Вскрытие показало… Часть 7. Косяк
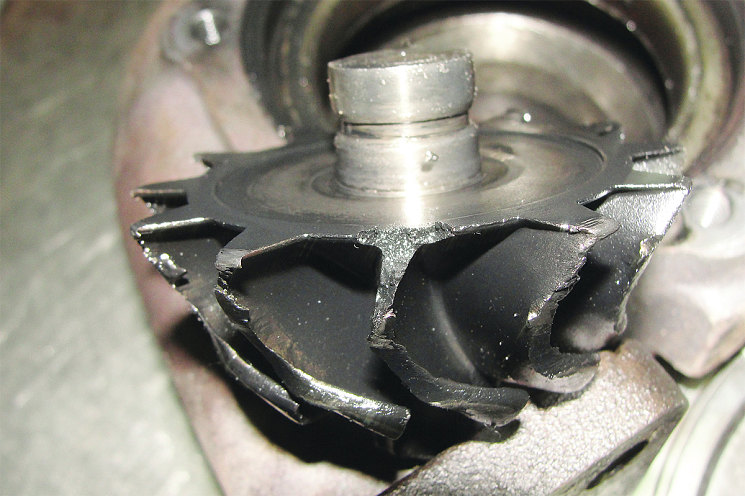
У читателей, ознакомившихся с предыдущими сериями турбоэпопеи, может сложиться мнение, что претензии к качеству турбин, поступающих на экспертизу, сплошь необоснованные. Это не так – часть из них, пусть и небольшая, действительно имеет под собой основание, а именно – брак, допущенный при производстве или ремонте турбины. Проще говоря, косяк. Объективности ради эта часть посвящается именно таким случаям.
Эксперту по турбокомпрессорам (ТК) приходится иметь дело со всевозможными агрегатами. На исследование попадают как оригинальные изделия от ведущих производителей турбин, поставляющих свою продукцию на сборочные конвейеры автозаводов, так и разного рода неоригинал. Последний включает так называемые аналоги оригинальных турбин более, менее или вовсе неизвестных брендов, а также подделки, о происхождении которых можно только догадываться. Наконец, часть из этого разношерстного множества агрегатов к моменту вскрытия успевает утратить первоначальную «девственность», т. е. пройти через руки ремонтников.
Надо сказать, что требования к любым объектам исследования самые демократичные. Главное, чтобы агрегат поступил к эксперту не разобранным, не отмытым и был полностью укомплектован. Если иметь в виду сегодняшнюю тему, упомянутые группы объектов экспертизы отличаются не только происхождением, но также вероятностью обнаружения в них косяков и их характером. Это дает основание структурировать повествование соответствующим образом.
Оригинальные косяки
Производители турбокомпрессоров и их дистрибьюторы на протяжении долгих лет мониторят ситуацию по отказам ТК и причинам, которые их вызывают. Результаты этих исследований подтверждают тот факт, что процент брака в оригинальных агрегатах, что называется, стремится к нулю. Такова особенность этих, во многом необычных устройств, что их работоспособность не может быть гарантирована без испытаний каждого сходящего с конвейера ТК в режиме, имитирующем условия работы турбины в двигателе. В ходе тестирования проверяются правильность сборки картриджа ТК, надежность газодинамических уплотнений ротора, величина остаточного дисбаланса ротора. Одновременно происходит обкатка турбины.
Это звено технологической цепи является непреодолимой преградой для подавляющего большинства турбоагрегатов, имеющих те или иные дефекты изготовления или сборки. К потребителю попадают только те изделия, которые успешно прошли этап выходных испытаний и подтвердили в свою работоспособность. Поэтому, действительно, вероятность производственного брака оригинальных ТК мизерна. Хотите – верьте, хотите – нет, но за почти десятилетний период работы эксперт с такими случаями сталкивался исключительно редко, а именно – дважды.
Один из них отражен в следующих ниже выдержках из акта экспертизы.
Вскрытие № 17
Объект – оригинальный ТК 11-литрового турбодизеля Mercedes ОМ 441, бывший в эксплуатации, не подвергавшийся восстановительному ремонту (фото 1) .
Внешним осмотром установлено:
– следов самостоятельной разборки ТК не обнаружено;
– на фланцах крепления магистралей подвода и слива масла обнаружены фрагменты герметика красного цвета, отверстие слива масла частично перекрыто (фото 2).
После демонтажа корпусов ТК выявлено:
– в корпусах турбины и компрессора обнаружено моторное масло;
– внутренние поверхности корпуса турбины, колесо и тепловой экран закоксованы продуктами деструкции моторного масла (фото 3);
– радиальный люфт ротора значительно превышает нормы технических условий завода-изготовителя;
– лопатки колес турбины и компрессора, а также их корпуса повреждены в результате соприкосновения (фото 4);
Разборка корпуса подшипников показала:
– опорный подшипник со стороны корпуса компрессора отсутствует (фото 5 и 6);
– детали уплотнения со стороны компрессора значительно изношены;
– в масляных каналах и на посадочном месте опорного подшипника со стороны турбины обнаружены частицы герметика (фото 7).
