Под капотом всё в порядке
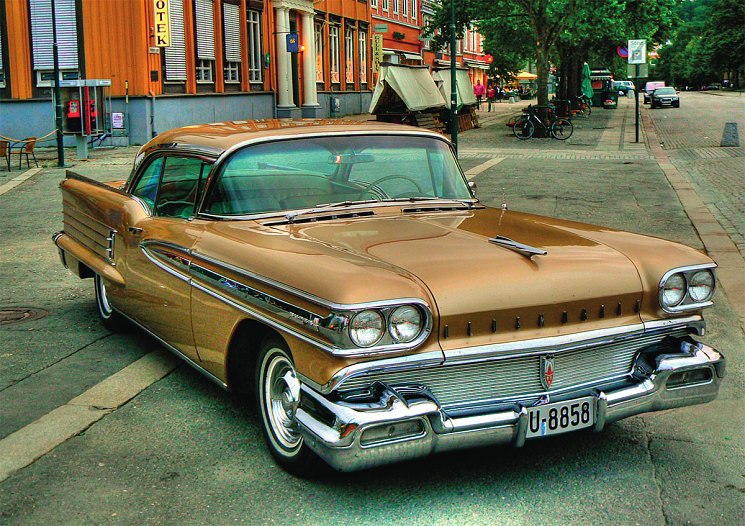
В августе журнал «АБС-авто» опубликовал статью «Воскирование. Дорожная карта». Сегодняшний материал можно назвать так же, но с дополнением «Часть 2». Однако мы изменили заголовок, поскольку разговор пойдет не о днище и колесных арках, а о деталях под капотом.
Эту тему мы уже поднимали. Но не упрекайте редакцию в повторах. Во-первых, кто-то читал предыдущие статьи, а кто-то нет. Во-вторых, сезоны «зима – лето» повторяются с завидным постоянством, и никого это не удивляет. Значит, неизбежны и сезонные публикации. Вот и сейчас – сентябрь, пора готовить сани и подумать о защите двигателя и его систем. Но защите специфической. Итак, мы начинаем.
Условия, в которых приходится жить и работать узлам и системам в подкапотном пространстве, уникальны. Иначе как экстремальными не назовешь. Больше всех страдают электрика и электроника, радиаторы системы охлаждения и детали кондиционера, многочисленные трубки и штуцеры. Почему? Давайте разберемся.
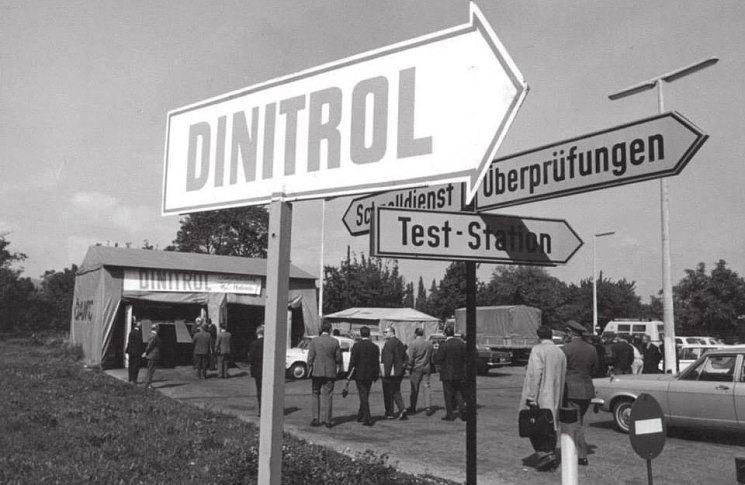
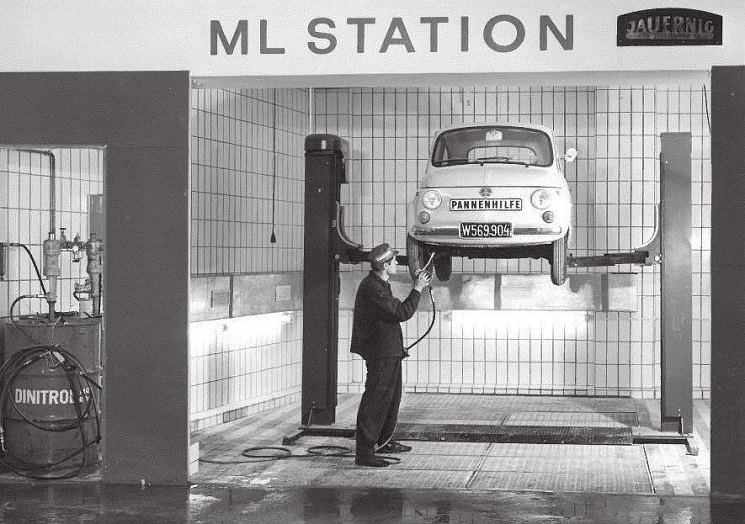
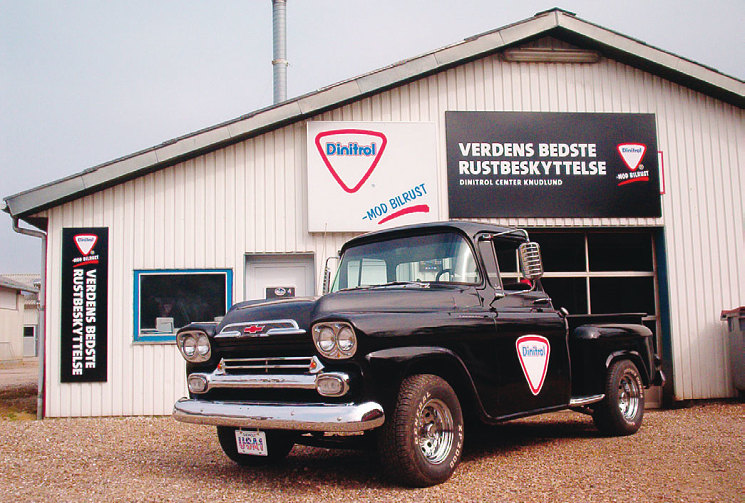
Возьмем тепловые режимы. Лето, жара. В нескольких сантиметрах горячий двигатель. Сверху на капот падают солнечные лучи. А прохладной ночью в моторном отсеке образуется обильный конденсат.
