Леонардо был бы доволен
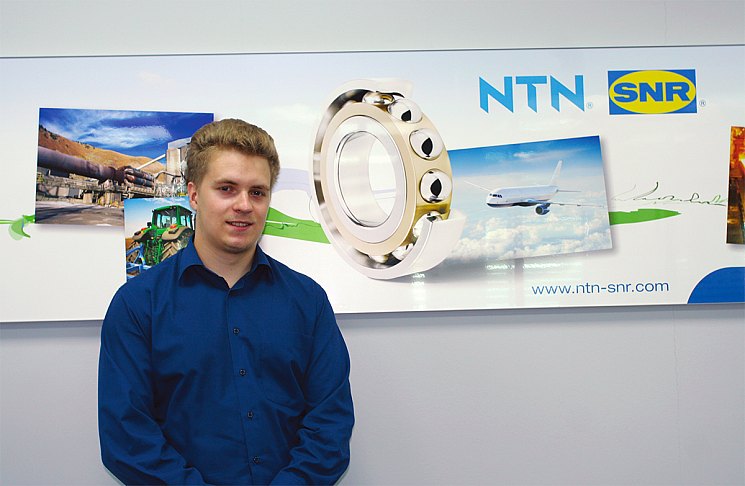
Встреча с техническим специалистом предприятия, работающего на автосборочное производство, для редакции всегда представляет значительный интерес. Особенно, если это компания мирового уровня и занимается разработкой и поставкой продукции узкого спектра на конвейеры очень многих мировых грандов автомобилестроения. Сегодняшний случай из таких. Мы побеседовали с Павлом Сорочинским, техническим специалистом компании NTN – SNR. В результате несложный разговор о продукции компании перерос в профессиональный анализ этапов трансформации простых колесных подшипников в интегрированные сложные узлы автомобильной трансмиссии. Вот как это было.
Редакция (АБС): Павел, если можно, расскажите коротко об истории компании.
– Компания NTN – SNR образовалась в результате слияния двух компаний: японской NTN и французской SNR. Произошло это в 2010 году. До этого почти 100 лет каждое предприятие работало самостоятельно. NTN – SNR входит в тройку крупнейших производителей подшипников в мире по совокупному объему выпуска и является мировым лидером в производстве подшипников для автомобилей. Коньком производственной программы мы считаем колесные, или ступичные, подшипники.
Есть и другой ассортимент, в который входят: ролики ГРМ и доп. оборудования, как натяжные, так и обводные, подшипники кпп, в том числе выжимные, подшипники верхних опор амортизаторов, шкивы колен валов. Начнем разговор со ступичных подшипников.
Если обратиться к истории вопроса, то специалисты технической мысли считают изобретателем первого прототипа подшипника Леонардо да Винчи. В одном из своих многочисленных технических рисунков он это отобразил. Если иметь в виду, что гений эпохи возрождения творил в XV веке, то мы вправе считать, что возраст этой детали составляет более 500 лет.
АБС: Сколько лет автомобильному подшипнику, какой путь он прошел с момента рождения и какие этапы модернизации претерпевал за свой век?
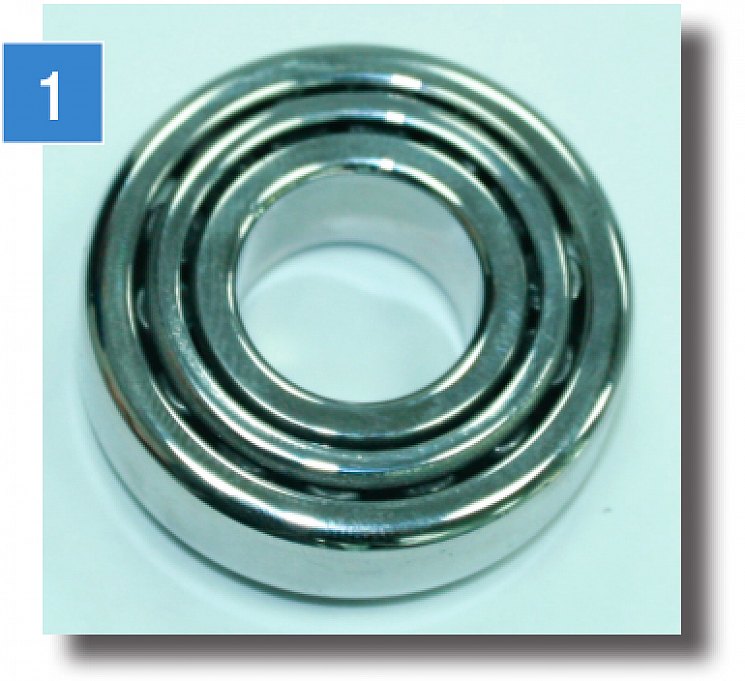
– О рождении автомобильного подшипника скажу чуть ниже. А всякую принципиально новую конструкцию этой детали мы обозначаем как новое поколение. Сегодня их четыре. Начнем с так называемого нулевого поколения. Оно характеризуется однорядной роликовой или шариковой конструкцией подшипников (фото 1). Элементы детали состоят из разборных (в случае роликового (конического подшипника) наружных и внутренних колец, сепаратора и тел качения. Один ступичный узел состоит из двух однорядных разборных подшипников. Это самый простой тип подшипников, которые применялись на самых первых моделях автомобилей. Время их появления совпадает с эпохой рождения первого автомобиля: конец XIX – начало XX века. Такие подшипники и поныне исправно служат в конструкциях некоторых транспортных средств.