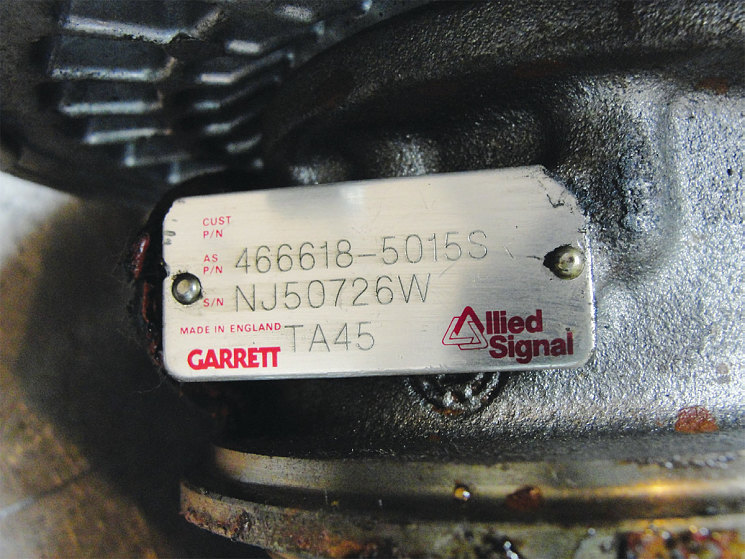
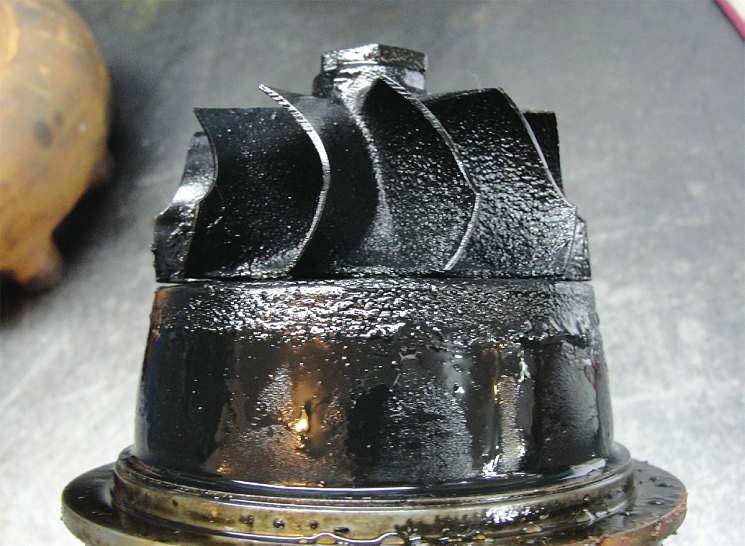
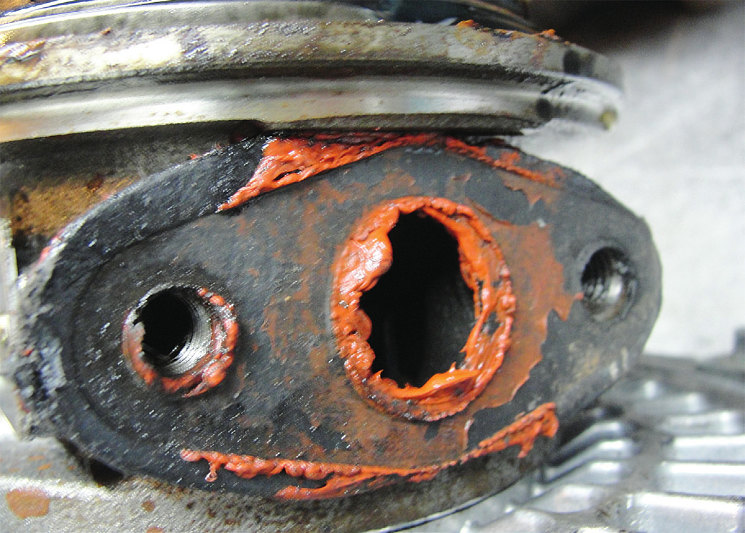
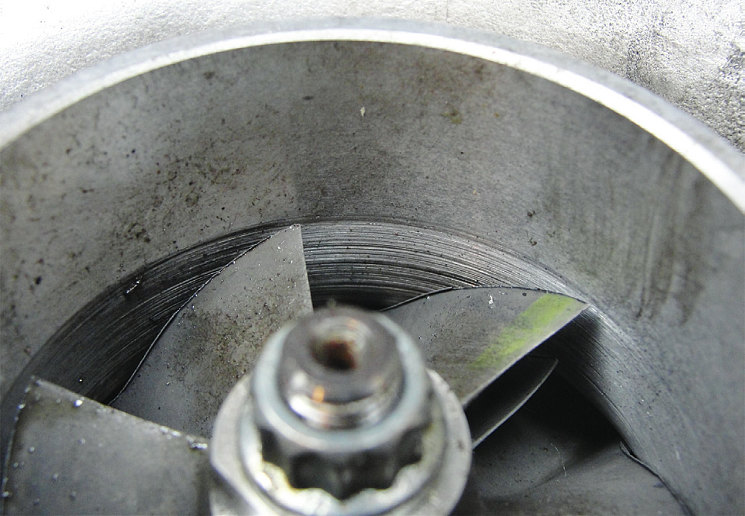
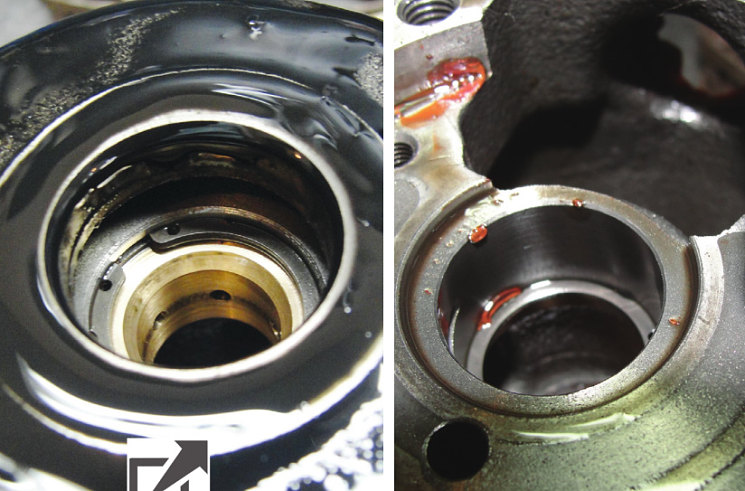
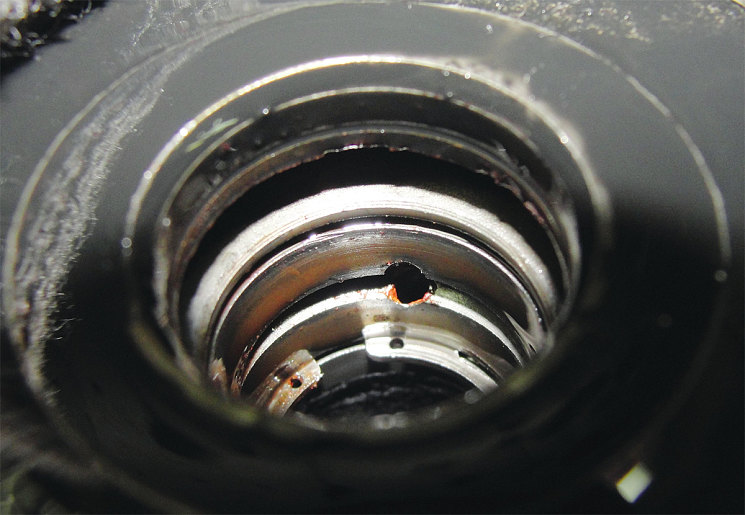
Выводы
ТК неработоспособен. Наиболее вероятная причина его выхода из строя – отсутствие опорного подшипника скольжения со стороны корпуса компрессора (заводской брак при сборке корпуса подшипников).
Что тут можно добавить? При отсутствии одного из подшипников опорой ротора стало уплотнительное кольцо со стороны корпуса компрессора. Это вызвало повреждение кольца и сопряженных с ним поверхностей вала и корпуса подшипников. В свою очередь, это привело к увеличению радиального люфта ротора вплоть до касания колесами корпусных деталей и выносу масла через турбокомпрессор.
Наличие производственного брака в данной турбине – несомненный факт, но совсем не факт, что этот случай был признан гарантийным. Причина – использование герметика при установке турбоагрегата. Едва ли кто-то до сих пор не знает, что применение герметика при монтаже турбин категорически запрещается и является основанием для отказа в исполнении гарантийных обязательств. Почему – понятно и на данном примере. Во-первых, герметик уменьшил проходное сечение сливного отверстия. Затруднение слива масла неминуемо приводит к увеличению его выноса через газодинамические уплотнения «со всеми вытекающими». Во-вторых: казалось бы, герметизировали внешние соединения в местах подачи и