Зима, холод. Опять же горячий двигатель, а по ночам колоссальные перепады температуры. Снова конденсат. Влажный рай для гальванических процессов, поскольку тут полно разнородных металлов. Например, сталь-алюминий. Разность потенциалов. Утечки тока по влажной поверхности – пусть и ничтожные, но для коррозии много не надо.
Механические нагрузки у разъемов, шлангов и трубочек невелики. Но настырны. Имя им – вибрация. В той или иной степени вибрируют все двигатели, ведь идеальной балансировки не бывает. А механические нагрузки, тем более циклические, способствуют развитию коррозионных процессов – это, извините, азбука.
Есть под капотом и более ответственные зоны, испытывающие серьезные напряжения. Это места крепления стоек амортизаторов. Опытные водители знают: у «пожилых» автомобилей там частенько наблюдаются рыжие круги ржавчины. Такие поражения напрямую влияют на безопасность движения.
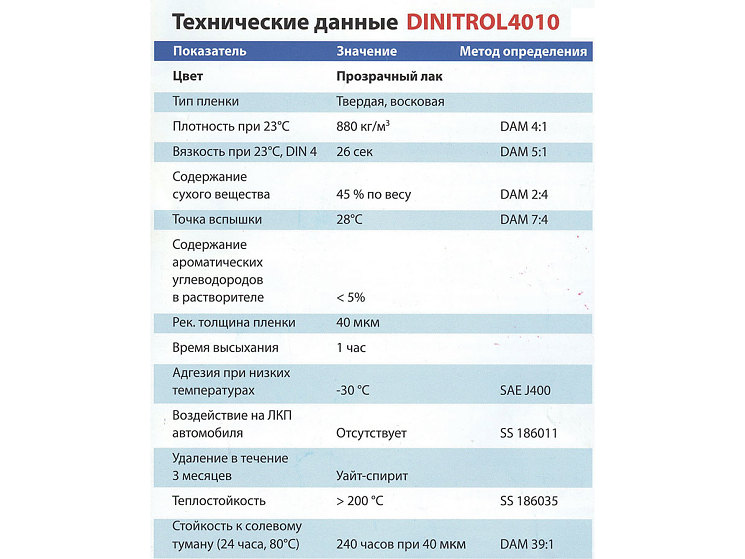
А теперь о главном. Ни одна из областей кузова не подвергается столь грозной химической атаке, как пространство под капотом. Вспомните, сколько там различных бачков с пластмассовыми крышками. Так вот: ни один из них не может считаться абсолютно герметичным. Микроскопические утечки будут всегда.
