У ближнего соседа
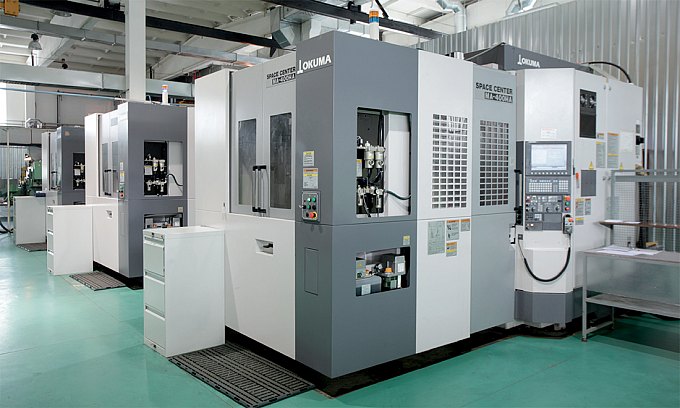
Издавна белорусы были известны своим гостеприимством, но то, как встретили меня в компании Fenox, – не просто гостеприимство, это стопроцентная открытость, с которой мне рассказывали и показывали всё. Здесь я хочу сразу предупредить наших читателей – не листайте судорожно журнал в поисках рекламы этой компании, ее нет.
В Минск я отправился исключительно по собственному желанию, чтобы узнать, как живет и работает обладатель первого в истории рынка запчастей и комплектующих обладатель Гран-при конкурса «Автокомпонент года». И знаете, не пожалел. На рынке автозапчастей я с 1979 года, многих моих коллег тогда еще и на свете не было. Так что повидать мне довелось многое, посетить десятки заводов в тогдашнем СССР, России и Европе – есть с чем сравнить то, что увидел в столице Белоруссии.
История компании началась в 1991 году, когда в Минске смонтировали линию производства автомобильной гидравлики, привезенную с завода компании Siemens. Немцы перешли на выпуск чего-то нового, а всю технологию выпуска рукавов и цилиндров вместе с заказчиками продали. Затем смонтировали и при этом еще и доработали завод по производству водяных насосов, доставленный из Испании. И снова вместе с заводом к компании перешли заказчики. Так, шаг за шагом, в различных районах и пригороде Минска возникло 12 цехов, а по сути – полномасштабных заводов по производству более пяти тысяч (!) наименований комплектующих для конвейерных поставок и вторичного рынка. Доля ОЕМ-поставок превышает 30% всего производства.
Предприятия компании Fenox выпускают детали для автомобилей европейского, российского и американского рынков: ВАЗ, УАЗ, МАЗ, ГАЗ, Audi, Mercedes, Volkswagen, Citroёn, Peugeot, Renault, Opel. Компания Fenox – официальный поставщик комплектующих на ряд отечественных заводов (УАЗ, МАЗ), а также является поставщиком второго уровня на зарубежные предприятия (в том числе на VW, Audi, Merсedes, Pegeot, Citroёn). Сегодня собственная сбытовая сеть компании включает 110 дилеров в России, Украине, Казахстане и Белоруссии.
Статус поставщика на конвейер обязывает руководство компании уделять повышенное внимание качеству продукции и сырья, используемого в производстве. Для целей поддержания качества собственной продукции и испытаний комплектующих и материалов поставщиков в 1996 году на одной из производственных площадок компании Fenox открыли испытательный центр «Качество». Сейчас центр имеет международный сертификат на право проведения испытаний материалов и готовых изделий и может выдавать заключения о соответствии продукции международным стандартам.