слива масла, а следы герметика обнаружились во всех внутренностях турбины. Это закономерный итог и притом еще не окончательный. Финал наступит тогда, когда оторвавшиеся частицы герметика, совершающие круговорот по системе смазки двигателя, частично или полностью перекроют один из узких каналов подачи масла внутри турбины, вызвав масляное голодание подшипника. Короче говоря, этой турбине в любом случае грозили серьезные неприятности из-за ошибки работников сервиса.
Второй случай, выявивший наличие брака в оригинальном изделии, также произошел с грузовой турбиной. Она попала на экспертизу с претензией, указывавшей на течь масла. Действительно, в ходе исследования был выявлен дефект сборки: резиновое уплотнительное кольцо в соединении центрального корпуса подшипников и опорного диска корпуса компрессора было установлено с ошибкой – оно частично вылезло из канавки.
Характерно, что оба упомянутых случая касаются турбин большого типоразмера (грузовых). Это не случайно. Технология их производства не включает упоминавшийся выше этап финального тестирования каждого агрегата – финишную балансировку. Причина в том, что требования к жизненно важному параметру – величине остаточного дисбаланса ротора – для больших турбин существенно мягче, чем для остальных турбоагрегатов. Выполнить их удается предварительной балансировкой деталей ротора, в сборе их балансировать не обязательно. Поэтому они, как правило, не подвергаются финишной балансировке, что увеличивает вероятность ошибок сборки.
