Сказание о красках
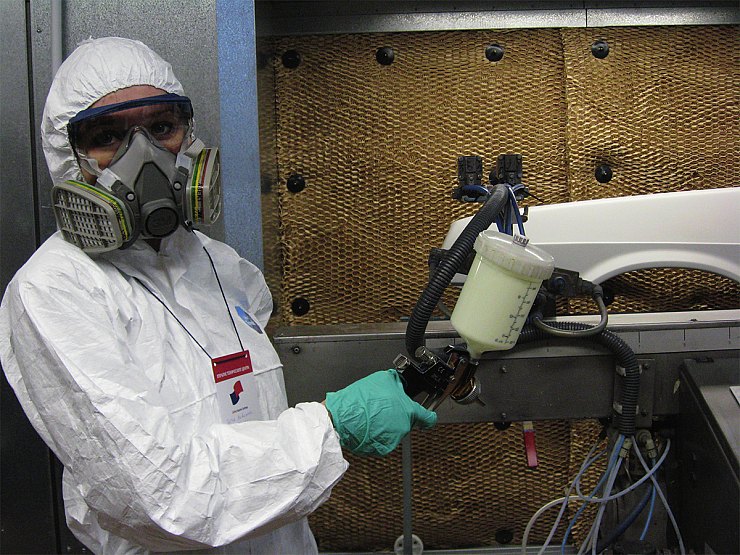
В том, что акриловые лакокрасочные материалы предпочтительнее, например, алкидных, никого убеждать не надо. Но почему, за счет чего? Давайте попробуем разобраться в этом, не вдаваясь в сложные физико-химические подробности. А заодно вспомним историю автомобильных эмалей – от «нитро» до современных на водной основе. Свой рассказ авторы попытались оживить вставками «Есть вопрос!». Жаль только, что вопросов много, а места в журнале мало...
Кузов на конвейере
Для начала посмотрим – какие операции предшествуют окраске автомобильного кузова на заводском конвейере?
Прежде всего кузов «в металле» тщательно обезжиривают, промывают и направляют на химическую обработку – фосфатирование. После этой операции на металлической поверхности образуется тончайшая пленка из фосфатов железа и цинка, назначение которой – защищать металл от коррозии при появлении микротрещин в слоях лакокрасочных материалов. Отметим, что фосфатная пленка обладает хорошей адгезией как к металлу, так и к грунтовке.
Попутно заметим, что сегодня для изготовления кузова или его деталей все чаще применяют предварительное цинкование или используют готовый оцинкованный лист. Но обезжиривание и фосфатирование обязательны и для них.
После фосфатирования кузов снова тщательно промывают, сушат, а затем на фосфатную пленку методом катодного или анодного осаждения наносят слой водоразбавляемой грунтовки с антикоррозионными добавками.
Если кузов служит катодом, сей процесс именуется катафорезом, в противном случае – анафорезом. Отметим, что катафорез обеспечивает более надежную коррозионную защиту сварных швов и скрытых полостей, поэтому он предпочтительнее анафореза.
Есть вопрос! Значит, анафорезная грунтовка уже не применяется?
Ответ. На некоторых заводах анафорезные установки еще работают, но они постепенно вытесняются катафорезными. К настоящему времени анафорезных ванн для окраски кузовов и кабин практически не осталось.
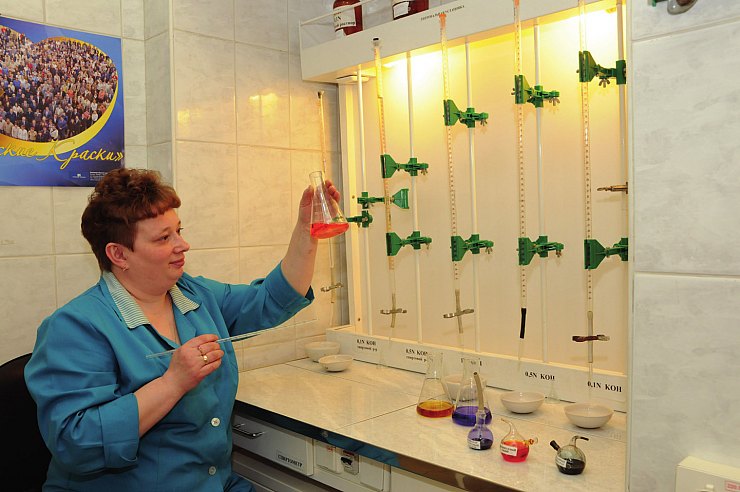
Толщина слоя катафорезной грунтовки достигает 20 мкм, а благодаря электроосаждению он распределяется равномерно как на горизонтальных, так и на вертикальных поверхностях, хорошо прокрашивая и скрытые полости.
