Тормозная рулетка
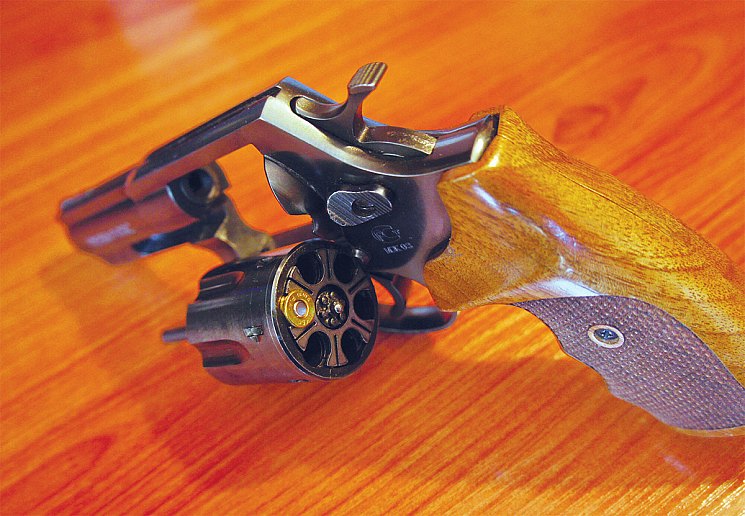
Пролог
Сколько ни сетуй на финансовый кризис, легче от этого не станет. Вон лягушка из детской сказки – свалилась в крынку со сметаной, трепыхалась-трепыхалась, сбила кусок масла, да и выбралась наружу. Мораль проста: работать надо!
Спорить с этим никто не станет. Да вот только «спасительное масло» каждый «сбивает» по-своему… В том числе и производители автокомпонентов, в частности – тормозных колодок. На этом сказка кончается. Дальше только факты, цифры и выводы.
В распоряжении редакции оказался «Отчет об исследованиях колодок дискового тормоза фирм <…> на предмет соответствия техническим требованиям при их реализации на российском рынке запчастей».
Мы намеренно опускаем товарные знаки. Почему – поясним в конце статьи. Оставим за кадром и страну, откуда прибыли эти колодки. Ограничимся лаконичным: наш ближайший сосед. А колодки от ближайшего соседа обозначим «Колодка Б», «Колодка Д», «Колодка Т».
Теперь раскроем отчет, оформленный в 2014 году. Его компетентность сомнений не вызывает. Документ подготовлен предприятием-производителем, поставляющим колодки дискового тормоза на конвейеры и в сервисные центры России и других стран и имеющим в своем составе Испытательный центр. Так что «экзамены» проводились ответственными и квалифицированными специалистами на современном оборудовании и по современным методикам. Далее для краткости мы будем именовать их просто Испытатели.
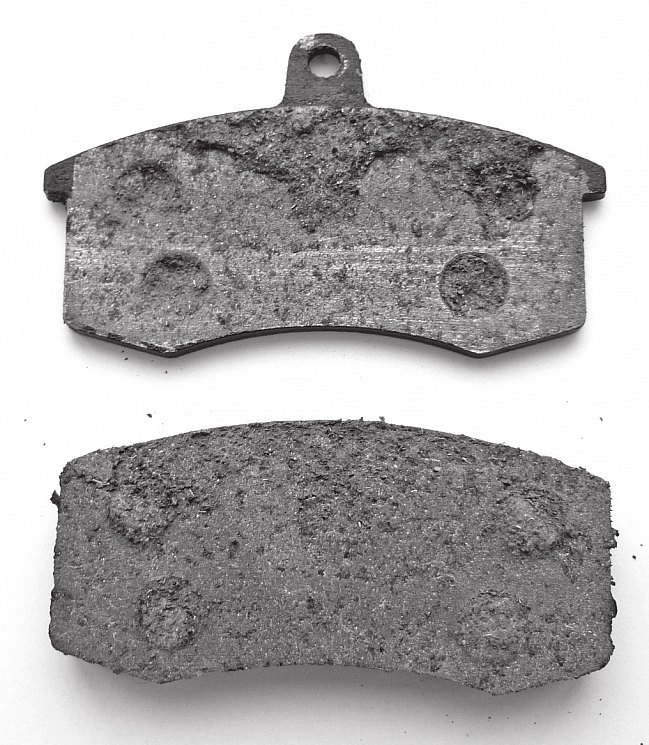
Иногда мы будем вынуждены переходить на формальный стиль изложения – как в отчете. Особенно если речь идет о методиках и оборудовании. Возможно, эти фрагменты покажутся сухими и скучноватыми. Но в данном случае протокольная четкость важнее литературных изысков.