К существенному недостатку данной конструкции следует отнести повышенные требования к квалификации механиков, устанавливающих такие подшипники. Монтаж их должен производиться при строгом нормировании усилий затяжки на крепежных элементах. В перечень работ по монтажу и обслуживанию входят и регулировочные процедуры. Отклонения от норм может быть чревато серьезными последствиями на дороге.
Поколение 1 ознаменовано появлением двухрядного подшипника в одном корпусе (фото 2). Его еще называют картриджным или кассетным. Он может быть как шариковым, так и роликовым. Конструктивно он характеризуется двумя внутренними кольцами и двумя рядами тел качения в одном корпусе. Такая конструкция гораздо проще при установке и не требует от исполнителя специальных знаний и повышенного внимания. Смонтированный подшипник просто фиксируется на оси болтом или гайкой с нормированным усилием. На автосборку такие детали стали поступать в 50-х годах прошлого века. Многие из них добросовестно трудятся в подвесках автомобилей и сегодня.
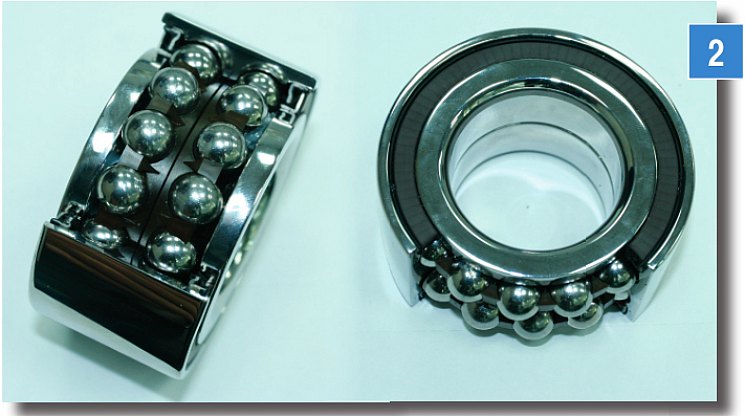
Поколение 2 связано с принципиально новой конструкцией ступичных подшипников (фото 3). В нем наружное кольцо имеет фланец, которым оно крепится к поворотному кулаку автомобиля. Этот эволюционный виток связан с началом применения в конструкции транспортных средств поворотных кулаков, изготовленных из алюминиевых сплавов. При таких технических решениях традиционный способ фиксации подшипника в кулаке с помощью запрессовки уже не подходил. Коэффициенты теплового расширения легированной стали подшипника и алюминиевого сплава поворотного кулака существенно отличаются. Под воздействием температуры такое соединение теряло надежность со всеми вытекающими. Чтобы решить эту проблему, был разработан новый тип подшипника. В нем фиксация подшипника и поворотного кулака осуществлялась с помощью резьбового соединения и не зависела от температурных факторов рабочей среды узла. Такие разработки появились в 80-х годах XX века.
