Исследуем молдинги автомобиля. Часть 2
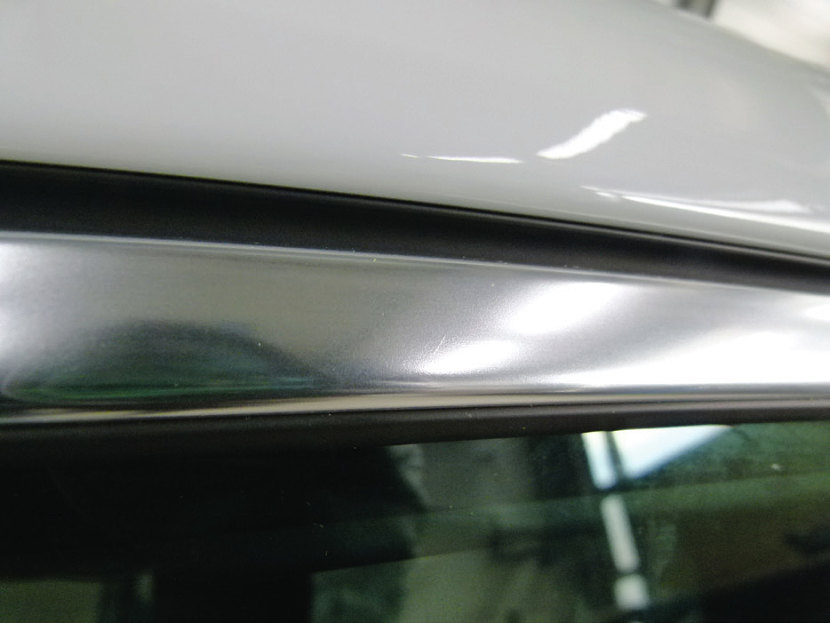
Первую часть статьи заканчивали так: «Мелкие матовые пятна удаляются с поверхности молдингов с помощью очистителя или безабразивной полировальной пасты. В наибольшей степени повреждены молдинги передних окон боковин левый и правый. Их верхние части повреждены в меньшей степени, а нижние части стали пятнистыми и матовыми в результате образования полупрозрачного слоя вещества светло-серого цвета, схожего по внешним признакам с продуктами коррозии алюминия».
Внимание. Данная статья является частью большой работы, начатой в прошлой номере журнала. Некоторая часть иллюстраций востребована в двух частях работы. Это вносит небольшой сумбур в последовательность расстановки иллюстраций. Но это не должно мешать читателю, так как каждая иллюстрация дублирует свой номер под иллюстрацией и в месте ее нахождения в тексте.
Теперь продолжаем.
В досудебной экспертизе сделан вывод, что причиной негативного изменения внешнего вида молдингов является скрытый производственный дефект – пористость внешнего слоя лака. Анализируя данный вывод, следует отметить, что в соответствии с ГОСТ 15467–79 «скрытый дефект – дефект, для выявления которого в нормативной документации, обязательной для данного вида контроля, не предусмотрены соответствующие правила, методы и средства». То есть предполагается, что наличие пор в слое лака на этапе производства молдингов не контролируется, а сам прозрачный лак наносится непосредственно на металлическую поверхность. Это утверждение требует проверки.
Для дальнейших исследований с автомобиля истца был демонтирован молдинг № 7. Молдинг имеет специальный вытянутый С-образный профиль поперечного сечения с толщиной стенки 1,2 мм. Поперечное сечение такого молдинга показано на фото 32.
Молдинг изготовлен из легкого немагнитного сплава серебристого цвета (алюминиевого сплава) методом экструзии. Молдинги имеют характерный микрорельеф наружной поверхности с нерегулярными выступами и впадинами малого размера, видимыми с помощью микроскопа и обеспечивающими отражение падающего света и блеск. Макрорельеф поверхности характерен для формирования заготовки детали методом экструзии с наличием продольных следов, образованных неровностями рабочих частей технологического оборудования (фильер, формующих отверстий).
