Школа Федора Рязанова. Урок 21. Оборудование дизельного диагностического поста. Продолжение
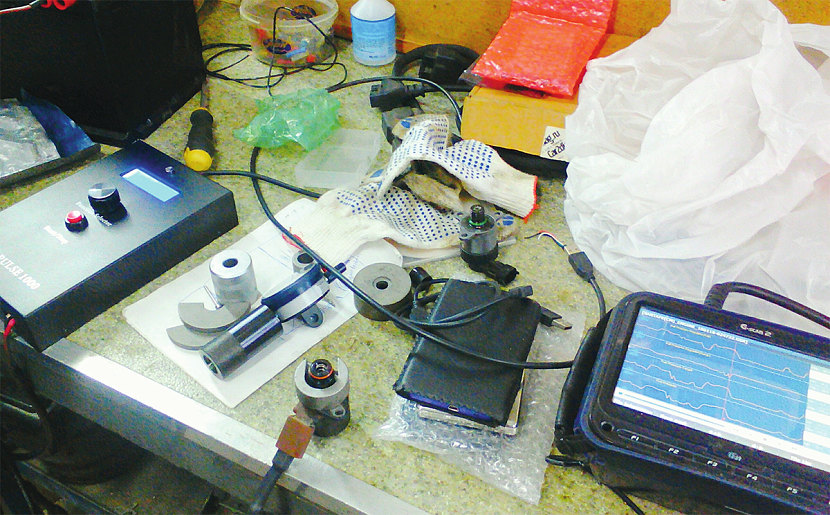
Поговорим о проверке регуляторов давления (потока)
В предыдущих уроках мы упоминали эти элементы систем Common Rail. Информация, даваемая по ним мануалами и различными публикациями в интернете, достаточно скудна, а порой и вовсе противоречива. Да и в наших с вами прошлых уроках вопрос их работы и проверки был рассмотрен только поверхностно. Пришло время уделить этим узлам более пристальное внимание. Часть информации, изложенной в этой статье, будет немного повторять ту, которая была рассмотрена на предыдущих уроках. Для чего это делается? Во-первых, повторение – мать учения. Во-вторых, законы психологии говорят, что с первого раза запоминается только ограниченный процент предлагаемой информации. Так что первый пункт народная мудрость придумала не зря. Но основное – с этого урока мы немного начнем приближаться к изучению электронных приборов и устройств, необходимых на посту диагностики современных дизельных систем. Напомню – человеческий глаз не в состоянии увидеть, как распыляется топливо, какие волны возникают в топливных трактах, как движутся различные подвижные детали в ТНВД, форсунках и прочих элементах дизельной аппаратуры. Времена, когда старый опытный дизелист на «слух и на нюх» определял неисправности в топливной аппаратуре тракторов ДТ‑75, КАМАЗов Euro 0 и допотопных «Икарусов», давно ушли в прошлое. Да, это была очень надежная и неприхотливая техника. Всевозможные дефекты были изучены «своими руками», и опыт помогал их находить и устранять прямо в «поле» – т.е. в самых различных, порой не очень приспособленных для этого условиях. Но вопросы ностальгии по ушедшим временам давайте оставим в прошлом, а сами вернемся к современным реалиям. С внедрением электронных систем управления добавилась еще одна проблема, связанная с человеческим глазом. Кроме потоков топлива в непрозрачных трубках и узлах, он еще не может видеть, как «бегут» электроны по электрическим цепям! И вот с этого момента на диагностическом посту, кроме привычных манометров, активно начали появляться различные электроизмерительные приборы. Начиная от простейших мультиметров (тестеров), заканчивая крупными компьютерными измерительными комплексами на основе осциллографа, плат сбора данных и других чудес современной цивилизации. На этом занятии мы начнем изучение этих приборов. Удобнее всего нам с вами будет изучить их применение на примере оборудования для простейшего исполнительного механизма (узла) системы Common Rail под названием «регулятор давления (потока)». Почему простейший? Ведь это достаточно сложный и высокотехнологичный узел. Все просто – импульсы управления этими клапанами (они носят название ШИМ) и соответственно приборы для их проверки являются самыми простыми из всех имеющихся на современном дизельном автомобиле. А начинать есть смысл с простого, и только потом переходить к более сложным способам управления. Но прежде чем перейти к этому изучению, давайте рассмотрим, что это такое и для чего они служат.
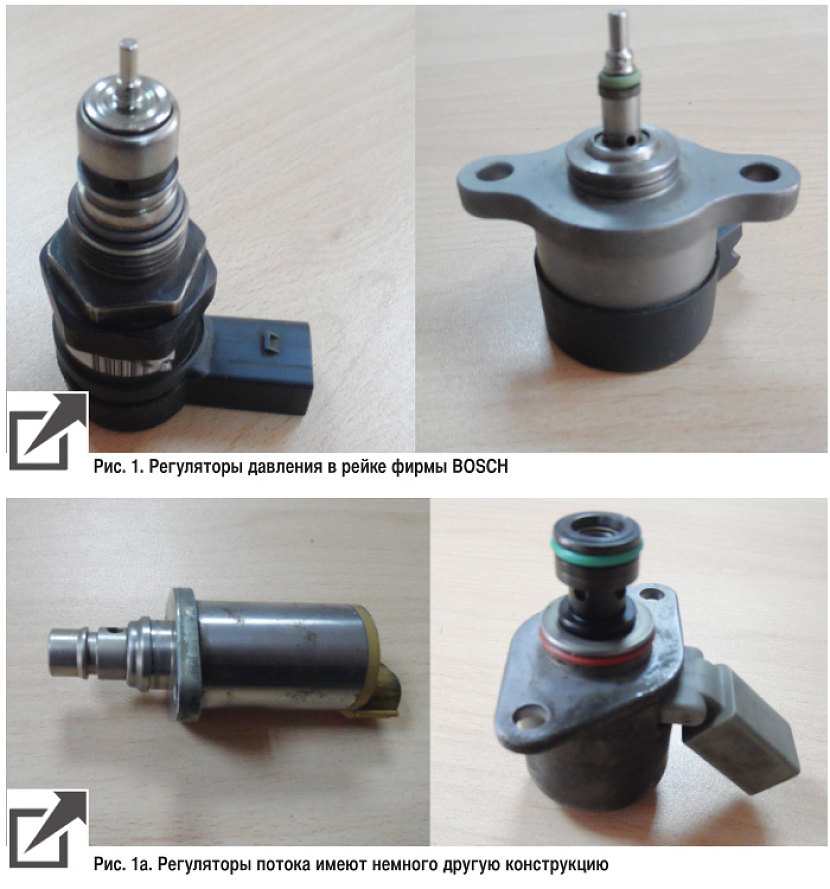
Для чего нужен регулятор давления в рейке?
