Собрались на работу
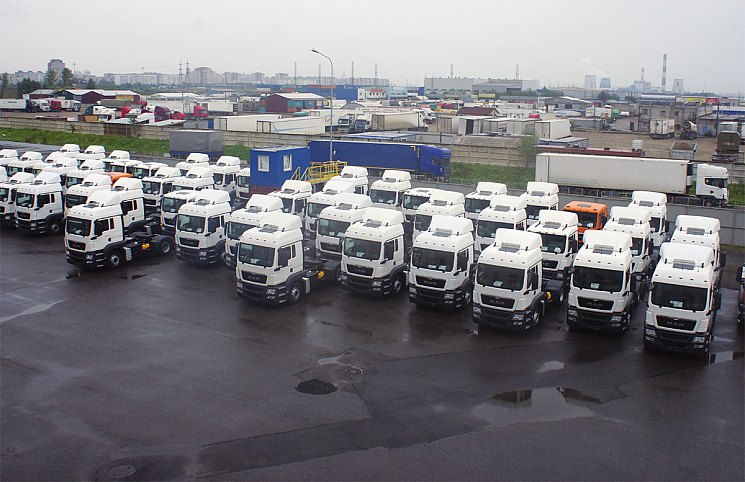
Посмотрел и понял, что заголовок получился двусмысленным. Но в любом случае правдивым – речь-то о сборочном производстве! А именно о заводе «МАН Трак энд Бас Продакшн РУС», что в Шушарах под Санкт-Петербургом. Здесь выпускают тяжелые грузовики MAN.
Сама марка в представлении не нуждается, но некоторые факты вспомнить полезно. Компания MAN Truck & Bus производит грузовые автомобили с полной массой от 7,49 до 44 т, тяжелую спецтехнику, предназначенную для перевозки грузов весом до 250 т, городские, междугородние и туристические автобусы и шасси. Выпускает она и двигатели – как дизельные, так и работающие на природном газе.
В грузовом сегменте производятся такие автомобили: легкой серии TGL с допустимой полной массой от 7,49 до 12 т; средней серии TGM (12–26 т); тяжелые TGS и TGX с полной массой от 18 до 44 т.
Но вернемся к предприятию в Шушарах. Старт и развитие завода были стремительными:
– 2011 год – подписание «Меморандума о взаимопонимании между MAN и администрацией Санкт-Петербурга»;
– 2013 год – получение лицензии на сложные производства, выпуск первого автомобиля и презентация его на стенде MAN на выставке COMTRANS'13;
– 2015 год – выпуск 1000-го грузовика.
Здесь трудятся 76 человек, из которых 40 заняты в производстве, а 36 – в обеспечении функционирования предприятия. Коллектив молодой, 70% работников не достигли и 40 лет. Интересно, что на производстве заняты только мужчины, коих на заводе 80%. Слабый пол в меньшинстве – но вообразите, как хорошо им 8 марта!
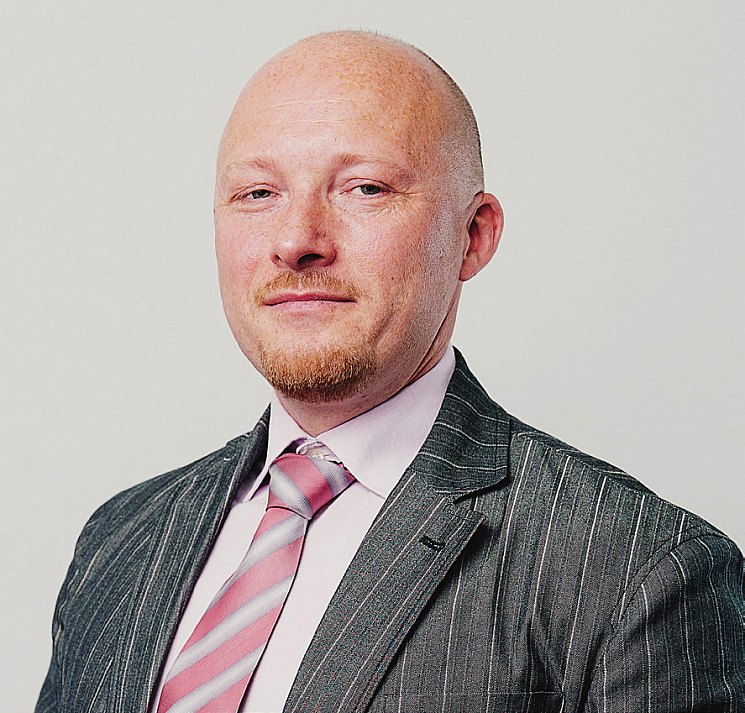
Давайте пройдем вдоль сборочной линии и проследим, как отдельные агрегаты, узлы, детали и системы превращаются в мощный грузовик.