Итак, всего два случая заводского брака за почти десятилетнюю, весьма интенсивную экспертную практику. Разве это не убедительное подтверждение справедливости заявлений производителей турбин о чрезвычайной надежности их изделий? Действительно, брак в оригинальных агрегатах сведен к минимуму. Отсюда следует практический вывод. Если вы столкнулись с отказом новой оригинальной турбины, версию о ее производственном браке оставьте напоследок.
К сожалению, такого нельзя сказать в отношении различных копий, подделок и самоделок.
Неоригинальные косяки
Многочисленным и разнообразным случаям брака, аккуратно выражаясь, неоригинальных турбоизделий была посвящена отдельная статья (см. № 6/2016). Поскольку эта тема актуальна и неисчерпаема, не будет лишним затронуть ее еще раз. Тем более что она и здесь кстати – это те случаи, когда претензии потребителей к качеству товара обоснованны и, по идее, должны покрываться гарантией производителя. Другое дело, что даже имея железные доказательства наличия брака, получить «сатисфакцию» покупателю неоригинала вряд ли удастся. Товар-то «ноу нейм», т. е. производитель неизвестен. Да и с продавца спросить едва ли получится. Его реакция предсказуема: «Какие гарантии могут быть за такую цену?».
Порывшись в архивах эксперта, ничего принципиально нового найти не удалось. Случаи брака неоригинальных агрегатов предсказуемо являются следствием применения некачественных материалов и несовершенных технологий, банальных ошибок сборки, игнорирования операций финишной балансировки и настройки устройств регулирования ТК. Но вариации на эти темы попадаются весьма любопытные. Например, вот такая.
Покупатель заявил, что после замены турбины двигатель его «фольксвагена» напрочь отказался запускаться. Турбина, произведенная «сами знаете где», была внимательно изучена. Внешне – ничего (видали и хуже), пневмокамера управления байпасом настроена правильно, люфты ротора в норме. Вот только канал, по которому отработавшие газы поступают к турбинному колесу, наглухо закрыт стеной из металла (фото 8). Турбину нечаянно заглушили, покупателю достался просто компрессор, без «турбо». Хорошо еще, что двигатель не запустился – негативные последствия оказались минимальными.
В отличие от предыдущего, скажем прямо, редкого и курьезного случая, следующий (фото 9) – наоборот, довольно частый. Отечественный грузовик марки ГАЗ с недавно замененной турбиной исправно «тянул лямку» и вдруг… в один момент его «шестерка» загудела так, как будто глушитель оторвался. Экспертиза ТК выявила, что технологическая заглушка в корпусе турбины, служащая для доступа к байпасному клапану, улетела. Видимо, заглушка была как-то закернена, но не проварена, а потому при нагреве вывалилась. При этом часть отработавших газов из турбины направлялась не в приемную трубу глушителя, а прямо на улицу. Так и до пожара недалеко! В выводах акта экспертизы сделана запись: «Данный случай может быть признан гарантийным, так как выход турбокомпрессора из строя вызван нарушением технологии его изготовления заводом-производителем».
Вот еще один любопытный случай. Во-первых, он интересен тем, что на вскрытие попал аналог отечественного турбокомпрессора ТКР-6.1, изготовленный не «сами знаете где», а на территории одной из бывших советских республик. Во-вторых, в отсутствие отечественных флагманов турбостроения, выпускающих продукцию оригинального качества, вообще сложно говорить об оригинале, аналогах, подделках и т. д. Агрегаты еще советской разработки для отечественных турбодизелей сегодня делают «там и сям» и «так и сяк». Моральное право отнести этот продукт к разряду аналогов дало «в-третьих», а именно – характер аварийного повреждения. Вскрытие показало, что у агрегата произошло тотальное разрушение колеса турбины. Турбинное колесо просто рассыпалось и исчезло (фото 10). Мало того: корпус турбины насквозь пробило осколками колеса как чугунок, обычный печной горшок (фото 11). Возникает ряд вопросов. Из какого материала были сделаны колесо и корпус? Куда подевались положенные по стандарту никель и хром? Кто ответит за растрату кремниево-молибденового чугуна? Вопросы, понятное дело, риторические. Ответ на них давно известен: воруют!
При вскрытии копии распространенной турбины, применяющейся на многих «боксерах», «джамперах» и «дукатах», была обнаружена картина, отраженная на фото 12. Как говорят некоторые остряки: «Вал – пополам, турбина – вдребезги». Оказалось, что полное истребление турбины случилось из-за нетривиального производственного брака. Пневматическая камера управления байпасным клапаном крепится к кронштейну контактной сваркой. Неоригинальная сварка не вынесла вибраций и циклических нагрузок, камера отвалилась, и байпасный клапан турбины перестал открываться в нужный момент (фото 13). В выводах акта экспертизы отмечено, что турбина «умерла» от превышения допустимой частоты вращения ротора (перекрута), вызванного неисправностью байпасного клапана.