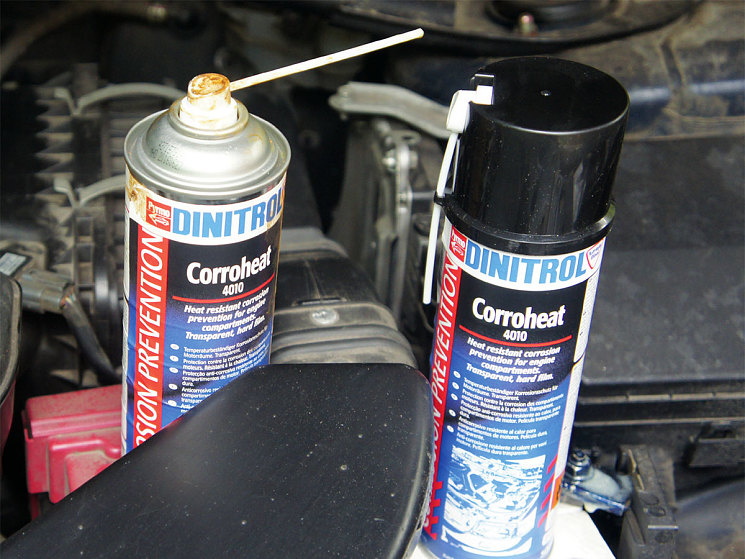
Во-первых, это коррозионно-активные испарения моноэтиленгликоля, входящего в состав охлаждающих жидкостей. Во-вторых, пары спирта – этанола, пропанола, а то и запрещенного у нас метанола из бачка стеклоомывателя. В-третьих, испарения гликолевой основы тормозной жидкости. Все перечисленное для металла не подарок.
Этого мало? Продолжим: пары топлива, горячего моторного масла, жидкости гидроусилителя руля, хладагента для кондиционера. А отработавшие газы, попадающие в подкапотное пространство? Для описания их «букета» понадобится не одна статья… И все это в условиях упомянутого «горячего цеха». Плюс дорожная пыль и грязь, противогололедные реагенты, остатки щелочных шампуней после мойки двигателя…
Если бы химическая и электрохимическая коррозия не воспользовалась такими условиями, мы перестали бы с ней считаться. И отказались бы покупать антикоры, пустив их производителей по миру. Но коррозия своего шанса не упускает. И больше всех атакует электрику и электронику.
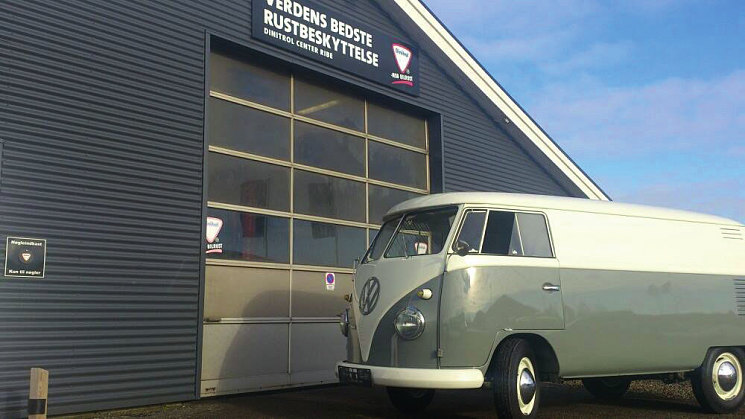
Стоит ли удивляться, что под капотом электрические контакты окисляются, «гниют», и начинаются сбои да отказы, отказы да сбои… Работники сервиса хорошо знают, что электрооборудование и электроника подводят чаще других систем автомобиля.
Электроника отказывает из-за «водобоязни» дешевых пластмассовых корпусов и микротрещин, провоцирующих утечки тока и короткие замыкания. Добавим сюда те самые окислившиеся контакты, перегоревшие предохранители и повреждения обмоток электродвигателей, вызванные снижением стойкости к «пробою» из-за влажности.
А печатные платы? Сама их природа противится работе во влажной среде. А технологии изготовления увеличивают плотность элементов на единицу площади. А тут еще температура, тепловые деформации…Изоляция страдает. Нужна, очень нужна подкапотной электрике защитная пленка. Но какая именно?