Все необходимое для сборки поставляется лотами (машнокомплектами). Двигатели поступают из Нюрнберга, они уже заправлены маслом. Кабины – из Австрии, мосты из Мюнхена. Впрочем, есть и плоды локализации. Так, коробки передач поставляет совместное предприятие «ZF КАМА» из Набережных Челнов. А краски, антитфриз, топливо, стеклоомывайка и прочие жидкости используются отечественные.
Выпускают здесь в основном грузовики TGS. Но есть и линия TGM – будут заказы, соберут и их. Сборка начинается с «Ворот качества», так здесь называют пункты входного контроля. Соответствует ли поставка заказу? Не повреждены ли упаковки? Тут используется и электроника, и визуальная проверка. Никаких отклонений от списка – только крепеж идет с запасом.
А вот сборка рамы. Этапы работы распределены по участкам – их называют станциями. Распаковываются лонжероны и поперечины. Каждую деталь сопровождает заводской номер, занесенный в электронное «досье». Компьютерная система хранит всю информацию данного заказа – тип грузовика, опции и проч.
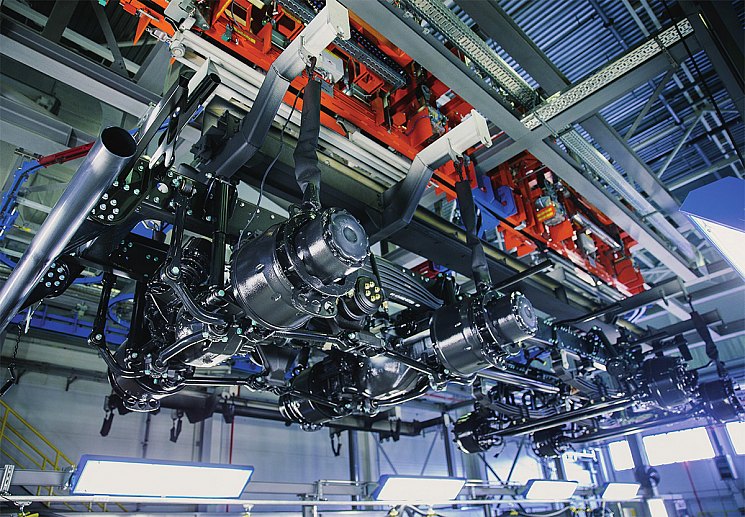
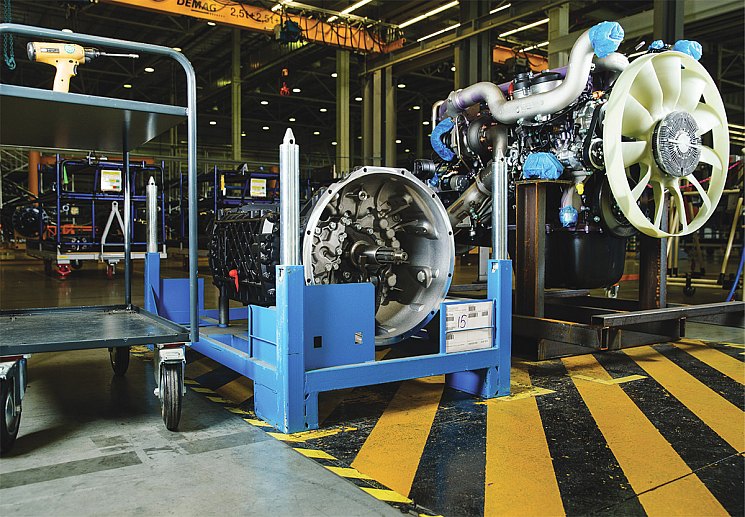
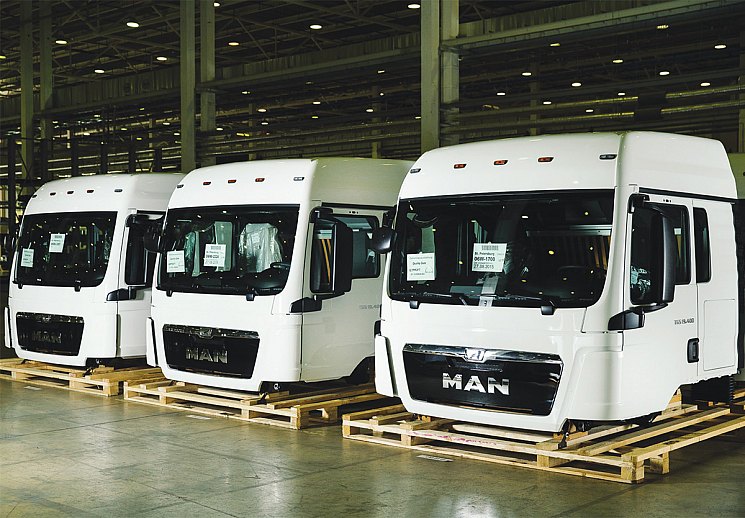
На первой станции проводится разметка – где какие болты или заклепки установить. Лонжероны соединяются с поперечинами, тут же производится подсборка разнообразных рычагов, балансиров и кронштейнов. Набивается номер и заносится в сопроводительный лист, который идет в архив и хранится 15 лет.
Болты затягиваются гайковертом с разбросом момента ±15%, а потом «доводятся до ума» динамометрическим ключом предельного типа. Ответственные соединения (например, крепления рессор) затягиваются электронным ключом.
По технологии сборки половина соединений рамы болтовые, а половина заклепочные. Клепка дешевле, но требует более дорогого оборудования.
Рама собирается в перевернутом состоянии – иначе как установишь мосты, не подавать же их снизу! Операция монтажа мостов – дело трудное и ответственное. Представьте: огромный вес и прецизионная посадка. И вот рама с рессорами, мостами, гидроусилителем руля, разнообразными рычагами и карданными валами (свободные концы, естественно, закреплены) готова. Теперь ее надо перевернуть.
Зрелище этого кульбита, надо сказать, впечатляющее. Плавно вращаются шкивы, ползут специальные стропы… Громадный стальной каркас весом примерно 7 т медленно поворачивается вокруг горизонтальной оси на высоте 2 м и наконец опускается на специальные подставки.
