NTN – SNR. Как создается качество
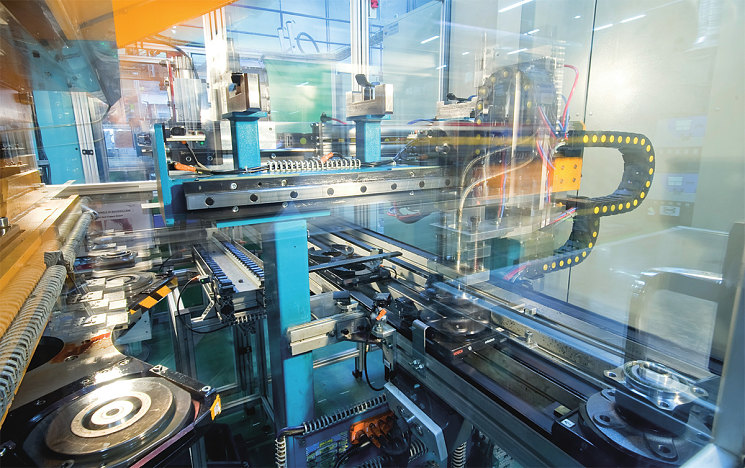
Продолжаем разговор о продукции и компании NTN – SNR. Сегодня, как и в прошлый раз, беседуем c Павлом СОРОЧИНСКИМ, техническим специалистом компании NTN – SNR.
АБС: В прошлую встречу мы говорили в основном о конструктивных особенностях ассортимента компании NTN – SNR. А что можете сообщить о качественных характеристиках изделий производителя?
– Если говорить о качестве изделий, которые производятся нашей компанией, то я бы вернулся к прошлой встрече. К конструкционной эволюции колесного подшипника. Действительно, все модернизации этой важной детали автомобиля были мотивированы запросом производителей автомобилей. Их интерес, и об этом мы говорили в прошлый раз, состоял в количественном уменьшении числа деталей, составляющих ступичный узел. Исключение даже одного компонента узла позволяет снизить расходы на производство ТС. Потому, что таким образом из технологической цепочки автосборочного производства выпадает ряд процедур, связанных с исключенной деталью. А это отдельные закупки, логистика, учет, сборка узла и т. д. И это все касается финансовой стороны вопроса. А как влияет такая интеграция на качество всего узла?
Известно, что качество всякого технического устройства зависит от трех параметров: конструктивных особенностей, достоинств материала и надежности сборки. При неизменно высоком качестве первых двух названных параметров, при новой технологии производства исключается последняя – сборка. Естественно, в таком случае потенциальная надежность всего узла повышается. В прошлой статье мы слегка касались ремонтной темы и отмечали особенности работ по замене колесных подшипников автомобиля. Это имеет самое прямое отношение к автосервису. Чем меньше процедур по ремонту узла производитель перекладывает на автомеханика, тем надежнее будут результаты ремонта. Причем, за редким исключением, каждая такая интегральная модернизация узла понижает зависимость качества ремонта от человеческого фактора. В нашем случае – автомеханика базовой квалификации.
АБС: А нормируют ли ваши заказчики – производители ТС по каким-то парамерам надежность ступичных подшипников?
– Безусловно. Автопроизводители, как правило, требуют не менее 500 тыс. км пробега для колесных подшипников. Это достигается в результате качественного проектирования и предсерийных испытаний. Автосборку же интересует в первую очередь такой параметр качества, как PPM (от англ. parts per million – частей на миллион). Общепринятый среди производителей деталей для ТС стандарт по ступичным подшипникам соответствует приблизительно 20 PPM. У нас это значение – до 4 PPM. То есть из одного миллиона произведенных компанией NTN – SNR колесных подшипников, могут быть отбракованы не более четырех. Причем к дефектам компания относит, например, и неправильную маркировку изделия.