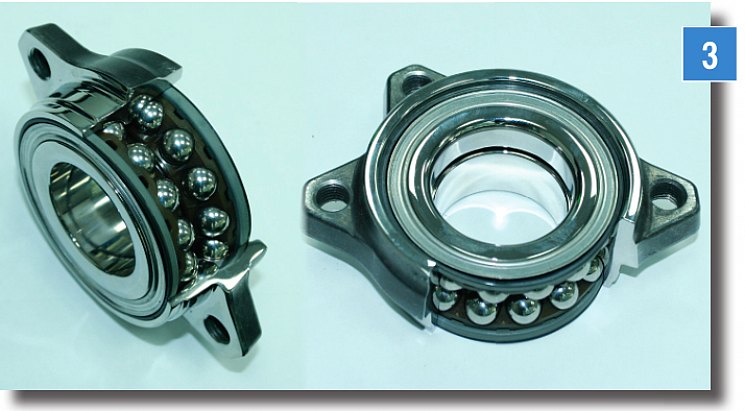
Следующий эволюционный виток в конструкции подшипника реализовался, по сути, как продолжение перехода от 1-го поколения ко 2-му. Только реализованного в другой идеологии и конструкции (фото 4). Поэтому ее условно называют поколение 2.1. В таком образце прекрасно прослеживается направление конструкторской мысли в сторону оптимизации количества элементов, составляющих узел «подшипник – поворотный кулак». В этой разработке внутреннее кольцо подшипника и ступица становятся одной деталью. Такая конструкция позволила существенно понизить и массу, и габариты узла, а также уменьшить количество деталей, из которых он состоит. История появления этого образца в автосборке относится к концу 1980-х – началу 1990-х годов.
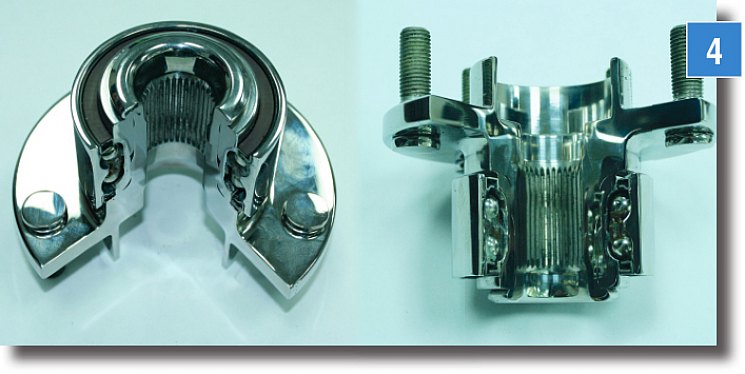
В связи с последним изобретением следует отметить определенный нюанс для автосервиса. Он состоит в том, что данное изделие не так просто устанавливается на автомобиль. Как правило, монтаж подшипника на ступицу производится с помощью запрессовки.
При проведении таких работ применяется общее правило. Оно состоит в том, что при запрессовке подшипника усилия следует прикладывать к тому кольцу, которое в данный момент запрессовывается. Если правилу не следовать и прикладывать силу не к тому кольцу, то усилия запрессовки будут передаваться через тела качения (шарик, ролик). Твердость поверхностей дорожек качения неоднородна. Если при запрессовке воздействовать на внутреннее кольцо через наружное или наоборот, то на дорожках качения можно оставить вмятины, которые в дальнейшем выведут из строя подшипник.
Указанное правило по монтажу подшипников появилось давно и ни у кого не вызывает вопросов в обычных случаях. С подшипником, о котором идет речь, ситуация иная. Применять к нему традиционное правило не представляется возможным без специального инструмента. И он у нас есть. Производит его наш инструментальный партнер HAZET. Эта компания производит также специнструмент для автомобильных конвейеров, где используется наша продукция.
Дальнейшие эволюционные шаги конструкторов автомобильных деталей привели к появлению на рынке представителей поколения 3. В нем легко узнаваем тот же интеграционный процесс по сокращению количества элементов, составляющих тот же узел «подшипник – поворотный кулак» (фото 5). Особенностью этого образца является соединение в единую деталь нескольких элементов узла: обоих подшипников, ступицы и фланца. Таким образом, отпала необходимость в производстве нескольких работ при сборке автомобиля. К такой конструкции производители повсеместно подошли в начале XXI века, хотя стоит отметить, что изобретена она была в 80-х годах. Но эволюция подшипника на этом не остановилась.