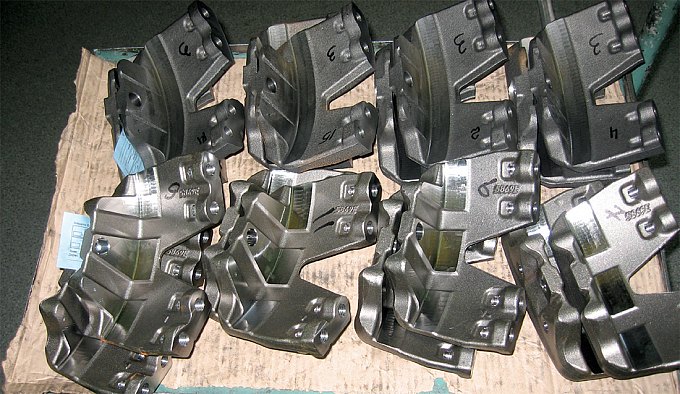
Главное условие выпуска качественной продукции, от которого зависят ее признание и востребованность, – современное высокотехнологичное оборудование на всех этапах производства. В цехах механообработки корпусов гидроцилиндров, водяных насосов, тормозных барабанов, стартеров, генераторов используются скоростные обрабатывающие центры Mori Seiko (Япония), Heller BEA (Германия), Variomatic (Голландия), металлообрабатывающие станки и комплексы OKUMA (Япония). В сборочных цехах установлены автоматизированные линии по производству тормозных дисков Minganti (Италия) и сборке суппортов Gimeco Cogis (Италия), линия по резке и обработке амортизаторных труб Vulcan (США), сварочные комплексы Dalex (Швеция – Германия). Все это оборудование не только обеспечивает эффективность и производительность труда, но и минимизирует влияние человеческого фактора на качество изделий. Вот один пример – компактный комплекс Variomatic способен заменить собой укомплектованный стандартными станками цех площадью 1000 м2.
Преимуществом компании Fenox на рынке производителей автокомпонентов является наличие полного собственного цикла изготовления деталей, который обеспечивает 100%-ную гарантию качества готового продукта. На заводах компании действует современная многоступенчатая система контроля. Начинается еще на этапах проектирования нового изделия, когда опытный образец подвергается многочисленным и всесторонним испытаниям, подтверждающим его эксплуатационные свойства. Интересно, что чаще всего эти испытания проводят сами конструкторы и разработчики, чтобы получить наиболее достоверную информацию о будущей детали.
С началом серийного производства вступает в действие механизм контроля уже готовых изделий. Причем и этот процесс в значительной степени автоматизирован. Первый раз деталь проходит проверку еще на конвейере, когда специальное оборудование тестирует ее на отсутствие дефектов, соответствие всех допусков установленным нормам и т.п. Затем она повторно проверяется на трехкоординатных 3D-контрольных стендах Braun-Sharp, которые отслеживают соответствие геометрии изделия расчетным параметрам с точностью до 0,5 мкм. Кроме того, уже перед отгрузкой потребителю каждая партия проходит дополнительное выборочное тестирование и проверку.
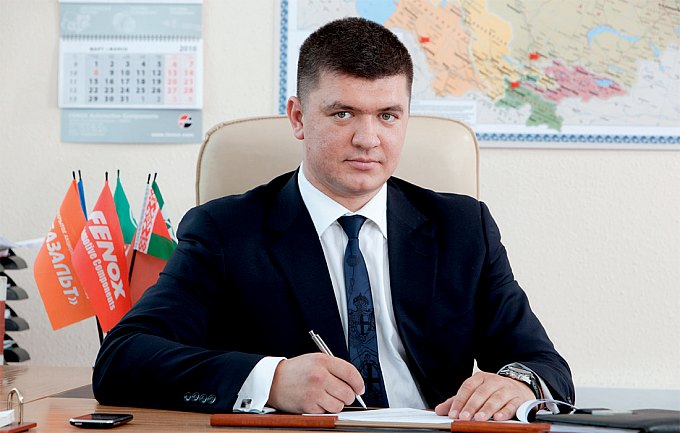
Контролируется качество не только выпускаемых узлов и агрегатов, но и инструмента. Обрабатывающие центры оснащены системами контроля износа режущего инструмента, которые контролируют его состояние и автоматически останавливают процесс, если его параметры опустились ниже допустимого уровня.
Сплошная система контроля качества обеспечивает точное соблюдение всех параметров, влияющих на безопасность движения и управления автомобилем. С ее помощью отслеживается состояние инструмента, оснастки и оборудования. В результате системного подхода к контролю качества своей продукции корпорация Fenox первая в СНГ получила объединенный сертификат производителей узлов и агрегатов для мировой автомобильной промышленности ISO/TS 16949.
Моим проводником по лабораториям, цехам и отделам компании Fenox был Валерий Тепешко, заместитель директора по маркетингу, настоящий фанат компании, знающий о производстве всё. В каждом цехе его встречали как своего. Благодаря его гостеприимству и терпению мне удалось познакомиться со многими технологическими процессами, которые я видел впервые.
Кто может рассказать о компании лучше директора по маркетингу? Верно, никто. Тем более что Юрий Клюшенков – отличный собеседник и поистине неиссякаемый источник информации не только о том, что происходит в компании, но и о том, как обстоят дела на вторичном рынке запчастей.