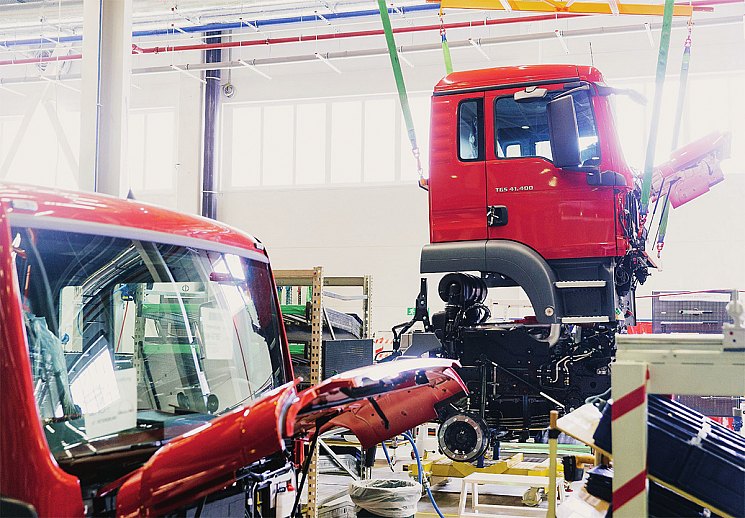
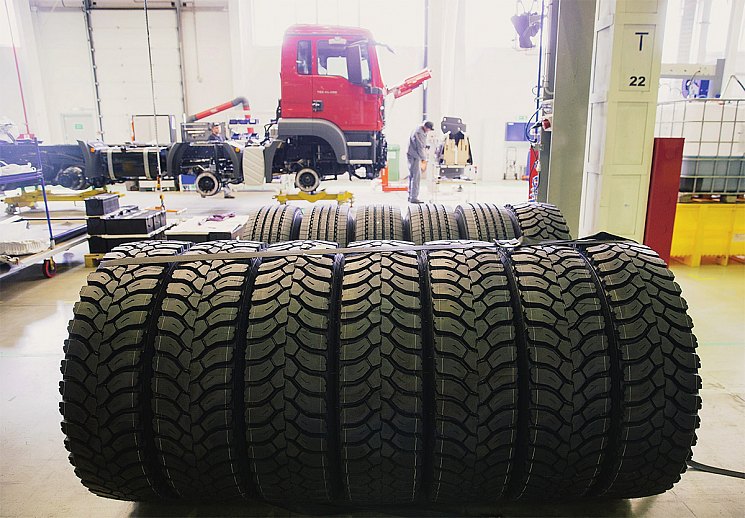
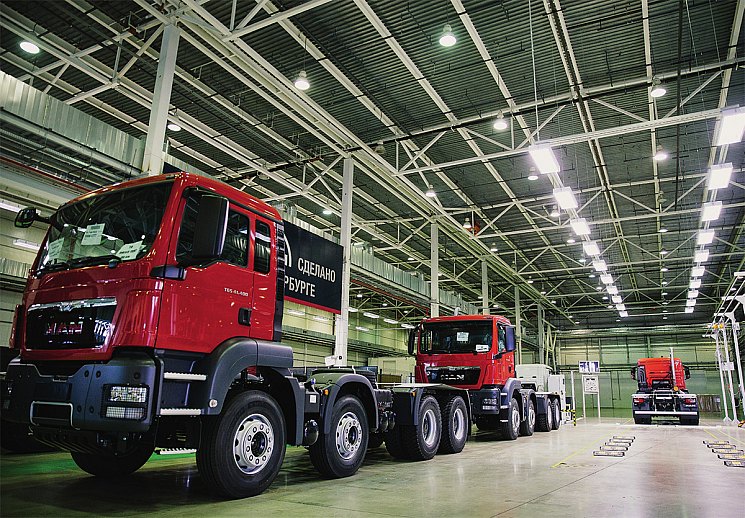
Что теперь? А теперь окраска. Логично: часть деталей рамы была окрашена, часть загрунтована, болты с гальваническим покрытием, а заклепки вообще не защищены – этакий разброс. Да и царапины возможны во время сборки. Надо все детали уравнять в антикоррозионных правах.
В нужных местах рама маскируется и отправляется в камеру, где ее покрывают экологичной трехкомпонентной краской «собственно краска + вода + отвердитель». Окрасочная камера – самой дорогое оборудование. Оно же задает производительность завода – на одну раму тратится 27 минут, и ускорить этот процесс нельзя. Итак, окраска, предварительная сушка при 45 °С, потом окончательная сушка при 85 °С и зона охлаждения, без нее с металлом не поработаешь.