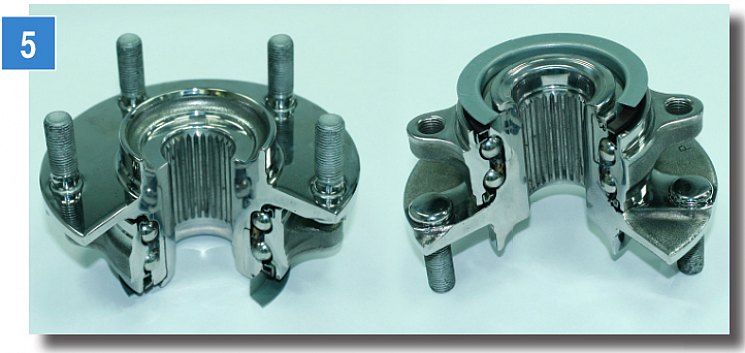
Последним конструкторско-технологическим решением стал образец изделия, включивший подшипниковый узел и тормозной диск (фото 6). Такая разработка является неразборной, и при выходе из строя любой части появляется необходимость замены всего изделия целиком. Это, вероятно, не очень устраивает автовладельца, но тенденции последнего десятилетия в мировом автопроме однозначно указывают нам путь на углубление интеграционных технологий в конструировании систем автомобиля. Агрегаты укрупняются и усложняются. Конечно, производителей транспортных средств (ТС) это устраивает: уменьшается количество единиц деталей, из которых собирается автомобиль. Значительно снижается и количество операций на конвейере. Все это удешевляет производство транспортных средств.
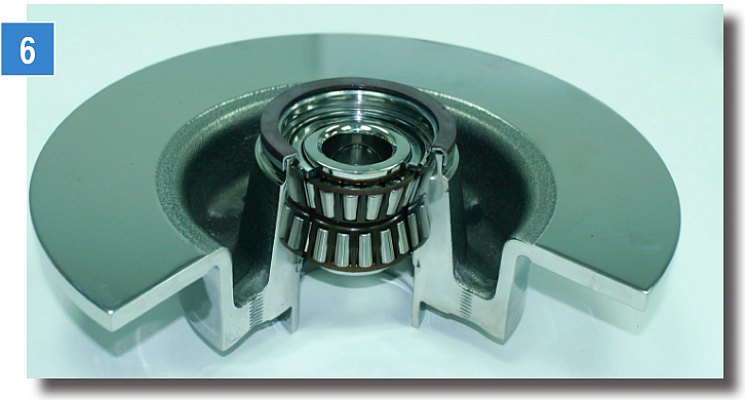
Стимулируется этот процесс путем делегирования производителем автомобиля части полномочий по разработкам изделий и узлов поставщикам комплектующей продукции. На примере эволюции продукции нашей компании этот процесс легко отслеживается. Кстати, последний продукт, о котором говорили – тормозной диск с интегрированным подшипником – является наглядным образцом подобных решений. Попутно отмечу, что наша компания является эксклюзивным поставщиком такой детали на мировые конвейеры.
АБС: А как происходит разработка подшипника для новой модели автомобиля?
– Международная статистика говорит о том, что новый автомобиль разрабатывается около семи лет. Подшипники для него конструируются в течение трех лет. Это очень длительный процесс, и связан он с многочисленными согласованиями, изготовлением прототипов, испытаний и т. д.
Прототипы при необходимости дорабатываются, вновь испытываются, и так до выхода готового продукта.
Далее следует предсерийное производство, отладка системы контроля качества – это самое важное на любом производстве. И только после всех этих многочисленных этапов продукт поступает в серию.
