Расчетная стоимость ремонта автомобиля Toyota Hilux за 276 948,65 руб., а трудоемкость ремонта равна 1,8 нормо-часа. Часть 2
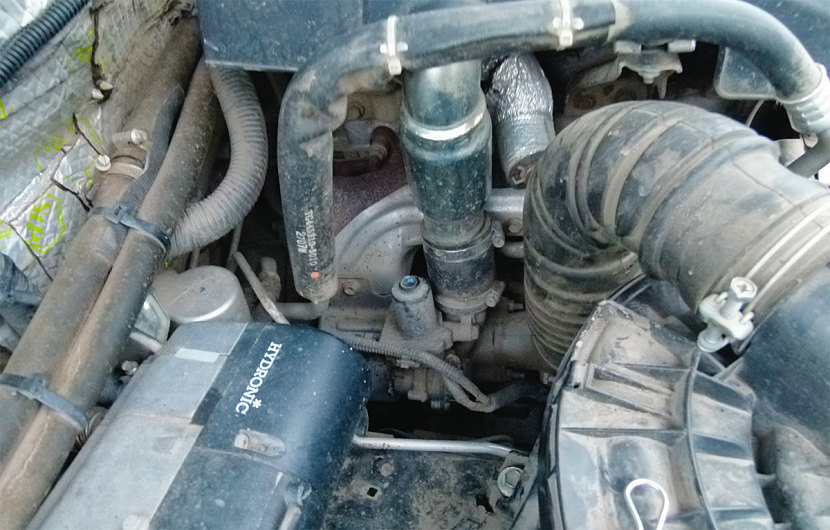
Результаты объективного контроля параметров свидетельствуют о том, что турбокомпрессор обеспечивает необходимое давление наддува и система управления, в том числе и направляющий аппарат турбокомпрессора, обеспечивают заданное давление наддува, ограничивая его рост при нажатии водителем педали акселератора и росте частоты вращения коленчатого вала. Отказы и сбои в работе турбокомпрессора и системы управления, отказы и сбои в работе двигателя в ходе испытаний не возникали. На комбинации приборов световые индикаторы неисправности систем автомобиля не включались (фото 13).
По субъективной оценке звук работы турбокомпрессора по своей громкости не выделяется на фоне общего шума работы двигателя и звуков, возникающих при движении автомобиля. Также была проведена проверка звука работы турбокомпрессора из салона автомобиля с места водителя с закрытыми дверями и окнами, с открытым окном передней левой двери, с открытой передней левой дверью, при открытом капоте. При всех условиях по субъективной оценке звук работы турбокомпрессора не выделяется по громкости из общего шума работы двигателя.
Внутренний шум в автомобиле нормируется ГОСТ Р 51616–2000. В соответствии с п. 1 данный стандарт не распространяется на автотранспортные средства, находящиеся в эксплуатации. Исследуемый автомобиль относится к этой категории транспортных средств, поэтому контроль уровня шума в салоне автомобиля не имеет технического смысла. Другие нормативы на внутренний шум в салоне автомобиля или шум в моторном отсеке транспортного средства отсутствуют. Есть действующий ГОСТ Р 52231–2004, действие которого распространяется на транспортные средства, находящиеся в эксплуатации. В соответствии с этим стандартом микрофон измерительного прибора располагается на расстоянии 0,5 м от среза выпускной трубы и проверяется уровень шума системы выпуска отработавших газов, а не системы впуска. Таким образом, нормы на внутренний шум автомобиля TOYOTA HILUX идентификационный номер отсутствуют.
ГОСТ Р 53637–2009 устанавливает требования к турбокомпрессорам. В ГОСТе предусмотрены требования к:
– основным и габаритным размерам;
– динамической балансировке ротора;
– надежности крепления на двигателе, герметичности стыков от протечек газа, масла, воды и воздуха;
– производительности и степени повышения давления;
– температуре газов перед турбиной;
– пропускной способности турбины;
– ресурсу;
– безотказности, ремонтопригодности и сохраняемости;
– требованиям технической эстетики.
