Поколение NEXT. Часть 2. «Стандартный» подход
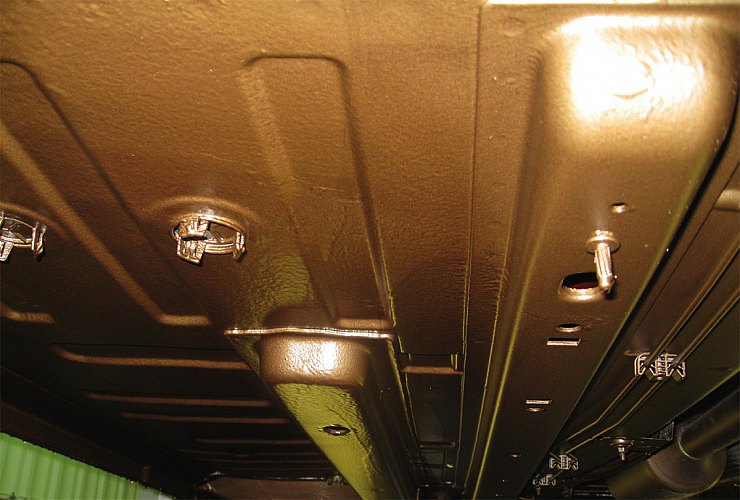
Антикоррозионные материалы четвертого и пятого поколений – по каким нормативным документам они выпускаются? И вновь мы обращаемся к опыту Шведского королевского института металла и коррозии (KIMAB).
Положим, автомобильному концерну требуется антикоррозионный материал для обработки кузовов на конвейере. Он заключает контракт с производителем антиткоров и выставляет требования к препарату: экологичность, возможность нанесения в автоматическом режиме в условиях конвейера, столько-то лет эксплуатации до появления сквозной ржавчины на кузовных панелях и т.д. Но как проверить выполнение этих требований?
Тут-то и выходит на сцену KIMAB. Этот научно-технический центр разработал наиболее полные методики тестирования антикоррозионных материалов, основанные на нормативах ISO, DIN и прочих фундаментальных базах.
Разумеется, институт трудился не в гордом одиночестве. В работе участвовали ведущие производители автомобилей, компании, выпускающие конструкционные материалы (в частности, листовой прокат и цветные металлы), специалисты по гальваническим покрытиям и, конечно же, производители антикоррозионных составов. Тем весомее результаты: методики Шведского института стали эталонами для всей Европы.
Для примера ознакомимся с некоторыми стандартами испытаний антикоррозионных материалов для защиты внутренних полостей кузова. Они представлены в таблице.
Даже беглое знакомство с таблицей убеждает в профессиональности подхода к оценке свойств материалов. А главное – в практическом смысле испытаний.
Возьмем, например, стандарт SS 18 60 11. Когда автомобиль обрабатывается антикором, неизбежны его попадания на лакокрасочную поверхность кузова. Отсюда требование: даже после высыхания антикоррозионный материал должен легко удаляться с кузова без обесцвечивания, вздутия и размягчения краски. И вообще – без малейших следов!
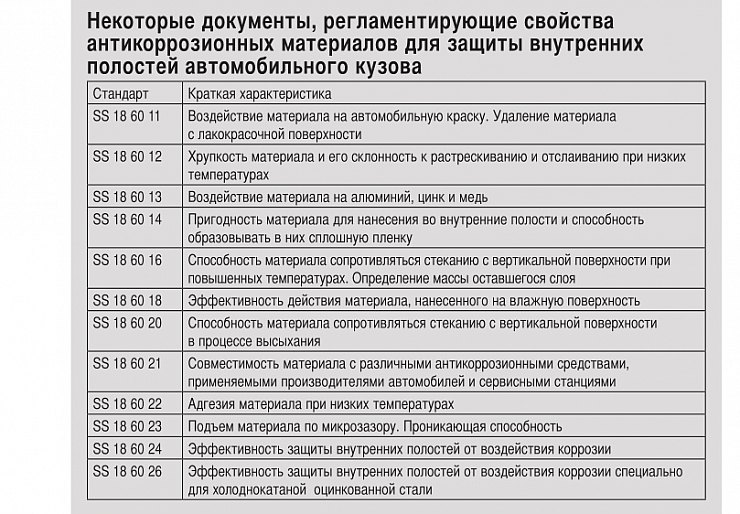
Или документ SS 18 60 16 – как следует понимать его? Обработанный антикором автомобиль может оказаться на жарком солнце или в сушильной камере при ремонте лакокрасочного покрытия кузова. Пленка не должна размягчаться и стекать с вертикальных внутренних поверхностей дверей, порогов и других полостей. А если это и допускается, то в строго определенных границах – на то и контроль по массе.