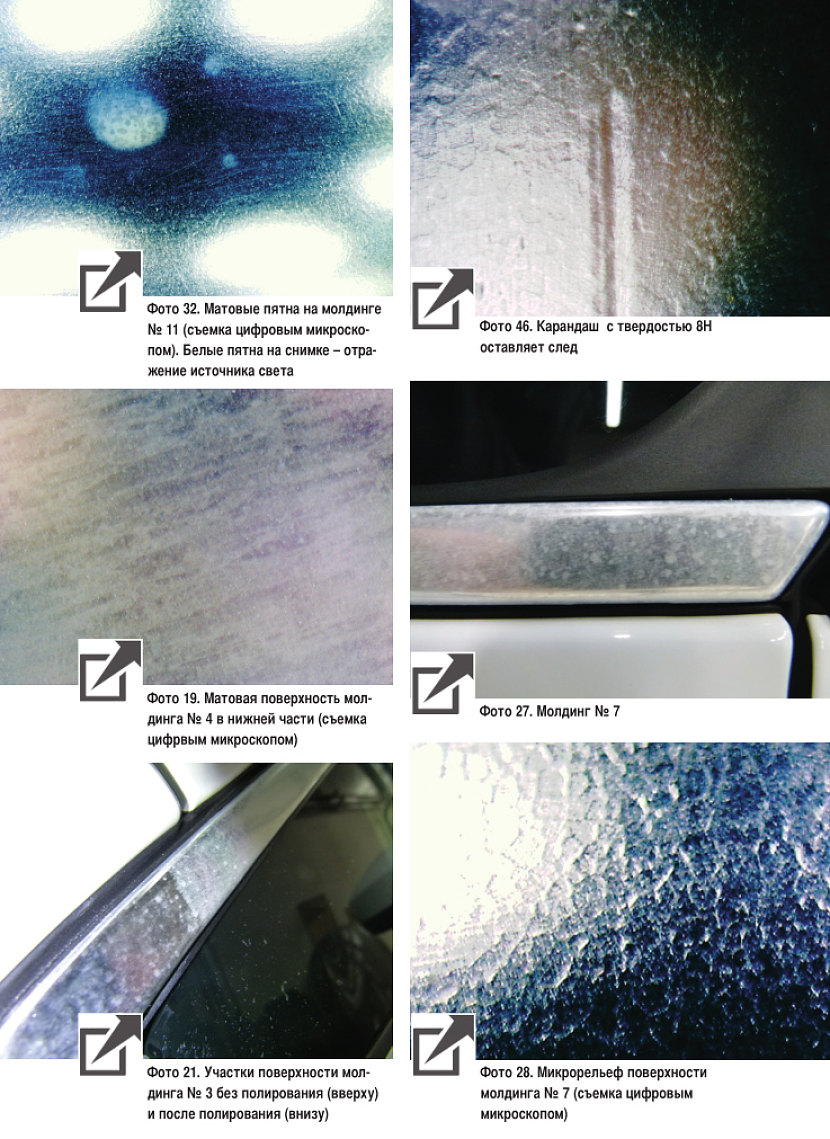
Также на поверхности сформировался рельеф, образующийся в ходе процесса растворения наружной поверхности алюминиевого сплава (фото 19, 21, 27, 28). Микрорельеф поверхности металла (сплава) виден через прозрачный поверхностный слой. На матовых участках молдингов № 3 и 4 внешний слой частично утратил прозрачность, и микрорельеф поверхности металла (сплава) виден хуже.
Следующий этап исследования проводился с целью установления наличия и свойств лака на поверхности молдинга.
Исследование твердости поверхности молдингов
Твердость материала или покрытия – свойство внешнего слоя материала или покрытия сопротивляться механическому воздействию другого объекта. На этом свойстве основаны методы определения твердости лакокрасочного покрытия, и других видов покрытий, а также самого материала детали. Для определения твердости поверхности молдингов использовался метод определения твердости по карандашу в соответствии с ГОСТ Р 54586–2011, стандартом ISO 15184: 1998.
Исследование твердости наружной поверхности молдингов автомобиля проводилось с помощью набора карандашей «KOH-I-NOOR» тип 1500 с твердостью: 6В, 5В, 4В, 3В, 2В, В, НВ, F, Н, 2Н, 3Н, 4Н, 5Н, 6Н, 7Н, 8Н, 9Н и 10Н. Карандаш с твердостью грифеля 7Н не оставляет след на поверхности молдинга, а карандаш с твердостью 8Н оставляет след (фото 46).
Результаты исследования показали, что твердость молдингов окон боковин и дверей исследуемого автомобиля соответствует параметру 7Н. Для лаков, используемых для окраски деталей автомобилей, характерна твердость от В до 2Н. У большинства автомобилей твердость слоя лака соответствует параметрам от НВ до Н. Твердость поверхности молдингов исследуемого автомобиля значительно выше и не характерна для лаков.