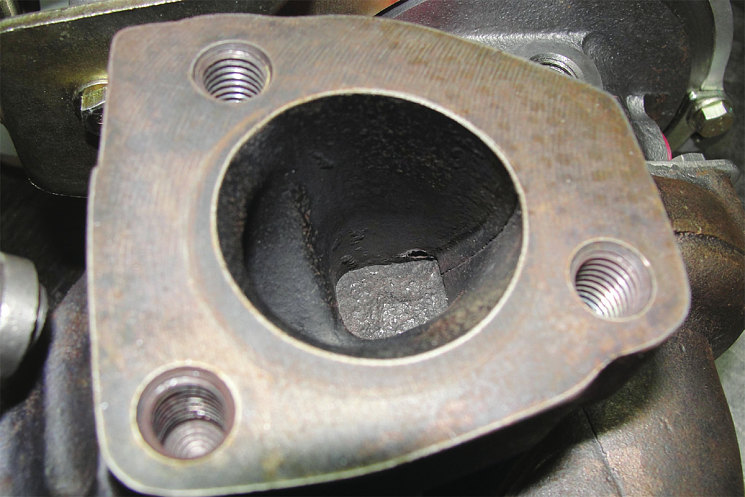
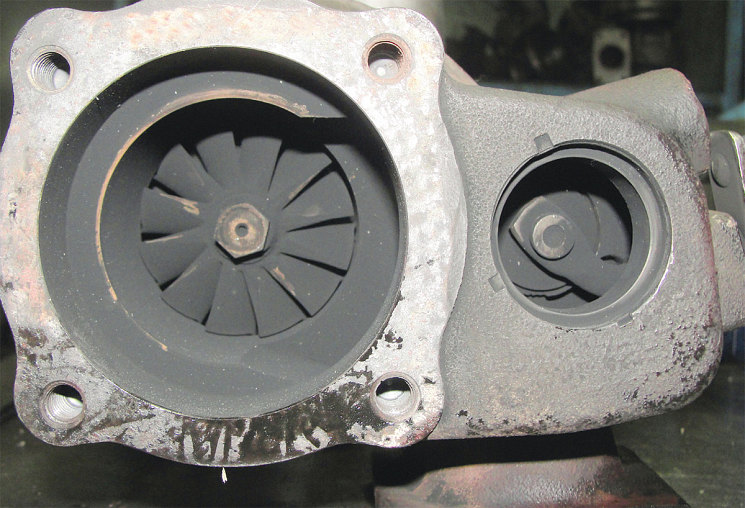
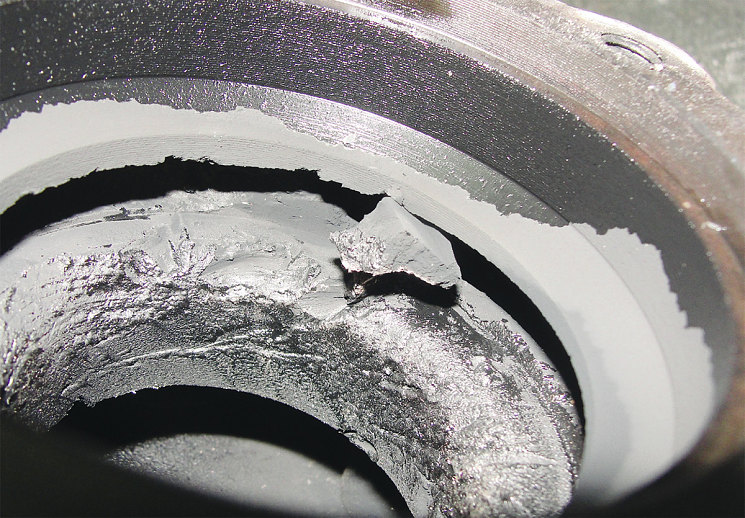
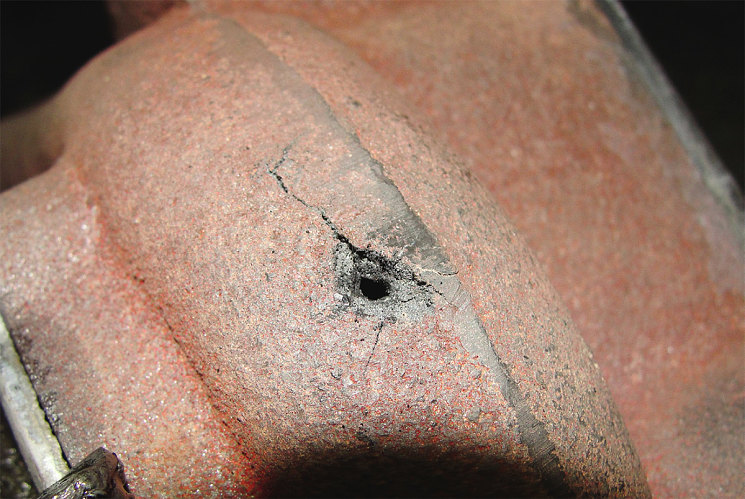
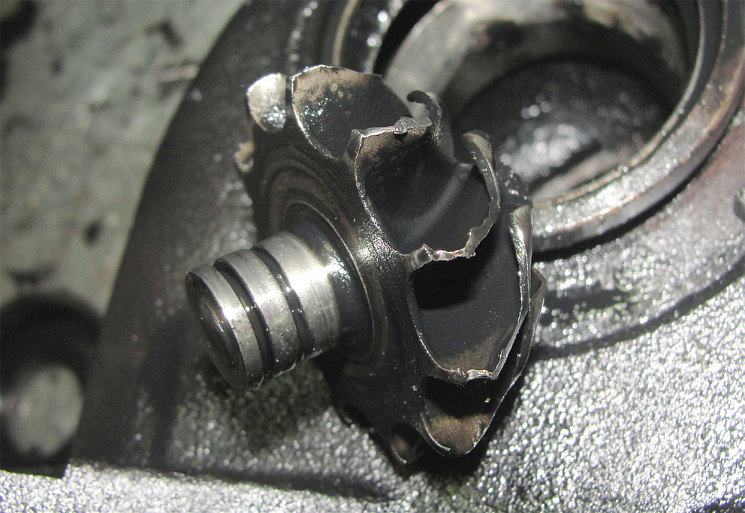
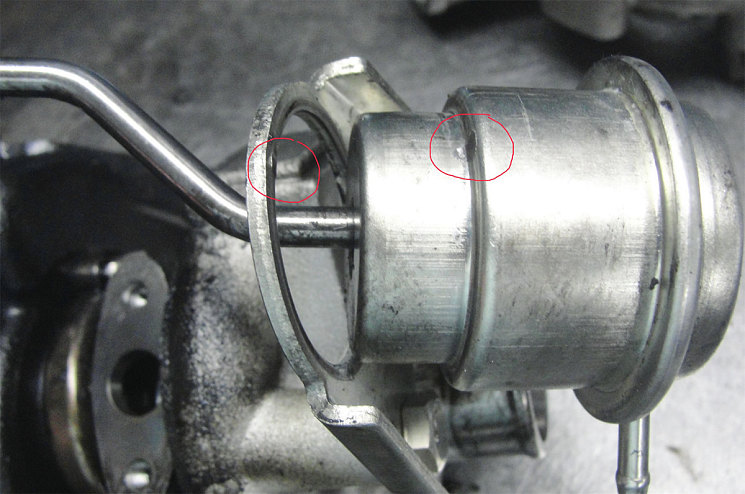
В завершение неоригинальной части повествования познакомимся с результатами экспертизы копии популярной турбины Borg Warner автомобиля Hyundai Starex 2,5 CRDI.
Вскрытие № 18
Объект – неоригинальный ТК, бывший в эксплуатации, не подвергавшийся восстановительному ремонту. Производитель турбокомпрессора не установлен (фото 14).
Внешний осмотр показал:
– следов самостоятельной разборки ТК и применения герметика не обнаружено;
– на корпусе турбины заметны признаки перегрева (цвета побежалости);
– настройка камеры управления регулируемым сопловым аппаратом (РСА) соответствует техническому регламенту завода-производителя оригинального ТК.
После демонтажа корпусов ТК выявлено:
– между корпусом компрессора и корпусом подшипников отсутствует уплотнение (резиновое кольцо);
– в корпусах турбины и компрессора обнаружено моторное масло;
– на гайке вала следов динамической балансировки ротора в сборе с корпусом подшипников не обнаружено;
– люфты вала ротора значительно превышают допуски;
– лопатки колес турбины и компрессора, а также ответные части корпусов повреждены из-за соприкосновения;
– механизм РСА турбины исправен, перемещение его деталей не затруднено.
После разборки корпуса подшипников выявлено:
– рабочие поверхности подшипников (опорного и упорного) имеют следы полусухого трения, перегрева и износа;
– на шейках вала ротора есть следы полусухого трения, прихвата, перегрева и наволакивания материала опорных подшипников (фото 15);
– уплотнительное кольцо корпуса подшипников со стороны колеса турбины разрушено, места его установки в корпусе и на роторе повреждены;