Еще один наглядный пример – стандарт SS 18 60 21. Совместимость антикоров от различных производителей, когда препарат наносят то на ПВХ, то на «послепродажный» антикор, то на материал трехлетней давности. Согласитесь: актуальнейшие задачи для антикоррозионных участков сервисов.
А вот стойкость в соляном тумане оценивается по стандарту ASTM B117. К слову, ряд производителей антикоров взяли на вооружение такую формулу: 100 часов испытаний в соляном тумане соответствуют одному году эксплуатации. Практика подтверждает ее справедливость.
А теперь обратимся к технологии изготовления современных антикоррозионных препаратов. Собственно «варка» антикора проводится в специальном резервуаре – реакторе. Он оснащен перемешивающим устройством пропеллерного или иного типа, а также системой подогрева и охлаждения, которые осуществляются водой, маслом или электричеством.
После контроля качества сырья, в частности проверки кислотности, плотности и наличия воды, его загружают в реактор и тщательно перемешивают.
Кроме основы (например, синтетических восков или полимеров для безрастворительных препаратов Solvent free) в реактор вводят ингредиенты, придающие «блюду» требуемые свойства. Именно они, ингредиенты, превращают безликую массу в современный антикоррозионный материал.
Рецептуры у каждой фирмы свои, общей является лишь конечная цель. Профессиональный материал обязан обеспечивать надежную адгезию к металлу, а также к фосфатированной, загрунтованной и окрашенной поверхности. Полученная пленка не должна смываться конденсатом, который всегда будет появляться в полостях.
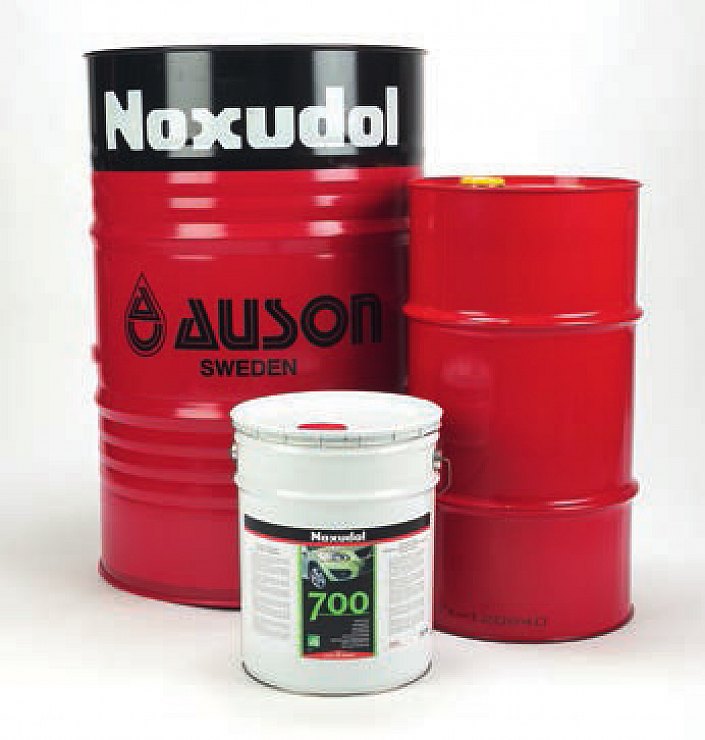
Тиксоторопность при нанесении антикоррозионного материала важна чрезвычайно. Это относится и к «легким» полостным составам, и к «тяжелым» густым препаратам для днища. Их вязкость меняется в зависимости от механического воздействия: при распылении материала под давлением она ниже, что способствует хорошему заполнению микротрещин и зазоров, а сразу после нанесения материал как бы загустевает и не стекает с обработанной поверхности.
