Моторное масло в машинах трения
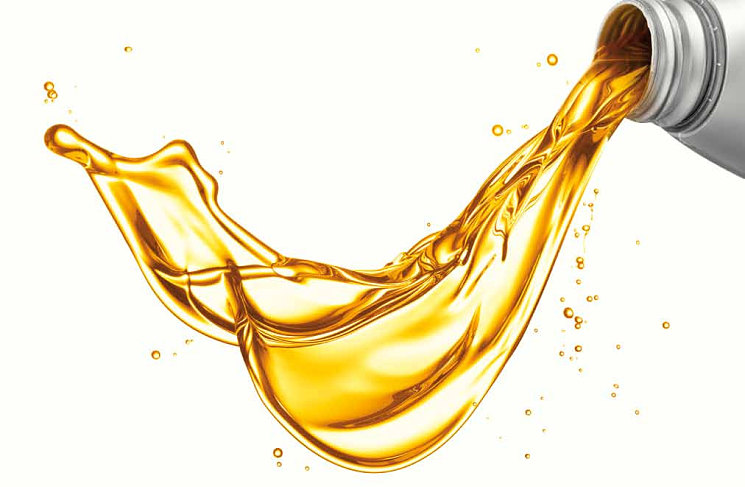
Мечта любого потребителя – найти такое масло, которое одновременно обеспечит ему отсутствие износа автомобильного двигателя, его максимальную мощность и заодно снизит расход топлива. Однако вынужден разочаровать: что бы ни писали в рекламе, но реально это неосуществимо.
Прежде чем приобретать любой смазочный материал (а в случае производителя – базовые масла и присадки), покупатель должен выстроить для себя приоритеты: что ему важнее? Максимальный ресурс? Максимальная мощность? Минимальный расход топлива? И только после этого начинать анализировать рынок масел – не поддаваясь на яркие и «завлекательные» объявления о том, что какой-то продукт обладает «чудодейственными свойствами», способными превратить старый двигатель в новый. Чудес, к сожалению, не бывает. А бывает грамотный подбор продукта, который даст реальный эффект.
Есть несколько критериев выбора смазочных материалов, а также фирм-производителей – попробуем в них разобраться.
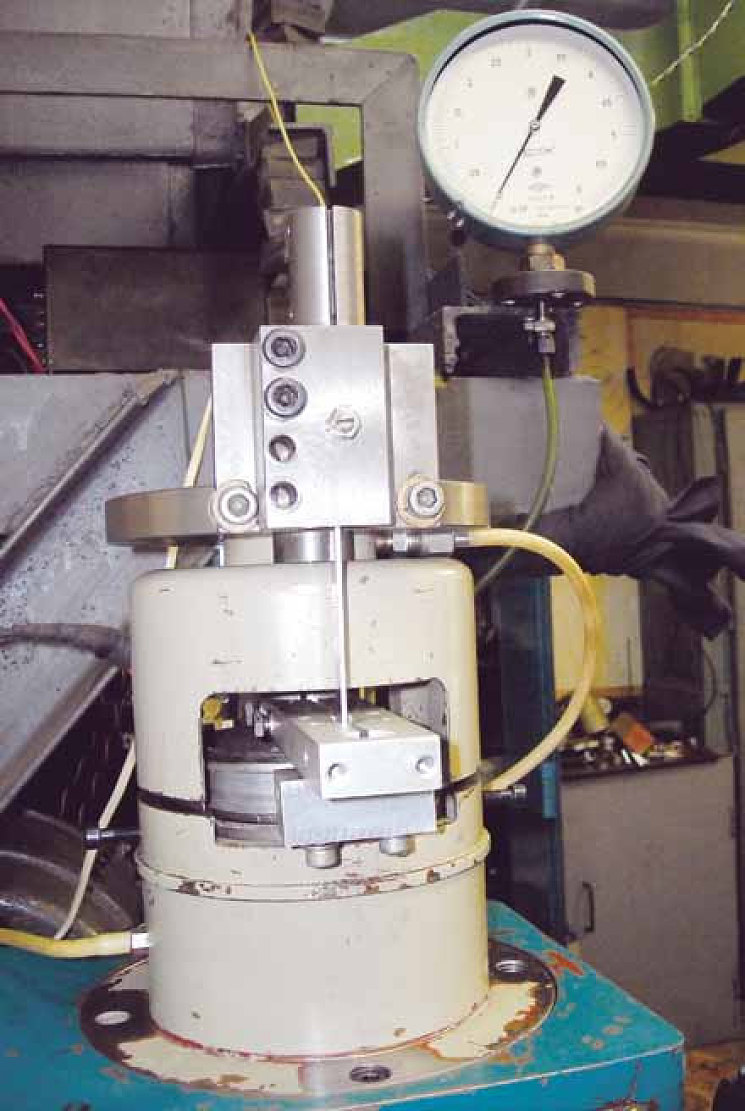
Например, если на этикетке препарата написано, что его применение экономит 7% и более топлива, то можно дальше не читать. Потому что если даже удастся свести потери на трение в узлах двигателя к нулю, то экономия топлива составит не более 7%.