После сушки при высокой температуре (180°С) на катафорезный слой накладывают еще одну грунтовку – выравнивающую. Ее назначение двояко: во-первых, заполнять и сглаживать мелкие дефекты поверхности, во-вторых – ограничивать развитие трещин, возникающих в лакокрасочном слое. К слову, в отличие от катафорезной, выравнивающая грунтовка от коррозии не защищает.
И наконец, после сушки и шлифования загрунтованная поверхность покрывается эмалью либо материалами двухслойной системы: базисная эмаль «металлик» плюс прозрачный лак.
Эмалями (зарубежное название Topcoat) окрашивают большинство грузовиков и автобусов и некоторую часть легковых автомобилей. С двухслойными системами ровно наоборот – ими покрывают большинство легковых кузовов и лишь малую часть грузовиков и автобусов.
Мы совершили этот краткий экскурс, чтобы напомнить: даже самые современные автоэмали не обеспечат качественную окраску кузова без тщательной подготовки – и конвейерные технологии иллюстрируют это как нельзя лучше. А теперь перейдем к главной теме нашего разговора – эмалям.
Растворители и разбавители
Растворитель и разбавитель – это не одно и то же, хотя и тот и другой применяются для получения требуемой вязкости ЛКМ.
Растворитель – понятие фундаментальное, он служит для получения истинного раствора, в котором молекулы растворенного вещества располагаются равномерно.
Разбавители, применяемые в лакокрасочной промышленности, строго говоря, не обязаны что-то растворять. Их задача – лишь понижать вязкость, не приводя к расслоению и коагуляции разбавляемого продукта. Поэтому разбавители могут быть и несовместимыми с разбавляемыми материалами. Иногда это свойство разбавителей оказывается полезным: нарушение «родственности» изменяет форму макромолекул ЛКМ, они как бы «поджимают лапки», что очень эффективно снижает вязкость продукта. Разумеется, такие разбавители не должны отрицательно влиять на процесс формирования пленки, и тут всю ответственность на себя принимает фирма, производящая разбавитель.
Несмотря на каталожное наименование «разбавитель», продукты марок 1301 и 1301М для «Vika-акрил» с физико-химической точки зрения являются все же растворителями.
Ацетон, являясь растворителем, непригоден для снижения вязкости ЛКМ – он слишком летуч и не обеспечивает оптимального высыхания пленки при испарении. В лакокрасочной промышленности он применяется в качестве компонента сложного растворителя (разбавителя).
Что такое эмаль?
С филологической точки зрения слово «эмаль» (от франц. email) – типичный омоним. Во-первых, так именуют стеклообразное покрытие, наносимое на металл (или, например, керамику) и закрепляемое обжигом. Такую эмаль изготовляют из легкоплавких цветных стекол с добавлением оксидов металлов и пигментов. За примерами далеко ходить не надо – эмалированые тазы и кастрюли есть в каждом доме.
Во-вторых, эмалью или эмалевой краской называют пигментированный ЛКМ на основе раствора пленкообразователей. Или ЛКМ, полученный диспергированием пигментов в лаках, – как вам больше нравится.
Как правило, эмалевая краска обладает высоким блеском (хотя встречаются и матовые эмали). С упомянутой стеклообразной эмалью ее связывает лишь некая схожесть внешнего вида и не более того.
Далее мы рассмотрим основные виды автомобильных эмалей.
Есть вопрос! А какая эмаль появилась раньше?
Ответ. Стеклообразная, поэтому во всех словарях и справочниках она упоминается в первую очередь. Но для автомобильных кузовов она не подходит – как по технологическим соображениям, так и из-за повышенной колкости покрытия. В дальнейшем под словом «эмаль» мы будем понимать ЛКМ.