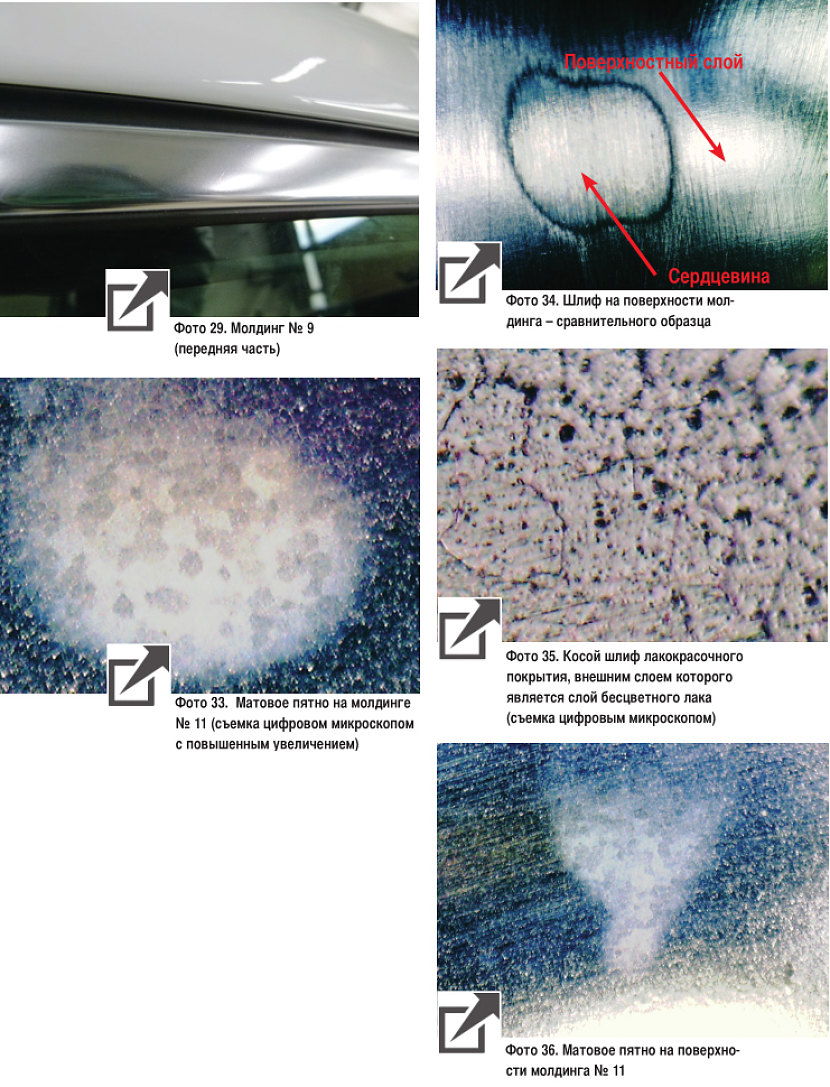
На участках образования матовых пятен светло-серого цвета твердость поверхности молдингов также составляет 7Н. На основании этого можно сделать вывод, что участки поверхности молдингов с матовыми пятнами по своей твердости не отличаются от поверхностей без пятен, появление матовых пятен светло-серого цвета не привело к снижению или повышению твердости поверхности молдингов.
Исследование наличия слоя лакокрасочного покрытия на поверхности молдинга
Важной характеристикой любого лакокрасочного покрытия является его адгезия с окрашиваемой поверхностью детали. При воздействии специальным образом заточенной стальной препаровальной иглой вдоль окрашенной поверхности лакокрасочное покрытие или отслаивается, или разрушается с образованием мелких фрагментов в зависимости от того, какую величину имеют адгезионные и когезионные связи. Методика такой оценки адгезии лакокрасочного покрытия описана в книге «Экспертиза технического состояния и причины неисправностей автомобильной техники». При исследовании молдинга автомобиля с помощью препаровальной иглы было установлено, что слой лака на поверхности молдингов отсутствует, так как разрушение и отслаивание какого-либо лакокрасочного покрытия не происходит.
Разрешение на применение разрушающих методов исследования в отношении автомобиля истца судом не было дано. Поэтому использовался молдинг такого же автомобиля, поврежденного в ДТП и находившегося в техническом центре (молдинг – сравнительный образец). Сравнительный образец имеет такую же конструкцию, как и молдинг автомобиля истца, такой же микрорельеф наружной поверхности, такую же твердость.
Для дальнейшего исследования от молдинга – сравнительного образца был отрезан фрагмент длиной 148 мм, и один его конец был помещен в стеклянный лабораторный стакан с растворителем «646». Глубина погружения исследуемого образца в растворитель составляла около 25 мм. При длительном действии растворителя должно произойти изменение свойств лакокрасочного покрытия. Последствия длительного воздействия органического растворителя на лакокрасочное покрытие описано в книге «Экспертиза технического состояния и причины неисправностей автомобильной техники».