Необходимые формальности
Итак, предмет исследования – колодки дискового тормоза для автомобилей семейства ВАЗ-2108–2112. Цель – сравнительная оценка их фрикционно-износных и прочностных характеристик на предмет соответствия техническим требованиям при реализации на рынке автозапчастей на территории РФ.
Начнем с объекта испытаний. Перечислим его составляющие.
• Суппорт переднего тормоза в сборе, дет. 2108–3501011.
• Тормозной диск сплошной (невентилируемый), дет. 2108–3501070.
• Колодки с накладками в сборе от трех фирм.
Теперь о методиках и оборудовании. Всего испытаний было три. Испытания на прочность соединения накладок с колодками проводились по ИСО 6312 в приспособлении ПО-87 на гидравлическом прессе П-10.
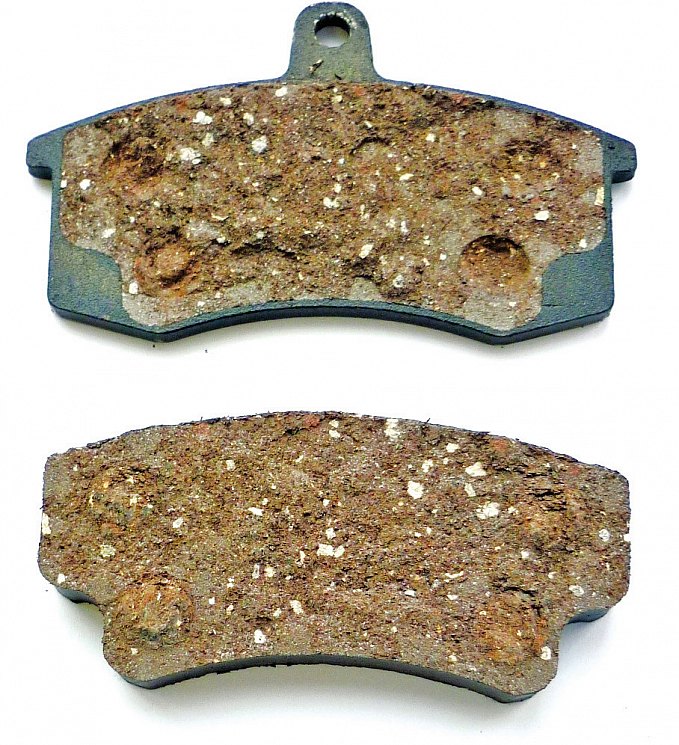
Испытания колодок на сжимаемость по ИСО 6310 выполнялись на машине Jurid Honeywell.
Фрикционно-износные испытания проводились по двум программам:
• по программе-методике АК-Мастер на соответствие требованиям ОАО «АвтоВАЗ» и ТУ 2571–093–00152129–2013;
• по программе-методике стендовых испытаний на соответствие Правилам ЕЭК ООН № 13-Н на стенде СТИН-2М.
Для измерения толщины колодок применялся микрометр 2-го класса точности, ГОСТ 6507–90 с диапазоном измерений 0–25 мм и ценой деления 0,01 мм типа МК-25.
Завершив это формальное описание, переходим к изучению результатов испытаний.
