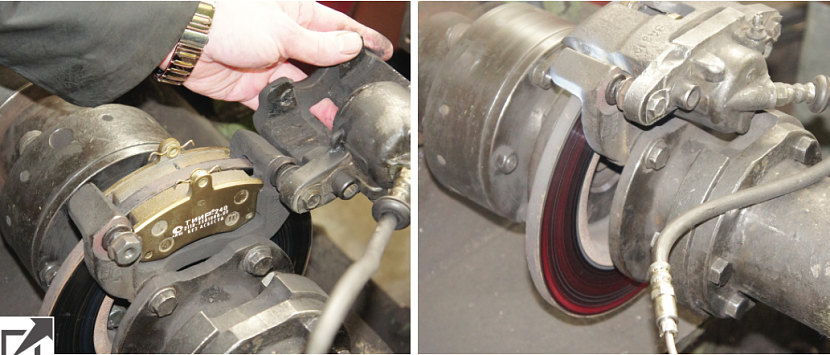
Радикально изменяют магнитуду пазы в теле накладки – особенно несимметричные, смещающие центр тяжести колодки. Их еще именуют пропилами.
Еще один способ уменьшения шума – это демпфирование. Заключается он в следующем: на поверхности колодки, не контактирующие с диском, наносятся полужидкие или твердые полимерные мастики. Они помогают колодке не входить в резонанс с поршнем, скобой и другими элементами тормозного узла.
Другая технология демпфирования – это особые пластины, закрепляемые на каркасе. Их так и называют – противошумные. Они могут приклеиваться, приклепываться или ставиться на защелки. Строго говоря, это не просто пластины, а довольно сложные изделия. Чаще всего их выполняют из металла и покрывают с двух сторон полимерной композицией.
Итак, резюмируем. В арсенале производителя колодок есть следующие средства борьбы с шумом при торможении:
• изменение рецептуры фрикционной смеси;
• оптимизация геометрия накладки, включая скосы и закругления;
• пазы в теле накладки, смещающие центр тяжести;
• демпфирующее полимерное покрытие;
• установка противошумных пластин.
О сжимаемости
А теперь – об интереснейшей и относительно новой теме в тормозном деле. Одно из ключевых направлений в работе над современными фрикционными накладками – это исследования и регламентирование сжимаемости тормозных накладок.
Вряд ли термин «сжимаемость» широко известен водителям. Да и большинству мастеров сервиса тоже. Но это не отменяет его важности. От того, насколько податлива фрикционная накладка, зависит пауза от момента нажатия на педаль до возникновения необходимого тормозного усилия. Мягкая накладка может недопустимо затянуть эту паузу, слишком жесткая – вызовет нежелательные писки и скрипы при торможении. Нужен оптимум.
Зная сжимаемость фрикционного материала, можно прогнозировать скорость срабатывания тормозного механизма. Получается этакий технологический «рычаг» для управления эксплуатационными характеристиками колодки. Так вот, производители колодок оптимизируют показатель сжимаемости, обеспечивая плавный ход педали тормоза, снижение вибрации, отсутствие «писка» при торможении и т. д.
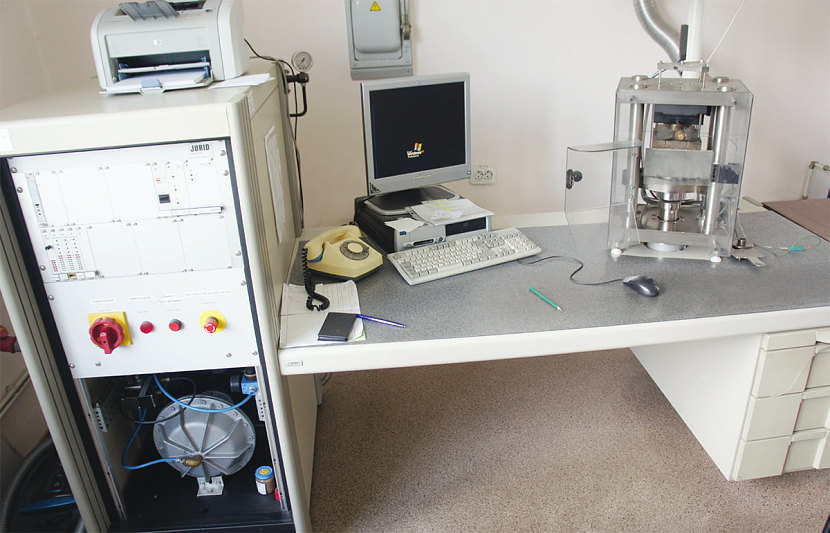
Но это еще не все. Управление сжимаемостью сокращает сроки и стоимость разработки новых видов продукции. А в итоге – повышает конкурентоспособность колодок. Кроме того, определение сжимаемости на разных стадиях изготовления накладки позволяет отследить:
• стабильность каждого звена технологической цепочки;
• правильность техпроцесса в целом.