– Юрий Александрович, компания Fenox стремительно набирает очки на рынке запчастей и комплектующих не только в СНГ, но и в Европе, и выходит на лидирующие позиции. Такой прорыв возможен только при наличии мощной стартовой базы. Из чего складывалась производственная база компании – были ли это действующие заводы или предприятия строились с нуля?
– Современная производственная база компании Fenox складывалась в течение почти 20 лет, начиная с 1991 года, когда был подписан первый контракт на производство запасных частей. За эти годы мы формировали ее несколькими путями. Это в первую очередь монтаж вывезенных действующих заводов, производящих изделия для конвейера, для выпуска запчастей и комплектующих также на конвейеры, в том числе европейских компаний. Мы также покупали лицензии на производство изделий и одновременно закупали необходимое для этого оборудование. Значительную часть оборудования мы проектировали, производили и устанавливали собственными силами. Здесь необходимо отметить, что в компании работает очень много специалистов из объединения «Автопромсборка», которое во времена СССР разрабатывало сборочные линии и автоматические комплексы практически для всех автомобильных заводов. Так что с самыми квалифицированными кадрами на постсоветском пространстве у нас проблем нет. К тому же мы часто приглашаем на работу главных специалистов с действующих машиностроительных заводов.
– Компания Fenox позиционируется как фирма с участием Германии, Белоруссии и России. Каковы доли участия представителей этих стран и как распределен производственный потенциал компании между ними?
– Да, компания Fenox позиционируется как фирма с участием Белоруссии, но именно на долю нашей республики приходится основная часть персонала. Только на самих производствах Fenox в администрации компании работает более 3,5 тыс. человек. Одна только конструкторская группа насчитывает 300 сотрудников. По численности занятых мы входим в группу лидеров белорусского машиностроения. Если же прибавить рабочих предприятий-поставщиков, например, литья и других полуфабрикатов, окажется, что в деятельность нашей компании только в Белоруссии вовлечено более 5 тыс. человек. Кроме этого, у компании есть собственные заводы в Германии и России.
– Кто был инициатором создания компании Fenox, чем оно было вызвано: потребностями вторичного рынка, ОЕМ, дефицитом запчастей и комплектующих?
– Формально инициатором создания компании Fenox был комитет ОЕМ, но на самом деле мы считаем, что здесь сошлось несколько факторов. Прежде всего, растущая глобализация и интеграция как автомобильной промышленности в целом, так и производства автокомпонентов. С другой стороны, промышленный потенциал Белоруссии хорошо известен в мире по поставкам жодинских самосвалов и минских тракторов и признан многими специалистами рынка. Нельзя не отметить важную роль решения социальной проблемы – после распада СССР не у дел оказался мощный и квалифицированный коллектив объединения «Автопромсборка». Без работы осталось несколько сотен грамотных специалистов, потенциал которых трудно переоценить.
– В состав компании входит 12 заводов по производству различных автокомпонентов. Кто, как и по каким принципам определяет техническую политику компании и необходимость развития тех или иных производств?
– Основной груз ответственности за определение технической и маркетинговой политики лежит на службе маркетинга, в которой занято 55 человек. Должен отметить, что большинство из них работают в компании более 10 лет и прекрасно знают рынок запчастей и комплектующих. На основе проведенных ими анализов и подготовленных прогнозов директор па маркетингу и сбыту определяет возможность продажи тех или иных изделий, а техническая служба предприятия рассчитывает необходимость и возможность развития действующих или формирования новых производств.
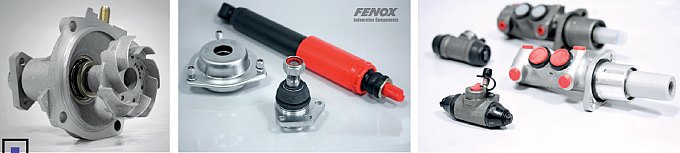
– Производственная программа компании Fenox составляет несколько тысяч деталей. Компания выпускает их только по чертежам и технологии компаний-изготовителей автомобилей или разрабатывает сама? Каков научно-исследовательский и испытательный потенциал компании?
– Все необходимые чертежи, регламенты и технологию производства компания Fenox разрабатывает сама. У нас есть собственный инструментальный участок, на котором занято около 400 человек. Здесь мы делаем необходимый инструмент и оснастку, которые передаем на производство. Специалисты участка следят за их регулярным обновлением. Чтобы представить себе объем работы, выполняемой нашими технологами, достаточно сказать, что компания Fenox ежегодно осваивает порядка 300 новых или модифицированных изделий. Мы ежегодно получаем около 10 новых патентов, и освоение выполненных по ним комплектующих требует большой конструкторской и технологической проработки.