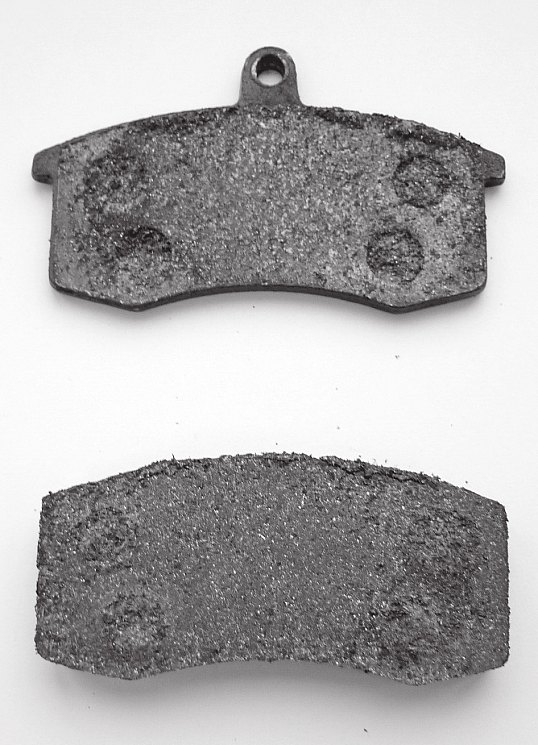
Прочность соединения
Возможно, для читателя будет понятнее такая формулировка: проверка прочности соединения фрикционной накладки с каркасом – металлической пластиной, на которой эта накладка крепится.
Суть в следующем: накладку нагружают усилием, направленным вдоль радиуса тормозного диска. Рано или поздно происходит отрыв накладки от каркаса либо разрушение фрикционного материала «по массе».
Оказалось, что по величине сопротивления сдвигу накладки все испытуемые колодки удовлетворяют требованиям двух нормативных документов.
Во-первых, это ГОСТ Р 41.90–99 (Правила ЕЭК ООН № 90) «Единообразные предписания, касающиеся официального утверждения сменных тормозных накладок в сборе и накладок барабанных тормозов для механических транспортных средств и их прицепов».
Во-вторых, ТУ 38.114499–96 «Накладки безасбестовые с колодками в сборе дисковых тормозов автомобилей ВАЗ 2110 и 2123 и их модификаций».
Наибольшее сопротивление сдвигу накладки продемонстрировали образцы «Колодка Т». Однако после стендовых испытаний значение показателя отрыва снизилось практически вдвое. Также изменился характер отрыва – на каркасе колодки остается 15–40% «голой» поверхности с отсутствием клея, что не соответствует нормативам (см. рис. 1) .
Наиболее стабильное значение показателя «Сопротивление сдвигу накладки относительно колодки» имеют накладки «Колодка Д». Характер отрыва у данных изделий таков – 100% «по массе» до стендовых испытаний и 10–15% «по каркасу» после них, что соответствует норме (рис. 2) .
А вот самое нестабильное значение показателя сопротивления сдвигу имеют накладки участника «Колодка Б». Различие составляет около 25% до стендовых испытаний и около 45% после них. При этом значение показателя снижается на 40%. А у одной из накладок составляет 2,6 МПа, что не соответствует требованиям ТУ и говорит о нестабильности процесса производства данных накладок.
По характеру отрыва данные колодки также имеют нестабильные показатели: на каркасах остается от 0 до 25% «голой» поверхности без клея и фрикционного материала (см. рис. 3) .
Сжимаемость
Современные требования к фрикционным материалам рождают новые термины и новые показатели. Один из них – сжимаемость фрикционной накладки.
От того, насколько податлива накладка, зависит пауза от момента нажатия на педаль до возникновения необходимого тормозного момента. Мягкая накладка может недопустимо затянуть эту паузу, слишком жесткая – вызовет нежелательные писки и скрипы при торможении. Нужен оптимум.