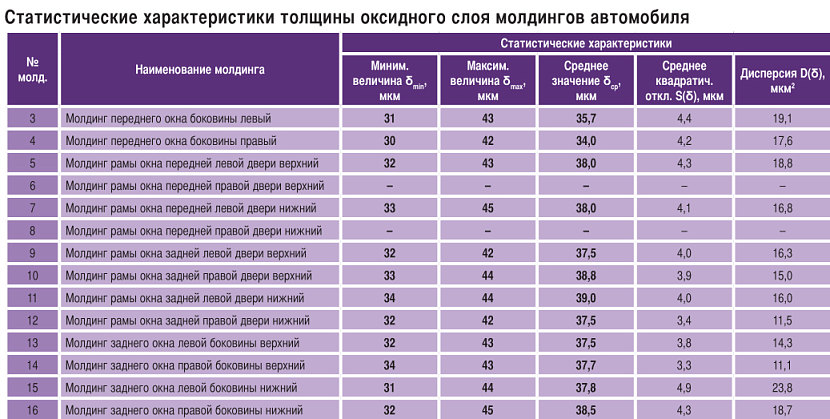
Исследуемый образец находился в сосуде с растворителем в течение 24 часов. Через интервалы времени 3 часа, 12 часов и спустя 24 часа образец извлекался из растворителя, просушивался, осматривалась его поверхность и проверялась твердость. Осмотр проводился с различных дистанций и с применением микроскопа. При наличии на поверхности молдинга слоя лака или иного лакокрасочного покрытия в среде растворителя будет происходить вспучивание покрытия, т. е. набухание покрытия и значительное снижение его твердости (примерно на 4 единицы).
При этом кардинально изменяется характер следа от карандаша. Если изначально карандаш оставляет вдавленный след на лакокрасочном покрытии, то после воздействия растворителя грифель карандаша не деформирует, а разрушает покрытие и отделяет его фрагменты.
При осмотре образца, подвергнутого длительному воздействию растворителя (от 3 до 24 часов), было установлено, что признаки набухания отсутствуют – контур по границе участка, подвергнутого воздействию растворителя, не образовался. Проверка твердости поверхности молдинга на участке, подвергнутом длительному действию растворителя, и на участке, не подвергавшемся действию растворителя, показала, что на обоих участках твердость поверхности молдинга соответствует параметру 7Н.
Исследование поверхности молдинга-сравнительного образца с помощью микроскопа показало, что микрорельеф поверхности молдинга на участке, подвергнутом длительному действию растворителя, и на участке, не подвергавшемся действию растворителя, идентичен. Таким образом, длительное действие растворителя (до 24 часов) не выявило наличие слоя лакокрасочного покрытия на поверхности молдинга – сравнительного образца. Так как молдинг-сравнительный образец и молдинги исследуемого автомобиля по всем параметрам идентичны, то можно утверждать, что на молдингах автомобиля истца слой лака отсутствует.
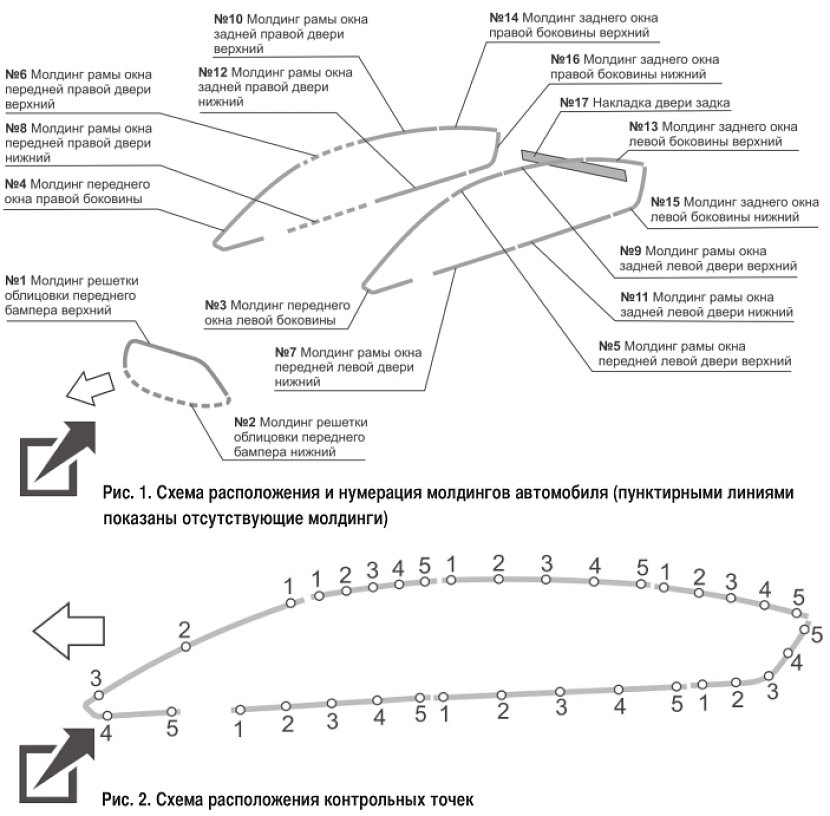
На молдинге – сравнительном образце на его внешней поверхности с помощью абразивных материалов зернистостью от Р500 до Р2000 вручную без применения высокоскоростного механического шлифования были сделаны шлифы (фото 34).