Бывают так: необходимость подкапотной обработки признают. Но защищают моторные отсеки грубо и чем попало. И забрызгивают непонятной черной массой разъемы, клеммы, проводку и прочие достаточно нежные места. А потом выходит из строя дорогущий ЭБУ. А дилер лишает владельца гарантии: мол, вы виноваты, залили всё каким-то «гудроном».
Обработка, может, и ни при чем, но это еще доказать надо! Экспертиза, судебные разбирательства, потерянное время. А в случае проигрыша и деньги – менять ЭБУ приходится за свой счет.
Так что же – не защищать подкапотное пространство? А как же ужасы, описанные в начале статьи? Нет, защищать, конечно. Но не тяжелыми густыми материалами для днища. И не препаратами для полостей – они не застывают до конца и не всегда дружат с высокими температурами. Тут требуются специальные составы. О них и поговорим.
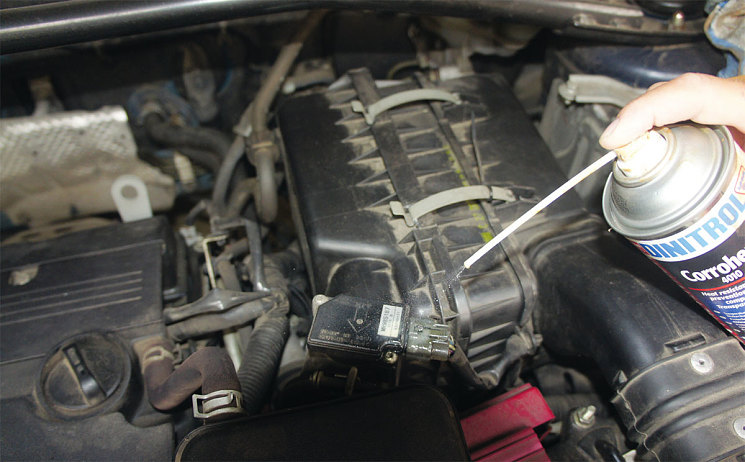
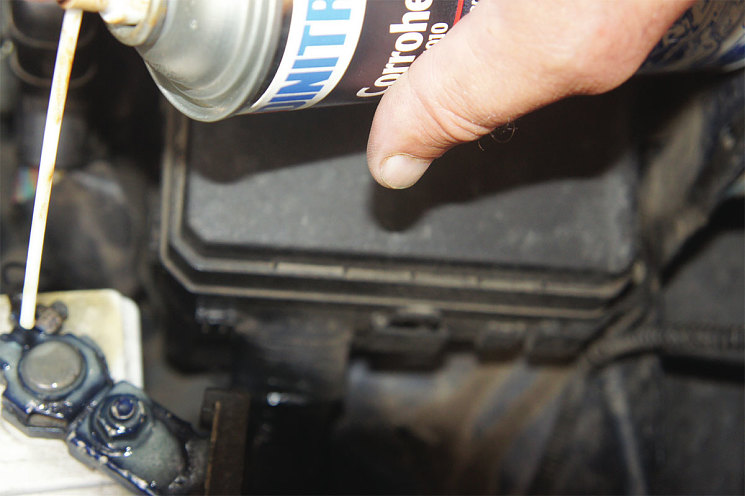
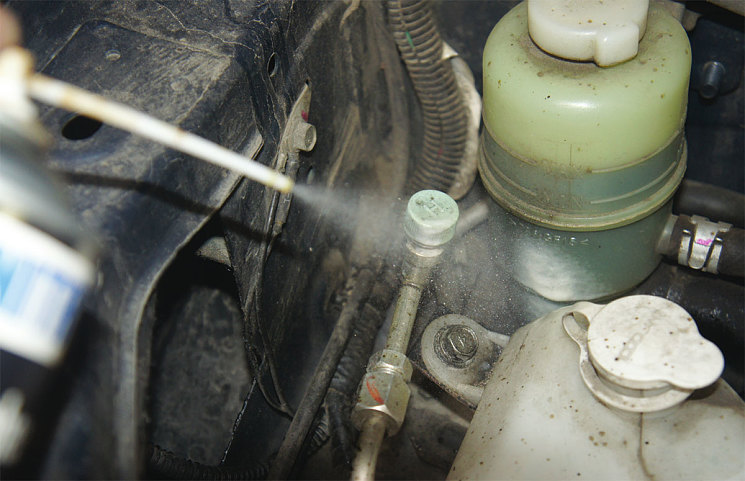
Давайте вообразим, что мы инженеры-химики. И получили задание разработать антикор для моторного отсека. Какими свойствами его наделить?