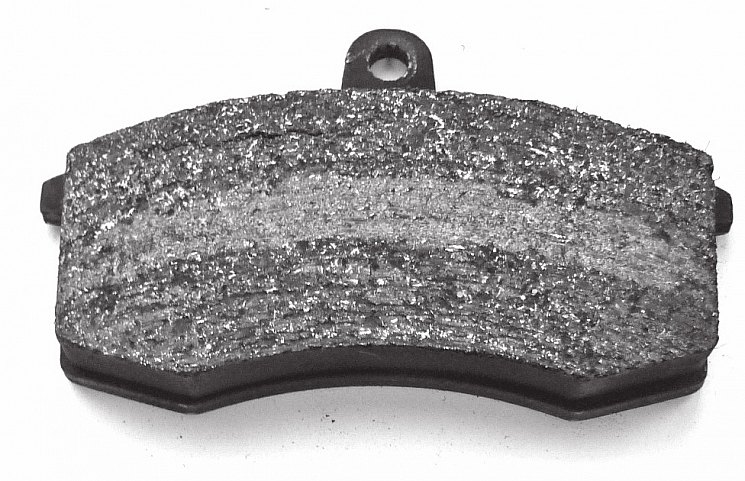
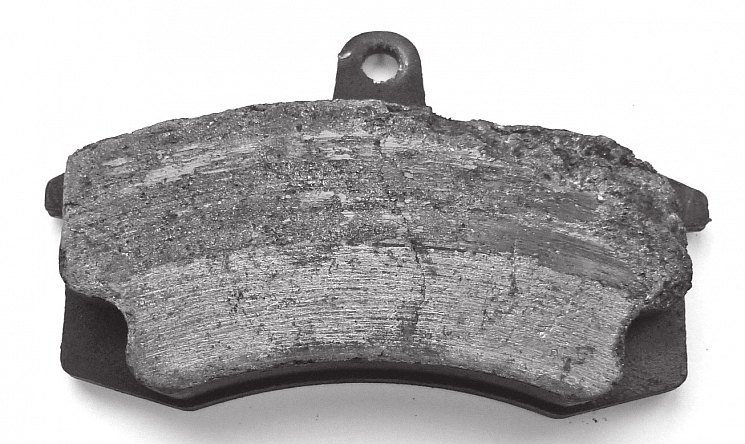
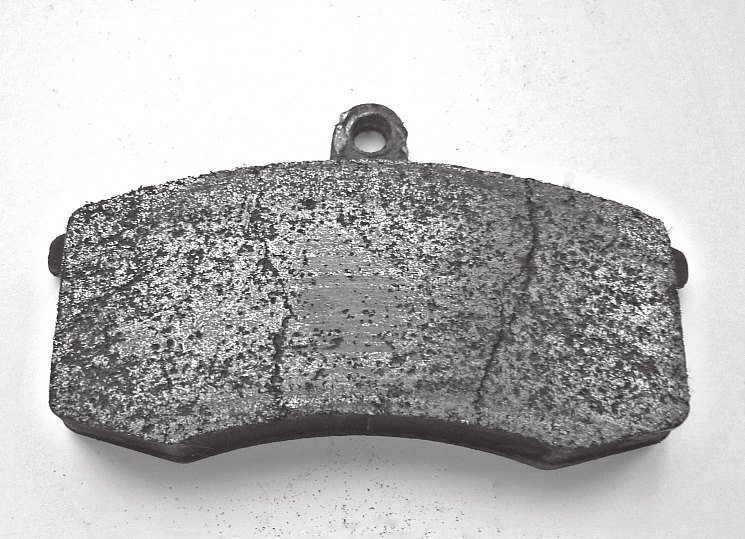
Кроме того, определение сжимаемости на разных стадиях изготовления накладки позволяет отследить, во‑первых, стабильность каждого звена технологической цепочки, во‑вторых, правильность техпроцесса в целом. Что же продемонстрировали испытуемые колодки?
Сначала о хорошем. По величине сжимаемости при нормальных условиях все колодки соответствуют требованиям ГОСТ Р 41.90–99 (Правила ЕЭК ООН № 90) .
Однако значения сжимаемости для всех представленных образцов нестабильны. Самый большой разброс выявлен у образца «Колодка Б» – 52 мкм (min 176, mах 228 мкм). А наименьший разброс продемонстрировал участник «Колодка Т» – 27 мкм (max 85 и min 58 мкм).