– конструкция опорного подшипника, выполненного в виде моновтулки, не соответствует оригиналу – масляные каналы в моновтулке и корпусе подшипников не совпадают (фото 16).
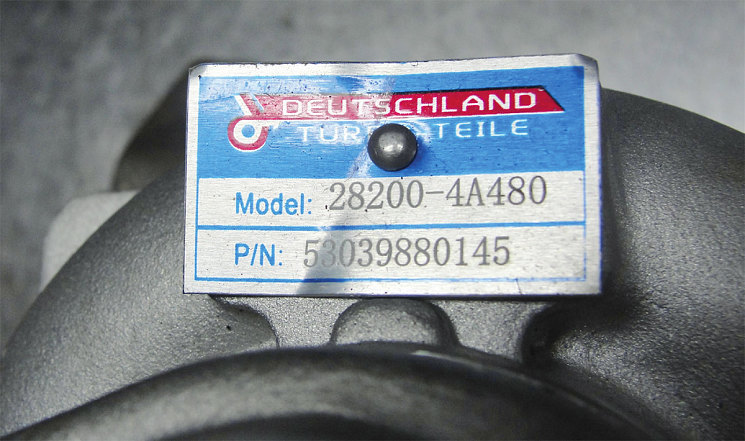
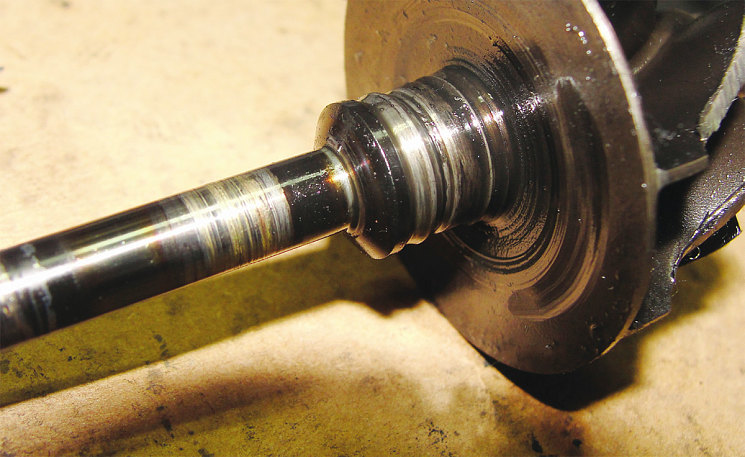
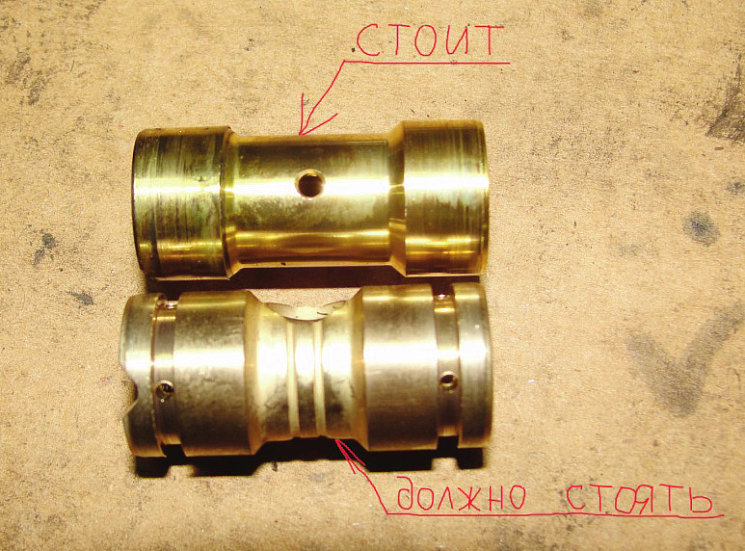
Выводы
Турбокомпрессор неработоспособен. Наиболее вероятная причина выхода данного ТК из строя – масляное голодание узла подшипников вследствие установки опорного подшипника скольжения другой конструкции, отличающегося иным расположением масляных каналов.
В надписи на шильдике этой неудачной копии содержится намек, что она изготовлена в некоей «дойчландии». Похоже, назначение отверстий на моновтулке было неведомо сборщикам из этой загадочной «дойчландии». Поэтому они установили подходящий по размерам подшипник от турбины того же модельного ряда Borg Warner К03, но другого конструктивного исполнения.
Вскрытие выявило еще несколько нарушений. Отсутствие уплотнительного кольца между корпусом подшипников и корпусом компрессора – вещь неприятная, но не роковая. Значительно опаснее то, что турбина не проходила финишную балансировку. Иначе она «умерла» бы еще раньше, при испытаниях.
Ремонтный косяк
За последнюю пару лет по понятным причинам резко увеличился спрос на ремонт турбин. Ремонт как альтернатива покупке нового агрегата позволяет сократить расходы примерно вдвое. Спрос предсказуемо породил предложение – сегодня ремонтируют все кому не лень. Ремонт по оригинальным технологиям, рекомендованным производителями турбин, по-прежнему в дефиците. Организация такого специфического производства требует немалых вложений в оснащение, запчасти и подготовку кадров. Поэтому предприятий, выполняющих действительно грамотный ремонт, – единицы, а желающих заработать любым путем – множество. В такой ситуации все чаще приходится сталкиваться с ошибками, допускающимися при ремонте турбин.