Еще одну группу ингредиентов следует отметить особо: это ингибиторы коррозии, или, как их образно называют, «отрицательные катализаторы». Они замедляют коррозионные процессы – причем настолько эффективно, что кузов скорее выйдет из строя от усталостных нагрузок, нежели получит сквозные коррозионные поражения.
Кроме адгезии, тиксотропности, способности к ингибированию и прочих необходимых свойств, составы должны обладать высокой стойкостью к абразивному воздействию. А если дорожный камешек все же повреждает защитную пленку, она должна затягиваться, самозалечиваться.
Специальные добавки не позволяют современному материалу для днища высыхать полностью – минимальная подвижность пленки сохраняется в течение всего срока службы. Это позволяет ей не трескаться при механических колебаниях и упругих деформациях кузова и, когда это необходимо, «включать механизм» самозатягивания.
Показательно, что современные антикоры имеют в своем составе до 250 компонентов.
Но вернемся к технологии. В полученную смесь водят инициатор, запускающий химическую реакцию, и начинают перемешивание и нагревание композиции. Строгое наблюдение за температурой ведут непрерывно, и по достижении 95° С нагревание прекращают.
Теперь продукт необходимо правильно охладить. Ведь реакция еще не окончена, она лишь перешла в заключительную фазу. Поэтому ускорение или замедление процесса охлаждения может привести к браку.
Следующий этап – ввод очередной порции сырья, смешивание и контроль вязкости, плотности и механических свойств при нанесении, в частности – тиксотропности. Кроме того, проверяется химический состав материала на IR-спектрофотометре. Полученный «дактилоскопический отпечаток» показывает, правильно ли прошла реакция.
Если все предварительные показатели в норме, у новоявленного продукта проверяют самое главное – антикоррозионные свойства. При получении положительного заключения продукт через специальные фильтры перекачивают в емкости для хранения.
Пока материал не передан заказчику, его состояние все время контролируют: не загустел ли он, не нарушилась ли однородность состава, не появился ли осадок? Перед отправкой продукт еще раз пропускают через систему фильтров и лишь после этого перекачивают в транспортные емкости.
А что бывает, если обнаруживается брак? Например, нарушается температурный режим, и реакция идет по неверному пути? Ответ прост и суров: вся партия материала уничтожается. А это, между прочим, тысячи и даже десятки тысяч литров. Лучше понести убытки, чем получить рекламации и подорвать доверие к торговой марке.
Таким образом, профессиональный антикоррозионный материал четвертого и пятого поколений – это не просто мастика или жидкий восковой состав, а специализированный химический продукт, основанный на требованиях международных и национальных стандартов и полученный в условиях высокотехнологичного производства.
Как уже говорилось, рецептуры материалов у каждой фирмы свои. По понятным причинам эти «формулы» не раскрываются. Однако бизнес есть бизнес, и фирменные секреты не мешают заниматься аутсорсингом – т.е. размещением заказов на заводах «коллег по антикоррозионному цеху».
Так, шведская компания Auson AB, производитель препаратов четвертого поколения Mercasol и безрастворительных составов пятого поколения Noxudol периодически выпускает партии антикоров совсем других марок. Это нормально – главное, чтобы заказчик и исполнитель были довольны.
Редакция благодарит Шведский королевский институт металла и коррозии и компанию Auson AB за помощь в подготовке публикации.