Чтобы снизить энергетические потери, можно идти двумя путями. Либо, используя высоковязкий смазочный материал «А» (рис. б), заставить все пары трения, дающие в сумме более 90% потерь (поршни, поршневые кольца, коренные и шатунные подшипники, кулачки и подшипники распредвала), работать в области минимальных значений момента сил трения Мmin. Либо перейти на менее вязкий материал «Б», который на режиме холостого хода Vxx будет работать, изнашивая граничные защитные пленки на трущихся поверхностях (рис. в).
Первое недопустимо, потому что в этом случае будет использоваться менее 50% мощности двигателя. Второе чревато резким износом пар трения. В обоих случаях специфика возвратно-поступательного движения поршней (в ВМТ и НМТ скорость поршня равна нулю, а моменты сил трения в этих областях достигают максимальных значений) накладывает серьезные ограничения на возможности снижения трения. Однако, используя менее вязкие смазочные материалы, можно вдвое снизить потери на трение в коренных и шатунных подшипниках, кулачках и подшипниках распредвала (или распредвалов в современных многоклапанных двигателях). Кстати, эти потери составляют около 45% всех потерь на трение в ДВС.
Можно подсчитать, что экономия топлива при этом составит менее 1,6%. С учетом мизерного снижения потерь в цилиндропоршневой группе можно сказать, что уменьшение потерь на трение в ДВС, достигающее 2%, – это блестящий результат.
Но к сожалению, он может быть существенно омрачен низким ресурсом. Дело в том, что сплошная гидродинамическая смазочная пленка между трущимися поверхностями (рис. в) в этом случае гораздо тоньше, чем в таком же диапазоне скоростей скольжения у высоковязкого смазочного материала. Кроме того, скорость скольжения холостого хода Vxx оказывается ниже скорости скольжения V2Б, при которой возникает сплошная гидродинамическая смазочная пленка – главный фактор, обеспечивающий длительную и почти безызносную работу.
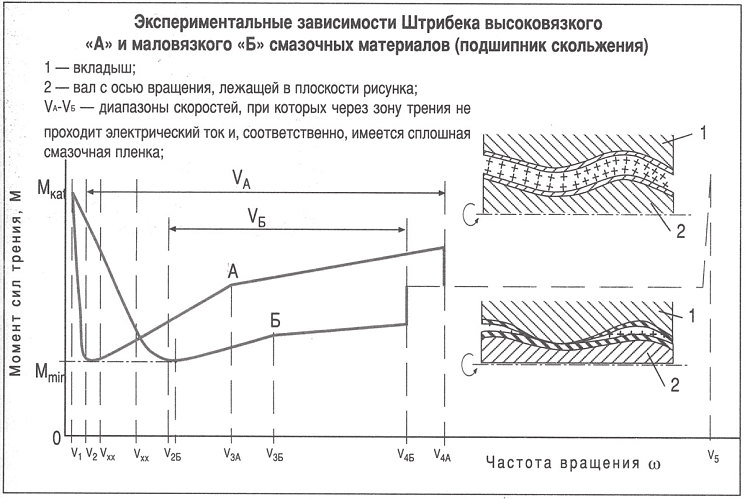
Особо следует остановиться на «прилюдных» экспериментах с использованием, в частности, машин трения. Демонстрируемые (в том числе и на выставках) «поразительные» результаты снижения трения и износа имеют, как правило, ту же природу, что и при механической обработке металлов.
Например, при токарных работах, сверлении и т.д. применяются различные жирные кислоты, в том числе и олеиновая кислота С18Р34О2. Взаимодействуя с металлами, она создает на трущихся поверхностях металлические мыла, что приводит к некоторому снижению твердости (разрыхлению) поверхностного слоя и «деликатному» его удалению.
Отсутствие омыленных поверхностных слоев, например, в гипоидных и тяжелонагруженных передачах может приводить к катастрофическим видам износа, таким как заедание и задир, с полным выходом узла из строя. Поэтому добавки, имеющие такое же воздействие, что и олеиновая кислота, могут использоваться в ступенчатых КПП и в ДВС, но в строго дозированных количествах. В противном случае они, слишком активно взаимодействуя с материалами синхронизаторов и вкладышей, быстро выводят их из строя.
Вернемся к началу разговора. Потребители приобретают смазочный материал, руководствуясь рекомендациями фирмы-производителя. Более «продвинутые» хотели бы иметь рекомендации для поиска оптимального смазочного материала – в соответствии с собственными приоритетами.