В шлифах отчетливо видно, что на поверхности молдинга имеется слой с иными внешними признаками по сравнению с сердцевиной. В процессе ручного шлифования ощущается, что внешний слой имеет большую твердость по сравнению с сердцевиной. На молдинге – сравнительном образце был методом ручного шлифования удален внешний слой на участке длиной около 20 мм. Высокоскоростное механическое шлифование не применялось, чтобы исключить возможность действия высокой температуры.
На завершающем этапе поверхность была отшлифована абразивом зернистостью Р2000. После шлифования поверхность была гладкая, блестящая, с мелкими прямолинейными, взаимно параллельными рисками от абразивной отработки, направленными в одну сторону. Твердость материала молдинга на отшлифованном участке проверялась методом карандаша. Для более четкой фиксации результатов движение грифеля карандаша происходило в направлении, перпендикулярном направлению рисок от шлифования.
Проверка показала, что твердость материала молдинга на зашлифованном участке соответствует параметру 4Н. Таким образом, было установлено, что внешний слой молдинга имеет более высокую твердость (7Н) по сравнению с сердцевиной (4Н).
Слой прозрачного бесцветного лака, при его наличии, плохо различим при визуальном контроле. Наличие или отсутствие слоя лака может быть определено в результате исследования косого шлифа. Такой метод применяется при исследовании структуры лакокрасочного покрытия. Методика приготовления и исследования косого шлифа описана в книге по экспертизе, приведенной в списке литературы.
Для примера на фото 35 показан косой шлиф лакокрасочного покрытия, внешним слоем которого является бесцветный лак.
На фотографии в шлифе отчетливо виден прозрачный слой лака и непрозрачные слои лакокрасочного покрытия.
Такой метод был применен при исследовании молдинга с целью определения наличия или отсутствия слоя лака. На молдинге – сравнительном образце был сделан косой шлиф.
Исследование шлифа молдинга показало, что на всей его плоскости виден только металлический сплав, слой лака на поверхности молдинга отсутствует (фото 36).
Таким образом, комплекс проведенных исследований молдингов автомобиля истца и молдинга – сравнительного образца показал, что на поверхности молдингов слой лака отсутствует. Поэтому появление матовых пятен на молдингах не может быть следствием производственного дефекта, связанного с нарушением технологии их окрашивания и низкого качества лака.
Алюминиевые молдинги окон боковин и дверей кузова автомобиля не имеют лакокрасочного покрытия (слоя лака), а обработаны методом анодного окисления металла (анодирования). Анодное окисление металла (анодирование) – электрохимический процесс формирования слоя оксида алюминия Al2O3 на поверхности детали, изготовленной из алюминиевого сплава, в кислотном электролите. В процессе обработки деталь является анодом (+). При прохождении электрического тока между катодом и анодом на поверхности детали образуется оксид алюминия, слой которого в процессе обработки увеличивается. Основными параметрами технологического процесса анодирования, влияющими на качество сформированного слоя, являются: состав электролита, температура электролита, плотность тока.
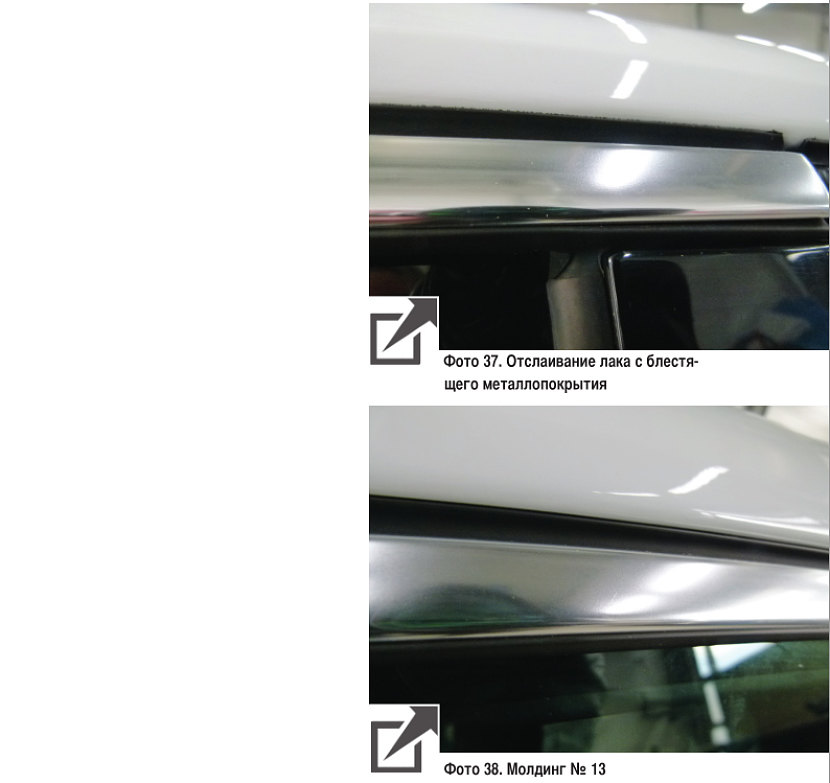
В процессе анодирования при увеличении толщины оксидного слоя одновременно происходит частичное растворение наружной поверхности. Соотношение скорости роста толщины оксидного слоя и скорости его растворения зависит от режимов процесса анодирования, главным образом от температуры электролита.