Родная сестра пороха
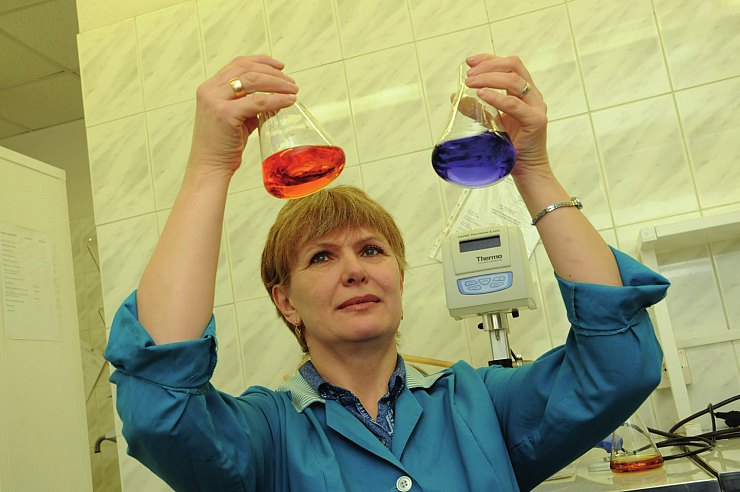
Не будем вдаваться в подробности окрашивания кузовов на заре автомобилестроения. Отметим лишь, что маляры использовали краски на основе природных смол, скипидара и олифы с добавками сажи и других пигментов. В 20-е годы на смену таким краскам пришла нитроэмаль.
Ее история такова: после окончания Первой мировой войны производственные мощности по выпуску пороха оказались незагруженными. Но химики мгновенно сообразили: позвольте, ведь пироксилин (тринитрат целлюлозы), применяемый в производстве пороха, и коллоксилин, идущий на изготовление нитролака, – близнецы-братья! И тот и другой являются сложными эфирами целлюлозы и азотной кислоты и различаются, в частности, содержанием азота.
Вот и получилось, что многие пороховые заводы занялись выпуском кинопленки, а также нитролаков и нитроэмалей на основе нитроцеллюлозы. А нитроэмали являют собой не что иное, как суспензии пигментов в нитролаках с добавками пластификаторов, в частности алкидных смол – без них покрытие получается слишком хрупким (что такое алкидные смолы, сказано ниже).
Кратко напомним некоторые свойства нитроэмалей. Низкое содержание нелетучих веществ в растворе коллоксилина определяет малую толшину пленки при высыхании, поэтому для получения качественного покрытия толщиной 75-125 мкм требуется наносить до десяти слоев эмали. Готовая пленка стойка к действию температур в диапазоне от -40 до +60°С. Если же нитроэмалевое покрытие нагреть до 100°С и более, пленка разрушится и даже может самовозгореться.
Для своего времени нитроэмали были, безусловно, хороши: они быстро высыхали при комнатной температуре и неплохо противостояли воздействию масел, бензина, солнечных лучей и атмосферных осадков. Правда, для сохранения высокого блеска они требовали частой полировки, но с этим приходилось мириться.
Есть вопрос! За счет чего происходит полимеризация нитроэмали
Ответ. Запомним раз и навсегда: никакой полимеризации в нитроэмалях не происходит! Отверждение, а точнее высыхание, осуществляется за счет испарения летучих растворителей – это чисто физический процесс. После высыхания образуется обратимая пленка, которая может быть снова растворена в растворителе.
Под маркой НЦ нитроэмали выпускаются и по сей день. В сегодняшних автомобильных делах они примененяются крайне редко.
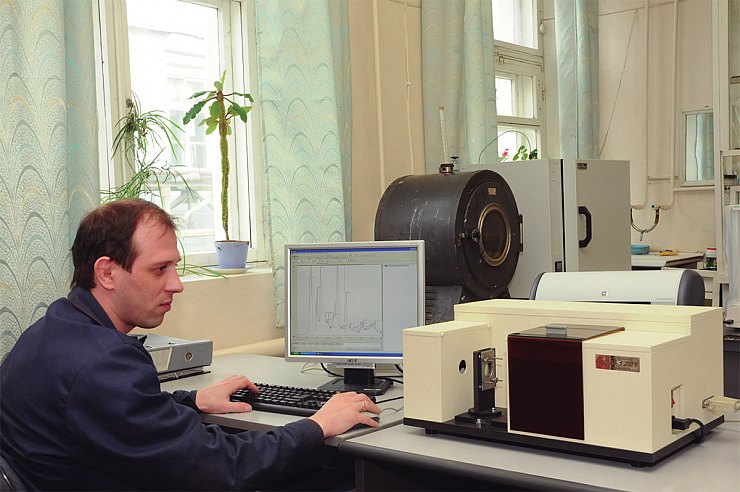
Безусловно, по всем показателям, кроме, пожалуй, цены, нитроэмали проигрывают современным ЛКМ, поэтому в тематических обзорах их принято ругать и пинать ногами. Мы же относимся к этим материалам с искренним уважением – все же «они были первыми».
И еще: в советские времена правительственные «Зилы» и «Чайки» окрашивали только нитроэмалями. Покрытия насчитывали до 12 слоев, включая грунтовочные, и выглядели те «членовозы» великолепно. Правда, их почти непрерывно подкрашивали и полировали – благо было кому...