Пытаясь классифицировать ремонтные косяки, можно выделить ряд причин, вследствие которых они происходят. Во-первых, это отсутствие необходимого оборудования, предусмотренного заводскими технологиями восстановительного ремонта. Как правило, дорогих стендов финишной балансировки, профессионального оборудования для очистки деталей. Во-вторых, отсутствие оборудования и/или данных для настройки устройств регулирования ТК, калибровки электронных актуаторов. Наконец, в‑третьих, отсутствие знаний и умения. Низкая квалификация персонала, которая приводит к ошибкам в сборке турбины или использованию непроверенных на практике ноу-хау. Наш ремонтник – человек творческий, что ярко подтверждается следующими «усовершенствованиями», внесенными в конструкцию турбин.
При вскрытии оригинальной грузовой турбины, подвергавшейся восстановительному ремонту (хочется добавить: …в извращенной форме), была обнаружена картина, показанная на фото 17. Колесо компрессора закрепили самопальной гайкой (видимо, родная деталь была утрачена). Это привело к аварии турбины с разрушением вала, так как значительно увеличило остаточный дисбаланс ротора, который не был устранен балансировкой.
На фото 18 представлена модифицированная версия узла подшипников. Опорные подшипники разного размера изготовлены самостоятельно. Для предотвращения их смещения в осевом направлении вместо стопорных колец использована распорная пружина.
Фото 19 демонстрирует «самоточный» вал ротора. В силу невозможности выполнить сварку трением турбинное колесо просверлили и закрепили на валу гайкой по аналогии с колесом компрессора.
У картриджа на фото 20 компрессорное колесо закреплено не гайкой, а болтом. Во что он ввернут – непонятно. Но ротор вращается!