Наверное, такими. Легкий распыляемый состав с мощными ингибиторами коррозии и надежной адгезией. При нанесении должен уметь вытеснять влагу. А после застывания блокировать доступ кислорода к алюминию, стали, меди, цинку, хрому – словом, ко всем защищаемым материалам.
Пленка после застывания твердая, но эластичная. Твердая, чтобы не пачкалась и обладала достаточной прочностью. Эластичная, чтобы не боялась вибраций. А еще она должна быть прозрачной – для визуального контроля за состоянием контактов и разъемов. И за VIN-кодом на табличке и номером двигателя на блоке.
Разумеется, материал должен выдерживать высокую температуру, не гореть и не плавиться. И не терять своих характеристик при нагревании.
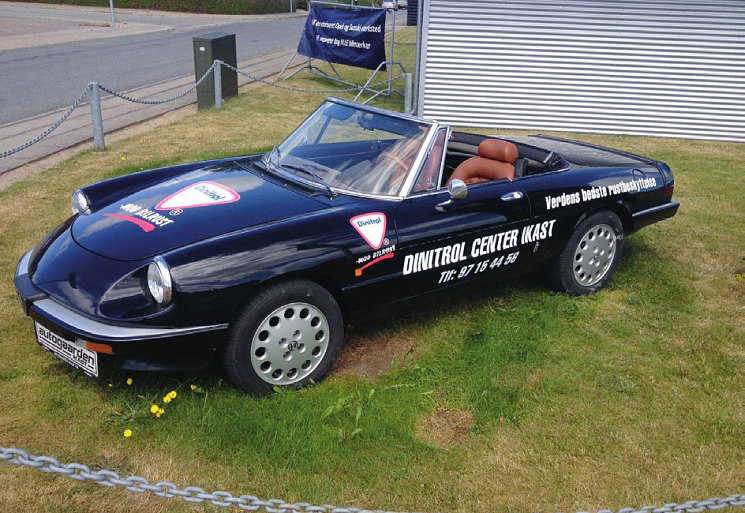
Сегодня под капотам может быть щелочная среда, а завтра – кислотная. Щелочная от моющих средств, кислотная от атмосферы большого города. Значит, препарат обязан быть стойким к обеим средам. И в то же время он не должен проявлять агрессии к пластикам и резине.
Впрочем, нам подсказывают, что такой материал уже есть. Называется Dinitrol 4010 Corroheat. Восковой состав с ингибиторами коррозии специально для моторного отсека. Недорогой, эффективный и простой в применении. А технические данные препарата – вот они, в таблице на c. 33.
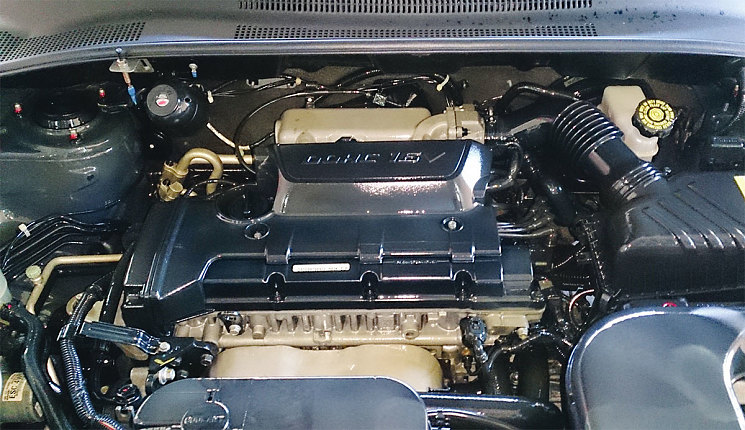
Фактически это уже известное нам воскирование, но для защиты подкапотного пространства. Как видно из фотографий, работать с препаратом довольно просто. Главное – очистить защищаемые поверхности, и можно распылять материал, защищая не только электрику, но и штуцеры, трубки, шланги. Важно делать это периодически – лучше всего два раза в год, весной и осенью.
Но это еще не все. Не так давно появился материал нового поколения – экологически безопасный на водной основе Dinitrol 964, создающий более прочную и долговечную прозрачную пленку. Оба препарата, 4010 и 964, продаются и в фасовках от 1 л до 208 л. Так что не баллончиком единым…