Требования к звуку (шуму) при работе турбокомпрессора не нормируются, и при испытании турбокомпрессора шум не контролируется.
При определении наличия или отсутствия дефектов и неисправностей технические регламенты, ГОСТ 15467–79, ГОСТ Р 27.002–859, ГОСТ Р51709–2001 предписывают определять соответствие или несоответствие параметра установленным требованиям нормативных документов, требованиям нормативно-технической документации. Так как установленные требования к звуку работы турбокомпрессора отсутствуют, то по данному параметру турбокомпрессор не может быть признан дефектным или неисправным.
Работоспособность автотранспортного средства и его составных частей определяется по способности выполнять заданные функции соответствию требованиям нормативных документов. Как показали проведенные испытания и объективный контроль параметров работы, турбокомпрессор исследуемого автомобиля выполняет заданные функции – обеспечивает повышение давления воздуха в системе впуска, обеспечивает регулирование давления наддува в заданных пределах. Таким образом, турбокомпрессор находится в работоспособном состоянии.
Для дальнейшего исследования персоналом технического центра турбокомпрессор и детали системы впуска были демонтированы, а турбокомпрессор был частично разобран и исследован экспертом. В ходе этого этапа исследования было установлено следующее (фото 14).
Детали системы впуска до проведения разборочных работ были установлены на своих штатных местах и плотно соединены штатным образом (фото 15, 16). Неплотности в стенках самих деталей и в местах их соединения отсутствовали. Турбокомпрессор был установлен штатным образом. На внутренних поверхностях деталей системы впуска после места соединения со шлангом системы вентиляции картера имеются наслоения маслянистой жидкости, что является естественным процессом вентиляции картерного пространства двигателя и невозможностью абсолютно полного удаления масла из газов, отводимых из картерного пространства.
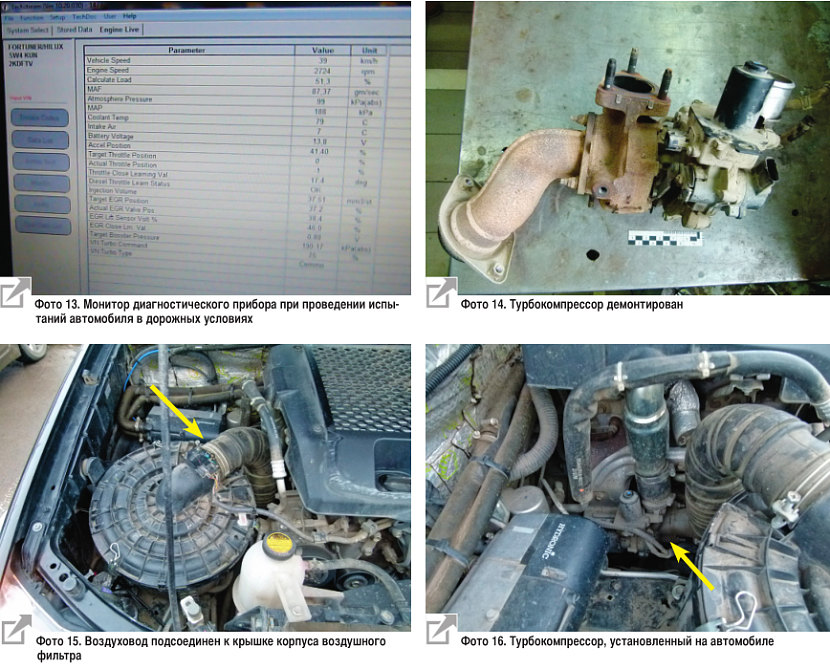
Во внутренней полости интеркулера (радиатора охлаждения воздуха на впуске) присутствует небольшое количество масла, что также является естественным для двигателей с турбонаддувом. Также масляная пленка покрывает внутреннюю поверхность корпуса дроссельной заслонки и саму заслонку. Объемные скопления масла в системе впуска отсутствуют. Посторонние предметы во внутренних полостях деталей системы впуска отсутствуют.