Однако существует парадокс – фирмы-производители не знают, какой смазочный материал образует при трении наиболее толстую (при данной нагрузке, температуре и скорости) разделяющую трущиеся поверхности смазочную пленку. А если и знают, то не публикуют эту информацию. А ведь более толстая смазочная пленка обеспечивает, кроме всего прочего, при существующих воздушных, топливных и масляных фильтрах снижение повреждаемости трущихся поверхностей из-за неизбежного наличия в масле абразивных частиц.
Фирмы-производители также не знают (или не публикуют) данные о том, при каких скоростях относительного перемещения трущихся поверхностей, в каких скоростных диапазонах VА или VБ при данных нагрузке и температуре у различных смазочных масел существует сплошная гидродинамическая пленка (рис. а). А ведь максимальная скорость, при которой еще существует сплошная смазочная пленка, – важнейший параметр, обеспечивающий при заданном ресурсе реализацию автомобилем максимальной мощности и надежности.
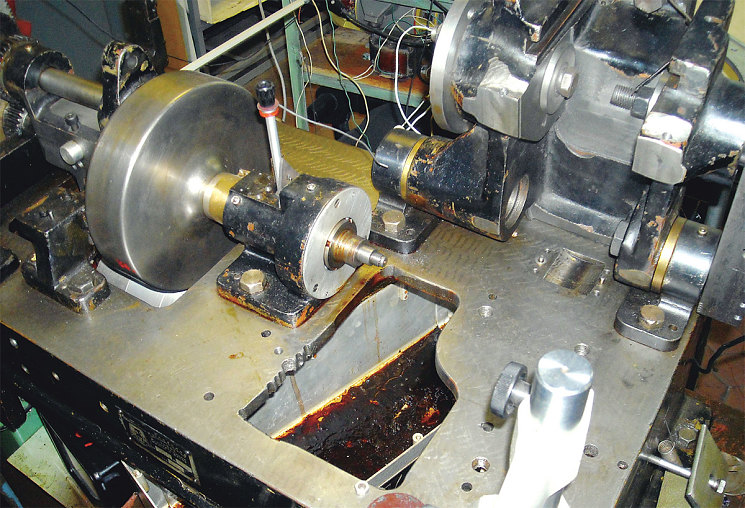
Таким образом, на этикетке следовало бы отражать ранг смазочного материала в соответствии со следующими параметрами.
Во-первых, реальным сроком службы вязкостных (загущающих) присадок. У некоторых загущенных масел задолго до срока смены из-за деструкции и других факторов вязкость снижается почти до вязкости базового масла.
Во-вторых, реализуемой толщиной смазочной пленки.
В-третьих, максимальной скоростью V4А или V4Б, приводящей к разрушению сплошной смазочной пленки, – Hi, Mild, Low.
В результате потребитель получит информацию о несущей способности смазочного материала, которая зависит от совокупного влияния температуры, давления, скорости сдвига, теплоемкости, стойкости вязкостных присадок и т.д.
Кроме того, было бы полезно знать, через какое время несущая способность пленки уменьшится на 10, 20 или 50%.
Все эти данные более полно отражают реальную способность смазочного материала предотвращать выход узлов трения из строя.
Здесь возникает еще один важный вопрос – насколько объективные данные могут публиковаться на этикетке?
Широко распространенные сегодня в испытательной практике машины трения используют испытательный контакт «шар – плоскость» (возвратно-поступательное или вращательное движение плоскости), а также «шар – цилиндрическая поверхность» (вращательное движение цилиндра).
Главный недостаток этих конструкций – отсутствие постоянства параметров исследований в течение одного опыта и от опыта к опыту. А ведь постоянство параметров является основой корректного экспериментального исследования.
Этот недостаток связан с тем, что в результате изнашивания тел, образующих зону трения, постоянно увеличивается площадь контакта, на которую приходится нагрузка. Проще говоря, вначале шарик касается пластины или цилиндра в точке, но в процессе опыта эта точка постепенно становится пятном. Так что в течение опыта давление и, соответственно, температура в зоне трения падают. Но при этом в каждый конкретный момент времени их величины неизвестны (измерить их невозможно технически).
Альтернативой контактам «шар – плоскость» и «шар – цилиндр» являются конструкции машин трения с эффективными, малоинерционными системами самоустановки трущихся поверхностей. Они позволяют (при неизбежных «неидеальностях» изготовления деталей, образующих испытательный контакт трения) обеспечивать постоянство формы эпюры давлений – независимо от тепловых и силовых деформаций, а также износа.
Кроме того, в этих машинах, созданных в Институте машиноведения имени А.А. Благонравова РАН (ИМАШ РАН), используется принцип непрерывного измерения износа, существенно повышающий корректность и точность измерений.
Например, проведенные на прецизионных машинах экспериментальные исследования моторных масел класса SAE10W-40 различных фирм, представленных в России, показали значительную разницу в величинах их несущей способности – около 40%. А это может (при ошибке в выборе масла) привести к снижению ресурса двигателя в 2–3 раза…
Павел Чхетиани, научный сотрудник Института машиноведения имени А.А. Благонравова РАН (ИМАШ РАН)