Все наши новые разработки, как и серийная продукция, проходят проверку в испытательной лаборатории компании. Она оснащена уникальными контрольно-измерительными комплексами, многие из которых разработаны нашими специалистами и изготовлены своими силами. Лаборатория сертифицирована как Госстандартом Белоруссии, так и ISO. По признанию многих зарубежных специалистов, работавших у нас и проводивших аудит, аналоги испытательной лаборатории Fenox в странах СНГ отсутствуют.
– Компания взяла сразу несколько призов на первом конкурсе «Автокомпонент года». Как отразились эти победы на имидже и рыночном положении компании?
– Не скрою, нам было приятно стать победителями первого конкурса «Автокомпонент года» сразу в нескольких номинациях, да еще и получить Гран-при. Мы расцениваем эти победы как аванс, выданный нам экспертами рынка, и надеемся победами в следующем конкурсе доказать, что выбор нас в качестве лидера был закономерен.
Несмотря на то что с момента объявления результатов конкурса прошло менее полугода, наша маркетинговая служба заметила, что рейтинг компании Fenox вырос, рыночные положение укрепилось, увеличилось количество партнеров и потенциальных заказчиков.
– Каковы ближайшие планы компании в технической и торговой политике?
– Компания Fenox намерена создавать новые производства, в том числе и в России, модернизировать и расширять уже имеющиеся. Основной акцент в формировании технической и торговой политики мы делаем на развитии производства запчастей и комплектующих для бюджетных иномарок, производимых в РФ. При этом мы планируем увеличить долю поставок на конвейеры, не ослабляя своих позиций на вторичном рынке союзного государства.
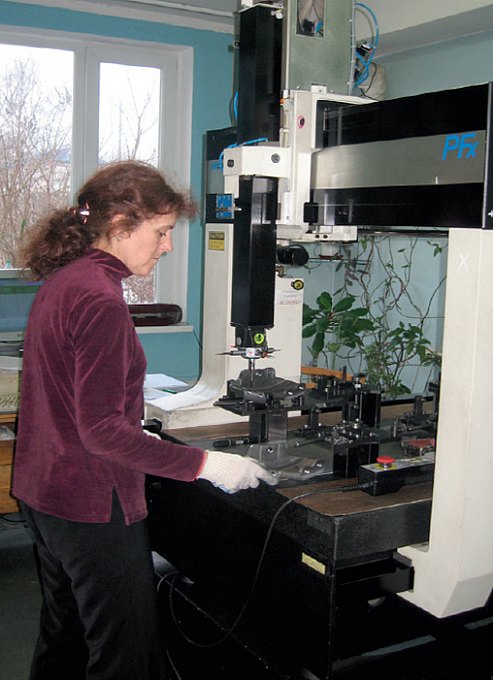
Кроме этого, в торговой политике компания Fenox намерена укрепить дилерскую сеть, повышать лояльность покупателей за счет улучшения качества производимых изделий. Одним из новых и развивающихся направлений в деятельности компаний, выпускающих запчасти и комплектующие, стало формирование собственных сетей и сервисных концепций. Наша компания также планирует работать и в этом направлении.
За два дня, проведенных в Минске, я смог посмотреть лишь часть производственных цехов компании Fenox, но и этого было достаточно, чтобы увидеть многое. Прежде всего обращает на себя внимание жесточайший контроль качества деталей и узлов на всех этапах производства. Причем критерии контроля крайне высоки и во многом диктуются заказчиками, среди которых немало ведущих автомобилестроительных компаний. Вторая особенность производства – наличие большой доли оборудования собственной разработки и производства. В первую очередь автоматизированных комплексов контроля выпускаемой продукции. Многие автоматы вообще не имеют аналогов и защищены патентами и авторскими свидетельствами.
У многих из нас сложилась какая-то мазохистская привычка ругать все свое, домашнее. В данном случае к «своим» я отношу и компанию Fenox – мы все из одного прошлого, и у нас одно будущее. Но это так, отступление. На самом же деле многие владельцы Audi и Mercedes даже не подозревают, что, доверяя свою безопасность тормозам этих мировых лидеров, они доверяют ее изделиям белорусских мастеров. Впрочем, произведенные в Минске узлы и агрегаты можно встретить и в автомобилях других марок, выпущенных и в Европе, и в Азии. Вот вам и свое, домашнее.