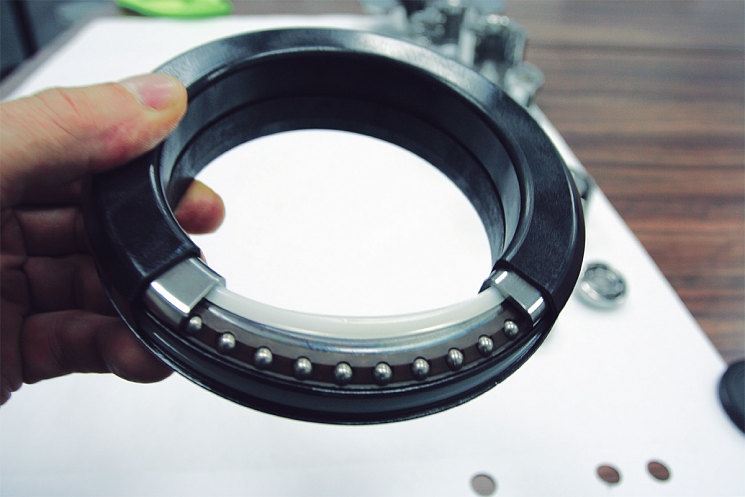
Такой уровень PPM достигается за счет контроля качества на каждом производственном переходе. В ступичных подшипниках таких можно насчитать 30–40. То есть каждый подшипник проверяется до 40 раз, прежде чем будет готов к передаче клиенту.
По другой линейке подшипников, а именно по опорно-упорным, качество сборки еще выше. Наряду со ступичными узлами мы относим эту продукцию к стратегическому ассортименту для конвейеров. С 2000 года и по сегодняшний день все изделия имеют 0 PPM. То есть более чем за 15 лет работы компания не произвела ни одной бракованной детали! А ведь мы поставляем эту продукцию практически на все мировые конвейерные линии.
АБС: Павел, в прошлой работе основное внимание мы уделили колесным подшипникам. Предлагаю рассмотреть и другую продукцию вашей компании.
– Мы только что отмечали высокое качество опорно-упорных подшипников, тогда о них и продолжим. Такие изделия, как и ступичные подшипники, представлены несколькими поколениями. Они родились вместе со стойкой Макферсона, конструкция которой включает амортизатор. Обеспечить такое инженерное решение можно было только на основе опорно-упорного подшипника. В отличие от ступичных подшипников, которые несут в основном радиальные нагрузки, подшипники стойки Макферсон подвержены больше осевым силам. Но на них частично влияют и радиальные нагрузки. Если посмотреть чертеж или рисунок в разрезе такого подшипника, то можно заметить, что тела качения по отношению к наружному и внутреннему кольцам расположены под небольшим углом. Это сделано как раз для оптимизации распределения нагрузок. Конструктивные различия опорно-упорных подшипников связаны с местом их установки.
Следует сказать, что компания NTN – SNR ежегодно патентует более 40 своих значимых изобретений. Некоторые из них имеют самое прямое отношения к опорно-упорным подшипникам. Для примера расскажу об одном из них. Мотивом для разработки новой конструкции опорного подшипника стала особенность обслуживания автомобилей в некоторых странах с загрязненными дорогами, в частности в РФ. В них принято промывать колесные арки ТС с помощью моек высокого давления (у нас их, как правило, называют Керхер). Мощная струя воды таких моечных агрегатов забивала подшипник дорожной грязью с песком. Как результат, через некоторое время подшипник выходил из строя. Для того чтобы с этим эффективно справиться, нашей компанией был разработан новый вид уплотнения для таких подшипников.

Конструкция включает оригинальное уплотнительное кольцо из специального пластика. Геометрические параметры подшипника и уплотнительного элемента, материал, из которого изготовлено пластиковое кольцо, обеспечивают надежную защиту полости подшипника от проникновения дорожной грязи даже во время промывки колесных арок с помощью мойки высокого давления. Эту разработку, защищенную патентом, разработчики назвали мобильным уплотнением. Это вполне соответствует функции мобильного уплотнителя, который при любом изменении угла стойки к кузову автомобиля максимально защищает опорный подшипник от проникновения дорожной грязи внутрь подшипника. Если покажете в статье фотографию такого разрезанного подшипника, то читатель сможет увидеть, как кольцо мобильного уплотнения отреагировало на появление новых возможностей. Оно «заняло позицию», максимально препятствующую образованию зазора между кольцами подшипника.