Цвет – черный и только черный. Кстати, в Германии применяется восемь цветов, но для наших условий это признано нецелесообразным.
И дальше, дальше, дальше по станциям. Монтаж АКБ, глушителя, прокладка электрики и пневматики, и вот мы прибыли на станцию, где на рамы устанавливают, радиатор, двигатель, коробку передач. Это уже почти автомобиль! Не знаю, как у грузовиков, а на «легковых» заводах стыковку двигателя с кузовом называют «свадьбой».
Теперь заправка жидкостей гидроусилителя руля и трансмиссии. И вот – кабина, с готовым салоном. Не хватает только магнитолы и тахографа. Ставим и их тоже. Монтируем аэропакет, бамперы и бачок стеклоомывателя. И наконец, устанавливаем колеса…
Но это еще не все – если мы собираем тягач, необходимо установить седло. Для этого требуются сварочные операции – единственные на заводе. Сварные швы покрываются пастой типа PVC (марка не раскрывается) для защиты от коррозии. Кстати, по заявкам возможна и дополнительная антикоррозионная обработка автомобиля методом распыления, для чего оборудован особый пост.
А потом автомобиль программируется, в блоках управления прошивается новейший «софт». И вперед… на обкатку? Не спешите – на проверку пневматики на предмет утечек и на заправку хладагента в систему кондиционирования.
Ну все, пора будить зверя! Заводим двигатель, нарочно проезжаем по неровностям, чтобы «встряхнуть» подвеску и заруливаем на тормозной стенд. Проверяем тормозную систему и переезжаем на яму для контроля сход-развала и рулевого управления. И на следующий пост под названием Green Line, где регулируем фары и проходим ряд дополнительных проверок.
Потом грузовик колесит 20 км по дорогам общего пользования с различным рельефом, калибруется тахогаф, после чего машина отправляется на заводскую площадку.
Есть среди грузовиков и счастливчики – каждую неделю аудиторы, прошедшие подготовку в Германии, отбирают две машины и подвергают их «суперпроверке», включающей 100-километровый пробег.
После этого выставляется оценка: 0 – все в порядке; 5 – есть недочет, но для клиента это вряд ли важно; 15 – дефект небольшой; 50 – дефект серьезный; 100 – недопустимый дефект. С оценками 5 и 15 автомобилю дают путевку в жизнь, но лишь после исправления дефектов, а с показателями 50 и 100 – нет.
По окончании трех дней выставляется рейтинг, согласно которому 1 – это идеальное состояние. Чем больше цифра, тем хуже результат. А каков рейтинг у продукции завода? У него очень хорошие показатели, есть даже два чемпиона: тягачи получали оценки 1 и 1,1.
Итоговая оценка по результатам аудита – это рейтинг QKZ, он рассчитывается в баллах по специальной формуле. Почему используется данная методика? Никакого секрета: разные грузовики имеют разную сложность, и возможное количество дефектов может варьироваться. Так, в 2‑ и 4-осных грузовиках возможное суммарное количество отклонений сильно варьируется. Чтобы качество конкретного грузовика было понятно всем, баллы пересчитываются в рейтинг QKZ. Вот почему он является итоговой оценкой.
Вы, наверное, заметили, сколько на предприятии контрольных постов и операций. Даже простое их перечисление заняло немалую часть статьи. Вот это и есть одна из основных черт современного завода, где по-настоящему заботятся о репутации.
А в заключение отметим, что инвестиции в проект составили 25 млн евро, а производственные мощности обеспечивают выпуск 6 тыс. грузовых автомобилей в год при двусменной работе. И еще очень важное замечание: грузовики MAN, произведенные в Санкт-Петербурге, могут участвовать в закупках государственных органов власти, проводимых по Закону 44-ФЗ. Немаловажное условие для нашего рынка.