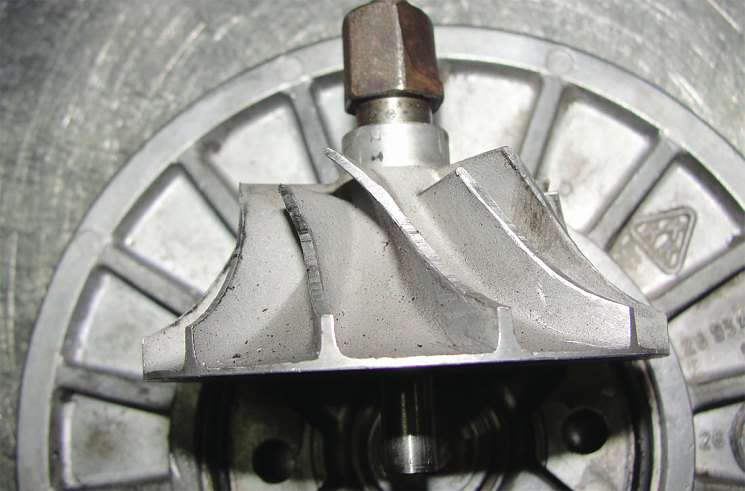
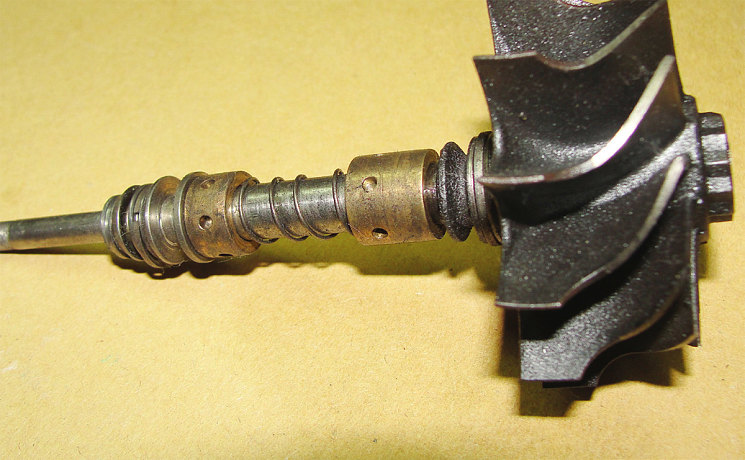
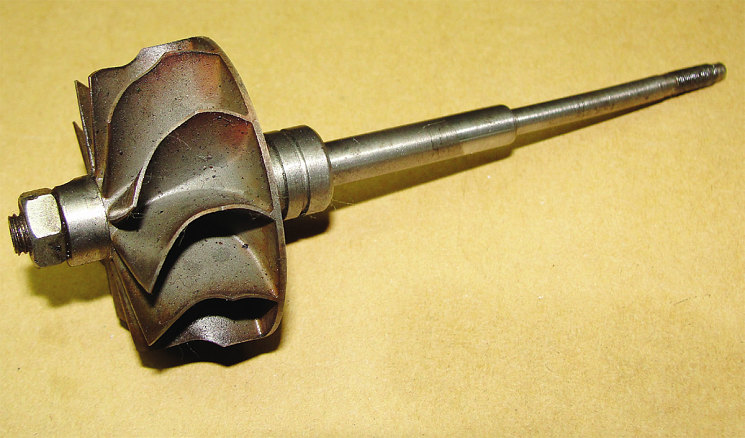
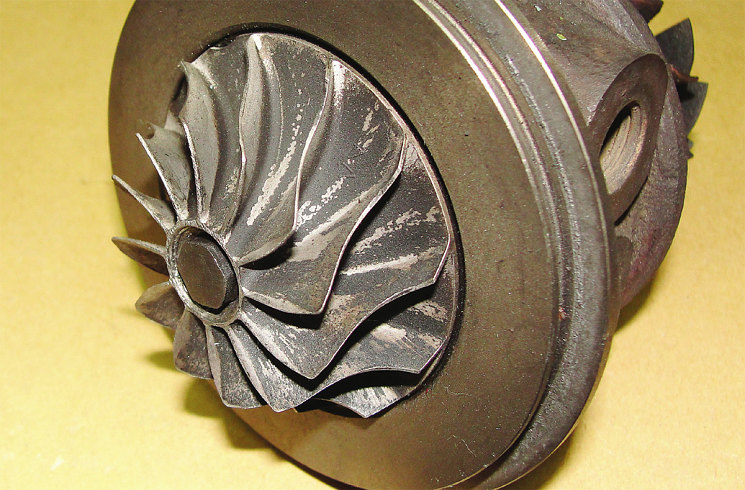
Самое интересное в этих историях то, что восстановленные таким способом турбины, прежде чем попасть на экспертизу, какое-то время работали.
Смех – смехом, но владельцам турбин, о которых шла речь выше, радости мало. Их претензии к качеству изготовления или ремонта турбин, безусловно, обоснованные. К сожалению, это не всегда гарантирует получение возмещения в том или ином виде.
Уникальную информацию по устройству, эксплуатации и ремонту систем турбонаддува смотрите на сайте turbomaster.ru