Катализаторы, инициаторы, отвердители
В публикациях на тему ЛКМ часто путают понятия «катализатор», «инициатор» и «отвердитель». В действительности это разные материалы и механизм их действия неодинаков.
Как известно из школьного курса химии, катализатор увеличивает скорость химической реакции, но сам в реакцию не вступает.
В качестве примера приведем так называемые кислые катализаторы. Будучи добавлены в мела-миноалкидную эмаль, они создают кислую среду, в которой меламинформальдегидная смола гораздо «охотнее» взаимодействует с гидроксильными группами алкидного компонента, что позволяет снизить температуру сушки.
В акриловых системах используют катализаторы на основе органических солей переходных металлов или органических аминов, ускоряющих реакцию уретанообразования.
Инициатор, в отличие от катализатора, участвует в реакции, генерируя радикалы, расходуется (распадается) сам и в конечном счете входит в состав полимера. Пример: второй компонент (тюбик) в полиэфирных шпатлевках содержит именно инициатор.
И наконец, об отвердителях. Отвердитель – это полноправный компонент связующего. Он не является ни катализатором, ни инициатором.
«Алкид»
Алкидные эмали у нас называют «эмалями воздушной сушки» – и вполне справедливо, поскольку отверждение их пленок происходит при комнатной температуре с участием кислорода воздуха. Впрочем, об этом чуть ниже, а пока поговорим о терминологии.
Начнем с формального определения: алкидная эмаль – это суспензия пигментов в алкидных лаках с добавками модификаторов. И тут возникает закономерный вопрос: а что такое алкидные лаки? Пожалуйста: это растворы алкидных смол.
Хорошо, скажет читатель, а что такое «алкидные смолы»? Слово «алкидный» происходит от англ. alcohol – спирт и acid – кислота. Соответственно, алкидные смолы получают на основе многоатомных спиртов и многоосновных кислот. Попутно заметим, что термина «алкид» в фундаментальной химии не существует, это термин из лакокрасочного лексикона.
К алкидным смолам относится, например, глифталевая смола, получаемая при взаимодействии глицерина (трехатомного спирта), фталевого ангидрида и растительного масла (сложный эфир глицерина и высших жирных кислот).
Можно вспомнить и пентафталевую смолу, ингредиентами которой являются пентаэритрит (четырехатомный спирт) и тот же фта-левый ангидрид. На основе этих смол российские лакокрасочные заводы выпускают лаки и эмали, маркируемые соответственно ГФ и ПФ. Это – классические алкидные ЛКМ. На автомобильный конвейер глифталевые эмали пришли в 40–50-х годах на смену нитроэмалям.
К алкидным относятся и некоторые зарубежные ремонтные автоэмали. Впрочем, не только зарубежные – например «Vika-алкид» (Vika-60), эмаль естественной сушки по сроку службы почти не уступает МЛ-1110 горячей сушки.
Возможно, кто-то удивится: неужели «дачная» ПФ-115 и авторемонтные алкидные эмали (как импортные, так и наши) стоят в одном ряду? Да, с точки зрения механизма отверждения это так. В отличие от нитроцеллюлозных, при сушке алкидных материалов параллельно протекают два процесса: испарение растворителя (физическая сушка) и химическое превращение компонентов связующего в пространственно-сшитый полимер. После полного отверждения растворить такую пленку невозможно, поэтому ее называют необратимой.
Необходимо помнить: в химическом отверждении (пленкообразовании) всех эмалей, дающих необратимую пленку, обязательно участвуют два компонента.
Есть вопрос! Но алкидные эмали считаются однокомпонентными материалами. Покупая банку с эмалью, мы не получаем никакого отвердителя...
Ответ. Давайте различать коммерческое название и химическую суть. Действительно, двухкомпонентными (2К) материалами называют ЛКМ, поставляемые в двух упаковках: вот, положим, акриловая грунтовка, а вот отвердитель к ней.
В банке с алкидной эмалью находится один реакционноспособный компонент – раствор алкидной смолы, модифицированный растительным маслом. От растительного масла продукту достаются «хвосты» высших жирных непредельных кислот, содержащих сопряженные двойные связи.
Второй компонент алкидных эмалей – это кислород воздуха. Благодаря его взаимодействию с указанными двойными связями образуется высокомолекулярное соединение, т.е. происходит полимеризация. А поскольку каждая молекула алкидного компонента имеет несколько двойных связей, полимер получается «пространственно сшитым». Так что кислород – полноценный компонент связующего, его вполне можно считать отвердителем.