Анодирование может проводиться без окрашивания и с окрашиванием детали. Молдинги исследуемого автомобиля имеют естественный цвет алюминиевого сплава и, следовательно, не окрашены. В автомобильной промышленности для такой анодной обработки применяется процесс низкотемпературного (холодного) анодирования. При этом оксидный слой получается большой толщины (около 20…100 мкм) (ГОСТ 9.303–84), высокой твердости, прозрачный, гладкий, он обладает достаточно хорошим блеском.
Твердость анодного слоя при низкотемпературном анодировании существенно выше, чем твердость самого алюминиевого сплава. При анодировании при повышенной температуре электролита анодный слой получается рыхлым и обладает малой твердостью. Исследования твердости поверхностного слоя, проведенные в отношении молдингов автомобиля истца и молдинга – сравнительного образца, показали, что твердость алюминиевого сплава соответствует параметру 4Н, а твердость наружной поверхности молдингов – 7Н.
Такая разница в твердости свидетельствует о том, что на поверхности молдингов сформирован более твердый слой. Это подтверждает наличие на поверхности молдингов слоя оксида алюминия, который имеет значительно большую твердость по сравнению с алюминием и его сплавами. Это же свидетельствует о том, что процесс оксидирования проводился при пониженных температурах. В местах образования матовых пятен на молдингах передних окон боковин исследуемого автомобиля (молдинги № 3 и 4) твердость поверхности также соответствует параметру 7Н, т. е. в процессе изготовления молдингов на этих участках также сформирован такой же по твердости оксидный слой.
С помощью микроскопа через прозрачный, бесцветный поверхностный слой оксида алюминий виден микрорельеф поверхности металла с неровностями, образовавшимися в процессе растворения материала при анодной обработке. Такое свойство анодированной детали соответствует нормам табл. 15 ГОСТ 9.301–86 и ГОСТ 9.303–84. Цвет молдингов на неповрежденных участках равномерный светло-серый, что соответствует нормам табл. 15 ГОСТ 9.301–86.
Сформированный на поверхности детали слой оксида алюминия является стойким к действию кислот и щелочей. Однако непосредственно после операции анодирования оксидный слой является пористым (ГОСТ 9.303–84) и представляет собой структуру, состоящую из множества полых трубок с соединенными друг с другом оболочками, а также барьерного слоя (рис.1).
Диаметр пор (каналов внутри трубок) составляет около 0,01…0,03 мкм (0,00001…0,00003 мм). Толщина стенок трубок составляет 0,01…0,02 мкм (0,00001…0,00002 мм). Толщина оксидного слоя, сформированного методом анодного окисления, составляет от 20 до 100 мкм (0,02…0,10 мм). Таким образом, длина трубок значительно (в тысячи раз) больше их поперечного размера и размера пор. Несмотря на малый размер поперечного сечения пор, агрессивные вещества способны проникать в них. Барьерный слой не обеспечивает надежной защиты от внешней среды. Поэтому после анодной обработки проводится операция наполнения покрытия или уплотнения оксидного слоя.
Эта операция проводится обработкой детали в горячей диминерализованной воде (кипящей или близкой к температуре кипения), или в среде водяного пара, или специальными химическими средствами. При взаимодействии оксида алюминия Al2O3 с водой образуется гидроксид алюминия Al(ОН)3. Он обладает большим объемом и заполняет поры, препятствуя проникновению в них агрессивной среды. Таким образом, наполнение покрытия, заполнение опор существенно повышает коррозионную защиту алюминиевого сплава детали.
Исследование толщины поверхностного слоя на алюминиевых молдингах
Оксид алюминия является диэлектриком, поэтому толщина его слоя может быть определена неразрушающими методами с помощью толщиномера. Толщина оксидного слоя молдингов окон боковин и дверей измерялась толщиномером в соответствии с ГОСТ. Толщина слоя определялась как средняя величина по результатам трех параллельных измерений в каждой контрольной точке с округлением до целых значений микрометра. Схема расположения контрольных точек при измерении толщины оксидного слоя молдингов представлена на рис. 2.
По результатам измерений получены статистические характеристики толщины оксидного слоя молдингов, представленные в таблице.