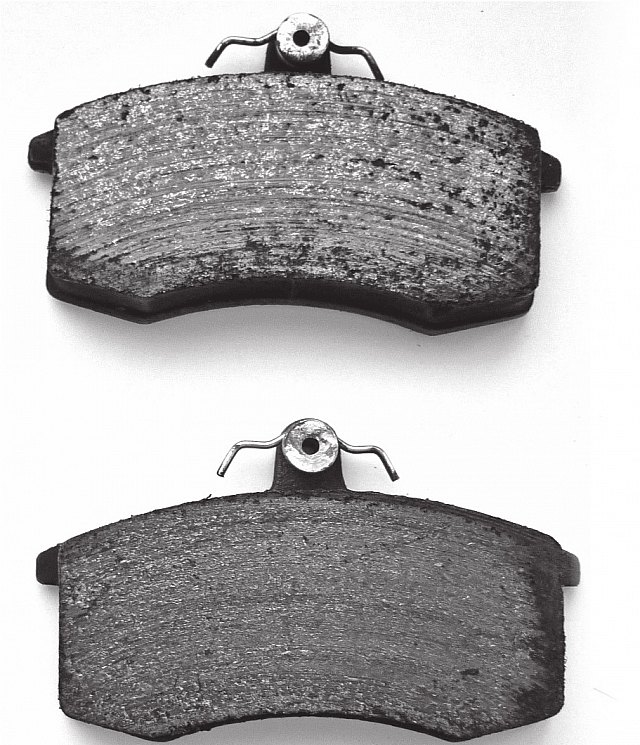
Испытания по методике АК-Мастер
Эти испытания проводятся на стенде, имитирующем реальный тормозной узел. Методика АК-Мастер, в частности, позволяет оценить:
• эффективность торможения;
• износостойкость;
• восстановление после нагрева.
По результатам испытаний все образцы сравнивались с аналогом (оригинальной колодкой). В итоге все участники продемонстрировали худшие, чем у аналога, фрикционно-износные свойства. Более того: они уступают оригинальным накладкам практически по всем показателям и не соответствуют требованиям ТУ. А теперь подробности – как и договорились, с использованием сухой, но строгой терминологии Испытателей.
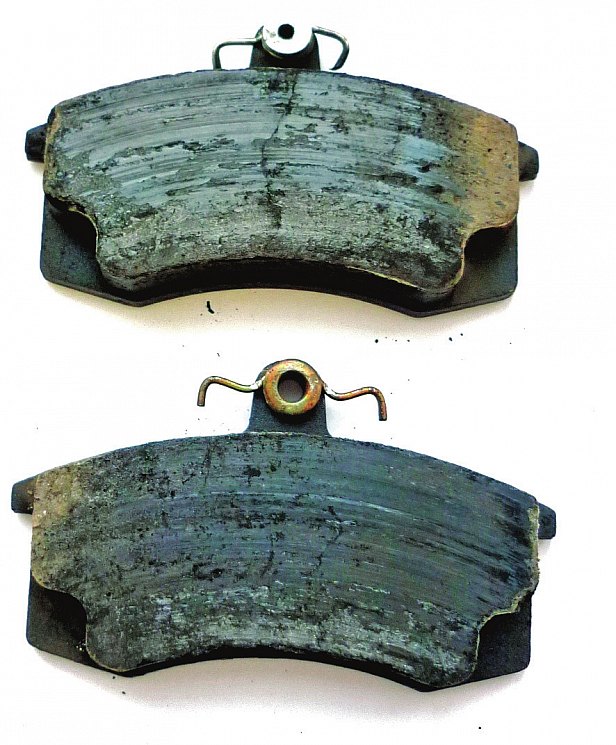
Средний показатель трения за испытание оказался ниже требуемого по ТУ. А именно: у накладок «Колодка Д» на 35%; у накладок «Колодка Т» на 29%; у накладок «Колодка Б» на 18%.
Значение минимального показателя трения за испытание также не соответствует норме. Наибольшее значение имеют накладки «Колодка Б» – они ближе всего к аналогу. Наименьшее значение у накладок «Колодка Т» – эти уступают аналогу в 2 раза.
Смотрим величину износа внутренней и наружной накладки. Наибольшее значение демонстрируют образцы накладок «Колодка Т». При испытании накладки «Колодка Д» произошло расслоение и разрушение наружной накладки. Зафиксирован небольшой износ диска в размере 0,01–0,02 мм, что является допустимым.