Можно привести показательный бытовой пример: как тщательно ни закрывай банку с эмалью ПФ, все равно в ней образуется пленка. Это результат реакции алкидной составляющей с кислородом, находящимся под крышкой банки. А вот у эмалей марки МЛ (о них будет рассказано ниже) такого явления не наблюдается.
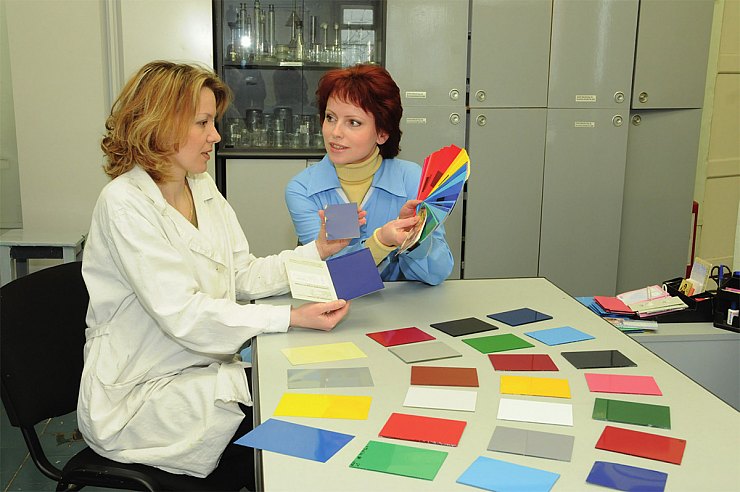
Всем известно, что алкидными эмалями легко и удобно красить. Поэтому их часто используют для окраски подержанных автомобилей перед продажей – вид отменный, а что там дальше будет, пусть новый хозяин думает. Иногда такие эмали применяют для обновления кабин грузовиков перед техосмотром – получается быстро и недорого.
На конвейерах алкидные эмали не применяются.
Есть вопрос! Маляры знают, что пленка алкидной эмали хорошо сохнет «сверху», а вот «вглубь» – хуже..
Ответ. Это характерно при отверждении кислородом – по мере полимеризации его доступ «вглубь» затрудняется. Подобных недостатков лишены автоэмали, которые мы рассмотрим в следующих разделах.
«Синтетика»
В этом разделе мы поговорим о меламиноал-кидных эмалях. Как и в предыдущем случае, при отверждении этих ЛКМ одновременно протекают два процесса: испарение растворителя и поликонденсация смол (образование необратимой пленки).
Во втором процессе участвуют два компонента – но до поры до времени они мирно соседствуют в банке (о механизме отверждения говорится ниже). Что же это за компоненты? Во-первых, это алкидная составляющая, модифицированная растительным маслом, или раствор полиэфирной смолы; во-вторых – меламинформальдегидная смола.
Есть вопрос! Меламиноалкидные эмали наши мастера давно и упорно именуют «синтетикой». Почему
Ответ. Одна из этимологических версий такова: при создании алкидной части этих эмалей химики использовали синтетические жирные кислоты. Отсюда и пошло – «синтетика», «окрасить синтетикой».
Но вернемся к компонентам эмали. В отличие от эмалей воздушной сушки алкидная составляющая меламиноалкидных эмалей содержит мало двойных связей (а полиэфирная и вовсе их не имеет). Но в ней, в этой составляющей, обязательно присутствуют реакционноспособные гидроксильные группы ОН – как у спирта.
Что это означает на практике? Да то, что в отличие от алкидных эмалей алкидная составляющая здесь практически не вступает в реакцию с кислородом воздуха. Но зато при повышении температуры упомянутые гидроксильные группы ОН начинают взаимодействовать с метилольными группами меламиноалкидной смолы.
Иными словами, при достаточном нагреве запускается реакция между двумя компонентами. Поэтому второе название меламиноалкидных эмалей – «эмали горячей сушки».
Внимательный читатель уже, наверное, догадался о преимуществах такого механизма: в отличие от кислородного отверждения алкидных эмалей полимеризация здесь проходит равномерно по всей глубине. В результате образуется надежная необратимая пленка с пространственной «сшивкой» по всем направлениям.