Анализ статистических характеристик толщины оксидного слоя показывает, что на наружных поверхностях молдингов исследуемого автомобиля толщина оксидного слоя лежит в пределах от 30 до 45 мкм. Такой диапазон изменения локальной толщины оксидного слоя является характерным для операции оксидирования деталей из алюминиевых сплавов. Разброс параметра составляет 15 мкм, что свидетельствует о стабильности технологического процесса анодирования.
В соответствии с ГОСТ 9.031–74 минимальная толщина анодно-оксидного слоя для различных типов коррозионной агрессивности атмосферы по ГОСТ 9.039, в условиях в которых эксплуатируется изделие, лежит в диапазоне от 15 до 25 мкм. Толщина анодно-оксидного слоя молдингов исследуемого автомобиля соответствует требованиям ГОСТ 9.031–74.
Толщина оксидного слоя одинаковая на поврежденных и на неповрежденных участках молдингов. Следовательно, причиной появления матовых пятен на молдингах не является недостаточная толщина оксидного слоя. Твердость оксидного слоя на поврежденных и на неповрежденных участках молдингов также одинаковая и соответствует твердости 7Н.
Операция оксидирования и операция наполнения покрытия, т. е. заполнения пор оксидного слоя, проводятся в промышленности на заданных стабильных технологических режимах (температура, рабочая среда, длительность обработки, плотность тока). Все процессы автоматизированы, в том числе и процесс наполнения покрытия и формирования таким способом защитных свойств оксидного слоя. Это создает объективные условия для обеспечения стабильного качества продукции.
Если были заданы неверные режимы технологического процесса, при которых не обеспечиваются защитные свойства оксидного слоя, то повреждения в виде матовых пятен возникли бы у всех молдингов автомобиля, обработанных по одинаковой технологии, и тем более не было бы резкого различия степени повреждения в пределах одного и того же молдинга. Однако у исследуемого автомобиля наблюдается высокая степень неравномерности распределения матовых пятен на поверхностях молдингов.
При осмотре молдингов установлено, что повреждения в виде матовых пятен светло-серого цвета возникли в нижней части молдингов передних окон боковин (молдинги № 3 и 4). Участки повреждения в нижней части молдингов № 3 и 4 составляют 65…70% площади, а в верхней и средней части этих молдингов – 6…11%. На нижних молдингах рам окон дверей, на нижних молдингах задних окон боковин матовые пятна присутствуют в значительно меньшем количестве, и размер их гораздо меньше (0,2…1,5 мм). На верхних молдингах рам окон дверей и задних окон боковин матовые пятна отсутствуют. Таким образом, установлено, что повреждения молдингов имеют существенные различия по степени интенсивности.
Нижняя часть молдингов передних окон боковин (молдинги № 3 и 4) приобрела матовый пятнистый вид. На верхних частях этих молдингов образовались только отдельные матовые пятна малого размера. На других молдингах также имеются только отдельные пятна малого размера или пятна отсутствуют вообще. Это является важным фактом для установления причины возникновения повреждений молдингов.
Если молдинги прошли анодную обработку по одинаковой технологии и эксплуатируются в одинаковых условиях, т. е. подвергаются одинаковым воздействиям внешней среды, то и повреждения их не будут существенно отличаться. Сильные различия в степени повреждений молдингов в виде образования матовых пятен могут объясняться различием условий их эксплуатации, различием воздействия на них внешней среды.
Гидроксид алюминия Al(ОН)3, который закрывает поры оксидного слоя, нерастворим в воде и, следовательно, пригоден для использования в качестве защиты от воздействия внешней среды в обычных условиях эксплуатации автомобиля. Такая же обработка (оксидирование) применяется не только для декоративных элементов автомобилей, но и для деталей из алюминиевых сплавов, используемых в авиации, строительстве, машиностроении и других областях. Однако гидроксид алюминия, стойкий к воздействию воды, взаимодействует с некоторыми кислотами, например, соляной кислотой HCl, плавиковой кислотой НF, а также с растворами щелочей, например, NaOH, т. е. не обладает стойкостью к воздействию этих химических соединений.
Для проверки действия кислотной среды на поверхностный слой молдинга фрагмент молдинга – сравнительного образца был помещен в слабый раствор серной кислоты (около 1,4%). Через 14 суток поверхность образца приобрела матовый вид. Таким образом, длительное действие слабого кислотного раствора приводит к появлению матовой поверхности молдинга.
Причиной образования матовых пятен на поверхностях молдингов могло явиться действие агрессивных химических веществ.
Защитные и защитно-декоративные покрытия, применяемые в автомобильной промышленности, не способны обеспечивать абсолютную защиту металла деталей от воздействия любых химических веществ. Какое конкретно химическое вещество воздействовало на нижние части молдингов № 3 и 4 и в значительно меньшей степени оказывало воздействие на верхние части этих же двух молдингов, а также на все остальные молдинги кузова автомобиля, не представляется возможным определить методами автотехнической экспертизы.