АБС: А как контролируется качество продукции, которую производит компания NTN – SNR?
– У компании имеются тестовые центры. Их несколько. Европейские заводы работают с французским центром. Он оснащен 150 испытательными машинами. Конечно, они работают в разных сегментах испытаний. Испытания, и, соотвественно, машины делятся на два типа. На прикладные – их четыре группы: автомобильные колеса и подвеска; автомобильные трансмиссии; авиационные и железнодорожные. Второй тип – для испытания элементов. То есть это отдельные испытания сталей, смазок, сепараторов и уплотнений. Эти машины испытывают как серийную продукцию, так и несерийную, собственную и от других производителей, как для своих нужд, так и по заказу от других производств. Центр работает 24 часа в сутки семь дней в неделю.
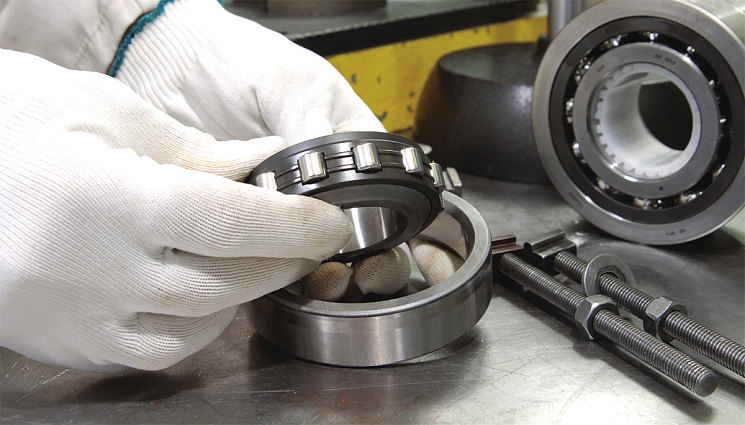
Не всегда там можно увидеть людей, некоторые испытания могут длиться и много месяцев в автоматическом режиме. Так, подшипники для железнодорожного транспорта испытывались 6 месяцев. Конечно, это не означает, что в течение 6 месяцев пошипники работали непрерывно. Цикл испытаний был подобран таким образом, чтобы максимально соответствовать режиму эксплуатации железнодорожного транспорта. Но в гораздо более жестких условиях. Это выглядело приблизительно так. Сначала, в течение двух часов подшипники вращаются в одну сторону со скоростью, соответствующей скорости движения локомотива 400 км/ч. Затем вращение останавливается. Через 10 минут процесс повторяется, только подшипники вращаются уже в противоположную сторону. Такой режим испытаний по нагрузкам на подшипники максимально приближен к пробегу высокоскоростного поезда TGV (сокр. фр. Train à Grande Vitesse – скоростной поезд) по маршруту от Лиона до Парижа за 2 часа. И так – на протяжении 6 месяцев: 2 часа в одну сторону, 10 минут перерыва и 2 часа – в обратную – день и ночь. Такие исследования называются ускоренными рессурсными испытаниями. Подобные испытания делаются и для автомобилей.

АБС: А сколько всего испытательных лабораторий у компании?
– Крупных три. Они расположены в Америке, в Японии и во Франции. Это крупные испытательные центры и центры научно- исследовательской и конструкторской работы (НИОКР). Обычных лабораторий значительно больше. Они работают практически при каждом производстве.
АБС: Случалось ли Вам бывать в таких заведениях?
– Случалось.
АБС: И какие впечатления у Вас остались?
– Всякий раз при посещении этих центров меня поражает, прежде всего, одна мысль: насколько сложна технология производства современного подшипника – детали, часто состоящей всего из нескольких элементов!