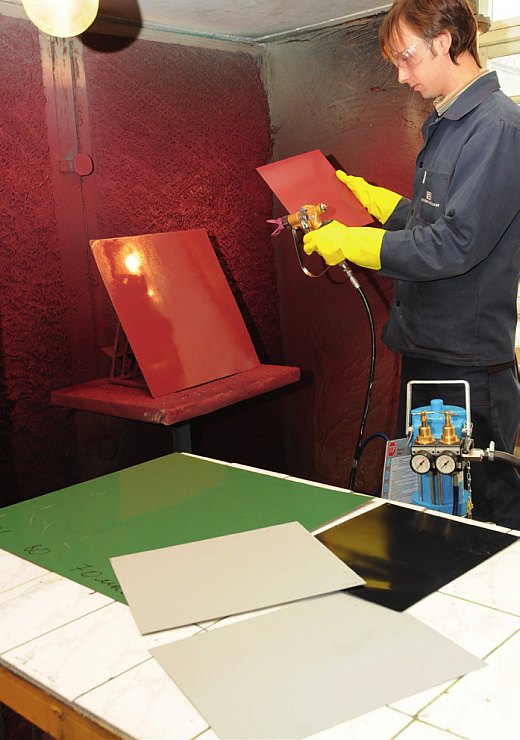
Если же равномерность отверждения «вглубь» отсутствует, это означает одно из двух: либо эмаль «левая», основанная на дешевом алкидном ингредиенте (пример – жирный алкид с обилием сопряженных двойных связей, в результате инициативу перехватывает кислород воздуха); либо нарушен температурный режим и реакция «не пошла».
Итак, при высокой температуре меламинформальдегидная смола в описываемых эмалях играет роль отвердителя. А каковы значения этой температуры? Никакого секрета: 150°С для грунтовок и 130°С для эмалей – например, для «Vika-синтал» (МЛ-1110).
Есть вопрос! В инструкции к меламиноалкидной эмали «Vika-синтал» (МЛ-197) написано, что она отверждается при 105°С. Как это согласуется с только что сказанным?
Ответ. В этой эмали применена иная, более реакционноспособная меламинформальдегидная смола – она-то и позволила снизить температуру сушки в сравнении с МЛ-1110. Но есть у «197-й» и минусы – более года ее хранить нельзя, поскольку даже при обычной температуре реакция хоть медленно, но протекает. Это своеобразная плата за повышенную реакционную способность смолы.
Меламиноалкидные эмали МЛ-1110 и МЛ-12 используют для окраски автомобильных кузовов на некоторых заводских конвейерах – но уже не столь широко, как раньше.
В ремонтной окраске мастера применяли их в соответствии с поговоркой «на безрыбье...». Но безрыбье кончилось: нынче рынок авторемонтных ЛКМ разнообразен и доступен, поэтому потребление МЛ-1110 за последнее десятилетие упало в несколько раз. Однако для мастеров, все еще работающих с «синтетикой», хорошим подспорьем являются ускорители сушки на изоцианатной основе. По сути, это отвердители, превращающие МЛ-1110 в двухкомпонентную эмаль.
«Акрил»
Не ищите в химических справочниках и энциклопедиях слово «акрил» – все равно не найдете. Этот термин является разговорным, жаргонным и означает «акриловый лак», «акриловая эмаль». Но прежде чем коснуться теории, посмотрим на тару, в которую разлиты акриловые ЛКМ.
В этой группе материалов компоненты связующего (пленкообразователя) разнесены по разным банкам. В отличие от меламиноалкидных эмалей, хранить их в одной емкости нельзя – они тут же вступят в реакцию. А теперь наберемся терпения и попытаемся, как говорится, «на пальцах» разобраться в химии этих ЛКМ.
Первый компонент содержит раствор акрилового сополимера. Это высокомолекулярное вещество, продукт совместной полимеризации акриловых мономеров – акриловой и метакриловой кислот, а также их сложных эфиров (если кому интересно – метилакрилата, бутил-акрилата, метилметакрилата, бутилметакрила-та и др.). И что важно: в составе этого сополимера есть звенья с гидроксильными группами ОН – запомним это.
Теперь о втором компоненте, фактически – отвердителе. В его состав входит полиизоцианат, подобранный именно для данной эмали. Нам важно знать, что он содержит изоцианатные группы 0=C=N-, весьма и весьма реакционноспособные.
И когда раствор сополимера и отвердитель соединяют, гидроксильная и изоцианатная группа вступают в реакцию по следующей схеме:

Конструкция, начертанная справа от стрелочки, – не что иное, как уретановая группа. Отметим, что изоцианатные группы, присутствующие в отвердителе, условно можно изобразить в виде трехлучевых звездочек:

Благодаря этому возникающая при полимеризации полиуретановая сетка получает пространственные «сшивки».