Это подтверждено опытом ведущих производителей фрикционных изделий. Для испытаний на сжимаемость применяется современное оборудование – например, стенд JURID. Изготовитель – немецкая фирма Honeywell Bremsbealing GmbH.
О термоударе
Приведем еще один интересный пример современных технологий. Новая, только что «испеченная» колодка тормозит не так уверенно, как обкатанная. Фрикционное изделие должно приработаться. В чем суть приработки в суппорте автомобиля? Накладка при трении о тормозной диск сильно нагревается, в результате чего происходит термическая стабилизация рабочего слоя фрикционного материала. И лишь после «термообработки» торможение становится эффективным.
А можно ли обойтись без приработки колодок? Все же дело это небезопасное. Можно, если применить термоудар – высокотемпературную обработку рабочей поверхности накладки на специальном оборудовании. Что значит высокотемпературную? Никакого секрета: 500–600° С. Зарубежные производители называют эту операцию «скорчинг».
При термоударе наружный слой фрикционной накладки видоизменяется и сразу получает высокие эксплуатационные характеристики. Это позволяет после замены колодок эксплуатировать автомобиль в обычном режиме. Кроме того, термоудар повышает комфортность автомобиля за счет увеличения сжимаемости накладок, а также прививает автомобилю иммунитет от «утренней болезни» тормозов.
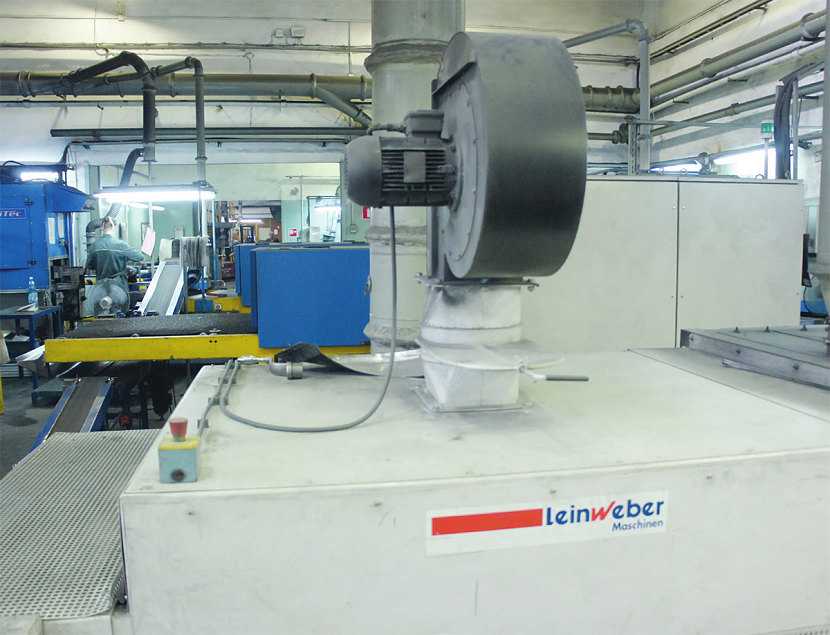
Любопытно, что в нашей стране термоудар применяли еще в 70-х годах прошлого века. Правда, лишь для колодок правительственного лимузина ЗИЛ‑4105. Эти были колодки марки «ТИИР». А не так давно для выполнения операции термоудара этот производитель приобрел оборудование фирмы Leinweber Maschinen GmbH (Австрия).
Эпилог
Есть горячие головы, твердящие, что тормоза придумали трусы. Что сказать на это? Только одно – что некоторые афоризмы придумали… не вполне адекватные люди. А тормоза изобрели другие – смелые и талантливые. И ведущие производители фрикционных изделий сегодня продолжают их дело.
Иллюстрации из книги Ю. И. Буцкого «ТИИР. Очерки новейшей истории. Технологии. Инновации. Экология». М.: Аудитория, 2017