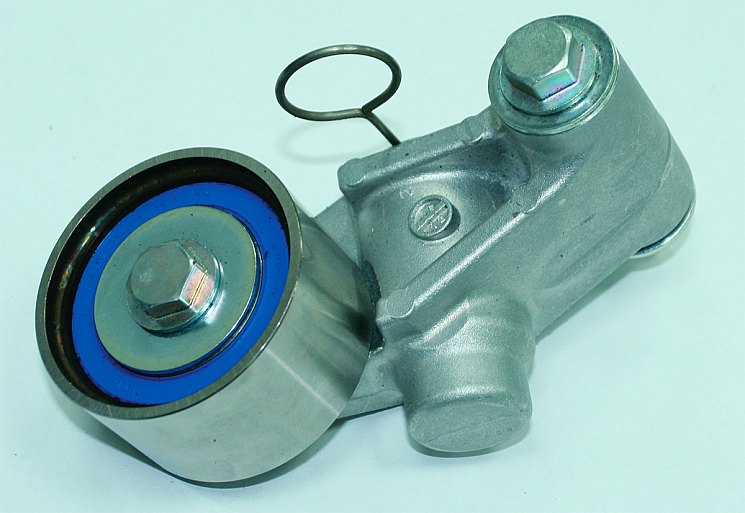
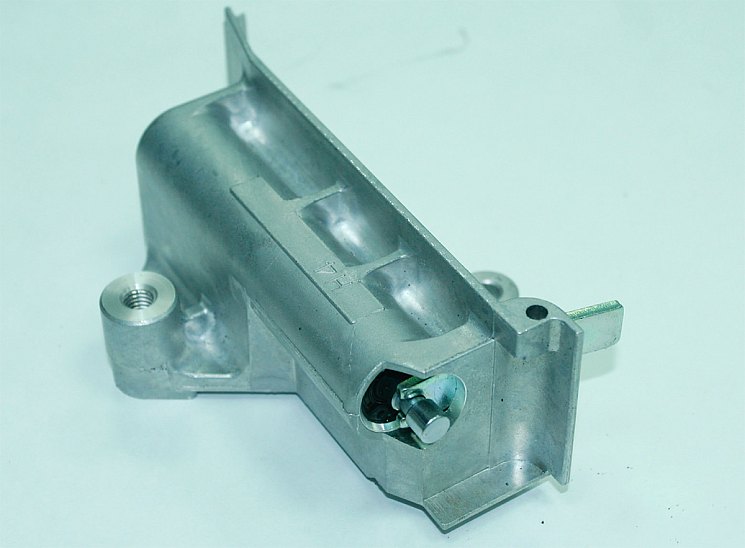
АБС: Расскажите поподробней о продукции компании.
– Если вернуться к началу статьи, следует сказать, что продуктовая линейка объединенной компании NTN – SNR довольно широка. Она сложилась из двух ассортиментных групп, которые имели оба предприятия на момент интеграции. Пересечения номенклатуры тогда составляли лишь 5%. И это считалось сильной стороной объединения двух производителей. Такие различия в ассортименте объясняются двумя факторами. До слияния каждое предприятие работало на разные рынки: SNR как европейская компания работала в Европе, Африке и Южной Америке, а NTN, как японская – в тихоокеанском регионе, Северной Америке и в Азии. Поэтому у них были разные клиенты и, соответственно, разные продукты. Я уже говорил об этом в начале нашей беседы.
Полезно отметить, что автомобильные подшипники имеют часто существенные отличия от промышленных аналогов. По сути, каждый образец такой линейки является уникальным и может быть разработан только под одну модель автомобиля. Поэтому они не попадают в универсальные справочники размерностей промышленных образцов.
Для примера возьмем продукцию нашей компании – подшипник для коробки передач (фото 7). Параметры любого подшипника определяет диаметр оси, на которой он работает. Наш подшипник имеет внутренний размер, равный 100 мм. А внешний – 130 мм. Смотрим универсальный справочник промышленных подшипников (фото 8). Минимальный внешний размер изделия с внутренним диаметром 100 мм составляет 125 мм. И это при том, что максимальные допустимые нагрузки, которые выдерживает этот образец, составляют всего около 20 N. Ближайший аналог, допускающий усилия до 44 N, имеет внешний размер уже 150 мм!
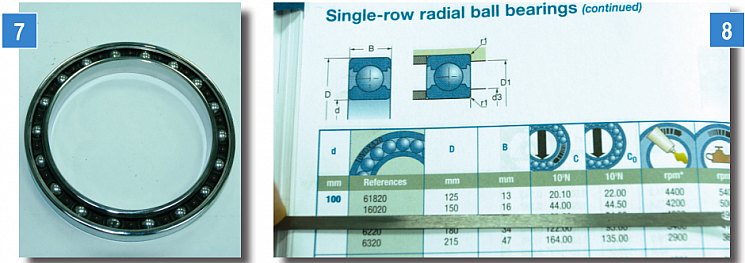
АБС: Какое следующее поколение подшипников поступит от вашей компании на автосборочные конвейеры?
– На этом эволюция подшипника не заканчивается. На выходе из экспериментального производства модели поколения 4. В них отражен тот же интеграционный процесс, в котором работают конструкторы и технологи последнее время. Разработка включает ШРУС и подшипник ступицы. Уже имеются прототипы, мы их изготавливали и испытывали, но в серийное производство они еще не пошли. Судьба любых новых технологий, как известно, в руках конечного потребителя. Попадет ли этот прототип на конвейер – пока неизвестно. Но, мы смотрим в будущее и работаем на опережение.
Редакция благодарит компанию NTN – SNR за помощь в организации статьи