В итоге в отвержденной акриловой пленке образуется полиуретан, придающий покрытию исключительно высокие потребительские свойства, в частности атмосферостой кость и эластичность.
Описанная система носит название «акрил-уретановой». Такие материалы имеются в арсеналах всех известных окрасочных систем. По этой же схеме работает отечественная «Vika-акрил».
Есть вопрос! Можно ли разбавлять акриловые ЛКМ отечественными растворителями серии 645-651?
Ответ. Категорически нет. Они содержат спирты, а следовательно, посторонние гидроксильные группы ОН. Они способны направить реакцию по ложному пути, в результате чего пространственно сшитого полимера не образуется. По той же причине в системе недопустимо присутствие влаги. Следует применять растворители или разбавители, рекомендованные производителем ЛКМ. Для «Vika-акрил» это Р 1301 и Р1301-М.
Есть вопрос! Можно ли отверждать «Vika-акрил» другими изоцианатами?
Ответ. Нет. В акриловых системах сополимер и полиизоцианат тщательно подбираются друг к другу. Если взять другой отвердитель – получим другой полимер с совершенно иными свойствами.
Тандем
Теперь самое время поговорить о двухслойной системе «базисная эмаль плюс прозрачный лак». Выше мы писали, что именно она пришла на смену просто эмали («topcoat») и теперь почти повсеместно применяется для окраски кузовов легковых автомобилей.
Что же в ней «системного»? Ведь эмаль уже есть, даже «базисная» («basecoat»). А лак зачем? Чтобы блестело лучше? Не только. У каждого слоя своя функция. Раньше эмаль решала задачи внешнего вида, блеска, цвета, укрывистости, а также защиты от внешних воздействий. В двухслойной системе функции внешнего вида, блеска и защиты перешли к прозрачному лаку, а укрывистость и цвет остались за базисной эмалью.
Первыми на свет появились базисные эмали, с алюминиевыми пигментами. Благодаря knowhow блестящие алюминиевые чешуйки укладывались в покрытии ровненько. А «эффект металла» появлялся лишь после нанесения прозрачного лака поверх базисной эмали.
В настоящее время в базисных эмалях применяют сложные комбинации перламутровых, алюминиевых, транспарентных пигментов, формирующие широчайшее разнообразие цвета и эффектов. Оказалось, что даже при использовании привычных укрывистых пигментов, дающих «обычный» цвет без какого-либо эффекта, двухслойная система по сравнению с однослойной эмалью выглядит куда более выразительно и привлекательно.
В химическом отношении прозрачный лак сходен с вышеописанным ЛКМ «Vika-акрил». Важное отличие – необходимость в специальных компонентах, защищающих лак от... света. Да-да, от солнечного света, этого злостного разрушителя полимеров. Кстати, в пигментированных эмалях светозащитную функцию берут на себя пигменты. Тоже не простые, а специальные, светостойкие.
Конструируют базисные эмали по-разному, но один из наиболее распространенных вариантов – комбинация полиэфира, меламин-формальдегидной смолы (напоминает МЛ из предыдущих глав) и ацетобутирата целлюлозы (заставляет вспомнить нитроэмали НЦ). Только в отличие от нитрата целлюлозы ацетобутират устойчив к солнечному свету.
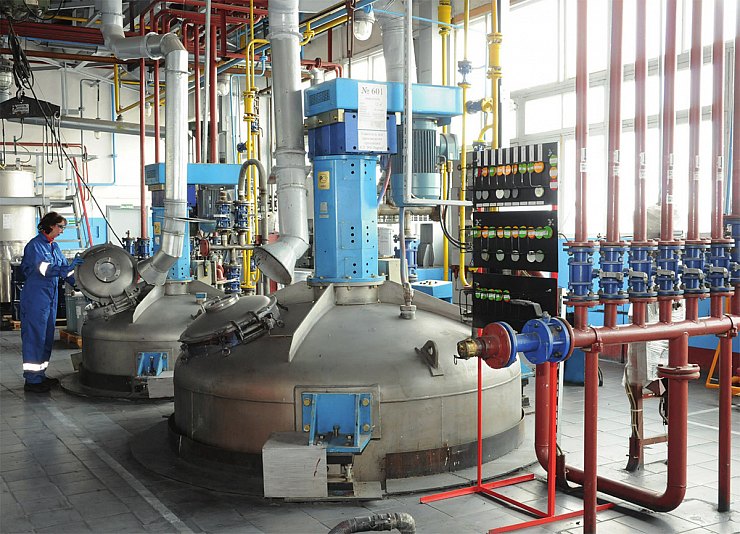
Базисные эмали содержат много растворителя, а усадка пленки при сушке способствует «укладке» пигментов. Сохнет эмаль быстро, поверхность чаще всего получается матовой, цвет разобрать трудно, эффекта вообще никакого. Восхищаться внешним видом, цветом, «металликом» и «перламутром» можно лишь после перекрытия лаком. Сам же лак может быть не только высокоглянцевым, но и матовым и даже с регулируемым блеском.