Фильтрующий элемент воздушного фильтра имеет маркировку производителя «TOYOTA 17801–00020 SMITHS10/13D» и маркировку материала каркаса PUR – полиуретан.
На корпусе турбокомпрессора имеется заводская маркировка производителя, выполненная выпуклыми рельефными символами, «285 IHI Turbo». На маркировочной площадке нанесено игольчатым маркиратором «IHI VB31 110426013Y17201–0L070» (фото 17). Из маркировки следует, что производителем турбокомпрессора является Ishikawajima Harima Heary Industries Co., Ltd (Япония) выпускающий оригинальные компоненты для автомобилей TOYOTA.
На корпусе подшипникового узла, турбинной и компрессорной части отсутствуют признаки разрушения и деформации. Турбинное колесо имеет девять лопастей (лопаток). Турбинное колесо и внутренняя поверхность турбинной части корпуса покрыты тонким слоем сухого нагара черного цвета (фото 18). Масло в жидком виде на поверхностях турбинной части компрессора отсутствует. Кромки лопаток турбинного колеса не касаются корпуса (фото 19).
Система изменения положения направляющих лопаток турбинной части компрессора находится в нормальном эксплуатационном состоянии. Лопатки направляющего аппарата легко, без заеданий изменяют свое положение под действием приложенной нагрузки (фото 20).

Компрессорное колесо имеет шесть больших и шесть малых лопаток (фото 21). Компрессорное колесо прочно закреплено на валу ротора резьбовым соединением. Одна большая лопатка в передней угловой части деформирована с изгибом на участке длиной 7 мм при общей длине лопатки 12,5 мм (фото 22, 22.1, 22.2). Радиус закругления в зоне деформации лопатки определялся специальными шаблонами, и он составляет от 4 до 5 мм. Кромки лопаток не касаются корпуса. На корпусе сохранился технологический рельеф, сформированный в результате операции точения при производстве. На корпусе компрессорной части имеется заводская маркировка.
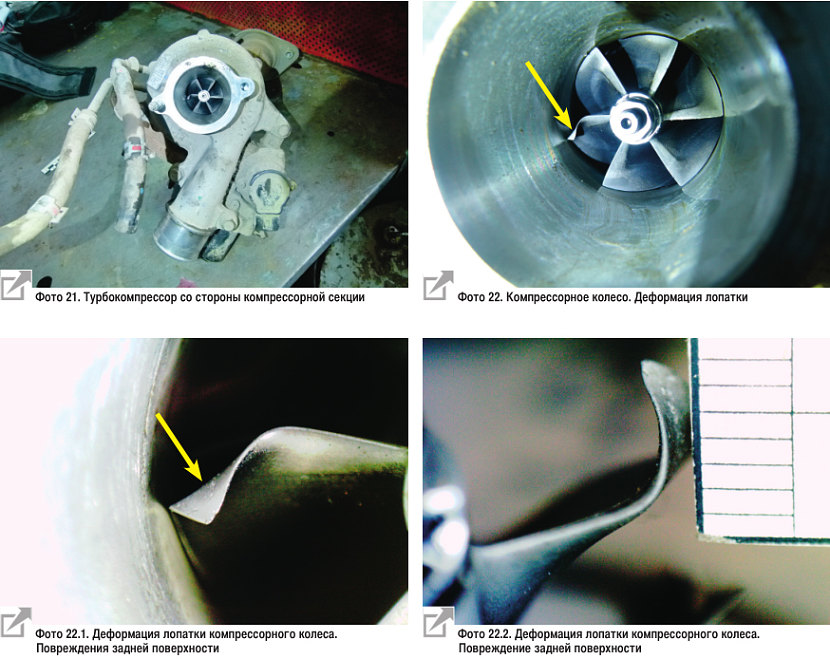
Ротор турбокомпрессора свободно вращается в подшипниковом узле. Повышенный радиальный зазор в подшипниках отсутствует. Контроль радиального зазора между кромками лопаток и корпусом турбокомпрессора проводился с помощью наборов плоских щупов. При проведении контроля к компрессорному и турбинному колесу прикладывалось радиальное усилие для того, чтобы зазор был полностью выбран в одну, а затем в противоположную сторону. У турбинного колеса зазор между кромками лопаток и корпусом составляет 0,07…0,10 мм, а у компрессорного колеса 0,07…0,15 мм. Такие величины зазоров являются нормальными для турбокомпрессоров, находящихся в эксплуатации и сохранивших свою работоспособность. Падение КПД турбокомпрессора начинается при величине зазоров около 0,3…0,5 мм.