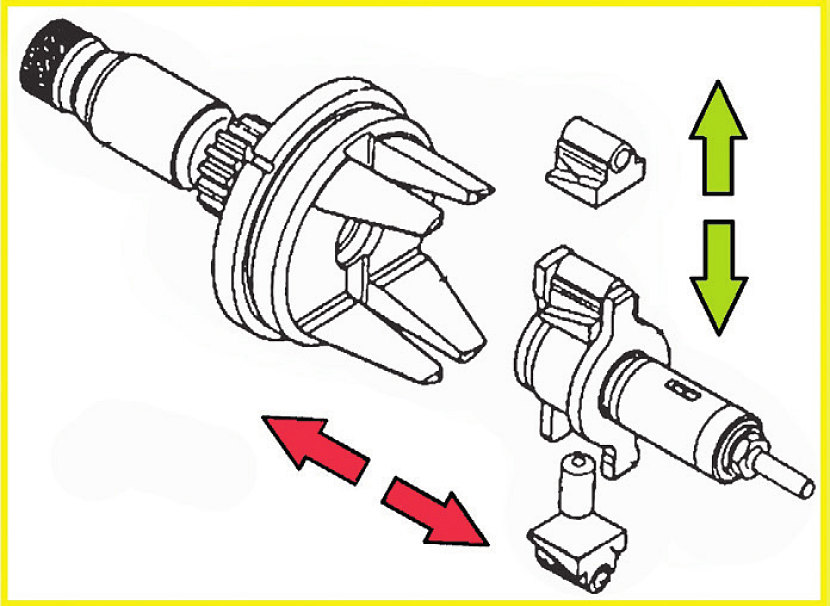
Вспомним еще раз. На первых системах Common Rail максимальное давление достигало всего лишь 1300 бар. Почему такое пренебрежительное «всего лишь»? Ведь на самом деле это очень большое давление! Все просто – внедрение норм Euro V (особенно на грузовиках) потребовало применения давления до 2400 бар! И автомобили, работающие на давлении 1300 бар, уже ушли в прошлое. Но разработчики этих систем столкнулись с одной проблемой. Даже при давлении 1300 бар требуемое время открытия форсунки на холостом ходу составляло менее 0,5 миллисекунды. А как мы с вами помним, максимальное время отклика форсунки, при котором возможна генерация кода, составляет 512 микросекунд. Фирме BOSCH (впрочем, как и другим лидерам в производстве элементов топливной аппаратуры) не удалось создать узлы, способные работать на таком малом времени открытия. И, скрепя сердце, конструкторам пришлось на холостом ходу снижать давление в рейке для обеспечения более длительного времени открытия форсунок. Это снижало качество распыла, но технологические возможности современных производителей просто вынудили их пойти на это не самое лучшее с точки зрения экологии решение. Оговоримся сразу – аналогичное техническое решение также применяется на моторах непосредственного впрыска бензина (за исключением моторов GDI фирмы Mitsubishi). Таким образом, необходимая цикловая подача на каждом режиме работы двигателя определяется двумя составляющими: давлением в рейке и временем открытия форсунки. Вот почему требования к регуляторам давления очень высоки – малейшие отклонения в его работе тут же приводят к отклонениям в реальном давлении топлива в рейке. Что, в свою очередь, ведет к неправильной цикловой подаче топлива. Нарушение экологии, повышенный расход топлива, жесткая работа двигателя, «плавающие» обороты и много других неприятных вещей становится просто неизбежным.
Для чего нужен регулятор потока в ТНВД?
Алгоритм поддержания давления в рейке прост: если ЭБУ определяет, что оно превышает требуемое, – дается команда регулятору давления открыться на большую величину и ставить излишек топлива в тракт обратного слива (на жаргоне, принятом у дизелистов, – «обратку»). Получается очень нелогичная вещь – ТНВД отбирает часть мощности у двигателя (помним, какую ошибку допустил Рудольф Дизель – он не учел эти потери), а потом просто тратит ее впустую! Другими словами, плунжер трудится «не покладая рук», «в поте лица своего» создавая высокое давление. А потом оказывается, что большая часть его трудов пропадает зря! Это непорядок, и с этим необходимо бороться. Единственное разумное решение – на малых цикловых подачах ограничить производительность насоса! Только сказать-то просто, а вот сделать – значительно сложнее. И на свет стали появляться различные конструктивные решения. Например, фирма LUCAS на своих ТНВД типа EPIC применила способ одновременной регулировки цикловой подачи и производительности насоса за счет изменения активного хода плунжера.
журнала "АБС-авто" № 10 (2019 г.)