Шумов при торможениях не выявлено во всех трех случаях, однако при нагреве до 500 °C произошло воспламенение накладки «Колодка Т». Это, разумеется, не соответствует никаким требованиям безопасности.
При осмотре после проведения испытаний у накладок «Колодка Б» обнаружены трещины и отслоения (см. рис. 6). На внутренней накладке имеются две полусквозные трещины по всей ширине, на наружной – отслоение накладки от каркаса с одной стороны на глубину более 10 мм. Также в результате испытаний данных накладок «просели» пружины поджатия колодок к суппорту.
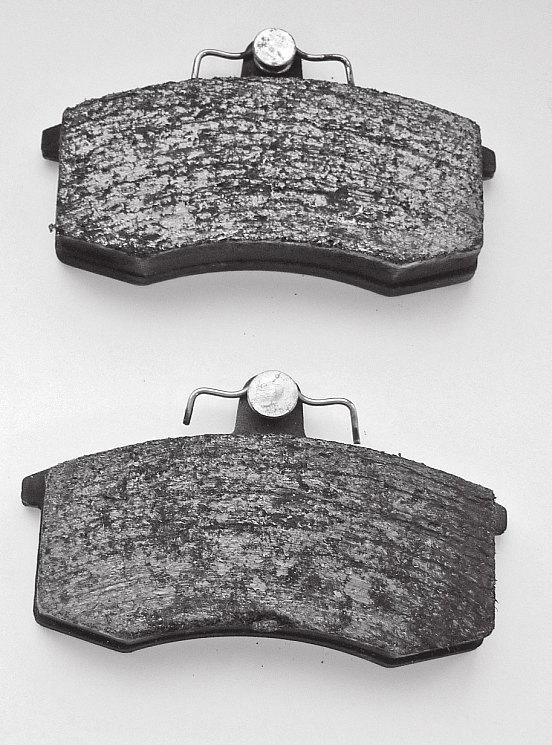
У образца «Колодка Д» произошло разрушение и расслоение половины наружной накладки. Фрикционные накладки «Колодка Т» остались без видимых дефектов.
Таким образом, данные испытания показали, что все образцы колодок от ближайшего соседа не соответствуют требованиям ОАО «АвтоВАЗ» и ТУ 2571–093–00152129–2013 по фрикционно-износным свойствам.
Соответствие Правилам ЕЭК ООН № 13
Далее были проведены стендовые испытания на соответствие Правилам ЕЭК ООН № 13. В качестве аналога выступили оригинальные накладки 2110–3501090, образцы взяты из серийной партии. И вот что выяснилось.
Наиболее близкие к аналогу показатели получены у образца «Колодка Б». Эффективность торможения двух других образцов оказалась в среднем на 25% ниже, чем у аналога. При том что норма отклонения от оригинала по Правилам ЕЭК ООН № 13 составляет 15%.
По испытанию на потерю эффективности все образцы показали удовлетворительные результаты. Для накладок «Колодка Б» отмечена недостаточная восстанавливаемость фрикционных свойств, составляющая 80% от первоначального уровня.
Восстанавливаемость фрикционных свойств накладок «Колодка Д» составляет 90%, а накладок «Колодка Т» – 130%, что говорит о значительной сверхвосстанавливаемости и нестабильности фрикционных свойств колодок.
После завершения испытаний при осмотре изделий была выявлена непригодность эксплуатации накладок «Колодка Б» из-за значительных (более 5 мм) отслоений накладки от каркаса на наружной колодке. Внешний вид этих колодок представлен на рис. 7.
У образцов «Колодка Д» на каждой из накладок отмечено по одной поперечной трещине и выкрашивание кромки (рис. 8).
На накладках «Колодка Т» отмечены отдельные короткие поверхностные трещины (см. рис. 9). Также при разогреве тормоза до температуры более 450 °С накладки воспламенились.
В конце главы – неутешительное заключение. На основании полученных результатов признаны непригодными к использованию в тормозных механизмах автомобилей ВАЗ 2108–2110 все образцы колодок:
• «Колодка Б» – по причине отслоений накладки от каркаса;
• «Колодка Т» – по причине воспламенения в процессе испытаний;
• «Колодка Д» – по причине разрушения и расслоения накладки.