Исследование деформированной лопатки компрессорного колеса и внутренней поверхности корпуса компрессорной секции с помощью оптического и цифрового микроскопов показало следующее.
На выпуклой ее поверхности деформированной лопасти, т. е. на том участке, на котором действовала деформирующая нагрузка, имеются множественные точечные и линейной формы вмятины с вытеснением металла (алюминиевого сплава) из зоны внедрения следообразующего объекта (объектов) в материал лопатки. Вмятины разнонаправленные, о чем свидетельствует разное направление внедрения объектов и направление вытеснения алюминиевого сплава (фото 23, 23.1). Размер вмятин менее 1 мм.
На передней кромке еще одной лопатки имеются три вдавленных следа в виде вмятин размером менее 1 мм с вытеснением алюминиевого сплава (фото 24, 24.1).
На поверхности корпуса компрессорной секции перед плоскостью вращения лопаток имеются множественные разнонаправленные мелкие по глубине царапины (фото 25). В плоскости вращения лопаток компрессорного колеса такие царапины отсутствуют.
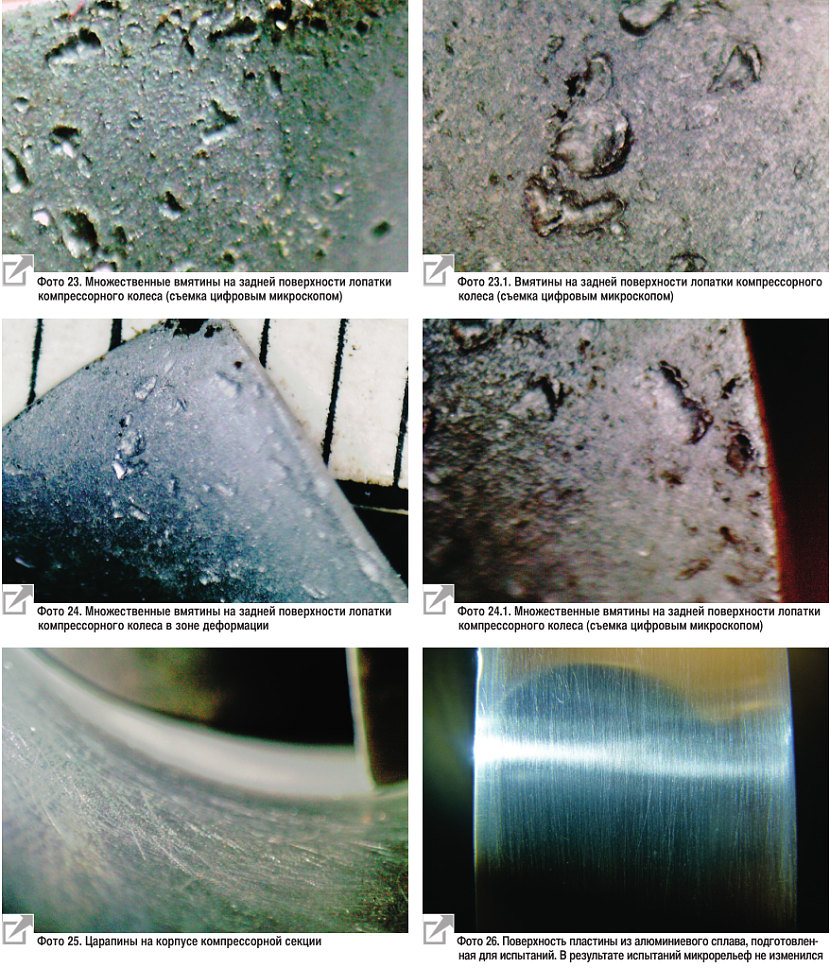
В материалах дела сформулирована версия, что деформация лопатки компрессорного колеса образовалась в результате попадания в область ее вращения кусочка льда из системы вентиляции картера.