С конкретными ассортиментами можно ознакомиться на сайтах производителей ЛКП.
Такова, если вкратце, ретроспектива развития автомобильных эмалей. От обратимой пленки «нитро», через отверждаемое кислородом покрытие «алкида», через пространственную сетку «синтетики» и полиуретановую «сшивку» «акрила» к фантастическим эффектам двухслойной системы. И все это в течение XX века. Что добавило в этот список нынешнее столетие?
Н2O
XXI век озаботился сохранением окружающей среды. Угроза всемирного потепления сменяется ужасами всемирного похолодания, и наоборот. Объясняют это одной и той же причиной: человек загрязняет окружающую среду. Лакокрасочники тоже загрязняют – и пуще всего растворителем, бездарно улетающим в атмосферу. Поставщики пишут на банках HS, VHS, а проверишь – у большинства в лучшем случае MS, а то и LS. Получается, обманывают и себя, и потребителя, и природу.
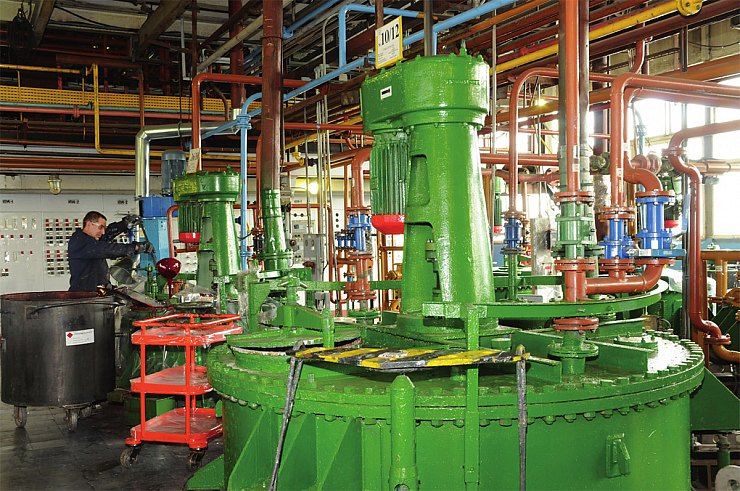
Но шутки шутками, а больше всего растворителей содержится в базисных эмалях. За них-то европейцы и взялись в первую очередь. Решили, пусть в атмосферу улетает вода. И приспособили свою продукцию «под воду», правда, для этого пришлось перерабатывать и смолы, и пигменты, и добавки.
Почему пришлось? Воду называют растворителем, но для ЛКМ в этом качестве она совершенно непригодна. Смолы для автомобильных покрытий вода не растворяет, некоторые пигменты начинают с ней взаимодействовать и в итоге портятся, а алюминиевые пигменты и вовсе могут привести к взрыву банок с краской.
Поэтому смолы переводят в состояние эмульсий, в которых мельчайшие (субмикро- и наноразмерные) капельки смолы диспергированы в воде. В таком случае вода выступает как дисперсионная среда и успешно понижает вязкость.
Вот так и родились эмали на водной основе. Их уже используют и на конвейерах, и в авторемонте. Европейские производители сырья готовы предложить компоненты на водной основе для всех слоев, формирующих авторемонтное покрытие. В России водные базисные эмали пока не производят, но зарубежные завозят и применяют в сервисах – прежде всего в дилерских. И даже отмечают технологические преимущества экологичных эмалей по сравнению с органоразбавляемыми.
Но вот незадача: вода замерзает. При этом эмульсии необратимо портятся. Краски на водной основе, устойчивые к замораживанию, существуют пока только для декоративного применения. Автомобильные эмали намного капризнее и защитить их от мороза пока не удается. Создание эмульсий, стабильных при хранении при низких температурах и пригодных к нанесению, да еще таких, чтобы внешний вид радовал потребителя, – задача необычайно сложная.
Применение водных ЛКМ требует обновления навыков работы. А для нашей страны – и особой логистики с учетом географии и морозных просторов. Только тогда экологичные авторемонтные эмали получат в России широкое распространение. На этой оптимистической ноте мы закончим сегодняшний обзор.
Фото предоставлены ОАО «Русские краски»