Невеселые итоги
Как и полагается, в конце отчета Испытатели суммируют сказанное. Кое в чем приходится повторяться, но таковы «законы жанра» – все выводы концентрируются в заключительной главе.
Итак, образцы колодок от ближнего соседа «Колодка Т» и «Колодка Д» не соответствуют требованиям ОАО «АвтоВАЗ» и Правилам № 13-Н ЕЭК ООН.
В частности, по эффективности торможения они значительно уступают аналогу. Так, при нормативе отклонения ± 15% «Колодка Т» демонстрирует показатели на 22–26% ниже, а «Колодка Д» – на 20–29% ниже аналога.
После нагрева эффективность торможения обеих колодок падает до недопустимо низких величин – их коэффициенты трения 0,15 и 0,17 соответственно. При том что норма не ниже 0,30.
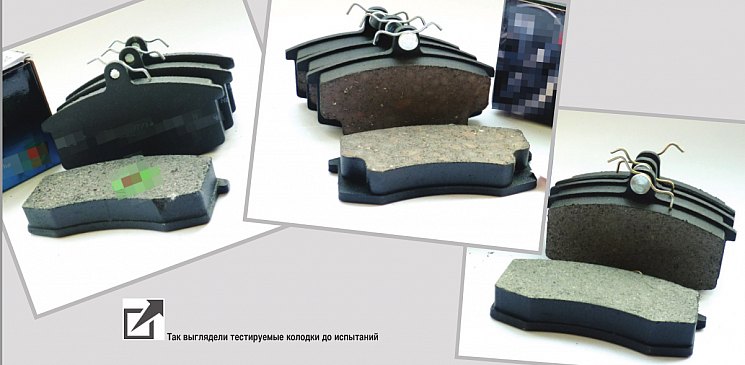
Изделия «Колодка Б» соответствуют требованиям по уровню эффективности торможения, однако после завершения испытаний наблюдается значительное отслоение накладки от каркаса (более 10 мм) и образование полусквозных трещин. Это не гарантирует безопасности применения данных колодок при длительном сроке эксплуатации.
Изделия «Колодка Д» имеют недостаточную термомеханическую прочность, разрушаются и выкрашиваются в процессе испытаний.
Изделия «Колодка Т» имеют нестабильные фрикционные свойства до и после нагрева, отличаются высоким износом, а при нагреве тормозов и достижении температуры более 450 °С накладки воспламенились.
И еще. Маркировка изделий «Колодка Д» и «Колодка Б» не соответствует требованиям п. 4.1 Технического регламента «О безопасности колесных транспортных средств», так как на них отсутствует знак обращения на рынке РФ.
Знак обращения на рынке отсутствует также на упаковке изделий «Колодка Б» и «Колодка Т». Иными словами, упаковка не соответствует требованиям п. 4.3 Технического регламента «О безопасности колесных транспортных средств».
Эпилог
Разумеется, мы пересказали и процитировали не все. Но самую важную информацию до читателя донесли. Колодка, которая разрушается или воспламеняется при торможении! Надо ли пояснять, чем это грозит водителю и пешеходам?
Почему мы не называем имена производителей этих колодок? Да потому, что таких «джентльменов удачи» очень трудно поймать за руку. У них всегда найдется в запасе партия образцов, сделанных более добросовестно. И они готовы представить их, если возникнут претензии – например, при страховом случае. А разыскать дефектную партию к тому времени будет невозможно.
Выход тут один – хорошо знать рынок, производителей оригинальных изделий, поставщиков конвейера и афтемаркета. Это же открытая информация. Добросовестные производители обеспечивают качество всегда – даже в ущерб прибыли. Кризис кризисом, а безопасность безопасностью. Да и честь товарного знака для них не пустой звук.
Но, как видим, есть и другие, для которых главное – прибыль. Сделать колодки подешевле, продать их подороже – тут уж не до качества. И что для них здоровье и жизни водителей, пассажиров и пешеходов? Фактически они предлагают нам сыграть в «русскую рулетку» – покрутить барабан револьвера и нажать спусковой крючок. А там уж как повезет. Если не повезет, божок, чье имя Золотой Телец, простит.