Образование вмятин на поверхности следовоспринимающего объекта возможно в случае воздействия на него следообразующего объекта, обладающего большей твердостью. Твердость объекта – свойство сопротивляться внедрению другого объекта. Компрессорное колесо изготовлено из алюминиевого сплава. Для изготовления компрессорных колес используются алюминиевые сплавы – силумины различного химического состава и обладающие различными физико-механическими свойствами. Временное сопротивление алюминиевых сплавов компрессорных колес турбокомпрессоров лежит в диапазоне от 260 до 420 Н/мм2 (около 26,5…42,9 кгс/мм2). Такие колеса при вращении выдерживают скорость до 700 м/с. Твердость алюминиевых сплавов по шкале Бринелля лежит в диапазоне от 50 до 90 НВ. Для льда определение твердости по Бринеллю не проводится. Твердость льда по шкале Мооса, используемой для оценки твердости минералов, составляет около 1,5. Такая твердость по шкале Мооса соответствует шкале твердости по Бринеллю примерно 10 НВ. То есть твердость льда существенно ниже твердости алюминиевого сплава.
Для опытной проверки версии о возможности образования вмятин на поверхности лопатки компрессорного колеса турбокомпрессора был использован пищевой монолитный лед без видимых газовых включений из пластиковой упаковки, хранившейся в морозильной камере при температуре –14,9° С. При исследовании использовалась лопатка, не имеющая повреждений и сохранившая исходный технологический рельеф, характерный для деталей, изготовленных методом литья. Кусок льда располагался на поверхности лопатки компрессорного колеса, и к нему прикладывалось усилие с постепенным его увеличением до момента разрушения льда. В результате исследования установлено, что силовое воздействие льда на плоскость лопатки компрессорного колеса, максимально возможное по условиям прочности льда, не образует на поверхности лопатки следы в виде вмятин, царапин и иные следы. Исходный микрорельеф поверхности лопатки полностью сохранился.
Для дополнительного определения возможного образования следов при силовом воздействии льда на поверхность детали, изготовленной из алюминиевого сплава, было проведено исследование на образце. Этот этап исследования проводился в лабораторных условиях МАДИ. Испытуемый образец представлял собой пластину из алюминиевого сплава толщиной 4 мм и габаритными размерами 45 × 90 мм (фото 26). Поверхность пластины была отшлифована абразивом с зернистостью Р1000 для получения ровной шлифованной поверхности без каких-либо вмятин и глубоких царапин. При плоском шлифовании было обеспечено продольное направление рисок прямолинейной формы. Риски с другим направлением на поверхности отсутствовали. На такой специально подготовленной поверхности легко определить вмятины и царапины в результате воздействия следообразующего объекта, которые могут появиться при испытании.
Пластина была помещена в морозильную камеру и выдерживалась в течение часа при температуре –10,7° С для исключения плавления льда во время испытаний. Монолитный лед помещался на поверхность охлажденной пластины, и к нему прикладывалась сила, величина которой приводила к разрушению льда. Куски льда имели размер в поперечнике от 5 до 20 мм. Было проведено восемь опытов с различными по размеру кусками льда. Во всех опытах поверхность образца полностью сохранила микрорельеф, сформированный при шлифовании. Вмятины и царапины на поверхности образца не возникли.
Проведенные исследования позволяют сделать вывод о том, что точечные и линейные разнонаправленные глубокие вмятины с вытеснением алюминиевого сплава не могли образоваться в результате контакта с фрагментом льда. Они образовались в результате силового контакта с твердым предметом или предметами, имеющими острые вершины и плоскую контактную поверхность, оставившую вдавленные следы линейной формы с вытеснением алюминиевого сплава из области внедрения.