Молдинги при их массовом и крупносерийном производстве проходят процесс анодной обработки и наполнения покрытия, в результате чего формируются их защитные свойства. Эти процессы в автомобильной промышленности автоматизированы и проходят на стабильных режимах или на режимах с закономерно изменяемыми параметрами в соответствии с заданными алгоритмами. В результате таких процессов формируется стабильный уровень качества. Если заданы ненадлежащие технологические режимы обработки, то в этом случае все молдинги, проходящие такую анодную обработку, будут иметь низкое качество с низкими защитными свойствами.
У исследуемого автомобиля наблюдается резкое различие в степени повреждений молдингов. Некоторые молдинги вообще не имеют повреждений, а два одинаково расположенных молдинга имеют сильные изменения декоративных свойств, но при этом только в своей нижней части. Верхние их части повреждены значительно меньше. Это свидетельствует о том, что имелись различия условий, в которых находились молдинги, различия воздействия на них химических веществ.
В соответствии с ГОСТ 15467–79 производственным дефектом является несоответствие требованиям нормативной документации на изготовление или поставку продукции. Так как некоторые молдинги автомобиля сохранили свои декоративные свойства, а некоторые – в значительной степени утратили декоративные свойства и при этом не по всей поверхности, а только в своей нижней части, то основания для вывода о производственном дефекте молдингов кузова исследуемого автомобиля отсутствуют. Причиной возникновения пятен светло-серого цвета на наружной поверхности анодированных алюминиевых молдингов автомобиля является внешнее воздействие агрессивного вещества. Такая причина возникновения повреждений классифицируется как эксплуатационная. Основания для вывода о производственном дефекте молдингов кузова автомобиля отсутствуют.
Такой вывод и был сделан по результатам проведенного исследования.
На основе изучения и оценки заключения эксперта и всех других материалов дела апелляционный суд отменил решение суда первой инстанции и в иске отказал.
В досудебной экспертизе был сделан вывод, что «причиной негативного изменения внешнего вида является скрытый производственный дефект – пористость внешнего слоя лака». В действительности никакого лака на молдингах нет. Однако следует сказать, что у некоторых моделей автомобилей на детали наносится декоративное блестящее металлопокрытие, а сверху – слой лака. Пример повреждений и негативного изменения внешнего вида детали, изготовленной по такой технологии, показан на фото 37–38.
В данном примере ручка двери изготовлена из полимерного материала. На ее внешнюю поверхность нанесено блестящее металлопокрытие, а затем слой бесцветного лака. На неповрежденных участках поверхность ручки блестящая. На отдельных участках произошло механическое разрушение слоя лака, механическое повреждение блестящего металлопокрытия, слой лака стал отслаиваться от поверхности металлопокрытия и образовались матовые участки. На фотографиях заметны участки отслаивания лака, четко видны границы слоя лака. Но это уже другой пример, другой автомобиль и другая экспертиза.
Литература
ГОСТ 9.311–87. Единая система защиты от коррозии и старения. Покрытия металлические и неметаллические неорганические. Метод оценки коррозионных поражений.
ГОСТ 28246–2017. Материалы лакокрасочные. Термины и определения.
ГОСТ 9.032–74. Единая система защиты от коррозии и старения. Покрытия лакокрасочные. Группы, технические требования и обозначения.
ГОСТ 9.072–2017. Единая система защиты от коррозии и старения. Покрытия лакокрасочные. Термины и определения.
ГОСТ 9.407–2015. Единая система защиты от коррозии и старения. Покрытия лакокрасочные. Методы оценки внешнего вида.
ГОСТ 9.302–88. Единая система защиты от коррозии и старения. Покрытия металлические и неметаллические неорганические. Методы контроля.
ГОСТ 15467–79. Управление качеством продукции. Термины и определения.
ГОСТ Р 54586–2011. Материалы лакокрасочные. Метод определения твердости покрытия по карандашу.
ГОСТ 9.303–84. Единая система защиты от коррозии и старения. Покрытия металлические и неметаллические неорганические. Общие требования к выбору.
ГОСТ 9.301–86. Единая система защиты от коррозии и старения. Покрытия металлические и неметаллические неорганические. Общие требования.
ГОСТ 9.031–74. Единая система защиты от коррозии и старения. Покрытия металлические и неметаллические неорганические. Общие требования и методы контроля (с изменениями).
ГОСТ 31993–2013. Материалы лакокрасочные. Определение толщины покрытия.
ГОСТ 9.039–74. Единая система защиты от коррозии и старения. Коррозионная агрессивность атмосферы.
Тихонов В. Н. Аналитическая химия алюминия. М.: Наука, 1971.
Дроздовский В. Б., Лосавио С. К. Хрулев А. Э. Экспертиза технического состояния и причины неисправностей автомобильной техники. М.: Изд-во АБС, 2019.